Manage electric drive systems engineering like a flock of birds anticipating the next move
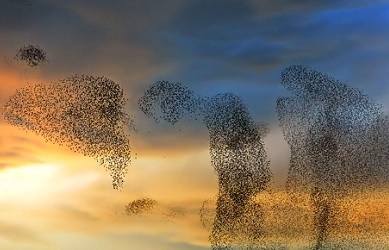
“When I was young, there were no signs of an electric drive or electrified vehicles. Car adverts were about speed and horsepower. Now, they are all about range and zero emissions,” comments Steven Dom, Director, Automotive Industry Solutions at Siemens Digital Industries Software.
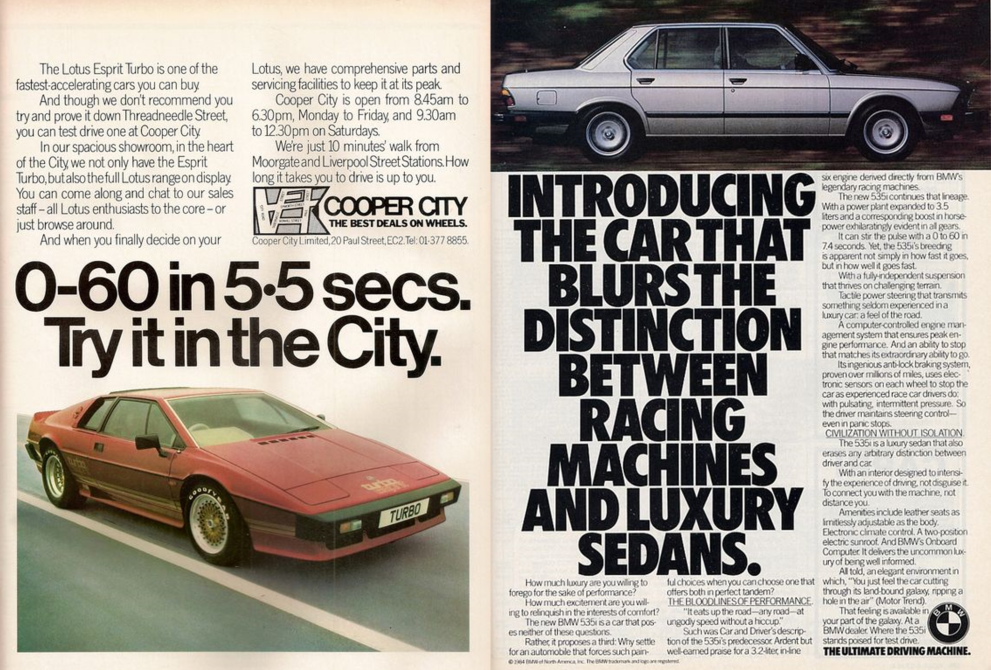
As electric vehicles (EVs) have changed advertising, they have also changed engineering. “A team of engineers tasked with developing a combustion engine might choose to buy or design a gearbox,” continues Steven. “As long as they meet the vehicle specification, the decision is theirs. That type of solo decision-making is not possible in EVs, where the trend is clearly to go to integrated electric drive units or e-drives in which the power electronics, motor, and transmission system which make up the drive are packaged as one entity. From a manufacturing perspective, it is easier to build one integrated box, but to get that package right, there must be an ongoing conversation between each distinct engineering discipline. For some individuals and organizations, this will be an enormous challenge.”
Managing the challenges of electric drive systems engineering
Siemens experts Steven Dom and Benoit Magneville, Electrification Product Manager, addressed all aspects of electric-drive systems development and how organizations can support engineering teams and embrace closer collaboration.
As Benoit explains: “The overall aim is to design an electric drive that is highly efficient in a wide range of operating conditions, yet there are many potentially conflicting requirements. Reducing the distance between the inverter and the motor, for example, presents benefits in terms of overall package size, cable weight, and harnessing; however, it creates new thermal and mechanical challenges as the inverter is evolving more restrained way.”
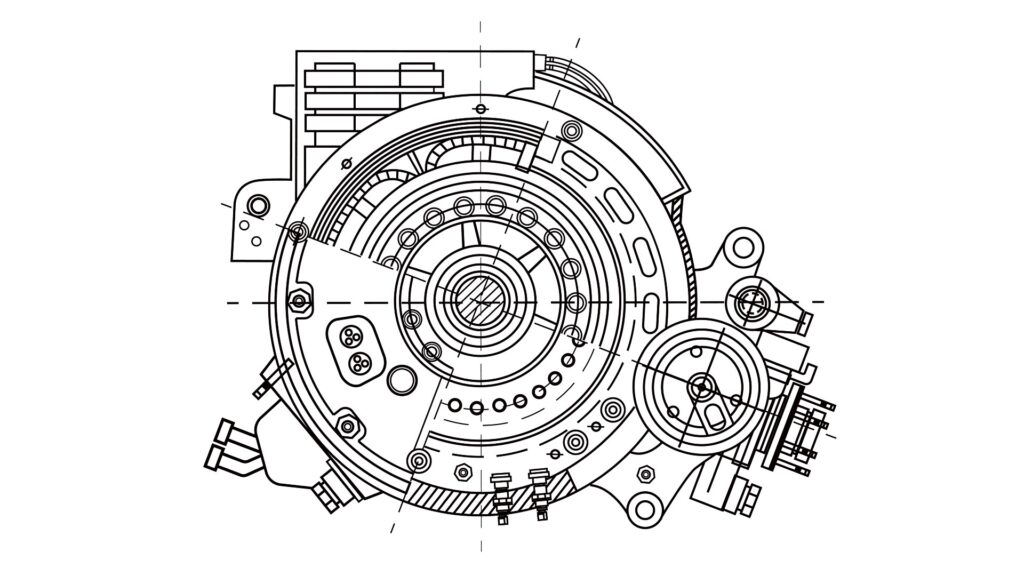
Other challenges related to thermal cooling include a critical requirement within a package of heat-producing items. Considering separate cooling systems for each component in an e-drive is not the most efficient approach. Integrating the cooling system for all components will simplify construction, doing away with an array of pipes, pumps, and heat exchangers. Still, it also makes for a more complex engineering task. On top of this, the battery and the passengers compete for effective thermal management, and appropriate cooling will need to be provided.
In addition, there is a complex dynamic between meeting operational targets for the e-drive and predicting how noise and vibration are perceived by people sitting in the cabin. From a commercial perspective, passenger comfort is essential to manufacturers, particularly for high-value brands.
Addressing Power Electronics design, system integration, and reliability
Topology design is one of the early stages of developing an electric drive’s electronics. Key metrics must be understood to define the best topology, such as efficiency, cost, tolerance, and EMI suppression. Much engineering time can be spent assessing how topology impacts the vehicle, then optimizing based on those results. However, the effort can be wasted if thermal implications are only discovered at the end of that process. Ideally, thermal design and simulation are entirely in sync with topology design and evaluation.
The choice of semi-conductor technology is also important. Still, the best decisions cannot be made if you do not know how to identify a semiconductor’s characteristics and compare available options. “The ability to understand junction temperature is key because that defines reliability,” says Benoit. “You cannot just rely on performance ratings from a supplier or on one set of test results.”
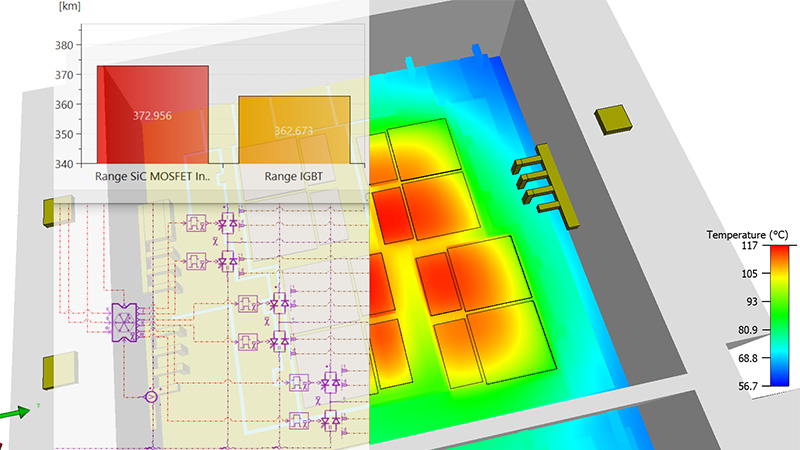
A thorough and accurate electronics design exploration encompassing PCB (Printed Circuit Board) and Busbar design requires integration with mechanical CAD and electromagnetic, thermal, and structural analysis. The solution is for development to take place within a single environment in which all engineers have easy access to other disciplinary areas, and specialists can interact with each other.
The ATZ International webinar will explain how to build a Simcenter workflow that incorporates design, simulation, and testing optimizes power electronics devices, and delivers the required power density in a reliable, compact package that ensures EMI/EMC compliance and performance.
If you want more background, look at this blog Inverters: the heart of electric vehicles.
From early electric motor sizing up to performance validation
One fundamental requirement is that a motor’s lifetime is reliably higher than the vehicle warranty and the vehicle’s lifetime. Thermal design is one of the main ways to improve lifetime and performance.
“As usual, success begins with the design phase,” notes Benoit. “Electric motor requirements are cascaded down from EV performance targets. The best way to obtain fast and accurate motor sizing and configuration is to quickly evaluate multiple design types and topologies against electro-magnetic efficiency, thermal and thermal and vibro-acoustics performance while still in the architectural phase.”
The Simcenter portfolio provides a connection between all these areas, enabling an assessment of how motor sizing and design impact the entire vehicle. In the initial stages, when the design only exists as a set of operational requirements, Simcenter offers an extensive library of motor templates and more than 200 materials. This opens the possibility of identifying a completely new motor architecture that will fulfill targets and generate the best thermal cooling system. Any virtual model can be tested and validated simply by exporting it into Simcenter Amesim.
Maximizing the efficiency of the electric drive transmission
From an operational point of view, the challenge is to maximize transmission system efficiency while minimizing weight and combining it with the rest of the drive within packaging limits. It is essential to assess gear contact stresses, bearing forces, and shaft flexibility so that noise and vibration from the rotating gear in the gearbox can be accurately predicted. Again, this means designing against multiple attributes, including durability and oil supply for lubrication.
Manufacturers want to create lighter vehicles and may consider using new materials, yet these bring specific challenges because they are not always fully proven.
Another factor is budget. The cost of prototyping a single gear can be up to $200,000 US. Hence, performance needs to be thoroughly evaluated, and any failure or weakness promptly addressed before a capital investment is made.
An ecosystem for electric drive systems, electromagnetic, thermal, mechanical, and acoustics engineers
As manufacturers compete for the best statistics and most favorable reviews, meeting customer demand is vital to commercial success, and the characteristics of an electric drive can make a significant contribution. The implications of various components and systems within the whole vehicle must be clearly understood.
One proven method for reducing vehicle cost and development time is for an organization to work within a single, collaborative environment where all aspects of engineering design, analysis, and testing are progressed simultaneously. The Simcenter portfolio provides a connection between all these areas so that output from each stage in the cycle can be used as logical input for the next, fed back to the previous step, and ultimately provide validation at the vehicle level.
Birds in flocks are able to change direction quickly, not because they follow a leader, but by anticipating what to do next. That is precisely the advantage of a collaborative and flexible ecosystem. It helps your organization to also move in unison.
“Change within any organization can be daunting, and any increase in the use of simulation must lead to higher fidelity and confidence,” states Steven Dom. “New workflows have far-reaching implications across an organization and therefore need to be established correctly.”
This webinar will guide you through the potential challenges and highlight some customers’ success, from subsystem design to vehicle integration.
More information about the electric drive
Power Electronics:
- Web page: https://www.plm.automation.siemens.com/global/en/industries/automotive-transportation/power-electronics-simulation-testing.html
- Video: https://www.youtube.com/watch?v=muf-pXuklqk
- On-demand webinar: Simulating and Testing the Latest Technology for EV Power Electronics
Electric Motor:
- Web page: https://www.plm.automation.siemens.com/global/en/industries/automotive-transportation/electric-motors-design-simulation.html
- Webinar series: https://www.plm.automation.siemens.com/global/en/resource/electric-machines-simulation/88329
- Case study: https://www.plm.automation.siemens.com/global/en/our-story/customers/gknautomotive/104997/
Transmission: