E-machine cooling simulation, the easy way

As a teenager, I recall how I was spending hours preparing CDs mixtapes from my favorite tracks. That was a tedious task, do you remember?
First, I had to get in my hands my CDs on which my favorite tracks were on. After that, convert each track into an MP3 file. With my few savings, I bought a CD-ROM burner on which I could burn my MP3 mixtape on a blank CD. Finally, a few hours later, I could brag around with my CD mixtape inserted into my Sony Discman D-151. Oh yeah, that was worth the effort and the learning process to get to it!
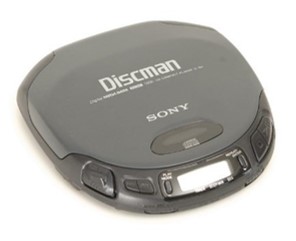
Today, you don’t have to think about it. Using your phone you just type in your favorite song into your preferred music streaming app. There you go, hit like and it is saved to your playlist, dead easy.
E-machine cooling designs: work seamlessly across simulations domains
Easily cope with complexity of e-machine cooling simulation
The reason I recall those teenage days is that I can see some similarities in some of the workflow which are used to perform an e-machine cooling simulation. A bit of a stretch I must acknowledge, but if you think about it, there is quite some effort involved.
Typically, we assign the e-machine cooling simulations to the thermal CFD (Computational Fluid Dynamics) engineers. However, they are not too familiar with these drivetrain components, nor are they familiar with the main physics phenomenon that governs their behavior, electromagnetics. So, it is quite often that CFD engineers struggle to get a clean CAD of the machine itself.
It may come from various sources. For instance, core e-machine geometry comes from one source and the cooling system geometry comes from another. Then, they must get the machine definitions, materials properties, etc. Finally, CFD engineers need to know the conditions in which this machine must run.
As for the cooling analysis part of it, for the e-machine, the key element is the losses coming from the machine in operations. Again, how to get this data? CFD engineers usually can go back to their colleagues, the electrical engineers, to get either:
- a rough estimate, uniformly applied to the entire machine
- or a one-off loss distribution field, which you map to the e-machine mesh.
Stay integrated in one simulation ecosystem
We know how CFD engineers like to go above and beyond, to predict the various local temperature hot spots, optimize the cooling device efficiency, and analyze the machine behavior in varying conditions. In order to achieve this, they really need an interactive loss prediction model, which only comes with an electromagnetics analysis coupled to the thermal solution. But, yet again, CFD engineers have little knowledge of this physics domain.
How to set a proper simulation with it? What information do we need etc?
There is quite some effort as we can see. What can we do to simplify this process, and enable CFD engineers to access more advanced e-machine cooling analysis?
Therefore, in Simcenter, we have worked on that, not as easy as creating your playlist on your phone, but close!
E-machine cooling simulations file import: an easy-to-use workflow
Go faster – Import e-machine design files from Simcenter SPEED & Simcenter Motorsolve
This brings me to introduce you to a new workflow to address e-machine cooling simulations. We call it the:
“Simcenter STAR-CCM+ e-machines performance workflow”.
It’s all about re-using design work already done by e-machine specialists and passing it on in a simple action to CFD engineers.
Within Simcenter, we are lucky to offer two of the best e-machines design tools, Simcenter SPEED and Simcenter Motorsolve. This is where the electrical engineer will design the details of the machine, choosing its type, parts, dimensions, materials, and machine conditions. All the details are there.
What if we could simply import these designs including all the details into Simcenter STAR-CCM+ in a straightforward process?
This is what the new workflow performs. With Simcenter STAR-CCM+, as a CFD thermal engineer, you can now import a machine design file from either Simcenter SPEED or Simcenter Motorsolve.
The workflow then takes it from here and automatically performs the following actions:
- Reads in the geometrical details of the machine and build two CAD bodies using Simcenter STAR-CCM+ CAD capability
a. One that is going to be used for the Electromagnetics simulations
b. And another one for the thermal/fluid simulation - Organizes the various parts with relevant names
- Imports machine materials data and machine conditions so they can be used to finalize the physics setup and boundary conditions.
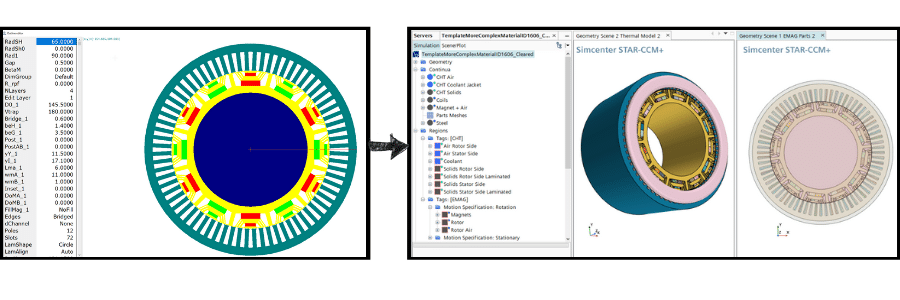
to the coupled magneto-thermal-fluid model in Simcenter STAR-CCM+ on the right
Model the complexity – Couple electromagnetics with conjugate heat transfer simulations
Great, in a few clicks you can get the machine geometry in, simple. Plus, to perform a coupled magneto-thermo-fluid simulation, it sets a geometry for the electromagnetics and one for the thermal solution.
However, you still have to set up the electromagnetics physics at this point… Quite some effort for thermal engineers. On the other hand, we have enabled that workflow into a template simulation file. The physics is already set. And, in most cases, that setup is going to be always the same.
That means, now, if I run that same import process into my template simulation file, it generates the geometries, reads in the materials and machine conditions to set them on the pre-defined physics. You’re all set! You have a ready-to-run magneto-thermo-fluid coupled simulation to perform your e-machine cooling analysis.
E-machine design case study
Perform a cooling analysis of a BMW i3 e-motor
Now, let’s see how this applies to the following case study.
Objective: perform a cooling analysis of a BMW i3 e-motor, using a water jacket cooling device. We have collected the information on the machine design and performance measurements from an ORNL study (published in the 2016 Annual Progress Report for Electric Drive Technologies Program). We use this information for the setup of our simulations.
It starts with the machine design in Simcenter Motorsolve: we define the BMW i3 e-motor.
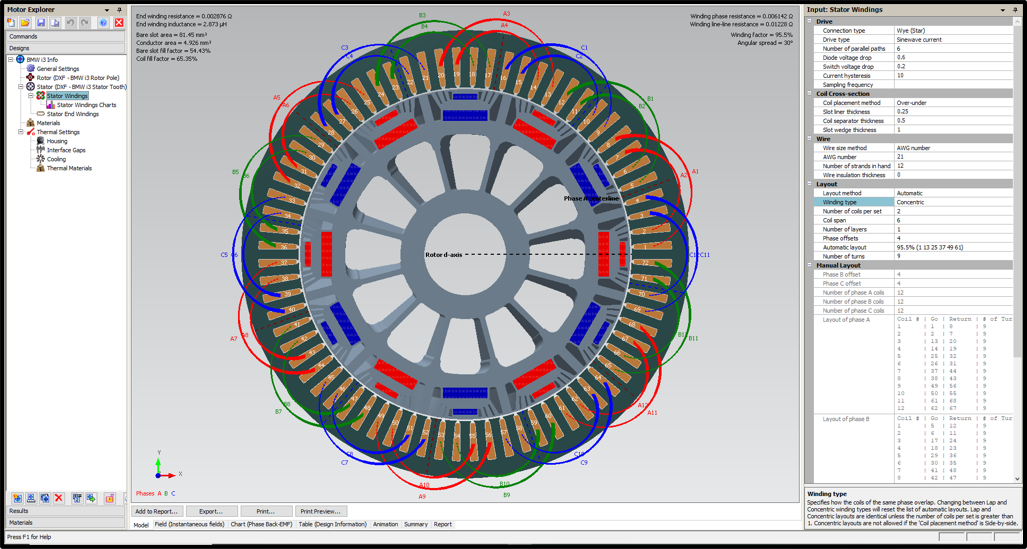
In a few clicks within Simcenter Motorsolve, the user can package this design into a single file that we can export to Simcenter STAR-CCM+. A feature of it is also to include stepped skew to capture such detail in electromagnetic and thermal simulations.
From there, using the workflow described above, the e-motor design is imported into a template simulation file, and then automatically sets the geometry, and physics for the e-machine cooling simulation.
All the details of the import process can be found in this Support Center knowledge base article.
Explore the possibilties – Cooling performance assesment
Once ready, let’s show you how you can run this simulation to analyze the machine cooling performance. We will consider the three following cases:
- A single e-machine load point simulation with a coolant flow rate of (4l/min) on the cooling jacket and an initial temperature of 20°C
- This uses and increased phase current level and increased coolant flow rate (6.5l/min)
- Again, the phase current level is increased further but keeping the coolant flow rate the same.
The objective is to define the right flow rate to obtain the proper distribution of coolant along the jacket channels spiral.
We then obtain the following results summarized in the table below:
1 – 400 A, 4 l/min | 2 – 500 A, 6.5 l/min | 3 – 600 A, 6.5 l/min | |
Magnet Temperature [°C] | 69 | 81 | 102 |
Winding Temperature [°C] | 60 | 67 | 81 |
Stay Integrated- Connect electrical and CFD thermal engineers together
We have seen the capabilities this workflow offers, a straightforward process to connect the electrical engineers and the CFD thermal engineers together.
Now, we know we cannot simply import our favorite Spotify playlist into our Apple Music account. With Simcenter however, we are already looking at how we can go beyond the import of designs from Simcenter SPEED and Simcenter Motorsolve!