What’s new in Simcenter SCADAS RS 2306
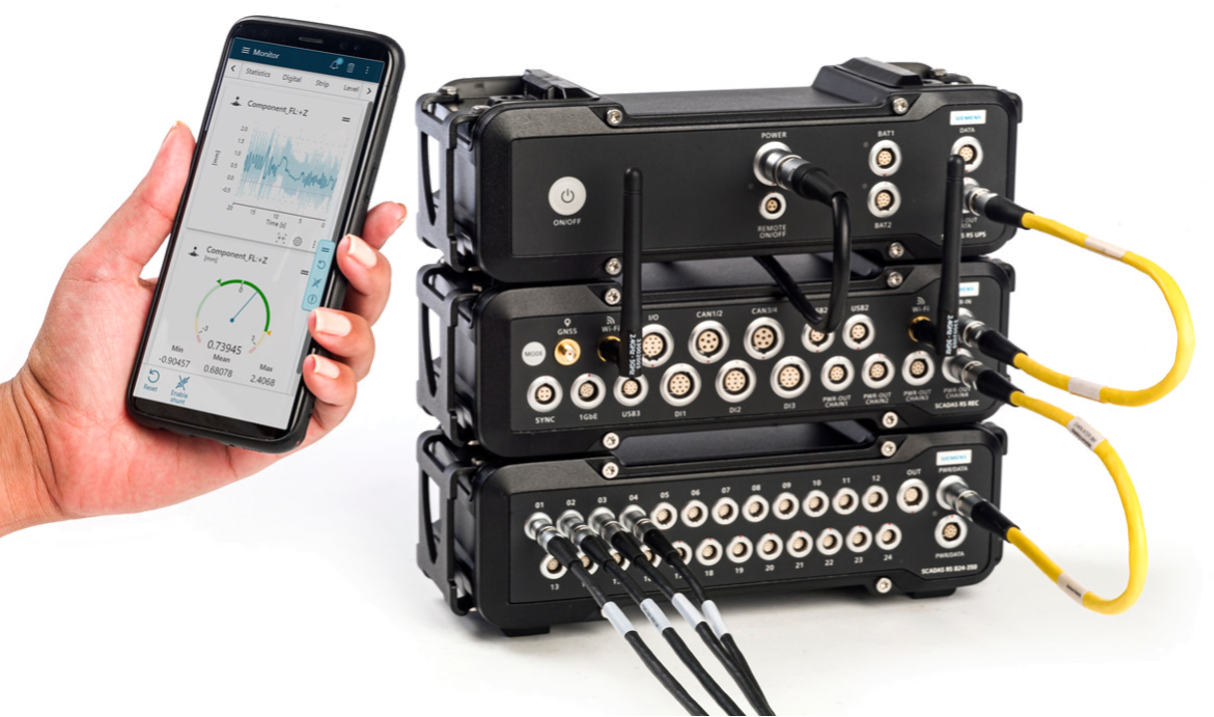
The Simcenter SCADAS RS, since its introduction to the market, has extended our hardware portfolio with innovative data acquisition capabilities.
- A rugged design with IP 66 and 67 ratings, large operating temperature range, and exigent shock and vibration specification.
- A distributed system across the test object with safe power management thanks to the UPS unit.
Simcenter SCADAS RS is the perfect solution, giving us access to the off-highway industry for Load Data Acquisition: Those measurements require a large variety of different sensor types. Strain gauges with full, half, or quarter bridge instrumentation, string pots, DC accelerometers, rotary or linear encoders, thermocouples, pressure sensors, and flow meters, just to name a few.
One more important thing to remember: every Simcenter SCADAS RS system is delivered with all required data collection software without additional cost. Each RS unit has its embedded WebApp. With the software included in the price of the Simcenter SCADAS RS hardware, users have a complete set of modern and performing tools managing a complete measurement campaign from the test preparation to the final data report. Some customers will also use the tool set to export the data for additional processing within in-house or third-party software packages. We of course recommend our customers to invest in Simcenter Testlab Desktop and pack of Tokens instead. Testlab Process Designer, with Durability and other processing libraries, offers them a more efficient solution avoiding data transfers and conversions.
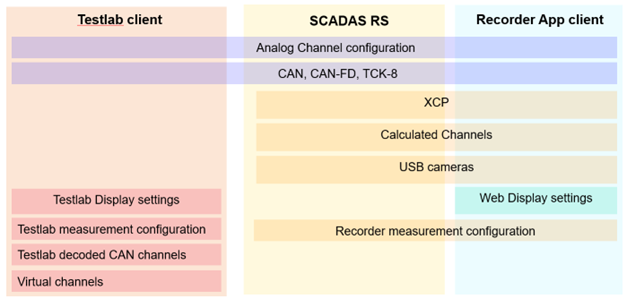
The heavy equipment industry market will immediately recognize how Simcenter SCADAS RS answered their needs. For them, a rugged system surviving heavy rain and mud projection is mandatory for any measurement campaign. On top, Simcenter SCADAS RS offers them the opportunity to distribute the different units across their very big machines. With CAN J1939 and the full unattended acquisition support, we are ready to systematically target all agricultural, construction and mining equipment manufacturers in the world.
What’s new in 2306
New hardware units
U12-E
The existing U12 unit is a universal unit, with sample rate up to 48kHz, supporting a large sensor set, including channel-to-channel isolation. The U12-E is an alias-free bandwidth extension to 20.7 kHz of the U12 unit, thanks to an additional Sharp FIR filter that blocks any alias already at Nyquist frequency
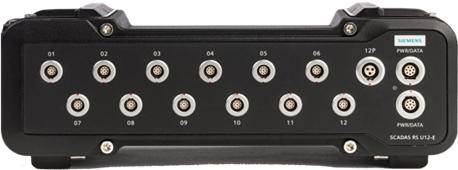
TC20
TC20 is a universal and high-density channel unit for 20 thermocouple sensors, supporting types K, J, T, B, E, N, R and S including an on-bard linearization for each type. It’s also equipped with an OUT connector for road-to-rig over EtherCAT bus with ECAT unit. Accuracy is better than 0.1%
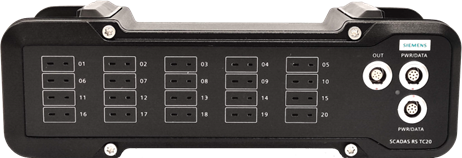
ECAT
Existing ECAT unit comes with more functionalities in Simcenter SCADAS RS Recorder app. It adds channel information automatically to the ENI (Ethercat Network Information) file. CAN-OPEN can also be used to automatically setup device settings in the Controller.
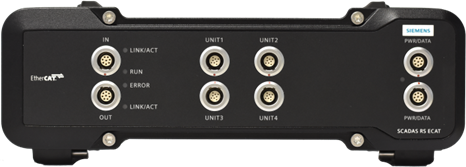
DI
Our current DI unit extends Simcenter SCADAS RS with 9 additional pulse inputs and 4 additional CAN input. The functionalities available on the DI’s inputs are the exact same as for the corresponding inputs of the REC unit. Most of our typical users were using CAN, or more recently CAN-FD to document the NVH or Durability measurements with a few signals available on the vehicle bus. Digital data becomes an integral part of the measurement campaign objectives.
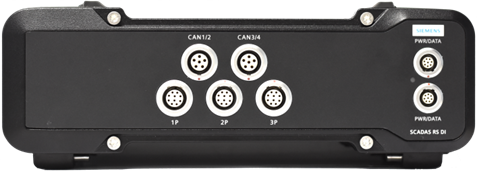
New functionalities
USB camera support
Document your measurement with up to 2 Cameras on REC, up to 30 / 60 fps including audio.
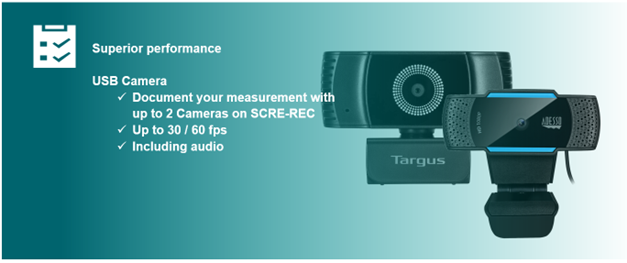
TEDS class I
Implemented read TEDS in U12-E, U12 and S24 for ICP sensors.
Calibration
New Sensitivity model added (Slope & Offset), Strain (only for Bridge conditioning), calibrate multiple sensors at once, e.g. flip call of a set of DC accelerometers, and AC calibration
Multi-client access
Robustness improvements: the client performing a measurement takes an automatic lock (no configuration changes can be made in a client while at least one client is recording data). Testlab client will break the connection if the hardware is in a state it cannot deal with, and will switch to Off-line mode.
Simcenter SCADAS RS Recorder App
It is now possible to also do the channel setup directly from the channel grid. This modification also includes more interactivity with MS Excel, e.g. export the complete or a subset of the channel list to MS Excel. Overlay of time traces: On-line (monitoring) and off-line (track-side validation), both for identical units as for mixed units (auto-scaled), up to 4 traces, cursor and Legend (collapse/expand), strip view and Custom page, mixed units support and cursors, template auto-backup every 3 min, download and export runs to your PC or USB.
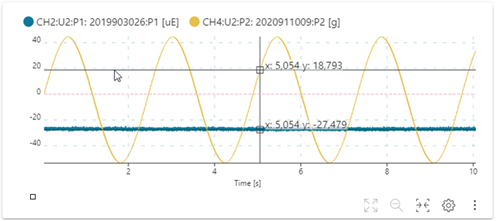
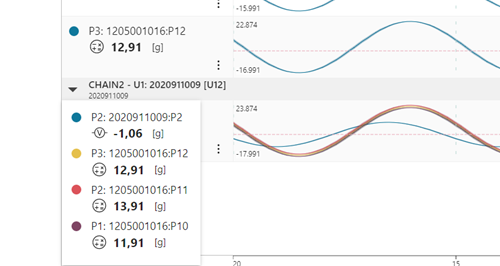
Simcenter SCADAS RS Configuration builder
Test engineer assembles virtual Simcenter SCADAS RS configuration and saves on PC to load & use it later in Testlab Neo. During the preparation phase, there is no need anymore for the physical data acquisition system.
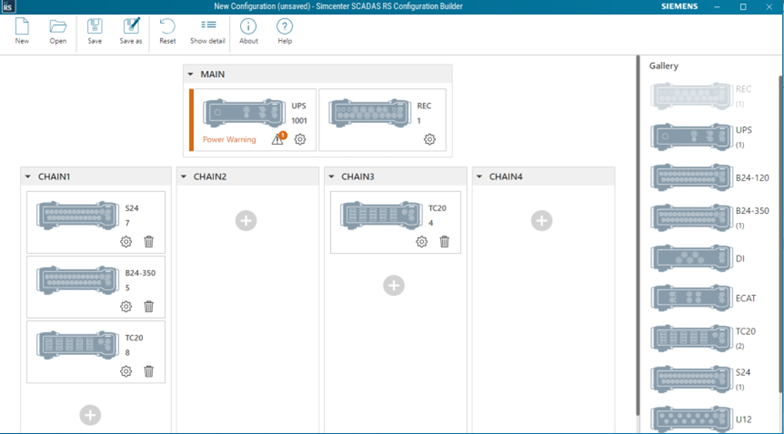
Digital Buses
We come with several functionalities regarding vehicle buses and digital sensors.

Configure completely CAN acquisition
Including CAN high speed, TCK8, new XCP. Overall usability improvement for Configuration, accessibility of information, validation & troubleshooting. The only remaining step to be completed in Testlab (offline) is to create a scdbd file from dbc to embed the Testlab Unit system properly and transfer this consequently to the hw, as well as a favorite selection if required. This step is done only once normally for each new dbc file. Once the scdbd files are stored on the REC unit, they can just be selected from the interface.
Activate and Deactivate Digital channels directly from the interface
It is now possible to automatically compile the proper OBD2 request for specific signals, e.g. Engine RPM or Vehicle Speed, by using the related new context menu when preparing a Simcenter SCADAS RS configuration. New dedicated properties for SAE J1939 CAN messages are now available, namely the PGN (parameter group number), the source address, and the destination address, which are useful for retrieving the required messages as well as understanding the source and destination of the data. New can merge functionality can be used to combine two CAN configurations (and related database files), to create e.g. incorporate signals from a new sub-system of the machine we are working on. This unique configuration can be assigned and measured on a single CAN bus.
The number of CAN channels that can be decoded on the Simcenter SCADAS RS REC and DI units has been increased to 32 per CAN bus. The Digital Bus page under the Measure tab has been enhanced with the possibility of promoting view & forget signals to Digital channels: Up to 80 (Up to 32 Digital Channels + Up to 48 pure view & forget) signals can be visualized in both Statistics and Strip format.
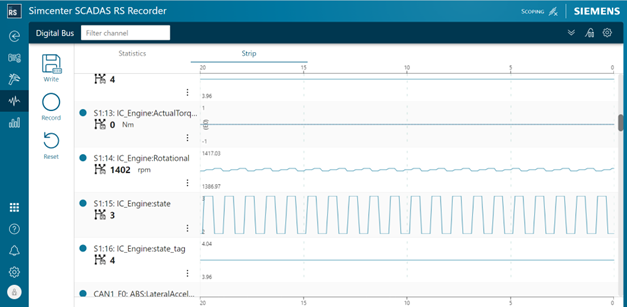
XCP over CAN
XCP is the acronym for Calibration Protocol. This protocol can be seen as a debugger for engine control units, ECUs. We got many requests over the past for XCP over CAN from NVH and Durability customers who needed to access parameters of their ECUs for documentation.
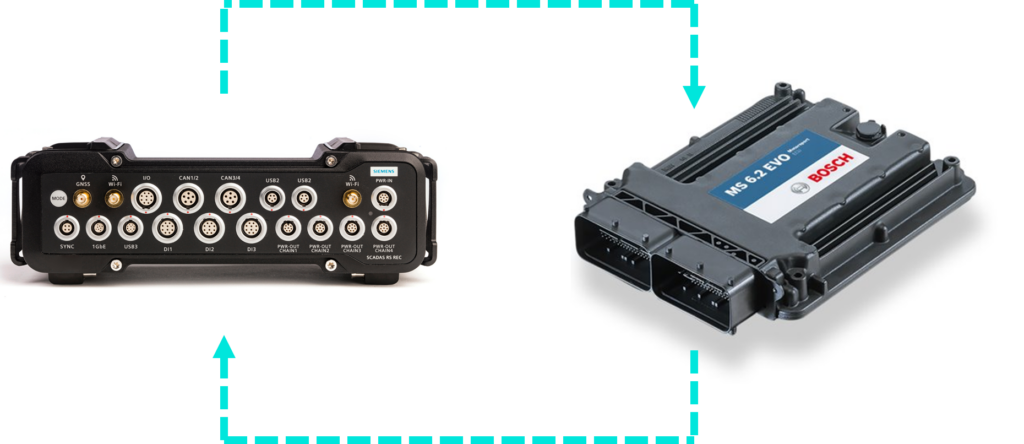
Load database files
Scdbd for standard CAN, A2L for XCP.
Testlab Neo – durability processing
Export data
Export of measurements directly into HBK’s nCode Glyphworks s3t format. Reading of nCode Glyphworks s3t is also available. Support for reading/writing was also added to Simcenter Tecware.
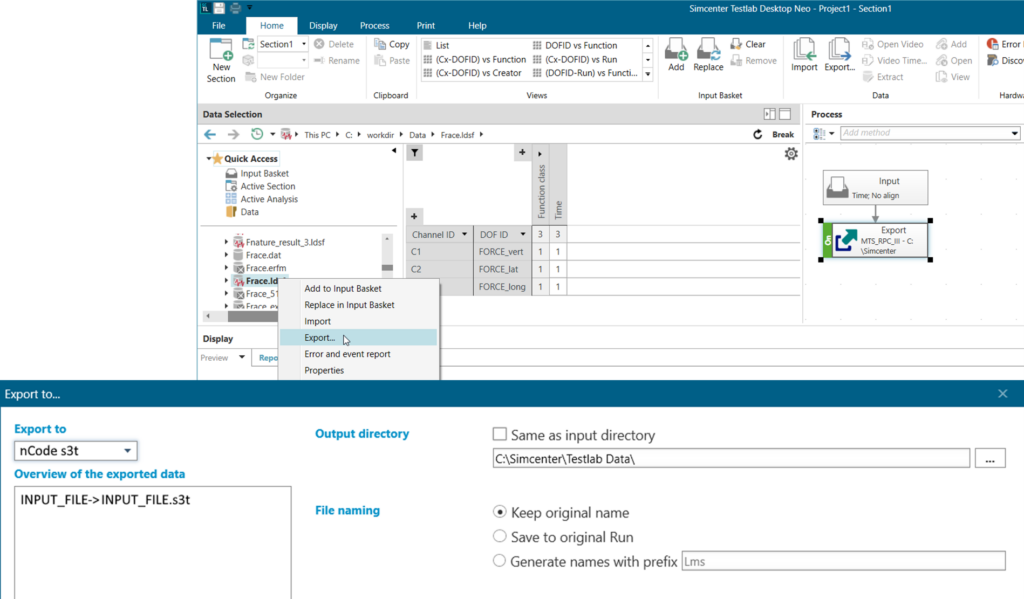
We have integrated the export directly into the native time data format of nCode Glyphworks called “S3T”. It’s available in Simcenter Testlab Neo both interactively, starting from files, runs or sections in the Navigator, or as a method inside Process Designer for automation of the export.
Time at Level 2D
Now with the Time at Level 2D, you can also use two channels as input, and you get a matrix with the occurrences or total time spent in each combination of values from the two channels. This can be used to determine how long certain loading levels occur and under which conditions. E.g. how long is the driver applying certain torque levels at which speed. The Time at Level 2D allows to additionally calculate the revolutions instead of occurrences or total time.
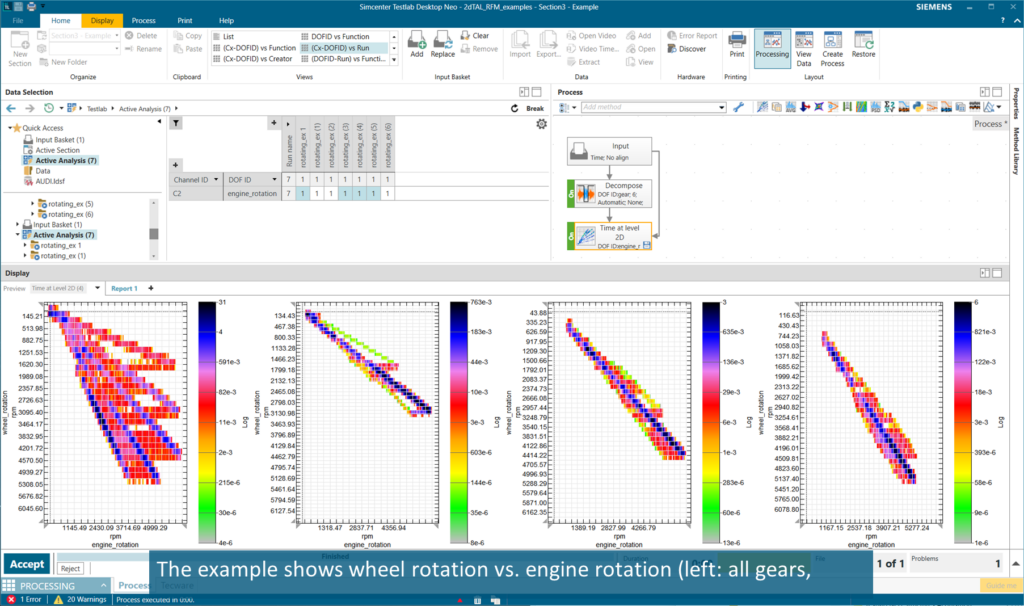
Interactive Analysis – Critical Plane Approach
For Rosettes: added CMs for variable/user-defined angles. Combined Method that automatically calculated the angles from 0° to 170°. For some cases, users want to specify one specific angle, e.g. because they know from the geometry of their component that this is an angle with severe impact on a notch.
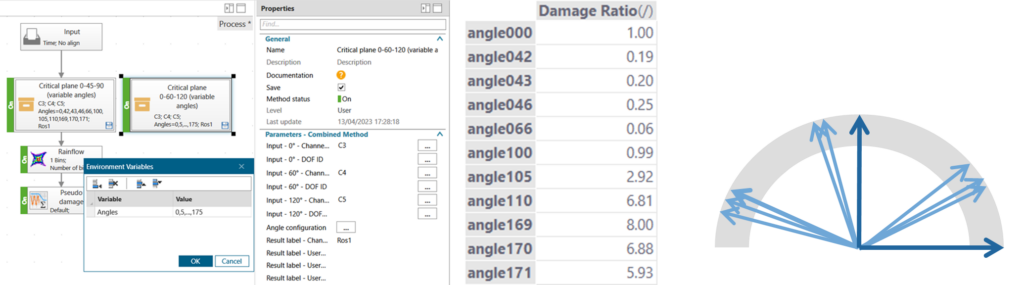