Executable Digital Twin: XiL testing with Simcenter Testlab RT 2306
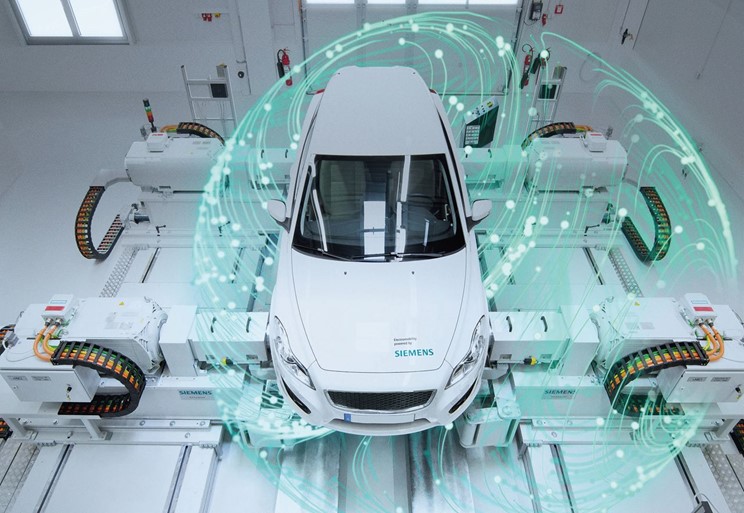
Hardware-in-the-loop (HiL) testing is a well-known approach to develop and test control software running on electronic control unit hardware (ECU). The ECU is interfaced with virtual worlds for emulating realistic environments. This is done in the early design stages when the final system, such as a car, in which the electronic control unit hardware will be integrated, is not yet available.
Can you imagine extending the HiL approach to the testing of systems that involve more than just electronic control unit hardware? This approach can be referred to as the XiL approach. It offers design engineers the capability to speed up their sub-system functional performance testing and validation in a lab environment.
Let’s take a look at how Simcenter Testlab RT facilitates the testing of physical systems “in-the-loop” on test rigs and simulators using Executable Digital Twins (xDTs).
Why using XiL test rigs?
The final design and performance validation in the field for most physical subsystems can only happen after the complete system in which they function is assembled. However, even then, it is time-consuming, costly or even dangerous to reproduce during the physical test program the variety of operating conditions the system might encounter during its lifetime.
Simcenter Testlab RT provides a powerful software and hardware real-time environment that allows a physical system to be connected to virtual representations (aka xDTs) of its operating environments. For example, a physical braking system or a physical powertrain system can be tested as if they were operating in any of the vehicle variants it will be used in. The XiL approach thus shifts the physical system test program earlier in the development cycle by reducing dependency on the availability of other physical systems. It also supports the evaluation of many system-level variants for a wide range of operating loads. The XiL tests will reveal potential issues far earlier in the overall system development program for the system-under test. As Simcenter Testlab RT handles the xDT sensors as if they were physical sensors, issues with the other components in the system might even be revealed.
