Hydrogen-fueled internal combustion engine
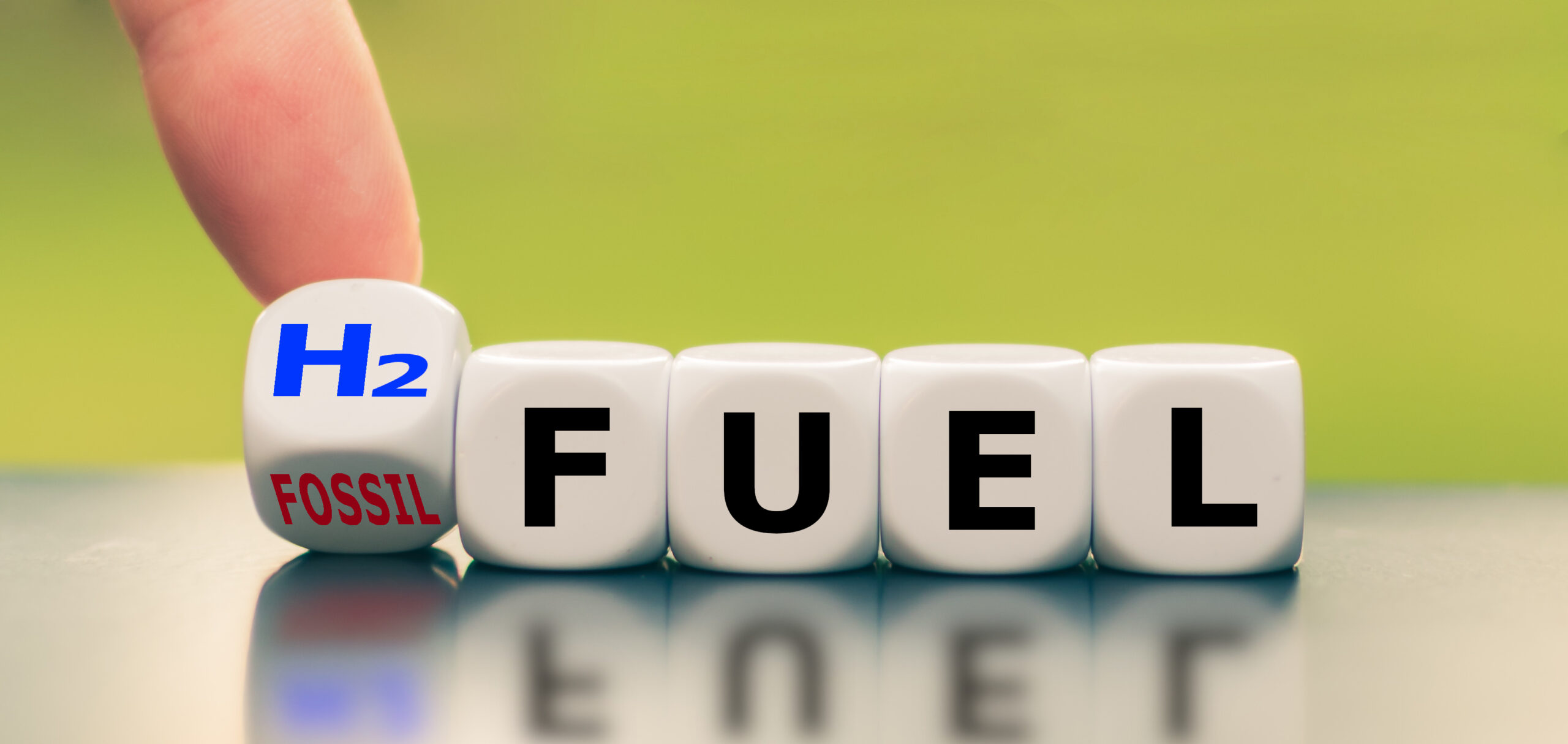
Define your Roadmap with Simcenter Amesim
Learn how to apply Simcenter Amesim to define your roadmap with hydrogen-powered vehicles and hydrogen-fueled internal combustion engines in particular.
Hydrogen is a promising fuel candidate for vehicles, to prevent CO2 emissions and hence reduce global warming. There are many questions and debates around its production and delivery. Indeed, they can have a dramatic impact on the global well-to-wheel benefit of hydrogen-powered vehicles. However, the usage of hydrogen in fuel cell and internal combustion engines could help meet the upcoming regulations, requiring major cuts in CO2 emissions.
The fuel cell applied in vehicles is largely studied and demonstrated with practical application in many transport sectors including automotive. The engineering of such fuel cell powertrains requires some CAE capabilities offered by system simulation tools such as Simcenter Amesim.
Another option is to burn the hydrogen in an internal combustion engine as one used to do for diesel or gasoline. Of-course there are H2-specific challenges related to the nature of hydrogen and its usage in an ICE. However, H2 engines can be an efficient technical solution towards a reduction of fleet CO2 emissions. It offers several advantages compared to an electric vehicle in terms of weight, cost, range and charging time. Additionally, it involves lower costs and higher versatility than Fuel-cell powertrains (no sensitive to H2 quality, ambient conditions, and availability [dual fuel]).
Once again, the virtual assessment of such a technology requires some modeling and simulation capabilities. This article exposes how Simcenter Amesim can support the development and evaluation of hydrogen-fueled vehicles.
The H2-fueled internal combustion engine
The application of hydrogen in ICE presents some clear advantages mitigated by some technical challenges:
- Avoid abnormal combustions (knocking, pre-ignition, back-firing)
- Define NOx aftertreatment system
- Adapt air charging systems
- Define storage System
- Implement dedicated safety concept
- Insure durability
Hydrogen storage and delivery
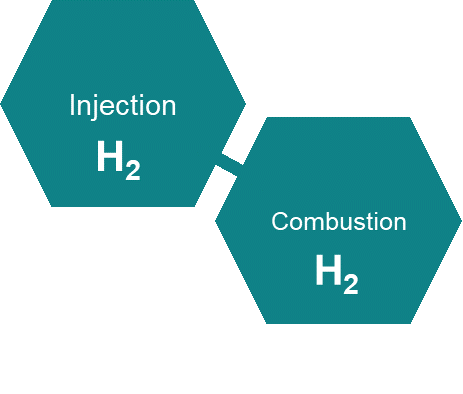
The hydrogen storage and delivery through the injection system and injectors is specific. H2 is indeed stored as gas in high-pressure tanks (300-700bar) and the injectors must comply with some H2-specific requirements (avoid injector nozzle backflows for instance). This system can be modeled using system simulation and the capabilities demonstrated for gas and liquid injection in Simcenter Amesim can serve the development of H2 application-specific components and systems.
Hydrogen combustion
The combustion process of hydrogen is significantly different from gasoline/diesel. This is mainly due to the nature and properties of H2. It has a low density and heating value, and high diffusivity and wide inflammability limits. Some aspects like the high laminar flame speeds are in favor of high efficiencies (and specific powers) whereas other characteristics lead to some challenges related to possible abnormal combustion (knocking sensitivity) and generation of pollutants (NOx, soot).
Simcenter Amesim provides a large scale of model for engine simulation, from crank-angle based approaches to simpler mean value engine and map-based approach. H2 applications can also benefit from this offer built around the phenomenological spark-ignition combustion model CFM1D(1), developed by IFP Energies Nouvelles.
Indeed, the CFM1D is fully capable of simulating hydrogen combustion with adapted modeling approaches to take into account the higher laminar flame speeds and the impact of species diffusion (modelled as an update of the formulation for the flame wrinkling). The model is hence able to deal with a large variety of operating conditions and variations in speed, load, equivalence ratio…
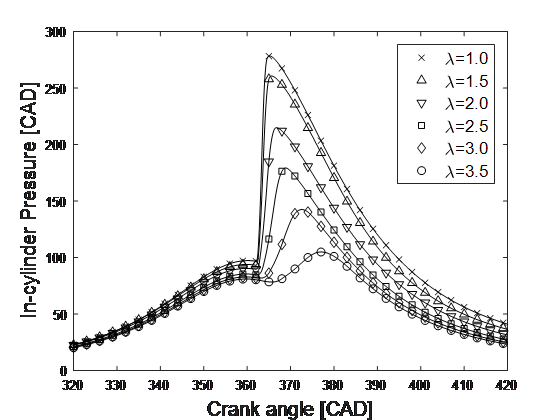
S. Richard et al., OGST – Rev. IFP, Vol. 64, No.3, pp. 223-242, 2009
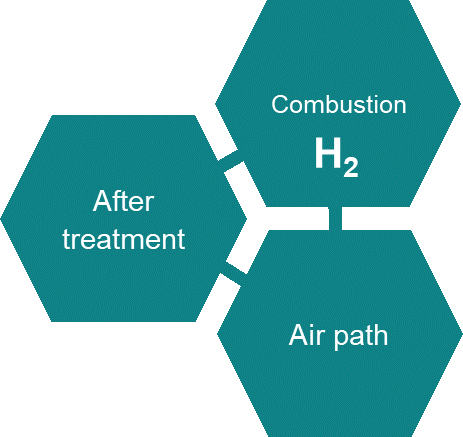
Adaptation of the air path
The design of the air path in hydrogen powered ICE is mainly linked to the type of injection (direct or port fuel) and the richness under which the engine operates (most of the time “lean”). The air charging and “boost” requirements could be significantly higher than for other spark-ignited applications. However, the methodologies and tools applied for the development of SI and CI engine air paths remain applicable. Simcenter Amesim offers the possibility to evaluate electrically assisted turbocharging systems to ensure a high level of boost combined with excellent transient responses.
Menegazzi, P., Wu, Y. & Thomas, V. Design of an electric supercharger for downsized engines. MTZ Worldwide 74, 36–41 (2013). https://doi.org/10.1007/s38313-013-0113-5
H2 ICE emissions and after-treatment
The combustion of hydrogen does not produce, by nature, CO2 emissions which is a key benefit. Yet, H2-fueled engines are not pollutant-free. Indeed, low amounts of NOx can be formed in certain conditions and partly mitigated by lean combustion. However, with the more and more stringent regulations, the residual NOx must be processed in dedicated conversion systems at the exhaust. The Selective Catalytic Reduction seems the most appropriate approach for de-NOx in Hydrogen ICE. The co-called H2 SCR also presents some potential in strongly oxidizing conditions found at the exhaust of H2 lean combustion engines. NH3 SCR (with Adblue) is more practical option in the short term (as it is for Diesel or lean gasoline combustion).
Some soot can also be formed during H2 combustion mainly due to the tight interactions between the flame and walls. The oil deposits on the liner and crevices can thus be burned producing particulate matter.
The modeling approaches and methodologies developed to simulate ATS(After Treatment System) in Simcenter Amesim, remain fully valid for H2 applications. Based on a physical approach, the monolith and filter models offer best-in-class simulation times. This allows their integration in broader powertrain models linked to the control strategies either off-line (Model or Software in the Loop) or on-line in real time (Hardware in the Loop).
A flexible modeling approach of the kinetic scheme permits to easily adapt generic monolith models to H2 specific reactions and catalysis. They can be handled with an on-the-shelves tool which supports the after-treatment system model set-up and validation.
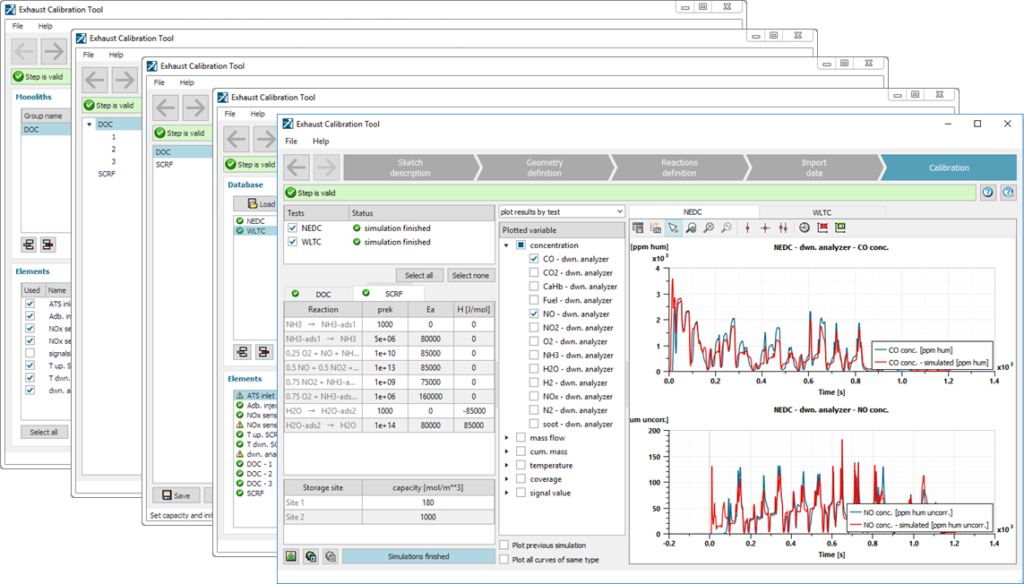
System integration
Analysis at the vehicle level
Beyond modeling capabilities for a given component or sub-system, system simulation offers the most appropriate approach to serve analysis at the vehicle level. Simcenter Amesim for instance supports the big picture and permits you to assess vehicle attributes including H2 consumption and vehicle range, performance or drivability.
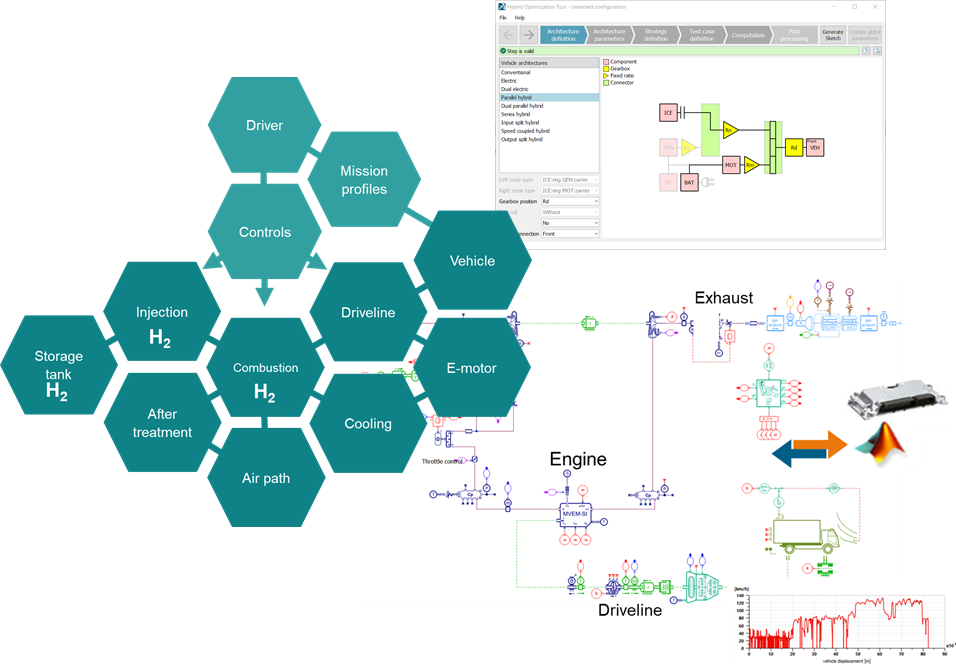
Concept phase analysis
Basically, the H2 internal combustion engine can be the core component of a “conventional” powertrain. It could also be combined with an electric motor in an hybrid configuration. Of-course, this option increases the weight of the vehicle as well as its complexity and costs. However, the Hydrogen-fueled ICE is not a Zero Emission Vehicle and might be combined with an electric motor to enter into cities where ICEs are banned. This kind of high level analysis can be conducted efficiently within the Hybrid Optimization Tool in Simcenter Amesim. No need to get a comprehensive set of data to start the analysis. Simple functional characteristics are sufficient to run concept studies and see the potential – in terms of fuel consumption / range of an electrified H2 powertrain. Typically, comparison between H2 ICE and FCV can be conducted in such a tool, offering all required versatility for Proof-Of-Concept studies.

Comprehensive models for vehicle development and evaluation
To continue the investigations at a lower level, Simcenter Amesim allows you to combine sub-systems physical model, with the appropriate modeling complexity according to the use cases, the controls and mission profile/driver models able to support the assessment of attributes over various scenarios.
Read this blog post to learn more on driver models for real driving cycles.
Apply the “right”modeling level
For instance, the high-fidelity engine model used for a detailed analysis of the in-cylinder process and Hydrogen combustion/pollutant formation, can be beneficially reduced to a lower order model. It could be better adapted to quick analysis of large scale scenarios (ex: Real Driving Emissions for cars, long routes for HD trucks) or complex system cross-coupling assessments.
A practical illustration of the concept is offered for the simulation of the internal combustion engine. Indeed, a scale of model is available for the engine – as for all the vehicle subsystems. Once again, this reduction toward simpler modeling approaches presents some better computation performances while preserving some component functional and behavioral attributes.
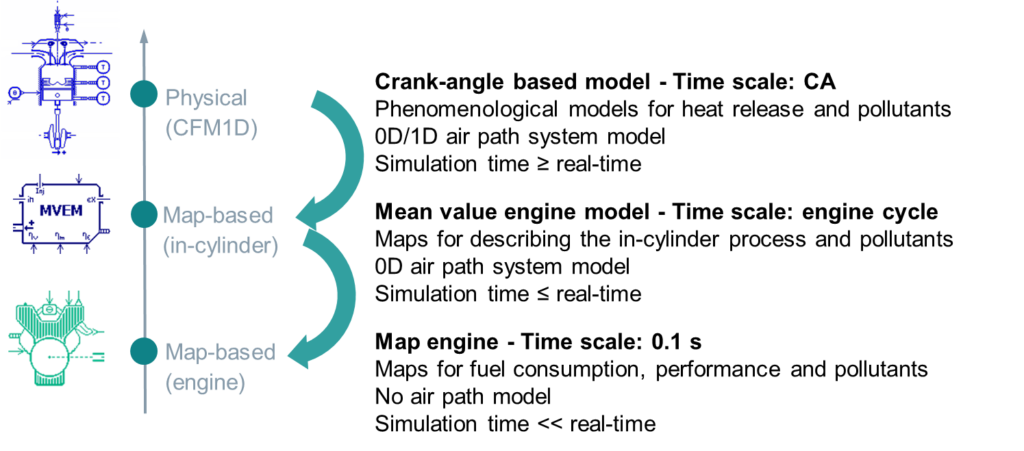
When studying the details of the impact of combustion control strategies on heat release and NOx emissions, a crank-angle based approach is fully required. Having the simulation of in-cylinder pressure and resulting instantaneous torque production is also a strong requirement for drivability or NVH studies at the powertrain level.
On the other hand, when focusing on air charging systems and their controls, a Mean Value Engine Model is definitely sufficient as it links a physical model of the air path system and a surrogate approach describing the in-cylinder process efficiency. Basically, the MVEM is able to capture turbo lags and manifold emptying/filling, and offers a good trade-off between cpu performance and accuracy and is well-adapted to analysis at the vehicle level.
Using the appropriate modeling for each subsystem permits to define the “right” vehicle model which offer the best balance between fidelity and cpu performance.
Supervisor and control models
Finally, system integration stresses the importance of sub-system interactions and the link with controls. Some capabilities that combine the plant model and the “controls” is a must have. On top of the native Simcenter Amesim feature to set-up vehicle control models (dedicated control library, ECMS), the software offers import/export and co-simulation with Simulink. It is also provided with model export capabilities to be able to apply vehicle physical models in an HiL environment and hence support ECU/VCU validation and pre-calibration. Following the industry trend toward heterogeneous simulation, the Siemens platform delivers full capabilities to deal with Functional Mock-up Units and hence serves actual needs for system simulation.
About the author:
Vincent THOMAS is Senior Product Line Manager for Simcenter Amesim. He has been supporting the internal combustion engine business for more than 20 years, leveraging a long-lasting collaboration with IFP Energies nouvelles to deliver to the market best-in-class system modeling and simulation capabilities to serve industry challenges.
Interested in learning more?
Stay tuned to discover our upcoming release of the Simcenter Amesim 2020.2 version and check our blog to read on related topics!