Audi uses Simcenter to enhance the accuracy and speed of simulations for EV batteries
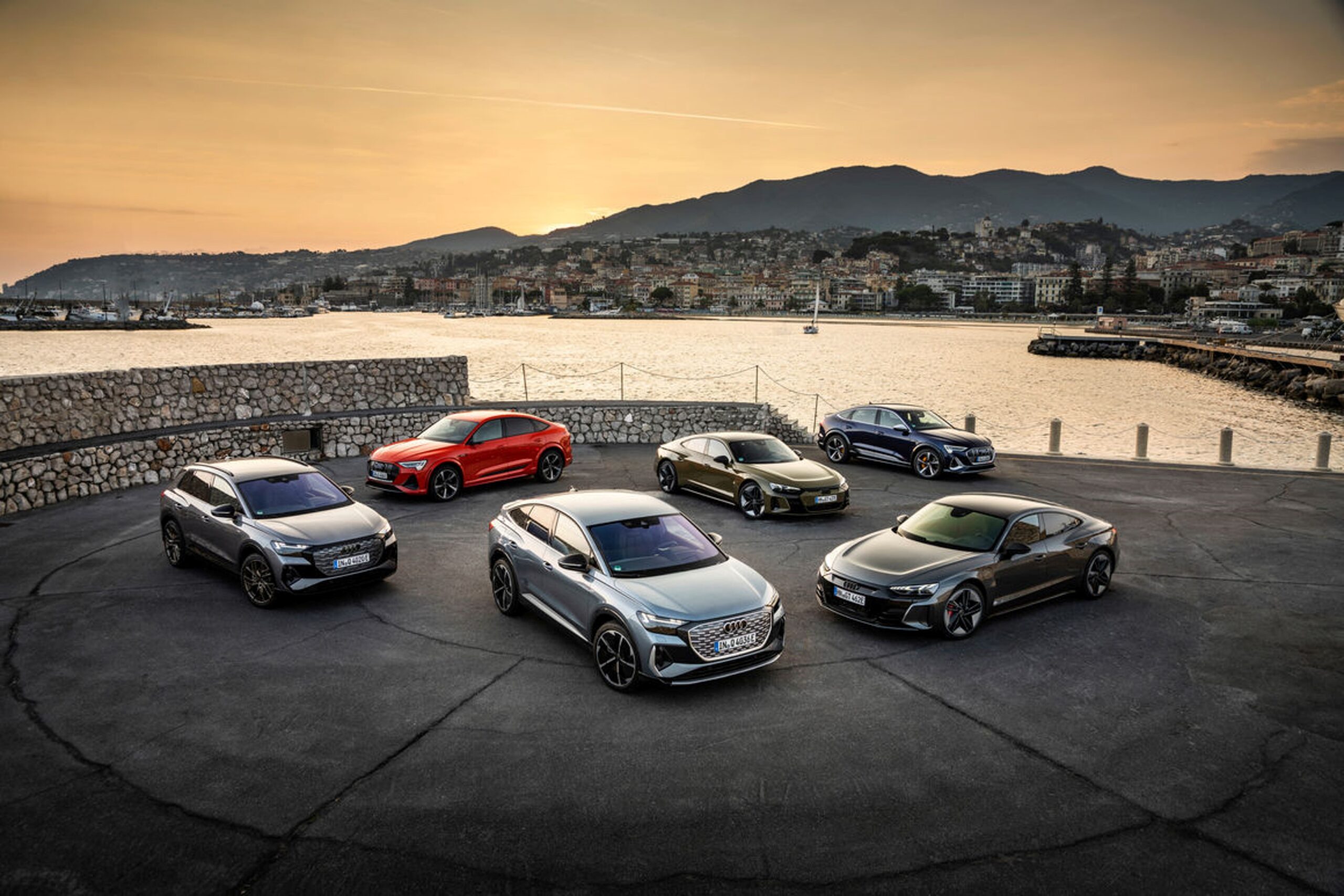
Developing safer, more reliable EV batteries
Accurately predicting the thermal performance of EV batteries is perhaps the most critical challenge facing automotive original equipment manufacturers (OEMs). Batteries have a temperature zone they can operate in to avoid failure. If the battery goes outside this zone, it can reduce the battery’s lifetime or even jeopardize occupant safety.
It is therefore no surprise that Audi, a brand known worldwide for its superior premium vehicles, has formed a highly specialized team dedicated to high voltage battery system concept development. Located in Germany, this team’s contributions are crucial to Audi’s vision of designing the mobility of tomorrow and ensuring an exceptional driving experience that is digital, electric and sustainable.
Increasing thermal model accuracy
Joohwa Sarah Lee, concept development engineer, is part of this team and specializes in battery thermal performance.
“Building accurate thermal simulation models is a critical aspect of my team’s work,” says Lee. “The models themselves are very important, as they directly contribute to our goal of optimizing thermal performance of the batteries.”
In 2021, Lee and her team discovered that, for certain cases and conditions, the simulation output did not match the test measurements. As a result, Lee set out to improve the quality of these simulation models. Lee and her team selected Siemens Digital Industries Software’s Simcenter™ Engineering and Consulting services as a development partner.
“We selected Simcenter because their tools enabled a seamless connection between not only 1D and 3D models, but also connectivity to third-party tools,” says Lee. “Simcenter Engineering Services provided the technical knowledge and support to help us set up these integrations and ensure the highest possible accuracy.”
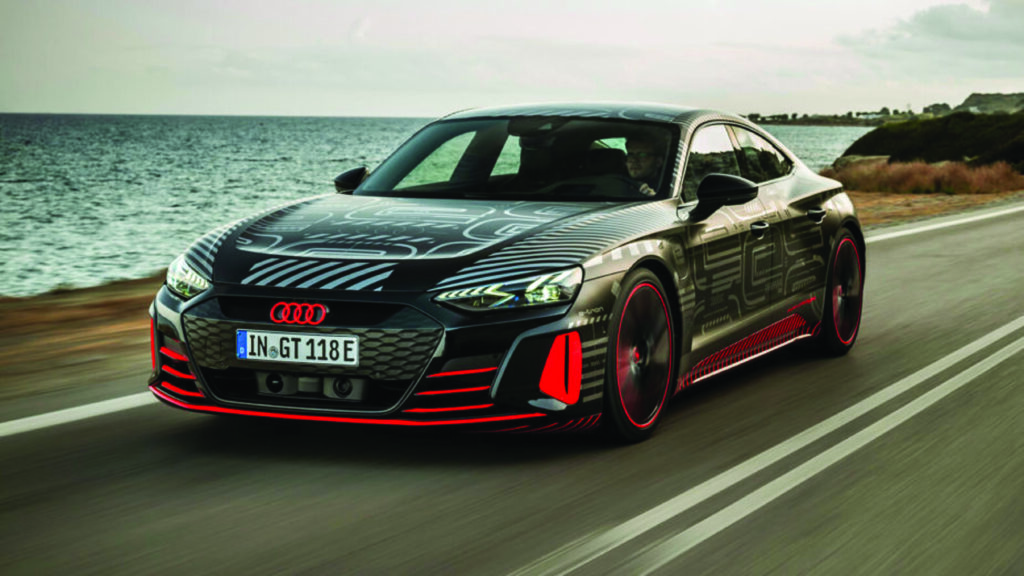
Combining 1D and 3D simulations
Traditionally, module and pack geometry have been modeled using 3D computational fluid dynamics (CFD) thermal simulation. This method has significant computational costs and can take days or weeks to complete. Additionally, extensive knowledge of parameters and 3D simulation experience is required to produce an accurate 3D model. Performing 1D system simulation is much faster, but it is often challenging to generate 1D models from a 3D model without compromising accuracy.
Simcenter Engineering Services set out to create a faster, more accurate battery stack thermal model to support Audi’s battery management systems, from the initial strategy development to validation with the rest of the vehicle’s subsystems. These models needed to consider several parameters, including current, coolant temperature variations, connectivity with 1D electrical models and integration with MATLAB/Simulink. Lee and her team provided the Simcenter team with test cases and boundary conditions for a variety of scenarios.
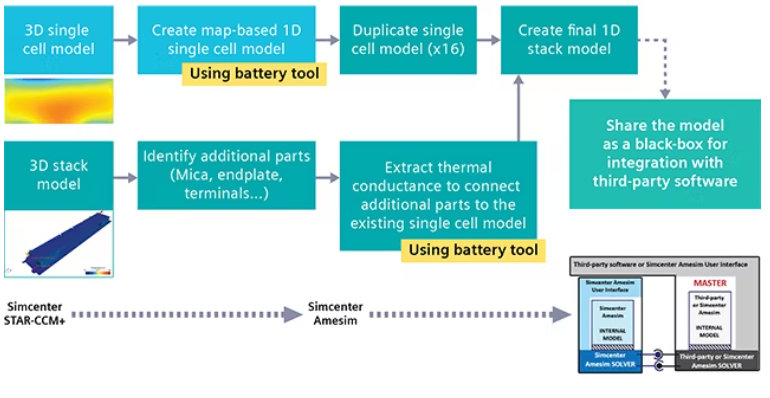
A customized workflow
By combining Simcenter STAR-CCM+™ software and Simcenter Amesim™ software, which are part of the Siemens Xcelerator business platform of software, hardware and service, Simcenter Engineering Services experts developed a semiautomated workflow to generate a 1D system-level model in Simcenter Amesim from a 3D Simcenter STAR-CCM+ model. The purpose of this workflow was to make sure Audi’s 1D simulation users could benefit from the high level of detail provided by 3D models while also maintaining the speed of 1D simulation.
Using specified inputs, Simcenter STAR-CCM+ was used to calculate several steady state conditions covering the chosen design space, such as inlet coolant temperature, flow rate and current. The data can then be used to derive a 1D electro-thermal model for investigating transient scenarios for the complete stack.
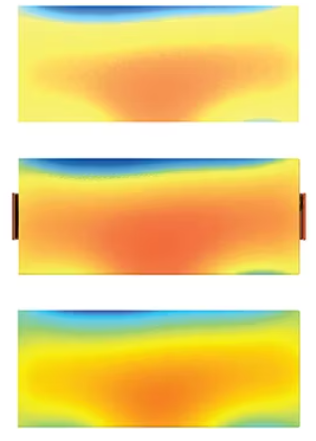
Reducing time, increasing accuracy
The workflow developed by Simcenter Engineering Services experts has reduced the computational time of battery thermal simulations to just minutes. One of the most vivid examples is simulating an EV battery charging scenario from 10 percent battery capacity to 80 percent.
“As a result of our project with Simcenter Engineering Services, we were able to reduce the simulation time of the charging scenario from almost an entire day to less than a minute,” Lee says. “This is a huge difference in calculation time. We have also seen a significant improvement in the simulation results, especially for thermal behavior studies.
“We explored other solutions for this problem, but no other company offered the level of connectivity between tools that Siemens did. Combining a detailed 3D model in Simcenter STAR-CCM+ with the speed and efficiency of Simcenter Amesim and third-party tools supported by the Simcenter Engineering Services team provided a crucial advantage. We are also excited to explore other aspects of the Simcenter portfolio, including Simcenter Battery Design Studio.”
Lee and her team are optimistic about the future of their partnership with Simcenter Engineering Services.
“We will continue to apply our new tools and methodologies to future challenges,” says Lee. “We are thankful for the support provided by the Simcenter Engineering Services team and their willingness and ability to help us solve difficult problems.”
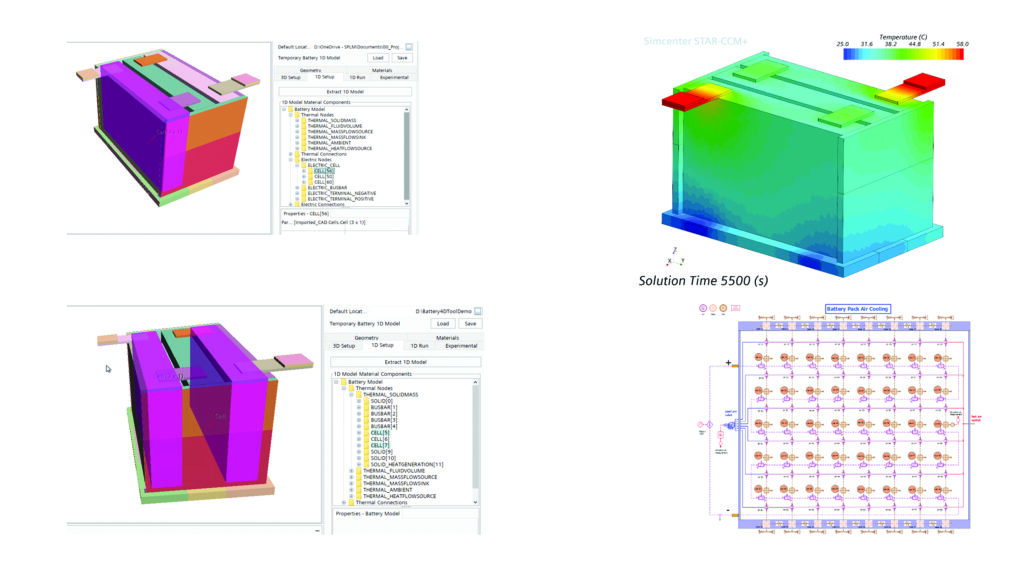
You may also enjoy
- Designing optimal battery thermal management using system simulation
- A multiphysics approach to battery thermal management and runaway analysis
- If you can’t take the heat… Simulate it! Reducing VTM costs & time to market
- Take a virtual tour of our vehicle energy management facility
- Tighter timeframes, tougher requirements, less stress? The argument for 1D-3D co-simulation