What’s New in Simcenter Mechanical simulation 2406
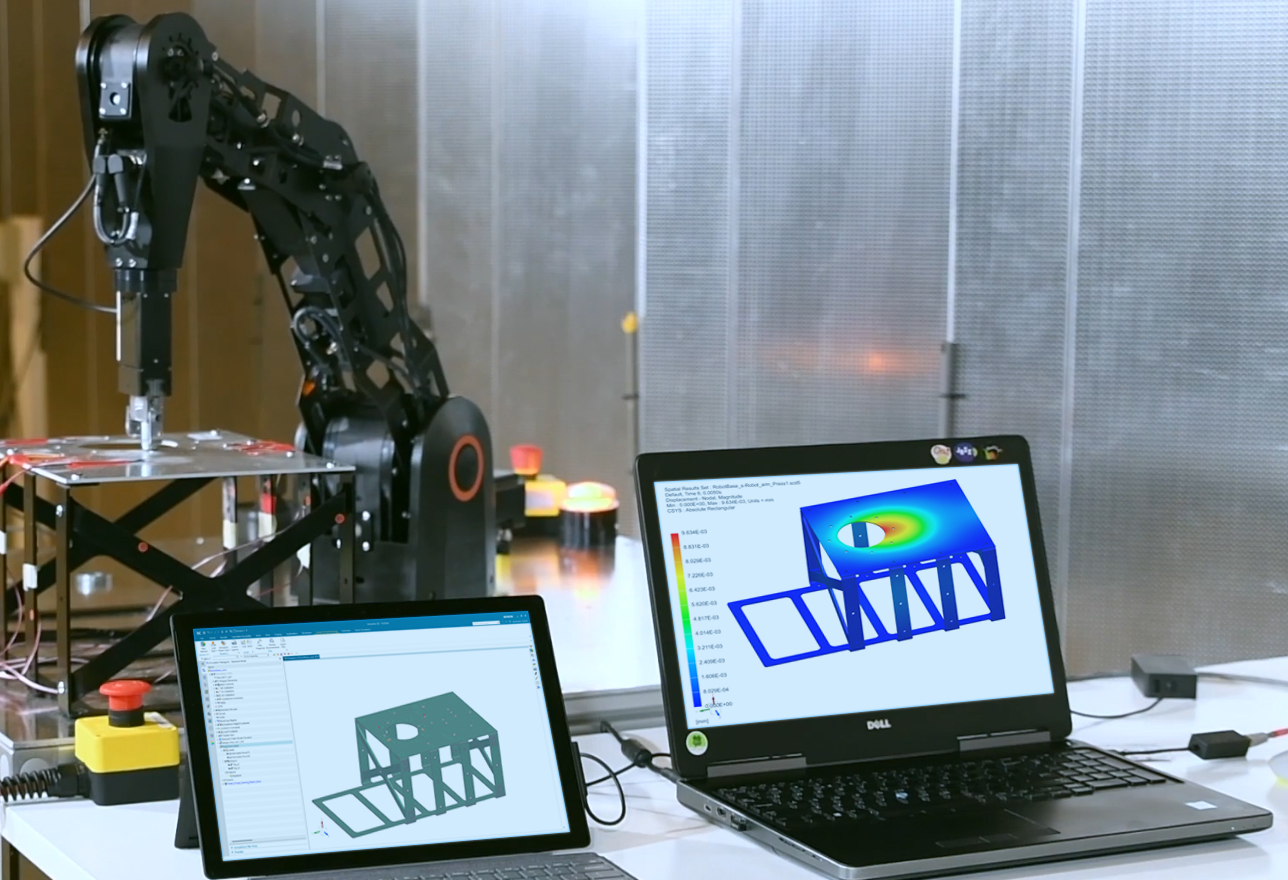
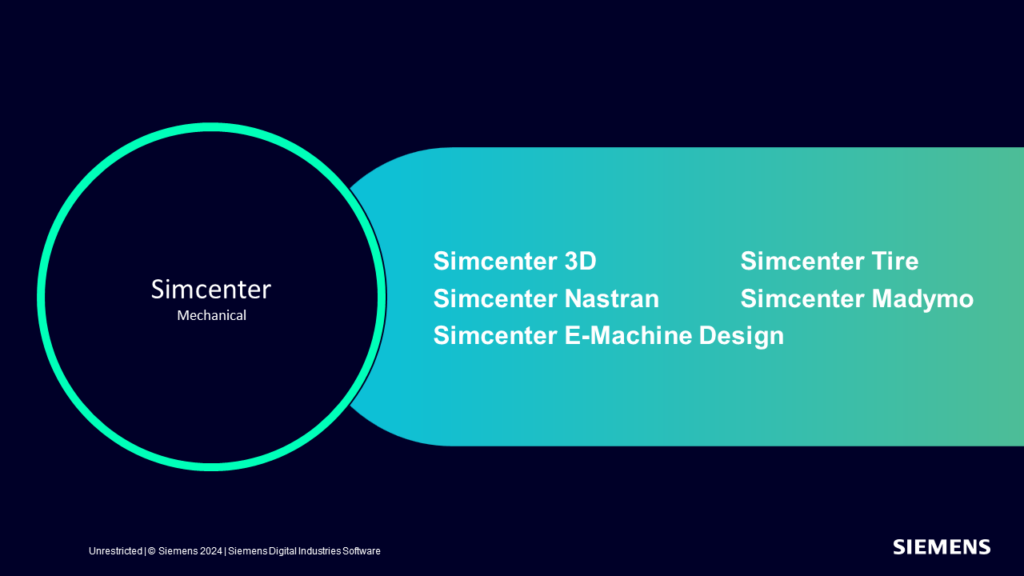
At Siemens, we develop technology that empowers our customers to transform their industries. We continuously improve our simulation software to simplify workflows and better integrate engineering teams. The latest product releases pull down barriers and blur the lines between simulation and physical testing, making engineering teams more integrated than ever before. Now, with reduced order models, you can simulate faster than in real-time, and with physical tests in the loop, you can integrate across engineering domains and explore new possibilities.
We set our engineers on a mission to improve our solution in one of four ways, and therefore, the enhancements to Simcenter 3D 2406 can be considered in the same four categories:
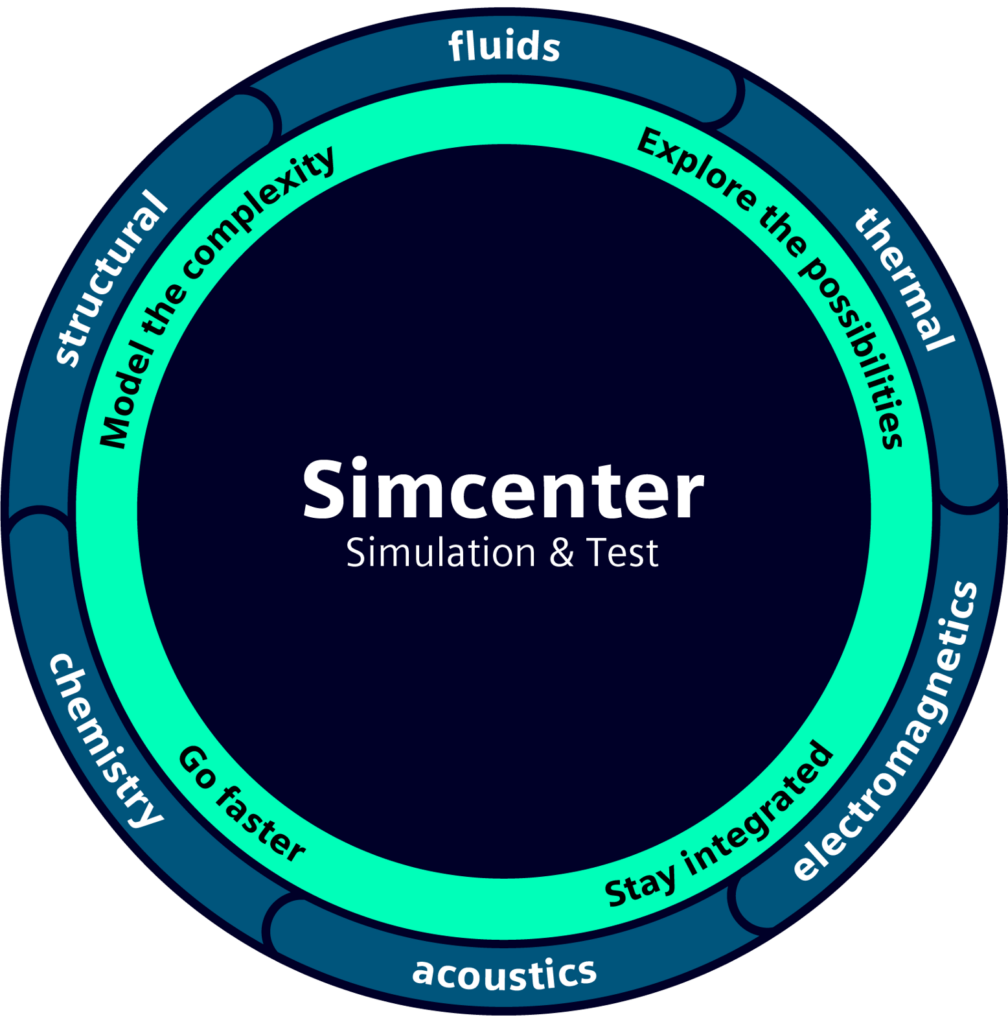
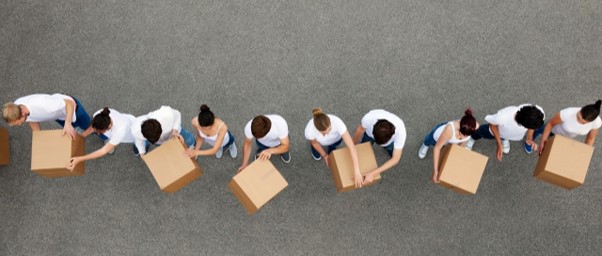
Stay integrated
Integration is imperative to maintaining robust workflows between simulation engineers who are experts in different fields and between simulation and other engineering, design and testing teams. In this release, we further integrate durability simulation and test engineers.
