Simcenter E-Machine Design: Accelerate, innovate, and optimize your electric machine design process
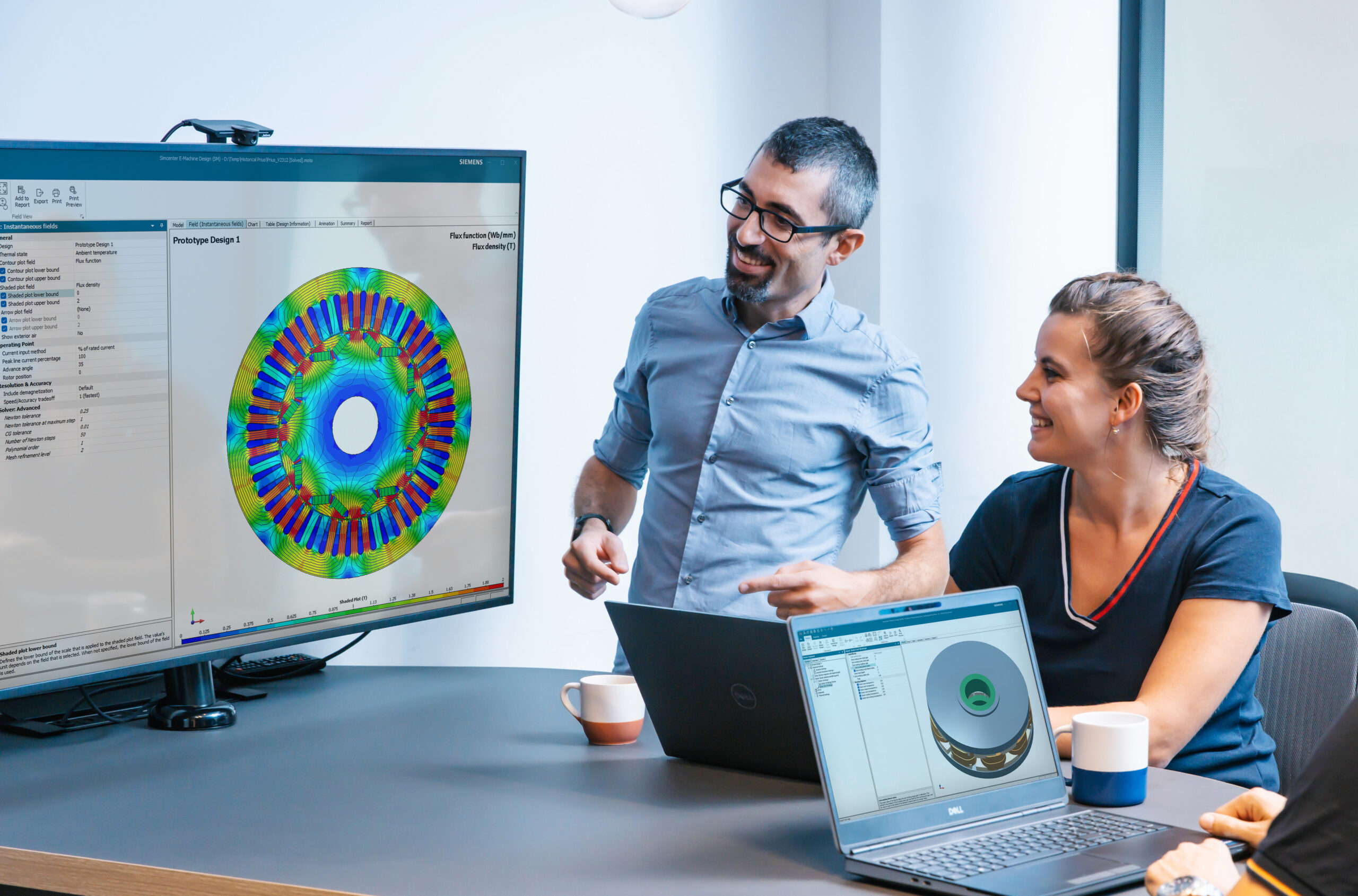
Meet Simcenter E-Machine Design software
Engineers and engineering managers often face a daunting challenge in the world of electric machine design. Product development can seem to stretch on for years, prototypes are painstakingly built and tested, and costs often soar beyond budgets. Additionally, size, weight, and sustainability goals get tighter and tighter. But now they have a solution to their problems, one that would transform their design process and propel them towards success.
Introducing Simcenter E-Machine Design software, a simulation tool that would accelerate the design process, validate designs early with multi-physics simulations, and strike the perfect balance between performance and cost. This was the answer you had been waiting for.
Siemens is proud to announce Simcenter E-Machine Design, built upon the shoulders of giants as it takes the best of Simcenter SPEED, Simcenter Motorsolve and Simcenter MAGNET for replicating electric machine experiments. Simcenter E-Machine Design is designed to connect the pieces of the electric machine V-cycle and deliver on the Simcenter vision to help companies reduce product development time from the typical 3-4 years to under two years. Imagine the possibility of skipping one or more physical prototypes!
You can’t use up creativity. The more you use, the more you have.
Maya Angelou, author and human rights activist.
When failure isn’t an option
But what makes Simcenter E-Machine Design truly extraordinary? Let’s dive into its captivating features:
First, Simcenter E-Machine Design utilizes a template-based design approach. Engineers can leverage pre-defined templates tailored specifically for electric machines and they can design hundreds of machines virtually without being FE experts. This not only slashes design time but also empowers them to think out of the box and optimize their creations.
Temperature kills motors
Toshiba motors
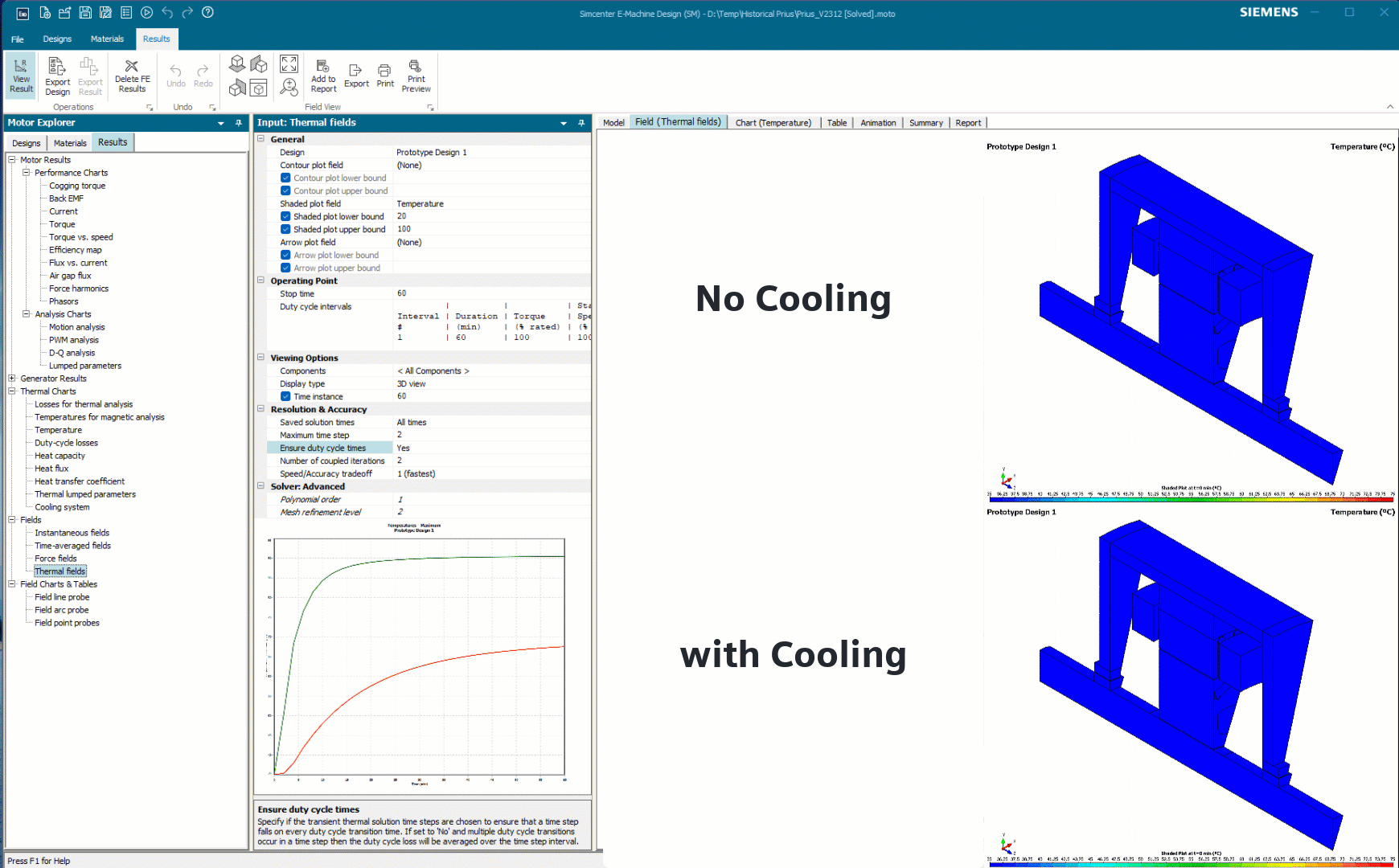
Second, Simcenter E-Machine Design unlocks the power of early multi-physics validation. Engineers can perform simulations early in the design phase, frontloading potential failure modes, and ensuring robust performance. The thermal performance of the motor takes center stage, as temperature can make or break its reliability and lifetime. As Toshiba Motors says, “temperature kills motors” and this is because knowing that a mere 10-degree increase can cut a machine’s lifetime expectations in half.
With this tool, engineers can predict and mitigate overheating issues, by running quick electro-thermal simulations in a single tool.
Don’t get left behind, when others have axial flux machines…
And there’s one more exciting part: Simcenter E-Machine Design now includes an Axial Flux machine module. This module boasts unique capabilities, enabling engineers to predict the performance of axial flux machines in seconds. Thanks to the combination of interface templates on the input side and analytical analysis capabilities on the output side, engineers can quickly harness the power of Axial Flux machines. These machines are being investigated in many sectors because the possibility of stacking them, has the potential to significantly increase performance. Users can now evaluate axial versus radial flux alternatives and prove to themselves whether higher power densities can be achieved. Many believe these machines could shape the future of electric mobility.
But the magic doesn’t stop there. Simcenter E-Machine Design allows engineers to validate the electric machine within the drivetrain by integrating with the Simcenter portfolio. Being able to do a digital integration of your components, enables you to go with higher confidence to your physical prototype stage, avoiding expensive failures.
The three examples of this integration that bring more value to our partners are:
Design is not just what it looks like and feels like. Design is how it works
Steve Jobs, co-founder of Apple, Inc.
You have everything to gain
System integration: optimizing the electric machine within the system is the only way to unleash the next level of efficiency and push your electric application to the next level. Simcenter E-Machine Design allows you to create accurate Reduce Order Models (ROMS)
which integrate into Simcenter AMESIM for a mechatronics simulation. If you are interested in an inverter-motor integration, then you can also incorporate your ROMs into Xpedition software or PartQuest software Explore.
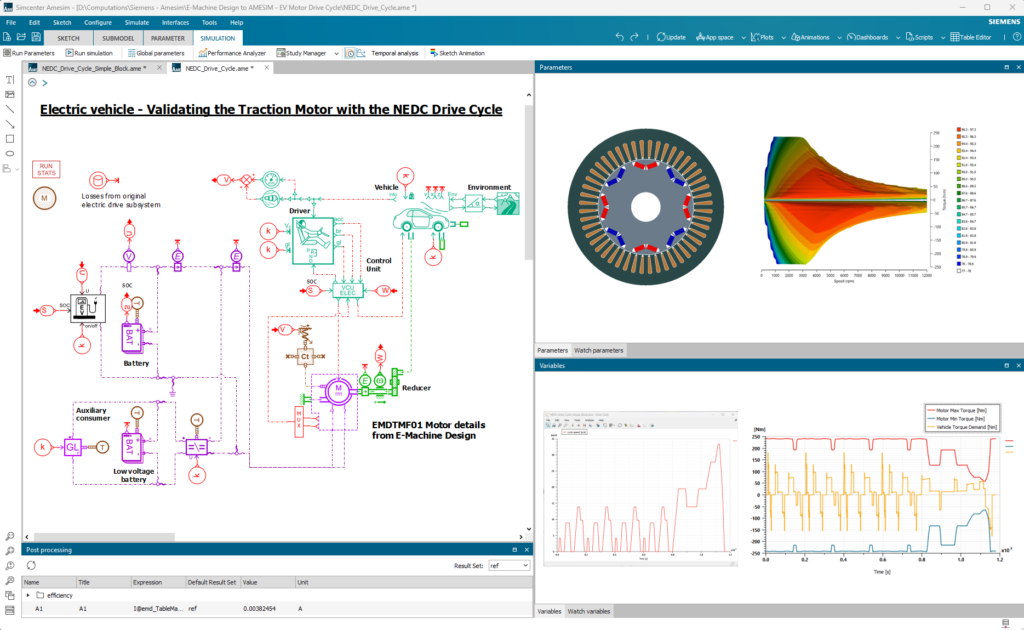
Thermal integration: to boost efficiency and performance, engineers continue to explore on more and more complex cooling strategies. The more complex the cooling, the more essential simulation becomes to validate everything works as intended. That’s why Simcenter E-Machine Design helps you leverage your model and build detailed multi-physics solutions in Simcenter STAR-CCM+, as our colleague Gaetan explained here.
Mechanical integration: in particular, validating the NVH performance of the machine, the gearbox, and the housing can be a nightmare. Classic approaches that don’t account for the integration between the electromagnetic loads and the transmission keep proving insufficient. That’s why, Simcenter helps you accurately replicate the integrated e-drive and review the system NVH. You can test and correlate your results with the physical system.
Intrigued? Deep dive into the topic with this on-demand webinar.
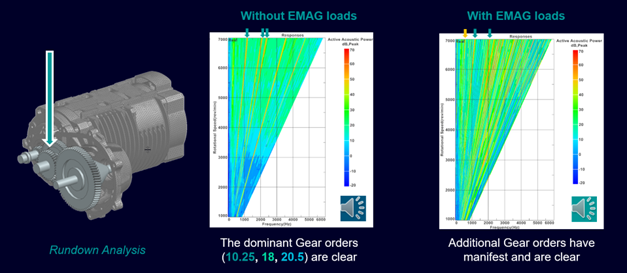
I feel the need – the need for speed!
Tom Cruise as Peter ‘Maverick’ Mitchell in Top Gun.
Are you hungry for more?
The story of electric machine design is changing at a fast pace. With Simcenter E-Machine Design as their ally, engineers can conquer challenges, accelerate their time-to-market, and create products of unparalleled quality, efficiency, and performance.
So, are you ready to accelerate? Step into the world of Simcenter E-Machine Design with this podcast (recoding is also available in the video, right) and reflect on your engineering process. Together, we can embark on a thrilling partnership and reshape the future of electric machine design.
To find out more about this new product see our webpage:
Or learn more about recent Simcenter Mechanical releases in this blog: