What’s New in Simcenter Mechanical simulation – 2212 Release
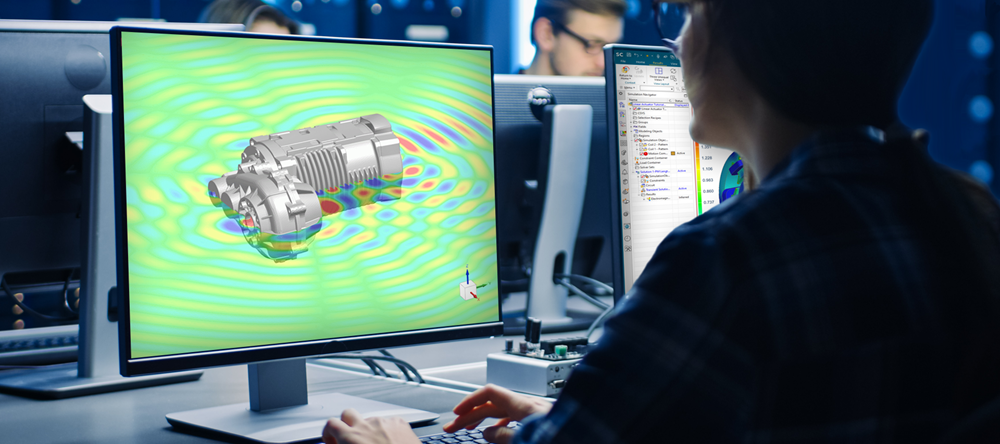
Simcenter for mechanical simulation
When engineering a new product, you often ask yourself questions like these about its performance:
- Will it break?
- Is it too loud?
- Does it get too hot?
- What size of motor do I need?
- How long will it last?
- Is it safe?
You need accurate, fast, insightful, and innovative answers to these questions. But how? Physical testing alone takes too long and is too costly.
Simcenter Mechanical simulation software tools can help get the answers you need before ever building a physical prototype. Simcenter Mechanical tools let you model the complexity of your products, help your development processes go faster, explore more possible design options, and keep your simulation data and processes integrated.
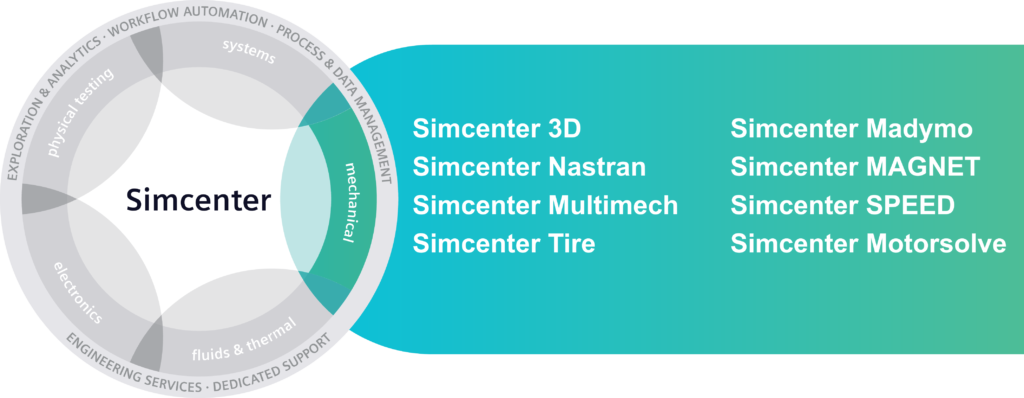
All of the simulation tools in the Simcenter Mechanical simulation domain, such as Simcenter 3D, Simcenter Nastran, Simcenter MAGNET, and more, are now aligned to the same release cadence starting with the latest 2212 release. New enhancements in the Simcenter Mechanical are aimed at solving engineers’ challenges in these industries:
- Automotive applications
- Aerospace applications
- Industrial machinery applications
- Applications across industries
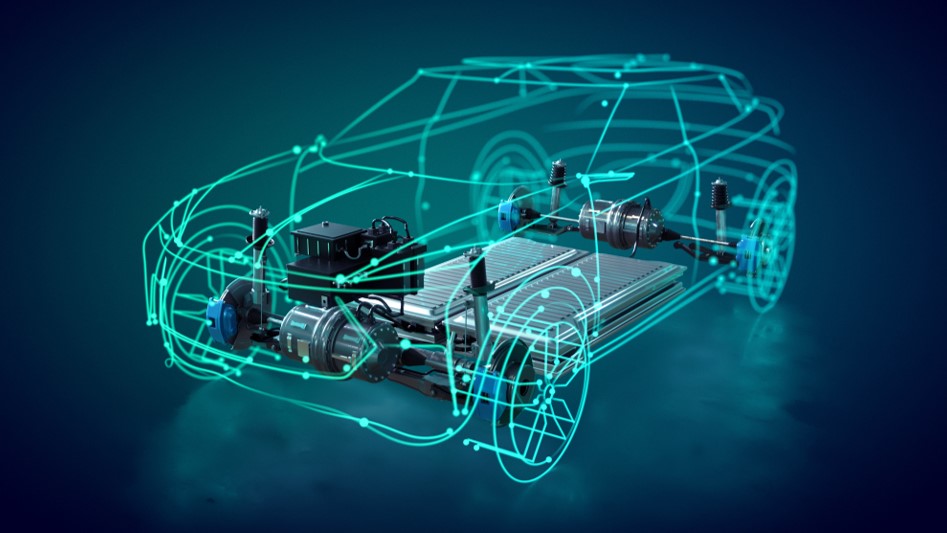
Automotive applications
A lot is changing in the automotive sector, and as a result, so are the demands engineers are making on their simulation tools.
Electrification of automotive powertrains has profound effects on the behavior of vehicles, from electromagnetics to dynamics and acoustics performance. Simcenter Mechanical simulation solutions include new features to help you streamline the e-powertrain simulation workflow.
Additional enhancements will also improve the simulation of other automotive applications from NVH, to tires, to windshield wiper performance:
Streamline the EV powertrain engineering workflow
Most automakers today are making a big push towards developing and introducing many new electric vehicles. This is a relatively new application domain area for everyone in this industry, and so development processes for EV powertrains are not streamlined operations. Engineers can find themselves working in specific silos from motor design, transmission structural performance, and acoustics among others. Most likely each of the teams in these silos are using different tools, and information doesn’t flow smoothly from one silo to the next.
Simcenter Mechanical can help you break these silos and stay integrated by allowing simulation and design to easily flow from one step to the next:
E-motor multi-attribute design
EV powertrains begin with electrical motor design. Simcenter Mechanical includes a template-based electric motor design and simulation tool that can completely automate the design iteration and selection process. This lets you evaluate hundreds to thousands of design options rapidly!
E-motor detailed analysis
Once you’ve determined a good motor design, you can move into Simcenter 3D for more detailed analysis to minimize losses or optimize the performance when designing the end-windings or connecting to the power electronics system. These analyses can be in 2D or 3D, and even allow you to perform multiphysics analysis, such as a coupled thermal analysis.
Transmission simulation
Easily move to analyze multibody simulation performance of your motor and transmission within the Simcenter 3D environment. Simcenter 3D can help you automate the creation of multibody models, including gear geometry. The multibody simulations can give you load information and you can even model gears as flexible bodies which can then lead to in-depth gear whine analysis which becomes even more critical in quiet EVs.
Acoustic simulation
The multibody simulation also gives you input to determine the vibration of the gear house structure, which you can use for vibro-acoustic analysis directly in the same Simcenter 3D environment.
Acoustic radiating surface
More accurately simulate internal aero-acoustically induced noises that come from the HVAC vents with new support for models with heterogeneous fluid domains inside the car cabin. This means you can model the seats as heavy air or as a real porous material even while the rest of the cabin is modeled with regular air fluid elements. This results in a more accurate representation of the sound experience for passengers.
Motion contact pattern display
The new contact pattern display in Simcenter 3D can help you better evaluate wiper contact patterns. By modeling the wiper as a flexible body combined with contact elements in the Simcenter 3D Motion application, the new contact pattern display will show results in a very easy-to-interpret animation of the wiper forces across the windshield. This lets you easily see how consistently or inconsistently the forces are distributed and if your wiper design will work as expected.
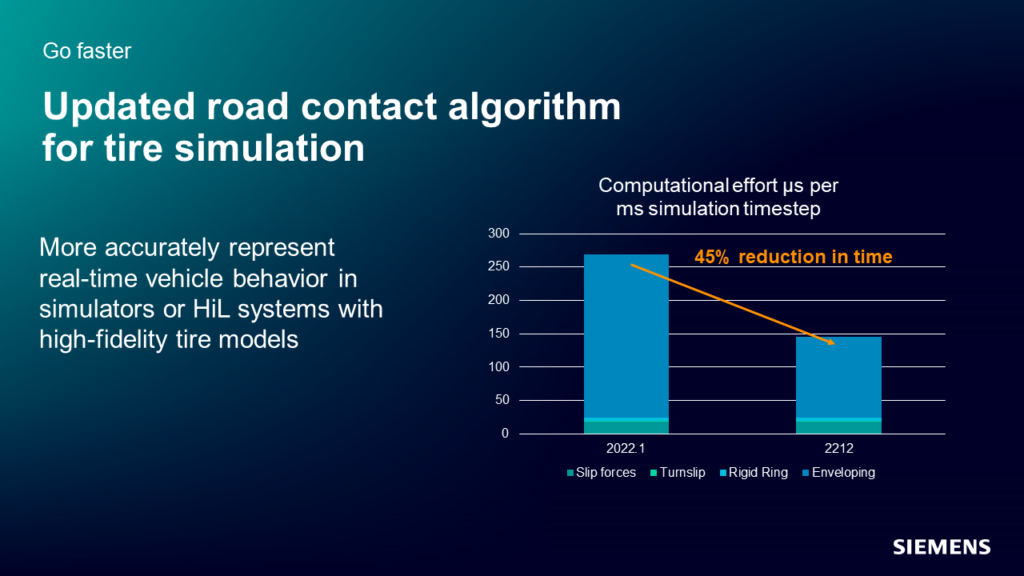
Updated road contact algorithm for tire simulation
In this latest release of Simcenter Tire, we updated the road contact algorithm to reduce road data exchange. What this means to you is an increased computational performance by 45% so that high-fidelity tire models can be used in real-time applications like simulators or hardware-in-the-loop (HiL) systems.
Include reduced order models and FRF data in assemblies
The Assembly Composer in Simcenter 3D has been extended to utilize reduced-order models as components, such as FRF data that could come from physical testing in Simcenter Testlab. Hybrid models that combine FE components and FRF or other reduced order models let you quickly explore more possibilities with more model variants faster.
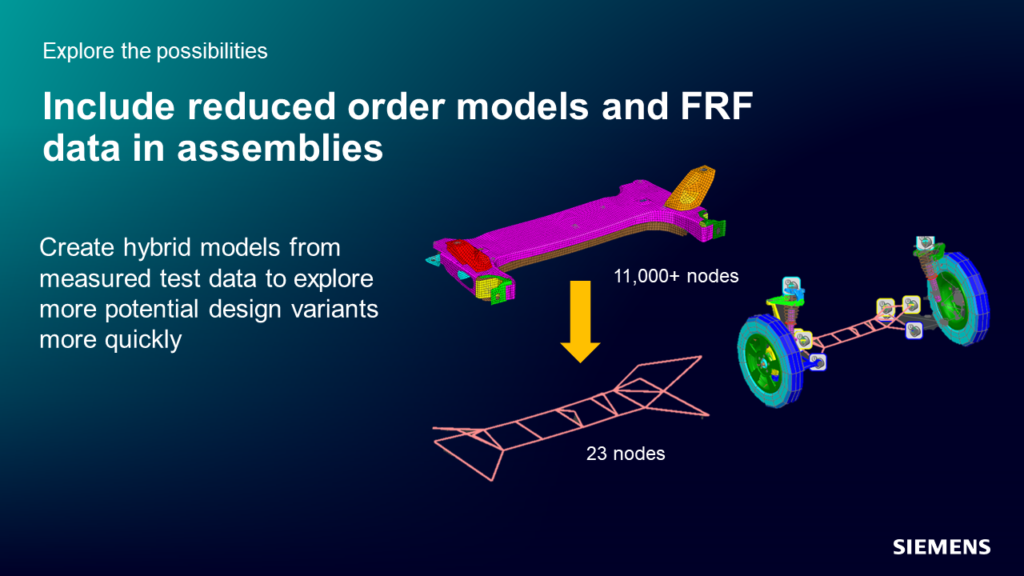
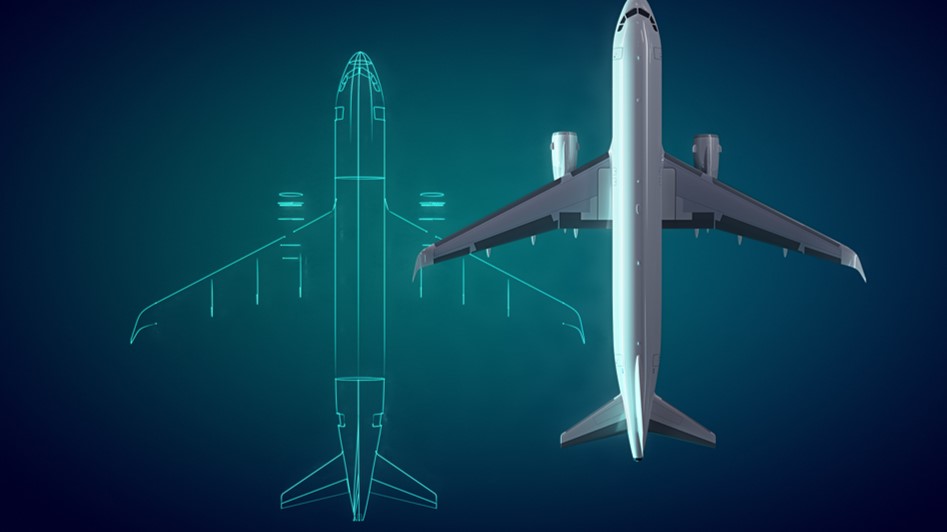
Aerospace applications
Airframe and rocket engineers rely heavily on simulation, and the simulation tools in Simcenter Mechanical are a valuable part of an engineer’s toolbox. New capabilities available in Simcenter 3D and Simcenter Nastran can help you calculate the margin of safety faster, model the complexity of thin aircraft skins better, and help you understand how liquid sloshing in fuel tanks can impact launch dynamics.
Standard margin of safety
calculation templates
New standard calculation templates can help you automatically prefill all the inputs based on a set of modeling rules. All that remains for you to do is pick a geometry to apply calculation on. You can also easily deploy these templates across your stress organization so that everyone has access to the latest and greatest.
Tension-only quad element
Airframe engineers face a challenge when modeling thin aircraft skins where they often need to create multiple models with different properties to account for all of the various loading conditions.
The new nonlinear tension-only-quad element helps solve this challenge. Depending on the loading condition, the tension-only-quad will automatically change from membrane behavior to shear behavior. This means you now only need one model to represent your structure for any loading condition, which reduces your simulation process time by 80%.
Simulate sloshing dynamics
New methods in Simcenter Nastran can help you simulate the sloshing dynamics of fuel in rocket tanks, which can interfere with guidance system controls. The incompressible fluid model helps you predict slosh frequencies and hydro-elastic modes.
Static shape correlation
Better understand FE model behavior by comparing static displacements with another set of static, modal, or dynamic displacements from another analysis. New error metrics help you to determine the degree of similarity between different load cases and whether static and dynamic solutions can be interchanged.
For example, you can run a comparison between results from a coarse mesh vs. results from a fine mesh model. If the coarse mesh model correlates well with the fine mesh, then you may be able to use the coarse mesh model for future applications – which can ultimately save you time in the future.
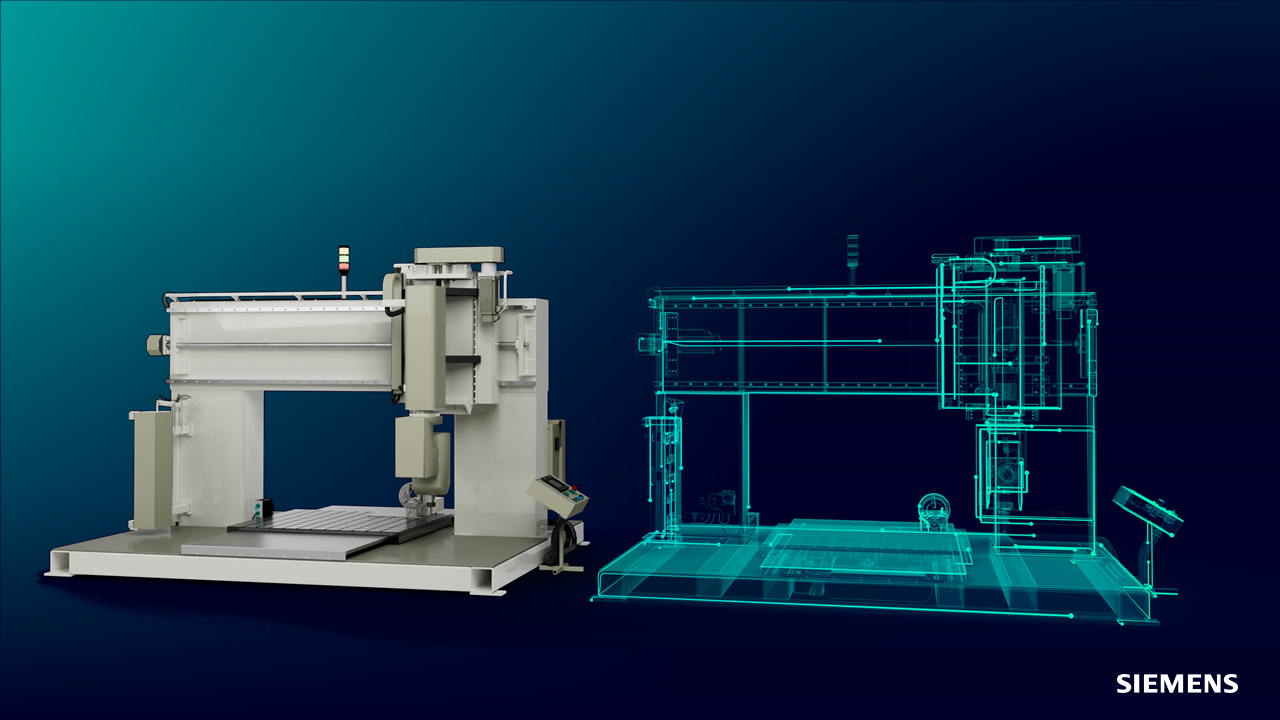
Industrial Machinery applications
Machine customers expect their machines to last with little downtime. However, machine manufacturers don’t have the time or resources to physically test their machines to the limits. Simcenter Mechanical includes new capabilities that can help you more easily predict durability without being a durability specialist.
Simcenter Mechanical can also help you better understand the performance of rotating machines and assess noise from electrical transformers.
Streamlined strength analysis
Simcenter 3D streamlines and automates strength analysis that adheres to the FKM guidelines. Simcenter 3D can compute the FKM parameters directly from your stress analysis results. After running the strength analysis, Simcenter 3D will automatically create a full report in addition to the usual results visualization and animation capabilities in Simcenter 3D. This greatly simplifies the strength analysis computation process for non-expert durability analysts.
Simulate magnetostriction and noise
Simcenter 3D can now simulate the complex multi-disciplinary magnetostriction effects that cause transformer noise. In addition, you can use these forces directly for noise and vibration assessment without leaving Simcenter 3D. This can help reduce the time needed to ensure your transformer meets the design criteria.
Generate a Campbell diagram during a nonlinear harmonic response
Campbell diagrams are used to determine critical speeds for linear rotating systems. What happens when your machine uses nonlinear bushings? You now have a nonlinear system. How do you assess critical speeds for this system?
Simcenter 3D can calculate complex modes during a nonlinear harmonic response. After the analysis, you can generate a Campbell diagram in Simcenter 3D so that you can assess the critical speeds of a nonlinear system.
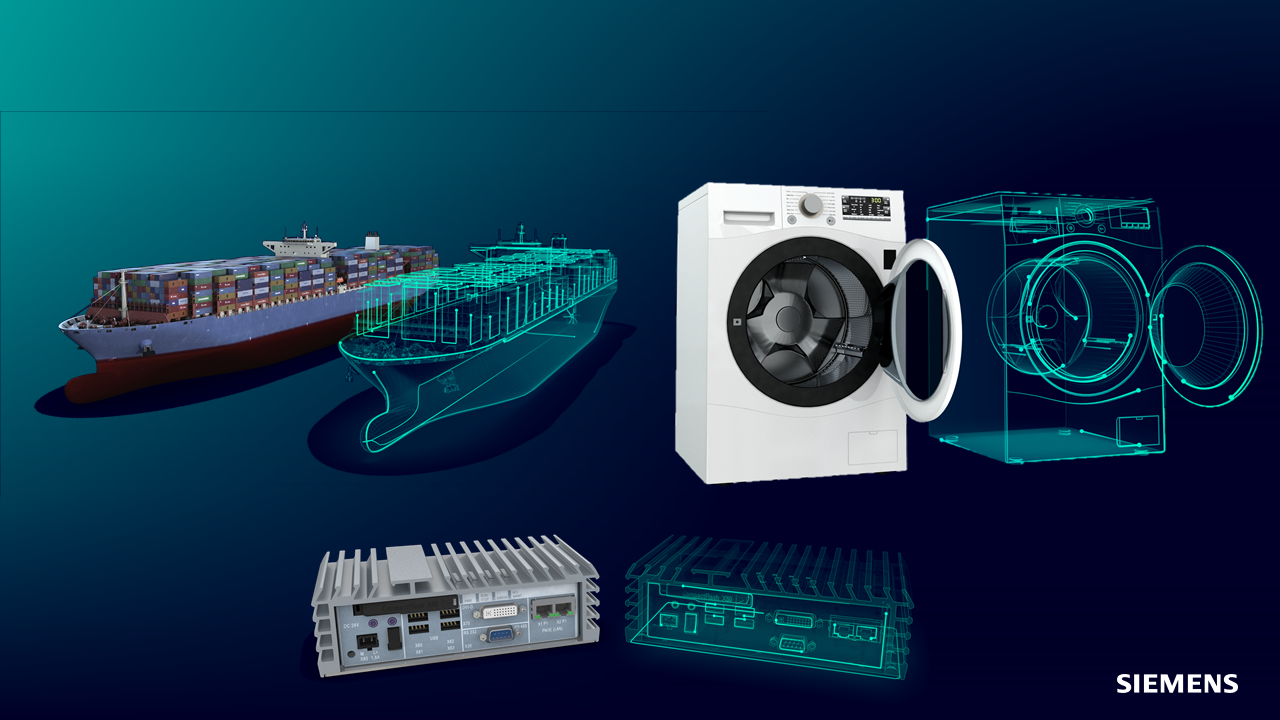
Applications across industries
Simulation engineers, whether you’re in the auto, marine, or consumer products industries, confront many common simulation tasks and processes.
New capabilities in Simcenter Mechanical can help you simulate the additive manufacturing build processes faster and easier than before as well as help you pre- and postprocess FE models more efficiently.
Voxel-based meshing for powder bed fusion
The latest release of Simcenter 3D Additive Manufacturing includes a new application for Powder-bed Fusion (or PBF for short). The advantage is that it’s very easy to use, and you don’t need to spend time creating a detailed mesh of your part. It’s using a robust voxel-based mesh in the background so that you can quickly model and simulate the PBF build process for your part. You can then get a good understanding of the likelihood that your part will be built successfully.
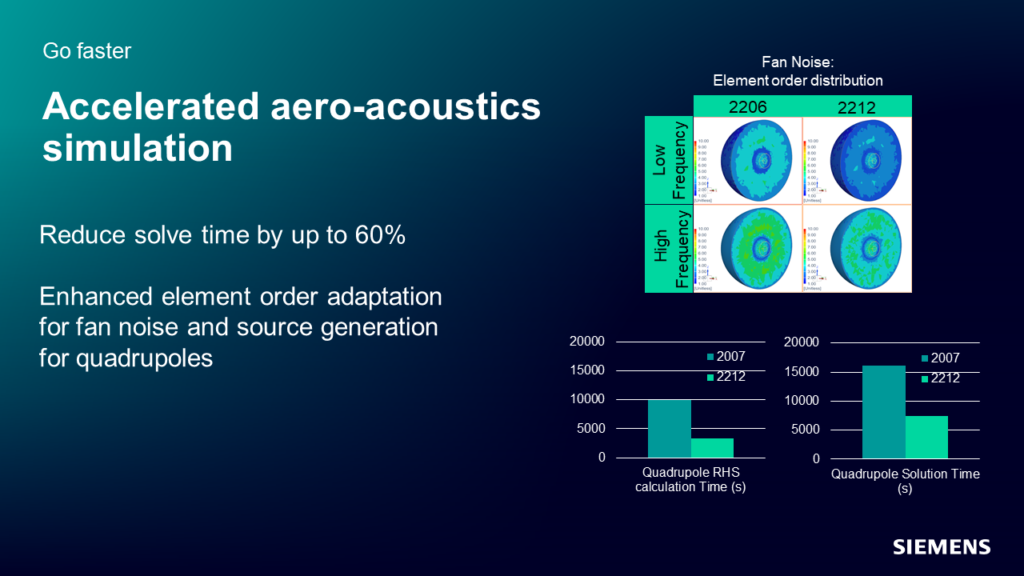
Accelerated aero-acoustics simulation
Simcenter 3D has improved solution speed for aero-acoustic simulations by up to 60%. This is achieved by giving the source elements frequency varying element orders.
Postprocess results in Remote Simulation
To help save you time, you now have the ability to review basic results of your simulation directly from the Remote Simulation interface in Simcenter 3D. That helps you decide if your simulation job ran correctly before you transfer large results files back to your local machine.
Additionally, you can also interface to other load balancing software, like PBS or LSF, as well as manage remote disk space.
Contact manager
The new Contact Manager in Simcenter 3D can help you review all the contacts, including glue connections, all under one central place in the user interface. You can also compute initial contact results in the form of contact status, penetration and gap values. This lets you easily confirm if your contacts are defined correctly in your model to accurately capture behavior
Learn more…
Leave a review – get a gift card!
Are you a Simcenter 3D user? If so, please add your perspective on Simcenter 3D to G2, an external peer review site. Your input will help others pick the right solution based on your real user experiences. Your review is valuable and will be rewarded with a gift card.
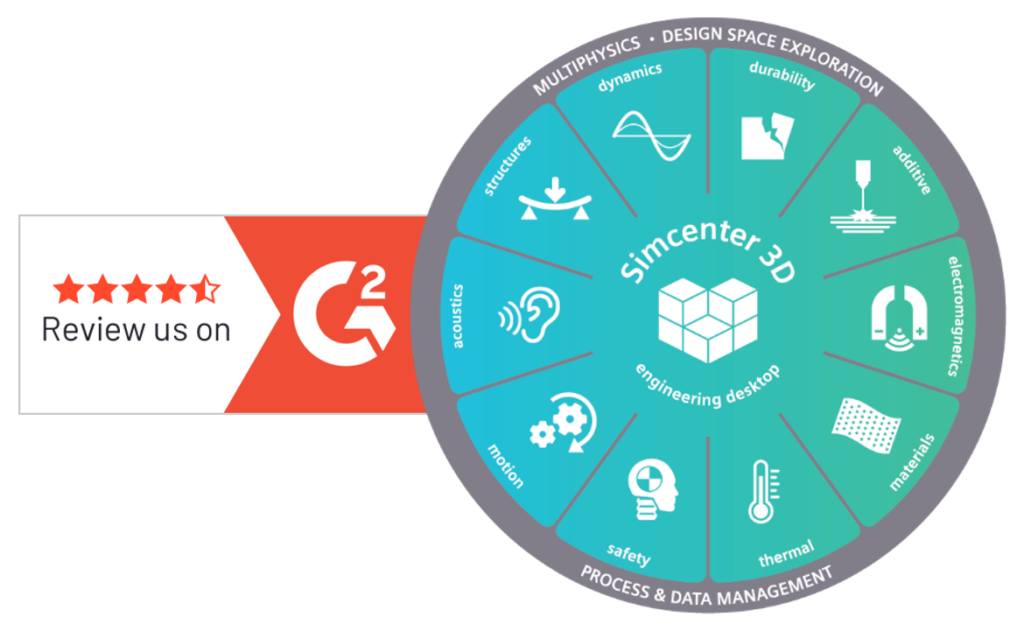