Simcenter 3D Smart Virtual Sensing:
Optimal Sensor Placement
Physical tests require a prototype specimen to be outfitted with many expensive sensors to record what happens to the product in the real world. However, technicians often do not know where and how to place sensors on the prototype to get good data. Instead, they use more sensors than they need, which takes more time to set up the test. Simulation with the new Optimal Sensor Placement capability in Simcenter 3D Smart Virtual Sensing can help identify exactly how many sensors are needed, where they should be placed, and their orientation to get good physical test measurements. This reduces the cost spent on unneeded sensors and saves time spent on instrumentation. Now, with good physical test data, they can optimize their future simulation models to more accurately predict physical test results. Capturing accurate physical test data also feeds downstream simulations, like durability analyses.
Simcenter 3D Smart Virtual Sensing:
New event in Simcenter 3D Specialist Durability
With Simcenter 3D Durability and Simcenter 3D Smart Virtual Sensing, you can predict the accurate loads for your durability analysis using just a few strain measurements. Simcenter 3D carries out the load prediction by leveraging both measurement and simulation data with an integrated data fusion method. Predicted loads are passed to Simcenter 3D Durability via a dedicated Smart Virtual Sensing Event. With this event, you can carry out the full durability post-processing analysis from max stresses and safety factors to any durability result.
Simcenter 3D Space Systems Thermal:
Send orbital fluxes to Simcenter Amesim for solar panel modeling
The latest integration improvements not only help Test Engineers but System Engineers too. In Simcenter 3D Space Systems Thermal, updates to the co-simulation interface allow the selection of all, convective, radiative, thermal loads, or orbital heat flux sources to exchange with external solvers. Therefore, systems engineers using Simcenter Amesim can include the thermal data in their system model to better understand the thermal effects on solar arrays, batteries, equipment electrical loads, and more. This combined Simcenter package, therefore, enables systems engineers to model the battery charge and discharge cycles and conduct a power budget analysis.
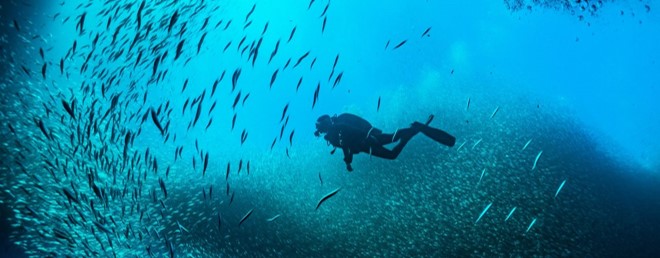
Explore the possibilities
To fully understand the intricacies of complex models with numerous interacting parameters, it is often useful to conduct a comprehensive design space exploration. However, this can be labor intensive, can suffer from human mistakes such as believing a local minimum to be the optimum result, and be simulation time-expensive. Simcenter 3D Design Space Exploration helps you automate this process to both speed up the process and reduce errors. The optimization engine uses a statistical model to select candidate variables for each simulation batch based on the results of previous simulations. Once the study is complete, results from all tests can be compared in its post-processor to get a better insight into feasible and unfeasible designs.
Simcenter 3D Electromagnetics:
Evaluate multiple design possibilities with multi-variable parameterization
Leverage the combination of Simcenter 3D Design Space Exploration with Simcenter 3D Low-Frequency Electromagnetics to quickly explore design options for electromagnetic performance. You can create a design table with multiple configurations for your geometry, mesh, and materials and then automatically evaluate them all to find the best-performing design.
Simcenter 3D Motion:
Enable early design phase gearbox multi-attribute balancing with an NVH focus
Simcenter 3D Motion introduces its new dedicated tool, gear design optimization, which also leverages the power of design space exploration. In this case, the tool provides a preconfigured gear design optimization project, including industry-specific post-processing capabilities that allow for multi-attribute optimization of gear designs.
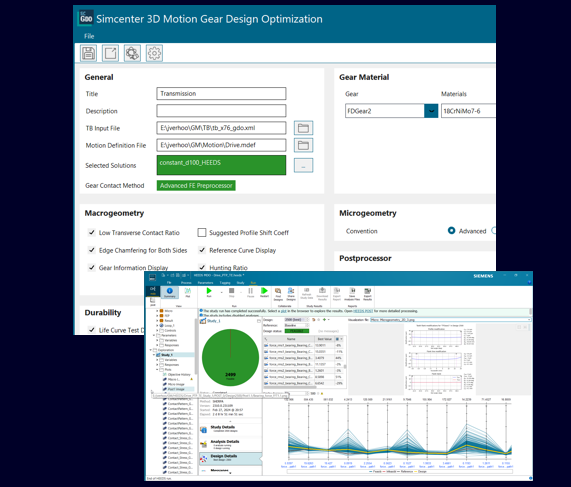
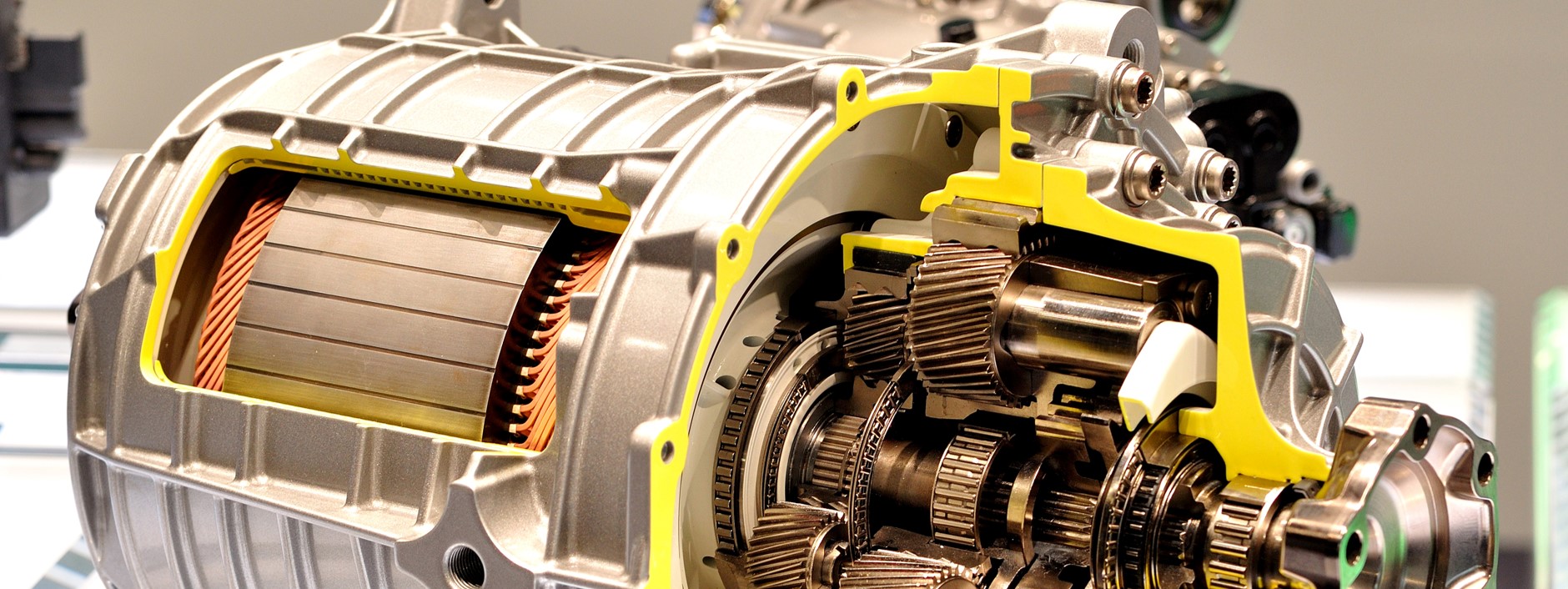
Model the complexity
Simcenter 3D Acoustics:
Support mapping of electromagnetic forces for NVH analysis of step-skewed rotors
For Permanent Magnet Synchronous Motors (PMSM), force spikes occur due to the alignment of rotor magnetic fields and stator teeth/slots. To reduce the spike and the subsequent torque ripple, it is common to step skew the rotor design. Such designs are easy to produce in Simcenter E-Machine Design, and with the latest update, you can import the multi-slice force information into Simcenter 3D and distribute it to the full vibro acoustic model for further NVH analysis.
Simcenter 3D Motion:
New and updated functionality for modeling compound planetary gears, asymmetric gear contact and thrust needle bearings
The intuitive definition of compound planetary gears in Simcenter 3D Motion Transmission Builder allows you to specify the most common industry layouts with minimal data entry. Compound planetary gears are compact and can handle high transmission ratios and power density, but their complexity heightens the risk of misalignment due to dynamic conditions, which in turn change the contact conditions. Therefore, to optimize NVH performance, it is imperative to find simple methods to negate misalignment and to understand the influence of gear mesh phasing and manufacturing errors.
To overcome these challenges, the latest updates provide the Analytical – Empirical gear contact stiffness method that allows engineers to specify the gear contact for asymmetric gears. Furthermore, you can now model needle-rolled bearings within Simcenter 3D Motion Transmission Builder to better understand the non-linear behavior of this bearing type.
Simcenter 3D Rotor Dynamics:
Unsymmetric models and multiple harmonics
The frequency response of rotor dynamics has been updated to include applied loads with different frequencies, and then subsequently use multiple harmonics to simulate the vibrational behavior on unsymmetrical models. To efficiently model an anisotropic rotor within a stator, a new mixed reference frame approach is now available. Model your anisotropic rotor in a rotating reference frame using equations while your stator is modeled in a fixed reference frame, allowing you to avoid periodic functions of time. Then, in post-processing, each harmonic response is output, and harmonics are combined in orbit plots to compute the resulting vibration.
Simcenter NASTRAN:
Avoid harmful resonance
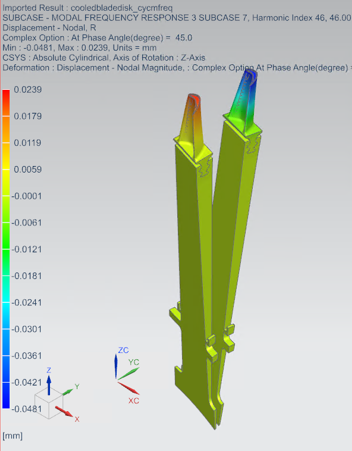
Perform a modal frequency response on a cyclic symmetrical structure to avoid harmful resonance cases.
Modal frequency response can be computed for a cyclic symmetry structure with a model defined in Simcenter 3D. Furthermore, you can include nonlinear effects (sliding contact, creep and plasticity, and large displacements), during the loading phase.
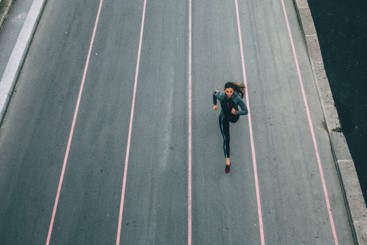
Go faster
Meshing is often the most time-intensive task for a simulation engineer; therefore, tools to improve this process can result in huge benefits. The updates to Simcenter 3D Engineering Desktop include two tools that will do just that.
Simcenter 3D Engineering Desktop:
Box imprinting and 2D touch point remesh, meshing tools
The Improved box imprinting for the mapped hole mesh control provides you with a new box option to create mapped-like mesh in a square-shaped region around selected holes. With additional options to define parameters such as box depth, elements through depth, lock box boundary, and extend-to-face boundary, you have control over the final mesh, but it’s a lot quicker. Additionally, the new 2D Touch Point Remesh command provides a quick and intuitive way of locally remeshing small element patches around a specified point.
Simcenter NASTRAN:
10% faster for large contact models
Reducing the complexity or repetition of the processes carried out by engineers is not the only way our software can save you time. Reducing the time the solver takes to solve a simulation, even by a small amount, can have a large total effect when replicated over many simulations. Our developers, therefore, continuously review the code to find ways of improving performance.
The Simcenter NASTRAN Multistep Nonlinear SOL401 MUMPS update makes it up to 10% faster when solving large contact models.
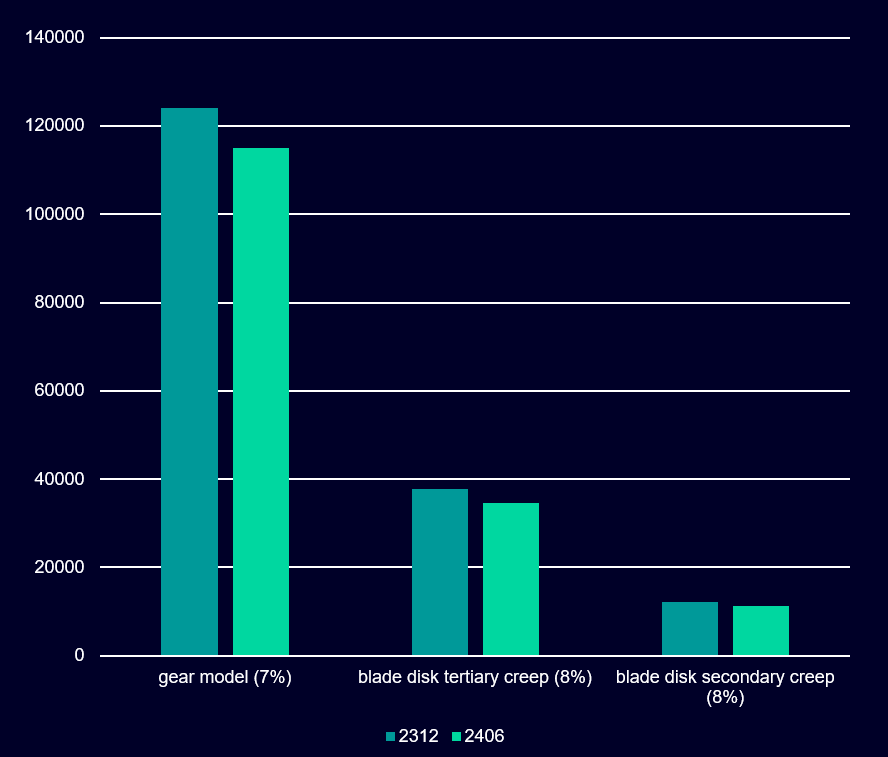
Download the Simcenter 3D trial, or if you are already a customer, get the latest updates.
Find out more
Existing customers and employees can find out more in our long-format introductory video, via this link: