35% reduction in plant-level fluctuations and 30% expansion of warehouse capacity: Simulation-based optimization for production smoothing in a European food manufacturer
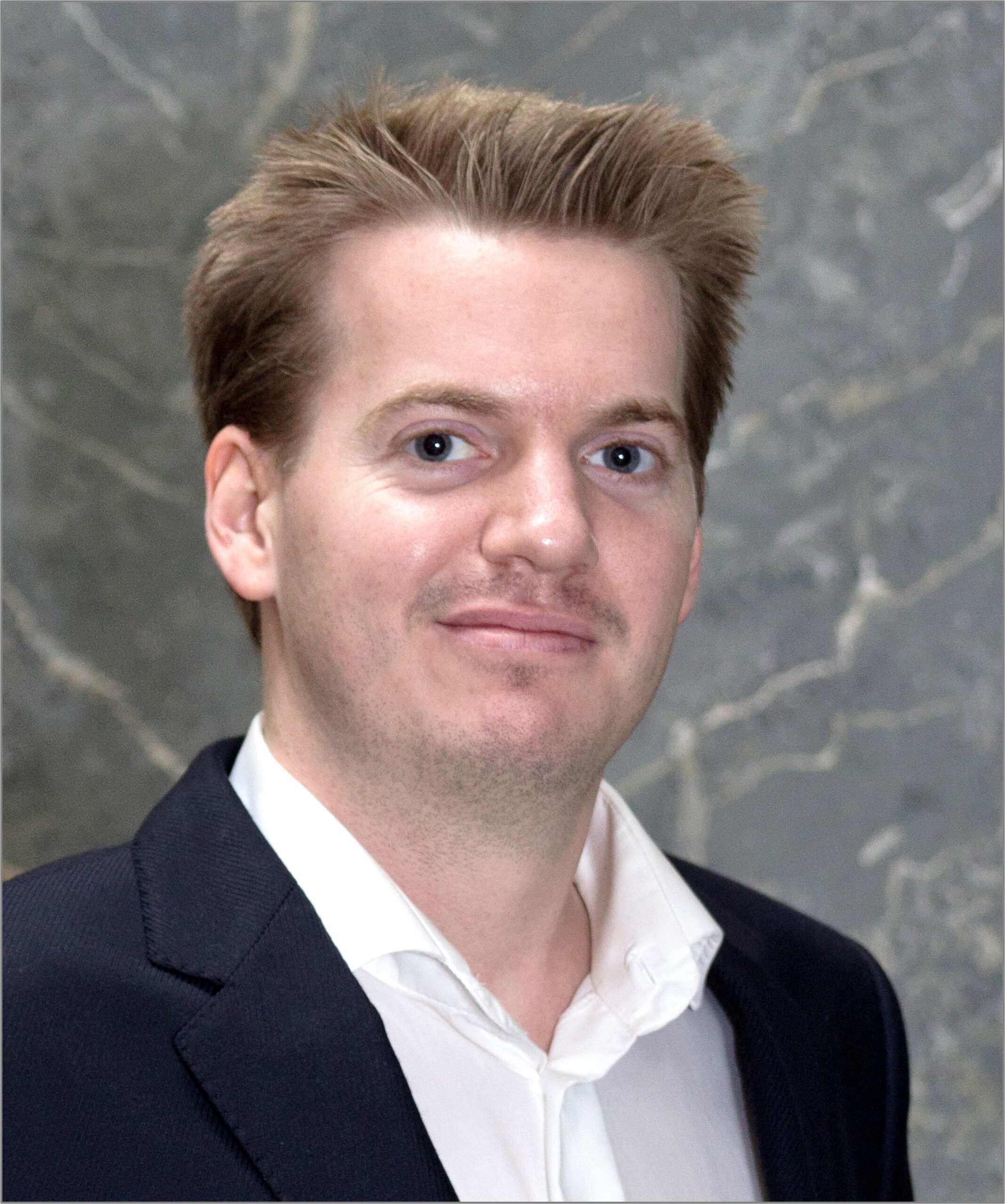
Fraunhofer Austria Research GmbH
DI Dr. Felix Kamhuber
Optimizing production: A simulation-based approach
Optimization is the core of Dr. Felix Kamhuber’s lecture, which starts with an innovative approach for optimizing production processes in the European food industry, specifically focusing on production smoothing in the consumer packaged goods sector. By combining simulation techniques with multi-criteria optimization methods, Dr. Kamhuber addresses the challenges of fluctuating demand and complex production systems. Through case studies and real-world examples, he demonstrates how this approach can lead to smoother production flows, reduced costs, and improved resource utilization. Attendees gain valuable knowledge on leveraging simulation-based tools to enhance efficiency and competitiveness in industrial production settings.
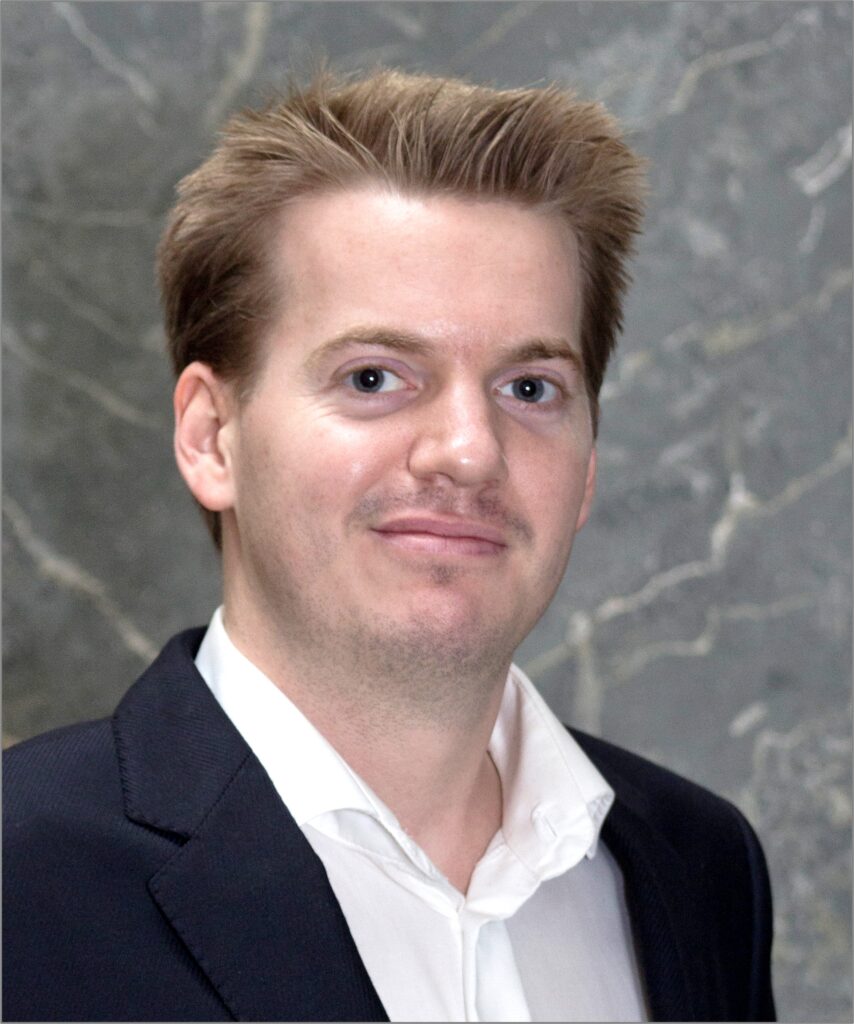
DI Dr. Florian Felix Kamhuber, a project manager at Fraunhofer Austria Research GmbH, holds a doctorate in industrial engineering from Vienna University of Technology and bachelor’s and master’s degrees in industrial logistics from the University of Leoben. Specializing in production planning and order management, Kamhuber’s expertise encompasses operations research, simulation, optimization, and demand- and production planning across diverse industries such as food, metal processing, plastics, pulp, and machine and plant construction.
He has led projects involving the implementation of production smoothing software for a food manufacturer, optimization of hospital operations with automated transport systems, and energy value stream recording in the metalworking industry.
Additionally, Kamhuber has contributed to projects optimizing order sequences in rail rolling mills and implementing planning systems like SAP-APO, along with collaborating on warehouse consolidation efforts at an international food manufacturer. His collaborative approach extends to factory and warehouse planning projects across industries, including food wholesale and timber.
Motivation and problem statement
Titled “An efficient simulation-based multi-criteria optimization approach for rolling production smoothing,” Kamhuber’s upcoming presentation will provide a comprehensive overview of the methodology’s development, evaluation, and real-world application.
Methodology development and evaluation
A key focus of the presentation will be on the methodology’s development and evaluation. Kamhuber will outline the hybrid optimization approach, which combines rule-based heuristics with metaheuristic algorithms such as simulated annealing and genetic algorithm.
Simulation applications in production planning
The lecture will also include detailed case studies showcasing the application of simulation techniques in production planning. Through simulations of the Salting Belt Unit and Basic Production processes, Kamhuber will demonstrate how the optimization approach can lead to smoother production flows and significant cost savings.
Optimization and Validation in industrial production
One of the highlights of the presentation will be the validation of the simulation-based optimization approach in industrial production. Kamhuber will present results showing a projected reduction in fluctuations at the plant level by up to 35%, along with anticipated substantial cost savings during the construction phase of the plant.
The application and validation of the simulation-based optimization approach in industrial production yield numerous benefits for businesses. Firstly, optimization efforts lead to a significant reduction of fluctuations at the plant level, potentially reaching up to 35%. This reduction in variability enhances operational stability and efficiency.
Moreover, substantial savings, often in the double-digit million euro range, are realized during the construction phase of the plant, attributed to optimized resource utilization and streamlined processes. The optimization approach also results in a proportional reduction in the number of units required for basic production facilities, thereby lowering operating costs. Notably, the production smoothing logic facilitates a more extensive dimensioning of critical infrastructure such as the maturing warehouse, optimizing space utilization by 30%.
Additionally, the calmer production environment resulting from better planning translates to reduced personnel costs, including overtime expenses. Furthermore, the extended service life of production units enhances resource efficiency and reduces long-term maintenance costs. Finally, the use of the self-developed planning tool as a digital twin provides ongoing support for rolling planning activities, ensuring sustained optimization and operational effectiveness.
“Our partnership with a European Food Manufacturer has yielded exceptional results. With our simulation-based approach, we’ve experienced a 35% reduction in plant-level fluctuations, resulting in unprecedented operational stability. This, coupled with savings in the double-digit million range during the construction phase, has been truly remarkable. Additionally, the corresponding reduction in required production units has led to significant cost savings across the plant’s operations.
With a 30% increase in maturing warehouse capacity, a relatively low-cost investment compared to the savings in capacity requirements for implementing the production smoothing logic, overall operational efficiency has increased significantly.”
DI Dr. Felix Kamhuber, Fraunhofer Austria Research GmbH
Conclusion and future directions
In conclusion, Kamhuber will emphasize the importance of economically efficient variabilization of production processes and outline future directions for research, including the extension of the methodology to other plants in the production network and the integration of downstream packaging processes.
Overall, Dr. Felix Kamhuber’s forthcoming lecture promises to provide valuable insights into an innovative approach to production optimization, offering practical solutions to the challenges faced by the European food industry.
Optimization lies at the heart of the 2024 Plant Simulation User Conference, where attendees will explore the impact and innovation of cutting-edge approaches to production processes. Held on June 6th, 2024, at the Infinity Hotel in Munich, Germany, this event follows Realize LIVE Europe, providing attendees with a unique opportunity to glean insights from industry experts, connect with peers, and discover the latest advancements in Plant Simulation software. Presentations will cover topics such as ‘What’s New in Plant Simulation 2404’ and engaging discussions that have the potential to revolutionize material flow simulation approaches. Join us as we delve into the future of optimization and efficiency in production processes.
Find more interestion presentations at the 2024 Plant Simulation User Conference e.g.
- https://blogs.sw.siemens.com/tecnomatix/bosch-user-friendly-modeling-plant/
- https://blogs.sw.siemens.com/tecnomatix/decarbonization-strategies-plant/
- https://blogs.sw.siemens.com/tecnomatix/wp-admin/post.php?post=9770&action=edit
- https://blogs.sw.siemens.com/tecnomatix/sustainability-bsh-co2-reduction/
- https://blogs.sw.siemens.com/tecnomatix/layout-planning-battery-production/
- https://blogs.sw.siemens.com/tecnomatix/8-axis-log-handler-simulation/
- https://blogs.sw.siemens.com/tecnomatix/ai-and-digital-twin-real-time-guid/
- https://blogs.sw.siemens.com/tecnomatix/electrolux-driving-efficiency/
- https://blogs.sw.siemens.com/tecnomatix/logistics-optimization-heat-maps/
- https://blogs.sw.siemens.com/tecnomatix/smart-factory-21-plant-simulation/
- https://blogs.sw.siemens.com/tecnomatix/logistics-simulation-modeling-ceit/