Unlocking the secrets of hydrogen combustion engines: A fascinating look at system simulation techniques
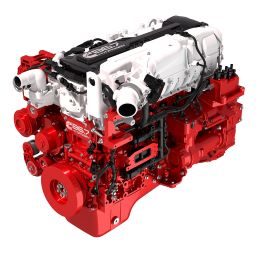
The impact of greenhouse gases on our environment has been a growing concern over the past few decades. The rise of industrialization and the increased use of fossil fuels have led to an increase in the concentration of greenhouse gases in our atmosphere. These gases, such as carbon dioxide (CO2), methane, and nitrous oxide, trap heat in the atmosphere and contribute to global warming, which has a devastating impact on our planet.
One of the most significant contributors to greenhouse gas emissions is the transport sector. According to the International Energy Agency, the transport sector accounts for around 24% of global energy-related greenhouse gas emissions. This includes emissions from cars, trucks, buses, airplanes, and ships. With the continued growth of the global population and the increasing demand for transportation, it is essential that we address the environmental impact of the transport sector if we are to mitigate the effects of climate change.
This blog will describe why hydrogen (H2) combustion engines can support greenhouse gas emissions reduction and how their design is supported by Simcenter Amesim 2304.
Why hydrogen combustion?
There are ambitious worldwide goals to reduce CO2 emissions in the road transport sector. These goals are most usually solution-neutral; meaning that they can be reached either through electric vehicles or internal combustion engine vehicles using e-fuels or carbon-free fuels (ammonia or hydrogen).
The carbon-free fuels combustion is promising in sectors where the transportation infrastructure is the easiest to adapt, and where the energy and power demands are high i.e., heavy equipment and long-haul trucks.
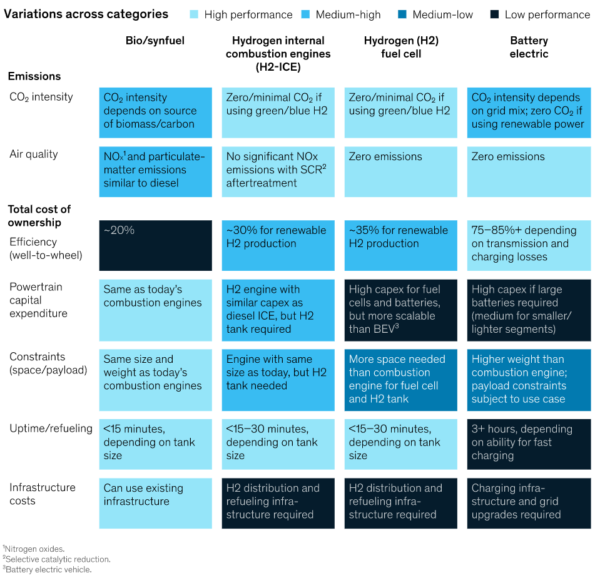
In that context, several industry players invest some R&D efforts in the hydrogen internal combustion engine technology pathway.
Critical design criteria of hydrogen internal combustion engines
The H2 combustion engine requires significant engineering efforts to meet power, efficiency, controllability and safety requirements.
Most of these engineering activities are related to the hydrogen thermodynamic properties. Indeed, the gaseous fuel has low density, high flammability and high lower heating value. It means for example that the fuel injection system is prone to H2 leakages, and that, when injected, it occupies a large part of the combustion chamber, requiring a lot of air and an efficient turbocharging system. Knocking sensitivity and NOx emissions are also significant challenges that can be solved in several ways (water injection, exhaust gas recirculation -EGR- …). Most of these challenges can be addressed in Simcenter Amesim engine solution using a high frequency modeling approach.
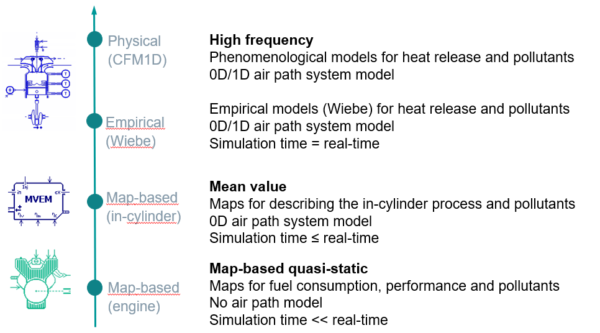
A proper engine calibration is also important to avoid misusing the designed engine components. Parameters like start of injection, lambda and spark timing will have a strong impact on NOx, knock and H2 consumption, regardless of the chosen design in steady state conditions. These calibration parameters are usually defined on engine test bench, but virtual (pre)-calibration is a cost-effective solution to save test bench running hours. This virtual calibration is most of the time done using Software-In-the-Loop or Hardware-In-the-Loop methodologies and these are best supported in Simcenter Amesim by using a mean value modeling approach.
Finally, the integration of the H2 internal combustion engine in the final product environment is of significant importance to assess the metrics that will be advertised and certified. These metrics are usually range, fuel consumption, NOx emissions and performances. To perform this metrics’ assessment, a switch to a map-based quasi-static modeling approach is recommended.
Let’s go through each modeling approaches with the Simcenter Amesim 2304 release.
High frequency engine models
The Simcenter Amesim high frequency engine models are compatible with H2 combustion with validated laminar flame speed correlation, fluid properties and knock auto-ignition delay table. The newly released “long-tail” Wiebe engine model includes an engine-out NOx observer either based on a Zeldovich mechanism or an Arrhenius’ law approach.
The Wiebe model has been validated with test data and is made available in the Simcenter Amesim standard demo portal, mostly thanks to the longstanding partnership with IFPEN research center. This demo’s scenario is about a 13.5l turbocharged direct injection H2 engine, with a variable nozzle turbine and low pressure EGR circuit.
This model enables many different studies:
- What is the maximum power and torque I could reach without having knock?
- What is the EGR rate to get the best trade-off between engine-out NOx specific emissions and H2 specific consumption?
- How low can fuel-air equivalence ratio (FAER) be and what is the impact on fuel consumption and torque?
- Is my turbocharger properly sized for reaching low fuel-air equivalence ratios?
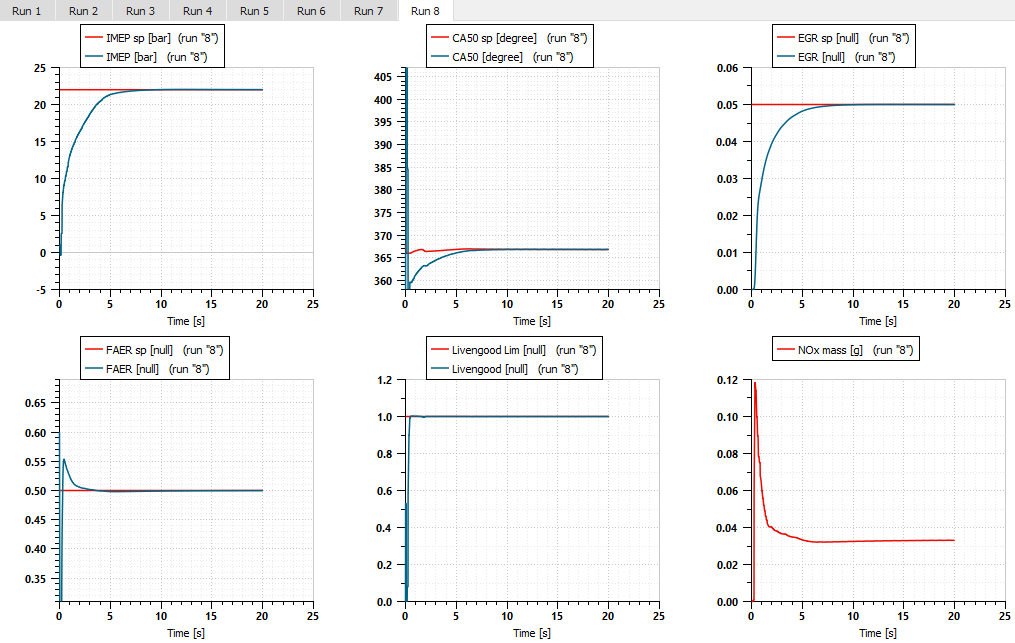
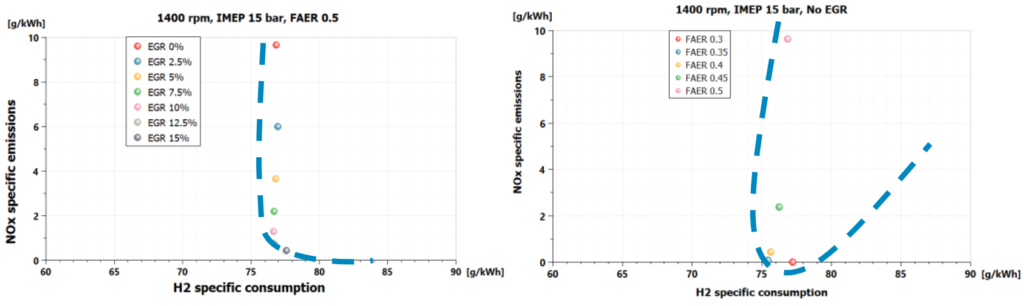
We can see on the Fuel-Air equivalence ratio variation that we cannot go lower than 0.3 (i.e., higher than lambda 3.3) to reach the 15 bar Indicated Mean Effective Pressure (IMEP) at 1400 revolution per minute. This is due to the turbocharger design limits particularly on the compressor wheel side. We need more air. To assess other potential compressor designs, Simcenter Amesim 2304 comes with the compressor table creator App. It allows to build a representative compressor map from engine operation setpoints (usually a full load curve) requiring very little amount of information.
The compressor table creator App has been validated on internal combustion engine compressors from a large range of turbocharger applications such as automotive, truck and marine. It can also generate fuel cell compressor maps, which can be relevant for early cathode side optimization.
Once the engine architecture is selected and meets the combustion requirements, we can reduce the high frequency model to a faster, lighter mean value engine model (MVEM) to enable pre-calibration of control quantities and virtual verification of engine control unit.
Mean value engine models
The MVEM modeling approach is based on a physical model of the air path system and a global energy balance characterizing the “mean” behavior of the in-cylinder process. It makes use of efficiency data and correlations to describe what occurs in the engine block during a complete cycle.
The transition from a high frequency engine model or engine test bench results to a mean value engine model can be done using the so-called MVEM tool which computes the volumetric, indicated and exhaust efficiencies maps used in the MVEM. This tool has been updated in Simcenter Amesim 2304 to provide an H2 engine conversion template.
Once these maps have been generated, they can be either directly incorporated in the MVEM model or combined with a neural network approach (using the Simcenter Reduced Order Modeling tool) to enrich the number of inputs and outputs of the model with for example EGR rate and NOx emissions.
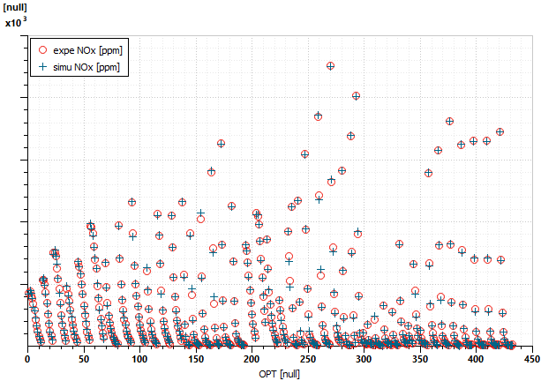
The accuracy of a such a joint approach allows to improve the simulation results accuracy while keeping a low CPU time and a real time capability to enable Hardware-In-the-Loop methodology.
The validation of the engine-out NOx emission neural network model included in the MVEM of the full engine range is shown here. It includes dependency on EGR rate, Lambda, engine speed and spark advance which makes it usable for virtual calibration and Hardware-In-the-Loop activities.
More information about the Simcenter Reduced Order Modeling can be found here.
Most of engine engineers would stick to this modeling approach to complete their simulation tasks, having a fast, robust and accurate H2 engine model in hands. But what about departments that don’t have sufficient data to generate such a model? What about transmission suppliers that would like to see impact of their technologies on engine performances and fuel consumption? For these people, a map-based quasi-static engine model is recommended.
Map-based quasi-static engine models
The quasi-static engine model which can be found in the IFP-Drive library is based on a variable set of maps (fuel consumption, maximum torque …) and some correction factors depending on the simulation objectives. It is widely used when the simulation goal is to estimate fuel consumption and vehicle performances over long mission profiles (driving cycles) and when the engine high frequency dynamics are not of primary importance.
This engine model can consider any type of fuel provided the fact that the user has access to a minimum set of maps and can handle dual fuel applications as well.
The main issue is that for H2 combustion engines, the fuel consumption and torque maps are not widely available and are most of the time confidential. Hence making difficult to use this modeling approach at a first look.
Therefore, the Engine table creator App has been updated to include validated hydrogen engine datasets. It enables IFP-Drive engine users to generate fuel consumption map out of very limited high-level data such as the engine architecture, maximum torque and power curves and combustion estimated parameters.
Having these tables created allow to assess vehicle range for a given tank on a given driving cycle. In this example, a 26 tons regional truck is simulated over the GEM transient cycle. The generated tables give a H2 fuel consumption of 15 kg/100km and the range is about 335 km with a 50 kg hydrogen tank (with compression storage around 700 bars).
To conclude, the Simcenter Amesim 2304 release has been completely validated for H2 internal combustion engine applications. It brings a robust and continuous workflow from highly detailed to fast and simple engine models and supplies Apps to generate missing data to avoid being stuck in a “data safari”. If you want to know more about other novelties of Simcenter Amesim 2304, have a look at this blog post or watch the video below.
Check out Simcenter Amesim free trial to experience the features for yourself!
Comments
Comments are closed.
This post is very useful to us thanks for sharing this info with us…
Thank you very much for the information you shared.