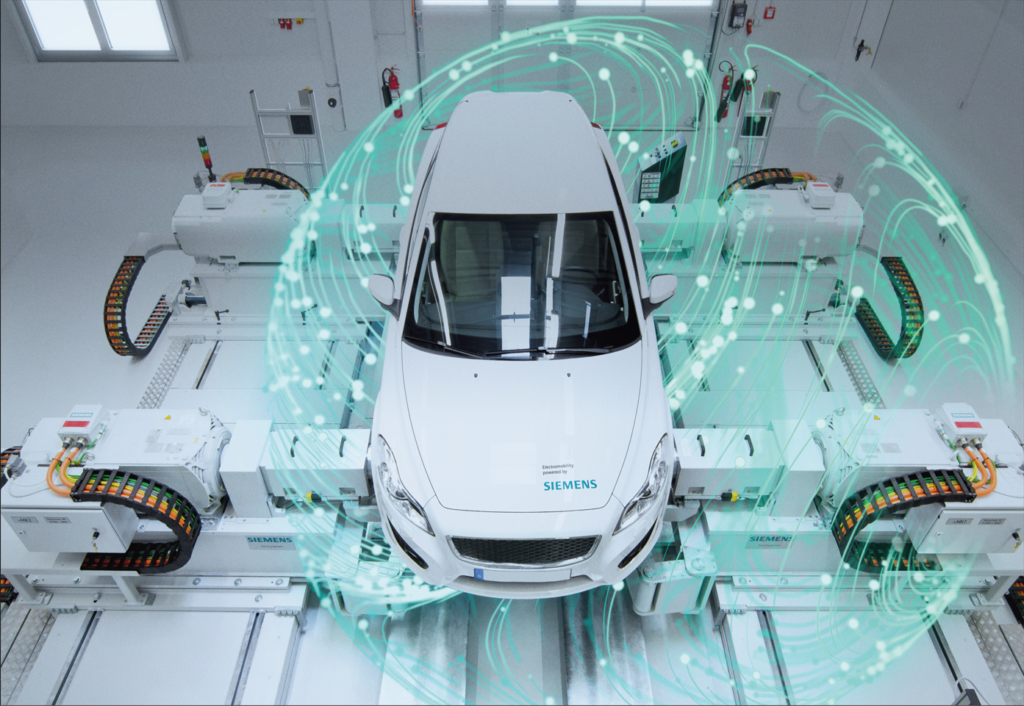
Example of XiL test bench including physical/virtual coupling
XiL testing for every test engineer
Setting up a XiL test mostly requires expert engineers to collect & reformat the simulation models and spend some programming time to embed them in the test configuration. Often, using models from release versions of multiple simulation & control software vendors leads to incompatibilities in the final configuration. These issues jeopardize the test program timing.
Therefore, Simcenter Testlab RT provides a zero-programming alternative for the XiL setup, through a feature-rich and intuitive web user interface.
Simulation and control models from multiple release versions of Simcenter Amesim, Simcenter 3D, MathWorks Simulink®, and other simulation software vendors can easily be uploaded to the Simcenter Testlab RT library and used as part of test configurations. Different formats for these simulation models are supported such as functional mock-up unit (FMU) according to the functional mock-up interface (FMI) standard and native model formats.
Load inputs for the XiL test program can come from file recordings from Simcenter Testlab (= LDSF file format), from real-time digital buses and field buses, or they can be directly embedded in the simulation models.
To make things even easier, the web user interface language can be changed in a few clicks to maximally accommodate the user’s needs.
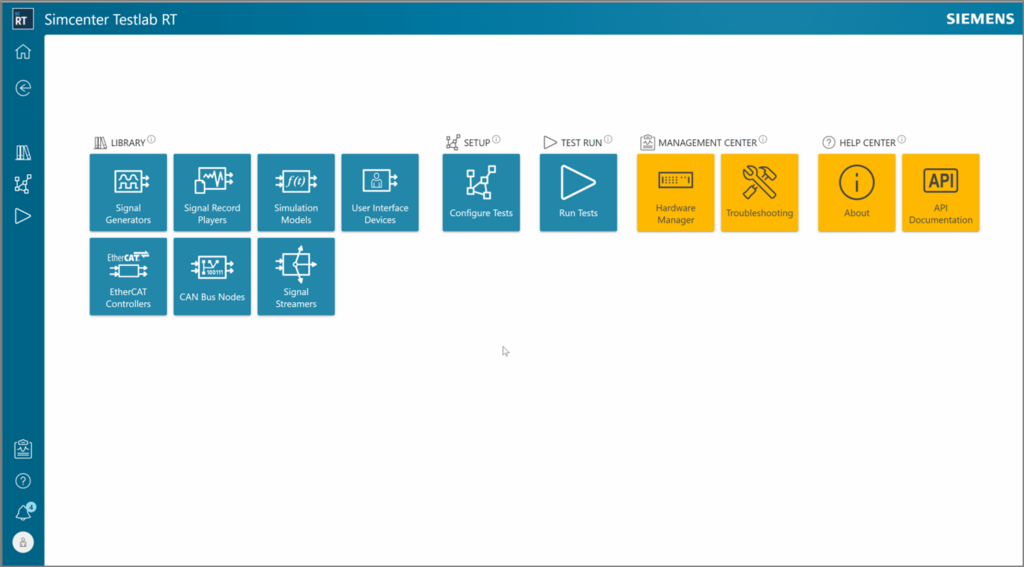
Simcenter Testlab RT intuitive web user interface
Scalable Computational Performance
Depending on the computational complexity of the simulation models, a suitable Simcenter Testlab RT hardware platform is selected from our catalog to be able to run them in real-time. For the most advanced use-cases, the sheer performance of Simcenter Testlab RT software and hardware platforms allows co-simulating multiple complex full order simulation models (FOM) in hard real-time. In case the model complexity would exceed the systems’ real-time performance, a model order reduction (MOR) step can be applied during the creation of the simulation model to reduce the computational complexity.
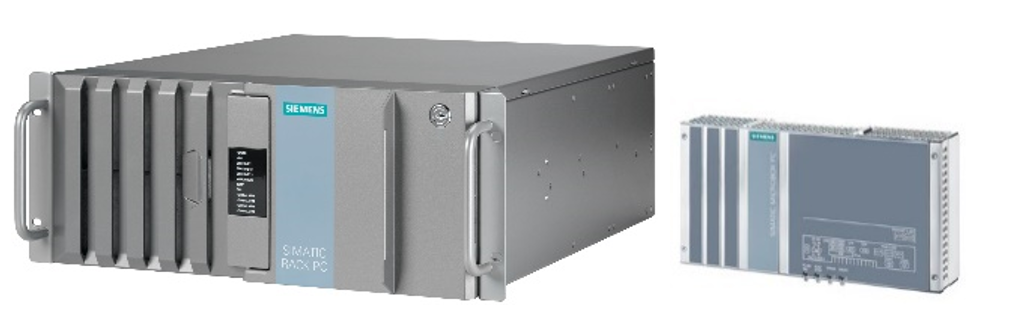
Simcenter Testlab RT scalable hardware platforms
Creating a new physical and virtual world
Simcenter Testlab RT seamlessly connects physical systems to virtual ones in real-time using analog I/O’s, digital buses such as CAN and field buses such as PROFINET and EtherCAT. The analog sensor data can be retrieved in real time from physical sensor conditioning units such as Simcenter SCADAS. This creates a performant and accurate coupling between the physical parts and the virtual parts of the world, thus enabling full system testing.
Simcenter Testlab RT can also be integrated with the user interfaces, control & automation systems of test benches and simulators.
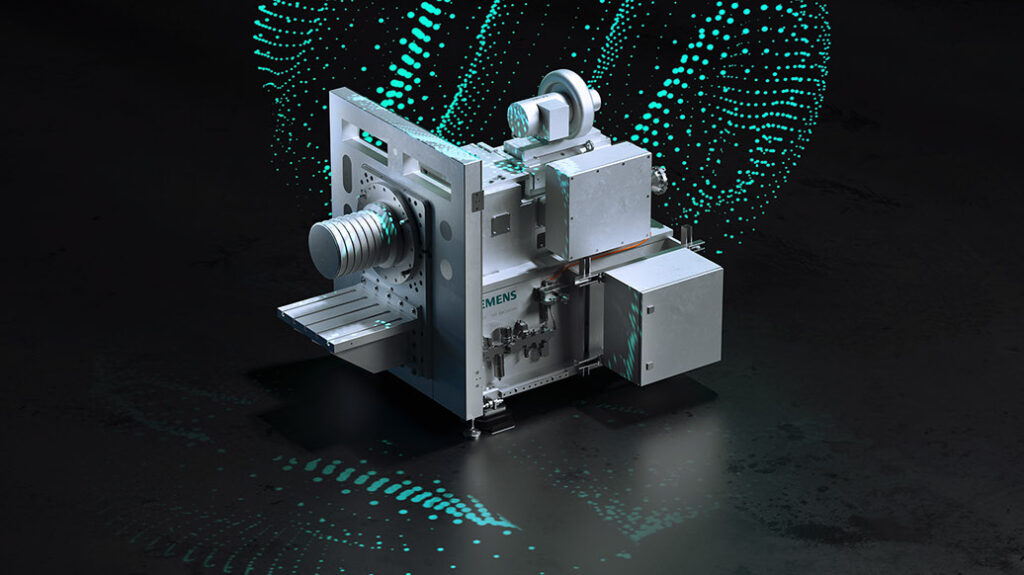
XiL e-motor test bench
Sensing the new physical and virtual world
Simcenter Testlab RT synchronizes its clock using the IEEE-1588 Precision Time Protocol (PTPv2) to the clocks of hardware systems used for sensor conditioning and data recording, such as Simcenter SCADAS. This allows sensing both the physical part and the virtual part of the world in a coherent manner. Physical and virtual sensors can be monitored using Simcenter Testlab Engineering Displays, stored using Simcenter Testlab Time Data Acquisition, and processed using Simcenter Testlab Process Designer. This provides immediate insight into the system-under-test behavior.
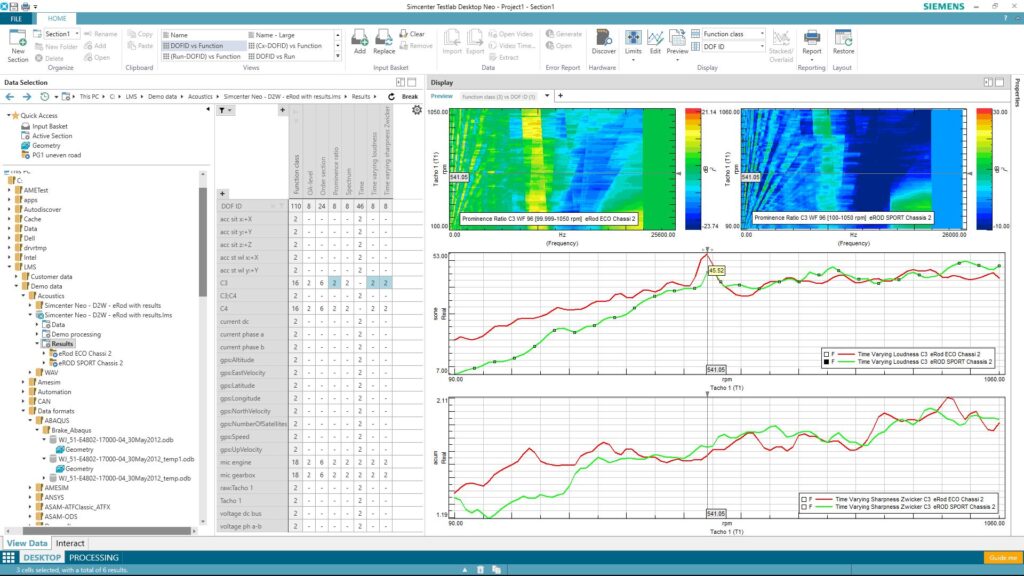
Advanced engineering visualization in Simcenter Testlab Desktop
Fast turnaround
Reconfiguring an XiL test bench for a new test configuration often takes the best part of the work shift, if not more. The intuitive web user interface of Simcenter Testlab RT ensures that defining and activating configurations is a matter of minutes, not hours. When the same physical component is to be tested and validated for use in different systems, multiple test configurations can be defined upfront. Switching between these configurations at the bench is done in a few mouse clicks, ensuring the downtime of the bench between tests is virtually zero.
Flexible test automation
Simcenter Testlab RT comes with an Automation API (Application Program Interface) that can be used to easily automate main actions on the real-time platform from any external system. It allows changing test parameters, selecting the active test, arming, starting, and stopping it, and parametrizing test parameters, such as the initial states of vehicle models. Of course, tests can also be fully parametrized within Simcenter Testlab RT using the web user interface.
Workflow
Simcenter Testlab RT provides the application software and real-time hardware to cover all activities in setting up and running an XiL test:
• Deploy simulation models (xDT’s) into the library of the real-time platform via the web interface or using the Automation API
• Deploy and configure any pre-recorded signals to be used as simulation model inputs
• Connect all hardware devices required by the application to the real-time platform
• Clock-synchronize the real-time platform to external systems, if required by the application
• Create Tests via the web user interface, add components (signals, simulation models, hardware devices…) and connect them to each other, and set up the visualization dashboards.
• Run the Tests from the external main controller using the Automation API or directly from the web user interface.
In a nutshell
Simcenter Testlab RT is a powerful and versatile real-time platform, providing hard-real time, scalable performance, easy-to-use co-simulation capabilities to virtualize the operational environments of physical systems-under-test.
A feature-rich and intuitive web user interface makes XiL testing accessible to every engineer, by offering a zero-programming experience.
Combining Executable Digital Twins to create the complete virtual operational environment is made easy by supporting multiple release versions of many simulation software solutions.
Support of many real-time communication interfaces and a well-documented Automation API ensure easy integration when upgrading existing test rigs with XiL capabilities or when developing entirely new advanced test benches.
XiL testing has never been so accessible and effective.