4 steps to predict road noise – a project with Hyundai Motor Group

Without the masking of a combustion engine, sound from the road is more prominent in electric vehicles (EV) and has become the dominant source of noise for drivers and passengers. Road noise is present in almost all driving conditions. Yet, predicting road noise is notoriously difficult and has become one of the critical issues facing engineers working on EVs.
“How to reliably assess road noise across a range of driving conditions and vehicle variants at each stage of development?”
This question was posed by a research team at Hyundai Motor Group (HMG). Respected for pioneering work in automotive technologies, HMG has solid expertise in road noise but wanted to expand this further.
HMG engineers had already begun exploring how to combine test and simulation technologies to create a more dependable digital twin. In particular, they wanted to characterize a suspension model, so had focused on creating test models that would be compatible with simulation models. However, they came across significant obstacles.
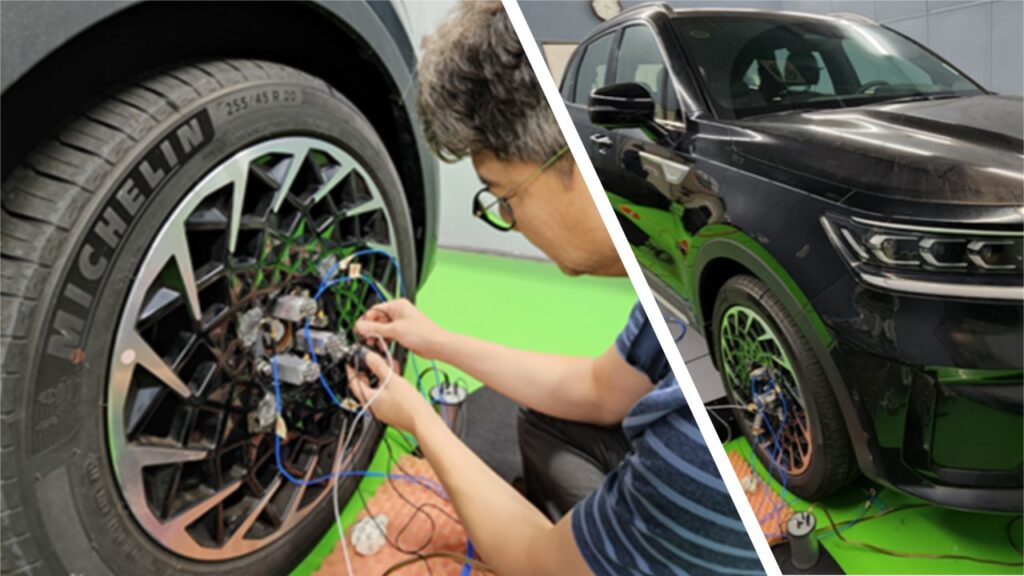
Step 1: Understanding the boundaries of each subsystem
As automotive engineers know, measuring how much each component contributes to road noise is challenging. Is the wheel, the suspension, or the vehicle body mainly responsible for the noise? The first challenge was understanding each subsystem’s operational boundary conditions as part of a larger assembly. We applied the structural testing in a free-free setup. It isn’t easy to get a correct representation as subsystems influence each other.
Here at Simcenter Engineering and Consulting services, we thrive on helping our customers achieve their technological and business objectives by tackling complex issues. Our work is interesting because we work with hardware, software, and people, using the skills and resources required to fulfill a brief. Logically, we were keen to assist when Sangyoung Park, senior research engineer at HMG, asked us if we could partner with his team.
Step 2: Separating the suspension
We began by focusing on the relationship between the tire (as the noise source) with the body, including the suspension as the receiver. We used component-based Transfer Path Analysis, or component-based TPA, to understand the nature of each substructure and estimate the loading. We validated this approach of estimating independent tire loads when HMG engineers confirmed that using those loads and tire representation on a different car predicted accurate road noise.
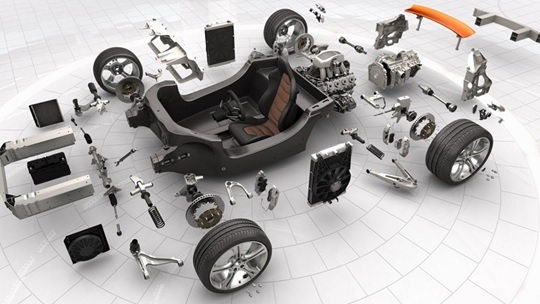
Read this white paper to learn more about the component-based TPA methodology.
Moving on with confidence, we used frequency-based substructuring (FBS) to understand the contribution of the vehicle body, suspension, and wheels. As the suspension is a chain of different components under a specific preload, it cannot be measured easily in a free-free condition. Instead, we used the new technique of FBS decoupling to characterize a component’s vibrational behavior by removing the influence of a supporting structure or test bench.
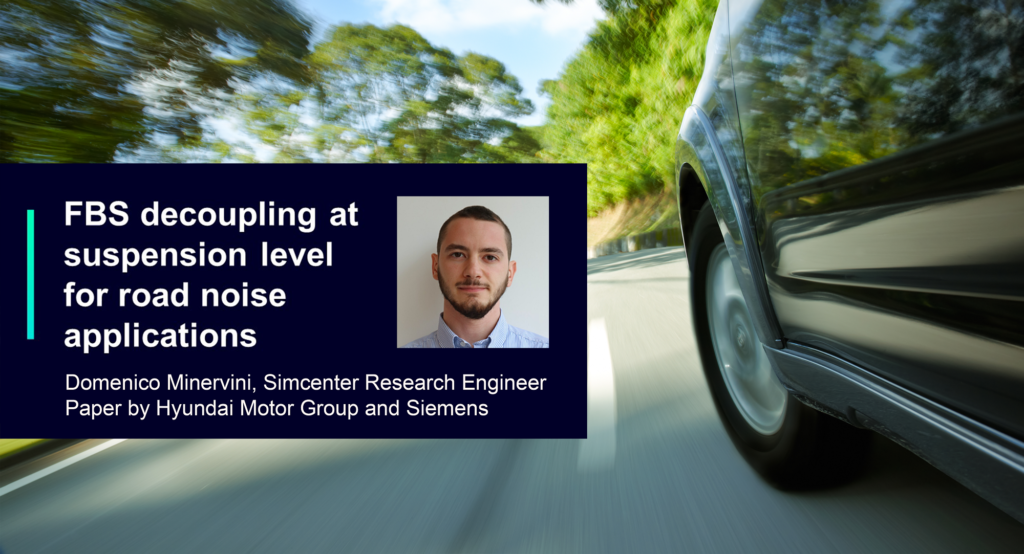
Last June, at the ISNVH congress in Graz, we co-presented with HMG a paper on the first test-based identification of a suspension assembly, including preload and operational nonlinearities. Follow this link to read the technical paper: FBS Decoupling at Suspension Level for Road Noise Applications.
Step 3: Designing, building, and validating the test bench
To apply the technique of FBS decoupling, we worked on the design, build, and validation of a customized test bench to assess the suspension model. This bench had to be designed so that it could later be used in-house by HMG engineers, allowing different suspensions to be mounted at interface points.
Our two teams worked exceptionally closely. The engineering services team in Leuven, Belgium, created CAD files to propose sensor and excitation locations which they sent to HMG in South Korea. There, test engineers used these CAD models to make instrumentation, measure the required transfer functions and provide feedback to Belgium for further validation.
After identifying the ideal test setup, positioning sensors, and ensuring accessibility, we used the jig to test a representative integrated front suspension model with the proper boundary conditions and under the correct pre-load.
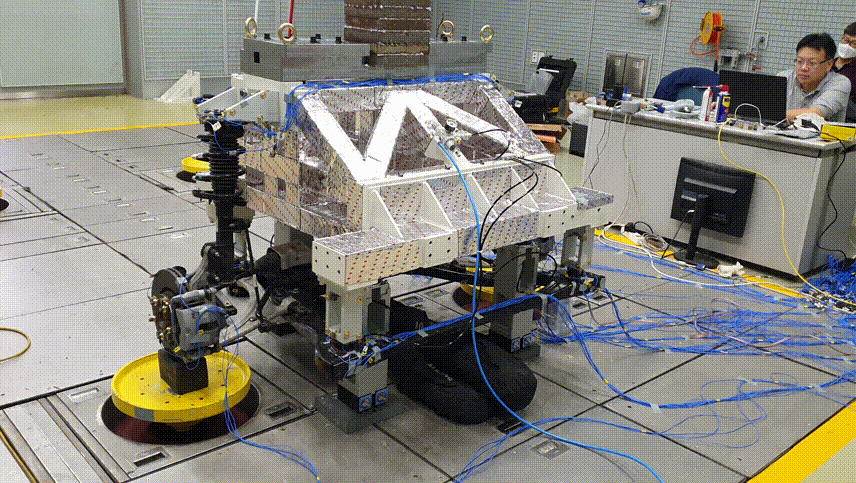
We measured the behavior of the whole assembly. And next, physically removed the suspension from the total and remeasured the bench only. Through an intense iteration process, we gradually validated the results. We built up a virtual model of the suspension, all based on actual test data generated by subtracting the bench-only measurements from the whole assembly.
Step 4: Predicting NVH system performance
The next step in the process was to combine all components and apply the tire loads to the full vehicle assembly or digital twin to listen to and validate the road noise.
When you have a virtual model derived from real-life measurements, you know it is reliable and can listen to it. If you don’t like what you hear, you can modify it and listen again. You can set targets and make choices about optimal sound based on the contribution of each component. For design engineers, this means much more flexibility.
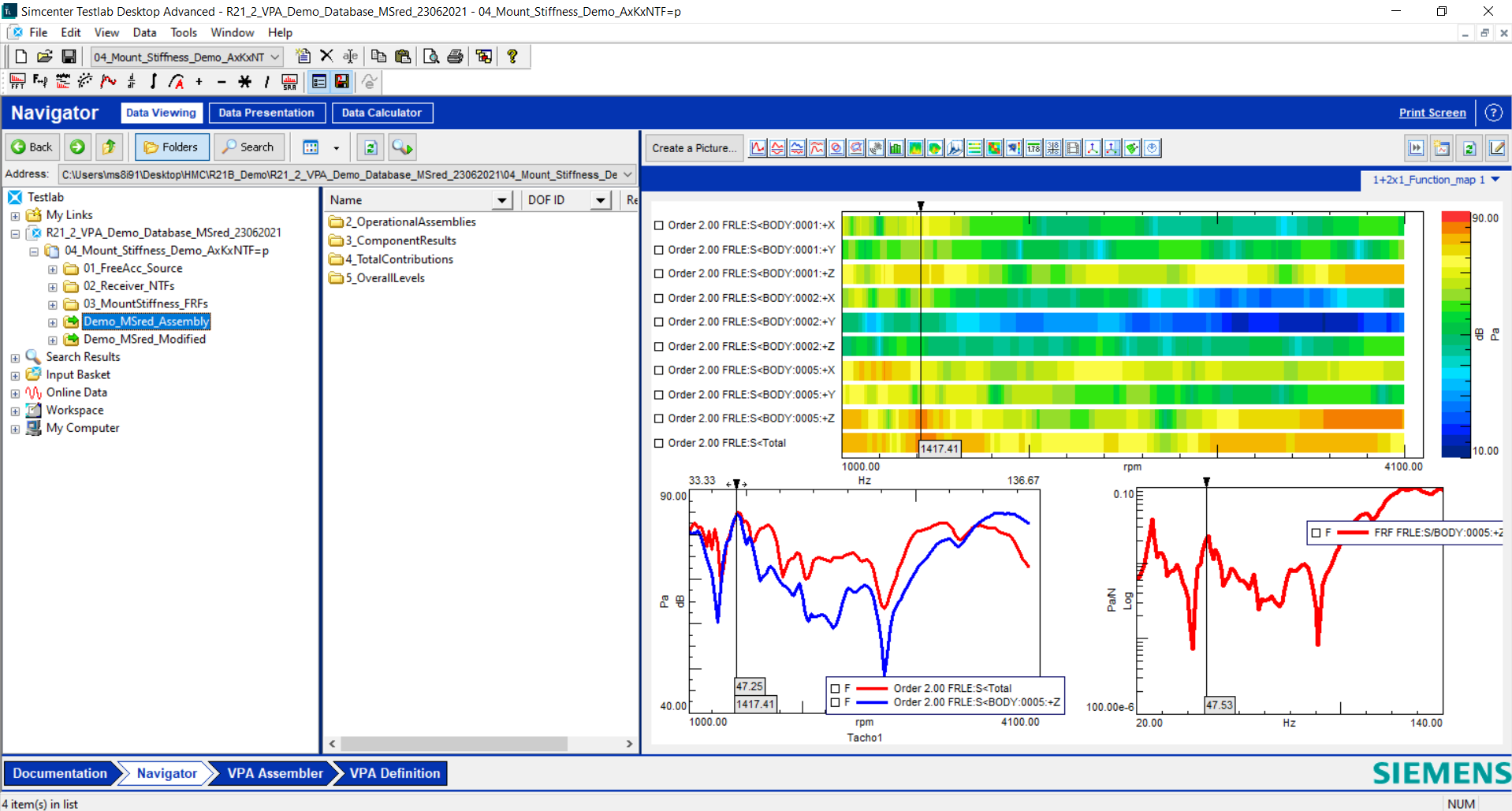
The test bench was delivered to HMG for use on-site, enabling detailed analysis of the investigated suspension, measuring other suspensions, changing suspension components or mounts, making modifications, etc., and studying their effect on road noise. This marks a step forward in the company’s ability to predict vehicle NVH performance virtually and transition to model-based virtual vehicle development.
Check this vehicle NVH prediction blog for more information on how to master NVH performance with a virtual prototype.
Teamwork makes the dream work
This multi-phase project had high standards and expectations. On the one hand, we pushed ourselves to engineer innovation in this project, while there was an exceptional degree of cooperation between the engineers at Siemens and HMG. We believe that this is the first commercial application of the FBS decoupling approach, and we are all proud of the sophisticated test jig we produced.
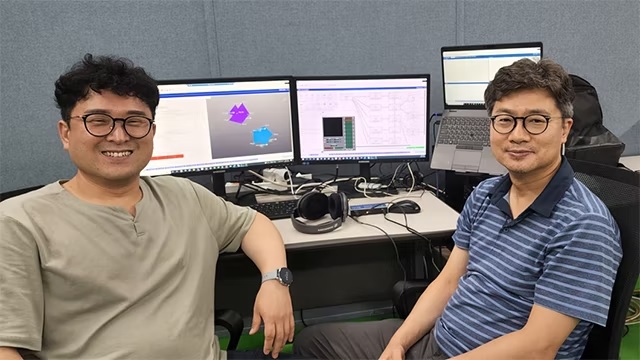
The two teams continue to collaborate. Our attention is now on creating a database of test results from different tires and suspensions so that HMG design engineers can enter targets and parameters, select options, and easily switch them around until they find the optimal combination for road noise.
Learn more about EV road noise challenges and how to use the Simcenter simulation and test solutions in this infographic.
Sharing road noise prediction insights
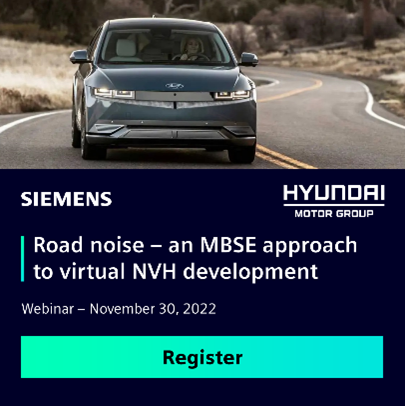
On November 30, Sangyoung Park is guest speaker in the live webinar Road noise prediction – an MBSE approach to virtual NVH development.
He will talk about the methods, results, and achievements of the NVH vehicle model project, the cooperation with Siemens, and HMG’s roadmap for EV road noise refinement.
The webinar will address the challenges of building good vehicle models, describe CAE & test-based component representation, and demonstrate how to define invariant loads. It will explain how to handle and model sources strongly coupled with the vehicle, for example, the tires. It will also look at which tools can easily replace one component or subsystem with an alternative version.
Interesting links
- Case study Hyundai Motor Group – Using model-based systems engineering to take a new approach to virtual NVH development
- White paper: Road noise engineering – Mitigating the most dominant noise sources in electric vehicles early in the development process
- Case study Renault – Expanding NVH prediction applications fivefold while eliminating physical prototypes