The beginner’s guide to 3D IC
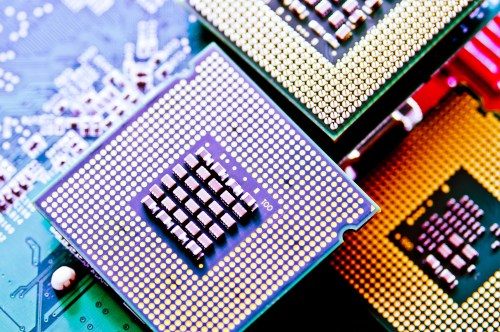
As consumer electronic devices grow increasingly connected, intelligent and advanced, designers need new methodologies such as 3D IC to address more than Moore limitations. The increasingly complex devices include more features and more complex electronic circuit design, requiring more processing capability. To keep up with these demands, designers need new methodologies for designing and connecting chips.
Watch the 3D IC podcast episode: An Introduction to 3D IC
If you prefer video to text, watch this 22-minute introductory video about 3D IC. Learn the basics of 3D IC advanced packaging, current trends and challenges for adoption.
We know that everyone has their own preferred learning style, and we want to make sure you can get the most out of this content in the way that works best for you. So, whether you prefer to read the copy below or watch the full episode above, we hope you find this information helpful!
What is 3D IC?
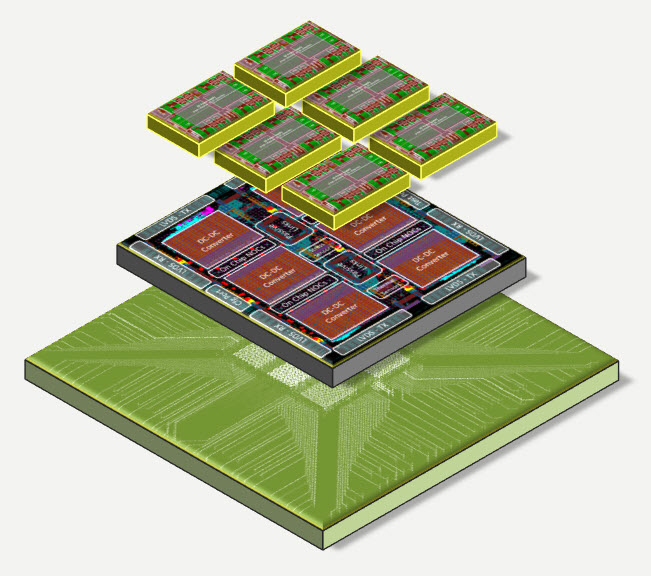
3D IC is a three-dimensional integrated circuit and refers to the integration, methodology and technology. Design teams disaggregate traditional monolithic implementation architectures into several smaller functional chips or chiplets integrated using a high-performance package. These 3D integrated circuits take up less space and deliver much higher performance than traditional monolithic technologies.
Technology for high bandwidth memories (HBM) came out about ten years ago where multiple memory chips are stacked. These stacked chips provided a lot of memory for a small footprint and integrated into ASIC on a 2.5D interposer, which is where that term originated.
What problem does 3D IC solve?
The semiconductor industry saw advanced application-specific integrated circuit (ASIC) technology nodes scale dramatically over the last 40 years, alongside higher performance. As we reach the limits of Moore’s law, device scaling becomes a challenge. Devices shrink at a slower rate, it takes longer and the cost is much higher for the technologies, design, analysis and manufacturing of these chips.
There are practical limitations on how large you can make a device. The photomask and reticle size ultimately determine a chip’s maximum size – roughly 25 to 27 millimeters on a side. So, physically, you cannot make a chip bigger than that. Since the number of transistors scaling has reduced, designers do not benefit from increased complexity by putting more and more devices into a single package. 3D IC designers do not face the same footprint challenges.
System on a chip (SOC) intellectual property are the basic building blocks implemented in that chip. Different types of functions require very specialized ASIC technologies. In some cases, it could limit what you can implement in the system because you would need all the IP available in the same process if you’re going to integrate that into a single chip. When we get into 3D IC, you no longer have that limitation. So, you can acquire chiplets, which perform a particular function, such as intellectual property. That chiplet can be optimized using the most appropriate technology for that type of functionality.
How does 3D IC work?
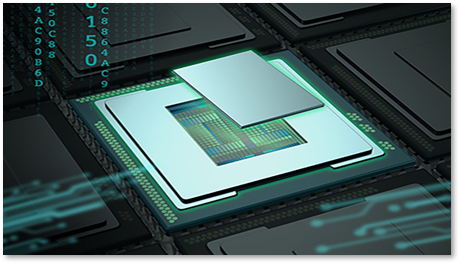
Since 3D IC is not limited to how large a device can be, designers can create much larger systems by putting multiple chips in a package. The implications of monolithic design for high-performance computing and AI devices will continue to use monolithic technologies. But they could leverage some of this disaggregation by splitting the design up into a smaller set of chips. But in general, if you can fit everything you need in a single chip, you will get the lowest unit cost and the highest performance. When designers start facing limitations, that’s where 2.5D or 3D technologies can extend their capabilities.
For years, designers created multi-chip modules (MCMs). They put one or more ASIC chips into a single package and connect them with traditional packaging technologies. MCMs are a very mature technology but also have some limitations. 3D IC is driven more by advanced packaging technology to integrate chiplets. A chiplet is an ASIC designed to integrate with other chiplets within a package. These chiplets come in two classes:
- 2D (or 2.5D): Integrating two chips on a single interposer and interconnecting those chiplets on that interposer using metal interconnect.
- 3D: Die stacking involves stacking memory or sensor chips on another chip (like memory). True 3D is a very advanced technology that splits an ASIC into two chips and stacks them.
None of the available choices semiconductor design teams have to counter some of the monolithic challenges seem to be a “one size fits all” or complete solution.
What’s different about 3D IC from other technologies?
The difference between the traditional MCM is the packaging technology – so that may be either 2D or 3D. One key difference is the interconnection between devices at the silicon level. The wires are much shorter and thinner, making the resistance and capacitance considerably slower and allowing for more connections between chips.
In effect, 3D or 2D packaging technologies enable increased performance with greater complexity with more interconnects – allowing designers to build systems with a much smaller footprint inside of a single package.
Designers can decompose systems into functions implemented as smaller chips, or chiplets, instead of putting everything into a single homogeneous ASIC device.
The other difference here is system designers now have more options to implement their complex devices and take advantage of some of the inherent benefits of 2.5D and 3D. So it offers them more options in developing their systems, taking advantage of some of the benefits provided by these technologies.
What challenges do we face with 3D IC?
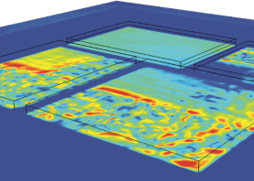
Now that we know what 3D IC integration is and how it’s different from other advanced integration packaging technologies, we know there are some challenges in moving into 3D IC:
- Thermal management: A traditional ASIC device uses a very simplified single power profile. In 3D IC package, designers must manage the thermal power profiles of multiple chips. Designers also need to understand the thermal interaction between different components to ensure the package meets the thermal requirements of the device.
- Mechanical stress analysis: When you stack die or stack a large silicon interposer on top of an organic substrate, the thermal expansion coefficients between the materials are different, so they will bend and flex differently. The potential mechanical stress on the connections between those devices can cause failures and reliability issues. Since every design is unique, designers should perform analysis with mechanical simulators to model that stress.
- Designing and analyzing the power delivery network: Package designers must consider that multiple chiplets may have different voltage supplies, power and noise requirements.
- Testability: Likely the most complex issue for 3D IC is testing, which is typically is a two-step process for single devices. The two types of testing are wafer-level and final testing once the chip is in the package. There are multiple chips inside 2.5D and 3D devices. Manufacturers likely wafer-tested them before delivery to the system integrators but would still require testing the interfaces between chips and restest packaged devices.
Want to learn more about 3D IC? Listen to the podcast now, available on your favorite podcast platform.
View the episode transcript
[00:10] John McMillian: Welcome to the Siemens EDA podcast series on 3D IC Heterogeneous Integration brought to you by the Siemens Thought Leadership team. I’m your host John McMillian. If you’re involved in any form of semiconductor and semiconductor packaging design, you will have seen and/or heard the term “3D IC” being broadly discussed and promoted. 3D IC is often referred to as a path to “more than Moore;” a reference to Gordon Moore’s observation that the number of transistors on a semiconductor doubles every two years, and along with that, the associated speed, capacity, and throughput. Another tenet of this so-called Moore’s Law asserts that this growth is exponential; however, experts agree that semiconductors may be close to reaching their physical limits due to multiple technical and technology reasons, as well as business and/or marketing reasons. This has led to design teams turning to the disaggregation of once monolithic implementation architectures into several smaller functional chips or chiplets, which are then reaggregated or integrated using a high-performance package. 3D IC refers to an integration, methodology, and technology.
[01:19] John McMillian: Today, in our first podcast in a four-part series, we are discussing what 3D IC integration technology is? And what exactly is driving it and why? I’m pleased to introduce my special guest, Anthony Mastroianni, who is the 3D IC Solutions Architect Director at Siemens Digital Industries Software. Welcome, Tony. And thank you for taking the time to talk with me today about 3D IC. And before we dive into the discussion, would you mind giving our listeners a brief description of your current role and background?
[01:49] Tony Mastroianni: Sure, John. Thank you for the intro, I’d be happy to do that. Again, my name is Tony Mastroianni. And I’ve been in the semiconductor industry for over 30 years. I’ve been involved primarily in the design of custom integrated circuits. Most of that time, in the role of a design manager. I worked for Semiconductor for the last 18 years. And in the last three or four years in that role, we started getting involved in working on two-and-a-half D designs that were using HBM memories for some very complex systems, processors, as well as 5G base station controllers. It became evident, as we started doing those complex two-and-a-half D designs, that our packaging methodology did require some considerable overhauls and improvements. So, I spent the last couple of years working and modifying our two-and-a-half D design process. The company I was with was acquired last year in 2020. I started with Siemens, and they’ve asked me to drive their advanced packaging design strategy and methodology. So, what I’m focusing on are complete solutions and workflows for two-and-a-half and 3D IC solutions, as opposed to just providing point solutions. That’s my primary role here at Siemens.
[03:20] Tony Mastroianni: So, I’d like to talk a little bit about what’s happening in the semiconductor in the design and the packaging space that’s kind of driving this 3D IC. What’s happened due to Moore’s law is the ASIC technology has been advancing over the last 40 years or so. And we’re getting to a point where the level of device scaling, it’s taking longer to make smaller transistors. And the costs are becoming extremely high for these technologies and the design, analysis, as well as the manufacturing of these chips. So, the advanced ASIC technology nodes, over the past 40 years, the transistors have scaled dramatically and the performance has also increased. But as we’re approaching the end of Moore’s law, the rate at which the devices are shrinking is reduced. It’s taking longer and the cost is going up dramatically. Another thing is HBM memories, these are high bandwidth memories. This is some technology that came out about 10 years ago, where multiple memory chips are stacked on top of each other to give you a tremendous amount of memory in a very small footprint. And that’s put into an unpackaged device, and that gets integrated into AISC on a two and a half d interposer. So that’s that’s where we come with the term “two-and-a-half d.” And it started really with HBM memory, so that really kind of drove this methodology. And that’s been around for about 10 years or so.
[04:55] Tony Mastroianni: Now again, due to Moore’s law, we’re hitting a limit; the transistor scaling is reduced. And there are practical limitations on how large you can make a device. And it’s really limited by what’s called the photomask and a reticle size, and that’s basically the maximum size that a chip can be. And it’s on the order of 25 to 27 millimeters on a side. So you really cannot make a chip larger than that, physically. Since the number of transistors scaling has reduced, we’re not getting the benefits of increased complexity by putting more and more devices into a single package. Another issue is intellectual property. So, an SOC, or System On Chip, intellectual property are the basic building blocks that are implemented in that chip. And this may be high-performance IO, such as, it may be PCI Express interfaces, HBM memory interfaces, and such. As some of these types of functions do require very specialized ASIC technologies, in some cases, it could limit what you can implement in the system because you would need all the IP available in the same process if you’re going to integrate that into a single chip. When we get into 3D IC, you no longer have that limitation. So, you can acquire chiplets, which perform a certain function, let’s call it intellectual property. That chiplet can be optimized using the technology which is most appropriate for that type of functionality.
[06:38] Tony Mastroianni: So, I talked about the device scaling. So, by not being limited to how large a device it can be, we really can create much larger systems by putting multiple chips in a package. So, the implications of monolithic design for certain products such as high-performance compute and AI devices will still continue to use monolithic technologies. But they could actually leverage from some of this disaggregation by perhaps splitting the design up into a smaller set of chips. But in general, if you can fit everything you need in a single chip, you will get the lowest unit cost and the highest performance. But when you hit some of those limitations, that’s where two-and-a-half D or 3D technologies can allow us to extend the capabilities of these systems.
[07:29] John McMillian: So there are a considerable number of growing pressures on traditional monolithic design. Can you tell us what approaches semiconductors teams have been adopting to achieving a device’s functionality goals?
[07:42] Tony Mastroianni:Sure. When we talk about putting multiple chiplets or chips into a package, there’s several different underlying technologies. People have been designing multi chip modules for many, many years, and that’s essentially putting one or more ASIC chips into a single package, and then connecting those with traditional packaging technologies. So, that’s referred to as an MCM module. There are many different technologies. And that’s a very mature technology but there are some limitations of that. So, when we get into 3D IC, this is really being driven by much more advanced packaging technology that allow you to integrate what I call chiplets. And a chiplet really is an ASIC that’s been designed to be integrated with other chiplets within a package. And there really are two general classes: 2D and 3D. We use the term “two-and-a-half D,” and that really came from the fact that we’re integrating a 3D HBM memory along with another ASIC. So, it really is 2D integration; you’re just integrating two chips on a single interposer – it may be organic or silicone. And then you’re interconnecting those chiplets on that interposer using metal interconnect. The other class is 3D. And that kind of falls into two different categories. One of them is Die Stacking. And there are really kind of two general applications that are being deployed today. One of them is stacking memory on top of a chip in one application that AMD and Intel and companies developing very large complex processor, they’re actually decomposing those processors into smaller building blocks. And then they’re actually taking some of the cache memories out of the die, and putting those in a separate die, and stacking that on top of the processor die. So, that’s what we call 3D. And in this case, it’s really just taking some of the functionality – maybe a memory – and putting that on top of the functional chip and then connecting those using the 3D packaging technology.
[09:56] Tony Mastroianni: Another application of Die Stacking would be in sensor type applications where you may have sensors that are gathering photo sensors or whatever. And then that sensor chip would be stacked on top of, say, a memory chip. So you would take that sensed data, store it to memory, and then maybe that would be stacked on top of a processing type trip. That’s what we call Die Stacking. Now, True 3D is a term where you’re actually taking an ASIC, and you have the ability to actually split that ASIC into two chips and stack them on top of each other. So, this requires the ASIC place-and-route tools to have the ability to not only place the logic in a traditional 2D manner on a chip, but now it can actually decide to partition some of the logic in one die that stacked on top of another or below another. So, this is really a very advanced methodology that will have some tremendous performance benefits. But it really is a newer technology, it is much more complex, so it’s really not really in production today. Whereas the other methodologies that I just mentioned are in production today.
[11:15] John McMillian: So, semiconductor design teams, they already have quite a range of choices to counter, some of the monolithic challenges. But as you point out, none of them seem to be a “one size fits all” or silver bullet, which I guess is why 3D IC integration is emerging. Please explain what 3D IC integration is and why it’s technically different from the other technologies we just discussed.
[11:36] Tony Mastroianni: So, what we’re talking about is putting multiple chips in a package. And primarily, the difference between the traditional MCM is the packaging technology – so that may be either 2D or 3D. And the key difference there is the interconnect between those devices is really being implemented at the silicon level. So, the geometries are considerably smaller. Since the wires essentially are much shorter and thinner, the resistance and capacitance is considerably slower. So that gives you the benefits that you can implement significantly more connections between those chips. And also you have much less parasitics, which means you can run them at much higher speeds. So, in effect, it is these packaging technologies, whether it be 3D or 2D, that offered the fine feature size of this interconnect enables increased performance that allows you to do much more greater complexity – since you can do many more interconnects – and allows you to build systems with a much smaller footprint inside of a single package. So, systems, in effect, can be decomposed into functions that are implemented as smaller chips, or what we call chiplets, as opposed to putting everything into a single homogeneous ASIC device. The other difference here is system designers now have more options to implement their complex devices and take advantage of some of the inherent benefits of two-and-a-half and 3D. So it offers them more options in developing their systems, taking advantage of some of the benefits offered by these technologies.
[13:20] John McMillian: It makes it clear what 3D IC integration is and why it’s technologically different. Can you tell us what a device design goals and/or objectives would be that would make a 3D IC the right integration platform?
[13:34] Tony Mastroianni: Any design goal or objective, obviously, is going to be unique to the particular design that the system designer is trying to design. So, again, the benefits of two-and-a-half and 3D would need to be considered to see how those objectives and goals can be achieved. So, the benefits that we’re talking about through 3D IC integration are, again, since we have smaller wires, we have reduced latencies which gives us – in the example of HBM memories – much higher memory bandwidth access, so you get performance advantages here: higher speed, better memory throughput. Scalability – so, we do have some practical limitations on how large a device can be made. If we have the ability to split a chip up into smaller chiplets and integrate those on a larger interposer or stack them, we can scale our systems much more gracefully. Building an ASIC device takes considerable time, cost, and time to market. It takes anywhere from one to three years to develop a complex SOC. But by having these pre-built building blocks, if you will, and maybe a smaller, less complex ASIC built into a system and package; it gives us the ability to implement different options of the product. So we can scale the product and have different product configurations leveraging this technology. Considerably shorter time to market, as well as reduced costs because you’re using packaging technology as opposed to the very expensive IC technology that we talked about before.
[15:16] Tony Mastroianni: The size, obviously, is smaller as well. So, for the reasons we talked about, we can implement a smaller footprint that goes into whatever product, ultimately, this will be in, leveraging either the two-and-a-half or 3D technologies. And power also – since we are connecting these chips that are placed right next to each other, the distances are much shorter, so we can run those at higher speeds at lower power, as opposed to putting chips on a board which may be several inches or a foot or more. So, we do have lower power because we’re driving these high-speed signals at much shorter distances. And also the benefits of cost, and the cost can become reduced by having smaller die, which would give us a higher yield and a lower unit costs for those chiplet components as well as the [16:15 inaudible] because if we’re integrating IP into an ASIC, for example, let’s say, a 56-gigs [16:22 inaudible] that may be on the order of $10 million for that piece of IP to be integrated into an ASIC. Now, if you need that functionality and that can be acquired from a chiplet, you’re really just paying for the end results, you’re not really paying for the IP costs for that. So there can be considerable savings in both the unit cost as well as the non-recurring engineering cost in deploying some of these technologies.
[16:49] John McMillian: Those are very compelling points. So, now that we understand what 3D IC integration is and why it’s differentiated from other advanced integration packaging technologies. But, sure, there must be some challenges in moving into 3D IC.
[17:02] Tony Mastroianni: Of course, yeah, there’s no such thing as a free lunch. So, 3D IC does bring some challenges to the table. And we’ll talk about some of these. The first is really thermal. So, in designing a traditional ASIC device, that device will have a certain power profile. And then that power profile can be modeled. And then the package design really just needs to be able to deal with that simplified thermal power model. And historically, you could just analyze the package, make sure you have the ability to take that heat out of the chip and dissipate that and you’re done. But when you put multiple chips inside a package, that power profile becomes much more complex. So, you do need to, rather than just having a very simplified single model, you have to deal with multiple chiplets in each of the power and thermal profiles of all those chiplets.
[18:01] Tony Mastroianni: The other thing that you need to be concerned with is the thermal interaction between these different devices. So, one example might be, let’s say, an HBM memory which has an operating condition of at 85C, maybe sitting next to an ASIC that is designed to run at 125C. And if those devices are too close and you’re not careful, the SOC can actually heat up that memory and knock it out of spec. So, again, you have to analyze the thermal interaction between each of those components to make sure that you’re meeting the thermal requirements of the device. Another thing which is unique to two-and-a-half and 3D type designs is mechanical stress analysis. So, when you stack die or stack a large silicon interposer on top of an organic substrate, the thermal expansion coefficients between silicon and those organic materials are different, so they will bend and flex differently. And that can create some mechanical stress on the connections between those devices, which can cause failures and reliability issues. There are different design techniques that are used to deal with that. And really, since every design is unique, that analysis needs to be done with mechanical simulators to model that stress.
[19:25] Tony Mastroianni: One of the probably most complex issues that comes up in these technologies is the testability. So, testing a single device, that technology is very mature. And generally, it’s a two-step process. So, as the chips are manufactured, they get tested while they’re still on the wafer. This is called wafer-level testing. So, there are probe cards that go and test the device. And if they’re good, they’ll go through and then they’re just marked if they’re bad, so you don’t package up the bad devices. And then once it’s in the package, generally, you’re going to retest the package with the chip inside of it, that’s called the final test. Now, when we get into two-and-a-half and 3D devices, we have multiple chips that are inside that package. So, you do need to test the interfaces between each of those chips, you still need to retest those devices once they’re in the package. So, presumably, the chiplet providers have tested those before they ship those to their customers. So, they are wafer-tested before they’re delivered to the system integrators. But during the assembly process, it’s possible that they may have been damaged. So, there is a need to retest those devices. So, that would require the test patterns associated for those chiplets to be a deliverable provided from those chiplet vendors.
[20:50] Tony Mastroianni: The other issue is you don’t have access to all the pins for each of those chiplets. So, different test techniques and test tools and DFT tools are required to be able to test those two-and-a-half and 3D devices. Another issue is your power delivery network – designing and analyzing that network. So, multiple chiplets may have different voltage supplies and different power requirements, different noise requirements – so, that all needs to be considered during the package design process, and making sure that you’re delivering the power to each of those components and meeting the requirements of that. So, there are other issues, but I’d say these are the primary things that need to be addressed in two-and-a-half and 3D designs.
[21:41] John McMillian: Thanks, Tony. I think that really does help us understand what 3D IC integration is, and why it’s differentiated from other advanced integration packaging technologies. So, what in target markets and applications are you seeing moving to or evaluating 3D IC as an AI platform?
[22:00] Tony Mastroianni: This 2.5D market really started with the advent of high-bandwidth memories. And as I mentioned, the applications well-suited for those are high-performance compute type processors that do have high memory bandwidth requirements and high capacity and AI type applications. Those markets will continue adopting these technologies. But as an ecosystem of general-purpose chiplets or building blocks becomes available to the general market, there really are no limitations in terms of what market these devices can be addressed. I really can’t think of any particular market that consumes ICs that would not benefit from some of these technologies. And this would benefit from some of the advantages that we talked about earlier, whether it’d be cost [22:52 inaudible], performance, speed, and just footprint size. So, I think it is really a true broad market that these technologies can leverage the two-and-a-half and 3D IC packaging technologies.
[23:10] John McMillian: Thanks, Tony, for this highly informative and educational discussion for this first podcast on 3D IC Heterogeneous Integration in our 3D IC series brought to us by the Thought Leader team covering what is 3D IC and what is driving semiconductor design teams to adopt it, and what advantages it brings. We’re looking forward to the future podcast with you on the same topic. And thanks to our listeners for joining us today.
About the Siemens 3D IC Design flow
The Siemens 3D IC Design Flow is a comprehensive set of tools and workflows targeted to develop advanced 2.5 and 3D IC heterogeneous system-in-package (SiP) designs. This proven, complete 3D IC design flow includes 3D architecture partitioning to planning, layout, design-for-test, thermal management, multi-die verification, interconnect IP, manufacturing signoff, and post-silicon lifecycle monitoring. Transform existing design and IP architectures into chiplets or build scalable 3D IC technology for faster time to market.
Learn more about Siemens EDA’s marketing-leading 3D IC technology solution: https://www.siemens.com/3dic