Advancing bevel gear contact simulation towards quiet transmissions
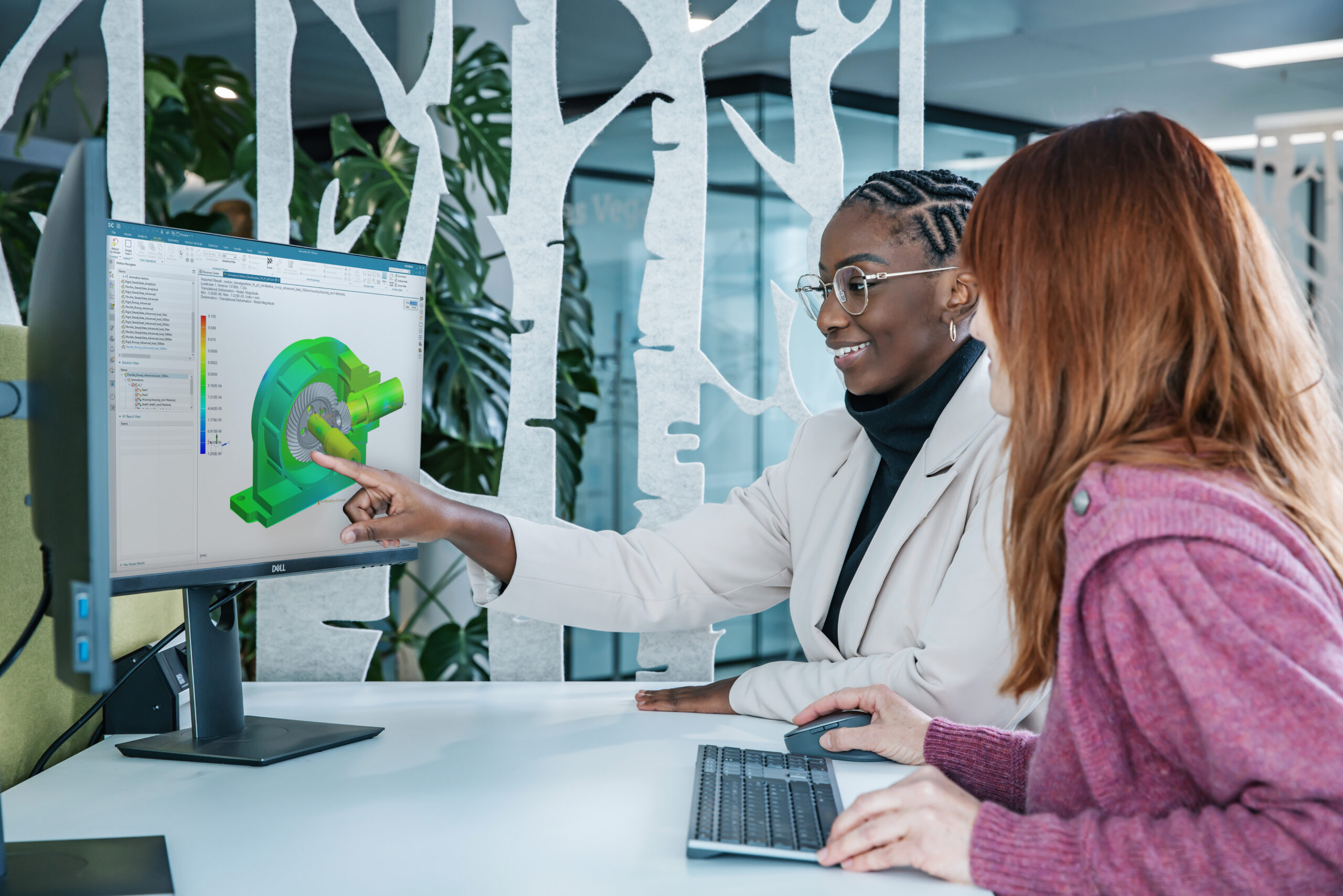
Vehicle electrification triggers an evolution of the vehicle design process
The rapid growth of electrification is drastically changing the foundations of vehicle powertrain development. The automotive industry can no longer leverage the experience it has gained over more than a century in internal combustion engine (ICE) powertrain development. On top of that, the market environment changes quickly due to altering regulations and many newcomers entering the market. The challenge is now to stay ahead of the competition and differentiate for electric drives.
Noise and vibration play an essential role in the overall comfort of a vehicle. Electric vehicles (EV) make the contribution of the gearbox to the entire noise signature more prominent [1]. Next to planar gears (that transfer rotational energy in the same plane), also bevel gears are used to transfer rotational energy into another rotational direction (e.g. in the vehicle differential). A crucial understanding of the bevel gear dynamics performance is the cornerstone for providing a system-level understanding of the bevel gear performance, which is elaborated in this article and in our new White Paper [6].
Resolving the bevel gear dynamic simulation challenge
Bevel gears are instrumental for the mechanical design and operation of the vehicle, but they represent a challenge for design engineers as their dynamic simulation performance, as well as the noise and vibration performance, are more difficult to predict and optimize.
Considering the growing need for accurate gear models that integrate into a system-level design process for mechanical transmissions, a clear simulation technology gap has been identified for bevel gears. While simulation methods for spur and helical gears have evolved to enable accurate prediction of lightweight gears within flexible multibody simulations, the numerical prediction of bevel gear contact dynamics is often hampered by challenges in the contact detection and contact force calculation.
To resolve the bevel gear vibration challenge towards quiet transmissions, Siemens Digital Industries Software has developed an innovative numerical analysis solution for bevel gear transmission acoustic emission [3]. This involves using a 3D gear contact force model within the Simcenter 3D multibody system dynamics simulation environment [4], enabling vehicle manufacturers to design and deliver tomorrow’s quiet transmissions within the growing EV fleet.
A novel advanced contact simulation solution for bevel gears
Simcenter 3D’s new bevel gear contact element provides a modular approach to bevel gear simulation that bridges the gap between accurate tooth flank description, fast 3D contact detection and contact force calculation with various levels of accuracy [4] into system-level calculation of dynamics and acoustics [5].
The new bevel gear contact element, achieved thanks to recent research and technology innovation efforts, includes three types of contact forces: a stiffness gear contact force, a viscous damping gear contact force, and a Coulomb-based friction force [2][3], and it can be used to analyze both straight and spiral bevel gear dynamics within the multibody simulation environment of Simcenter 3D Motion [4].
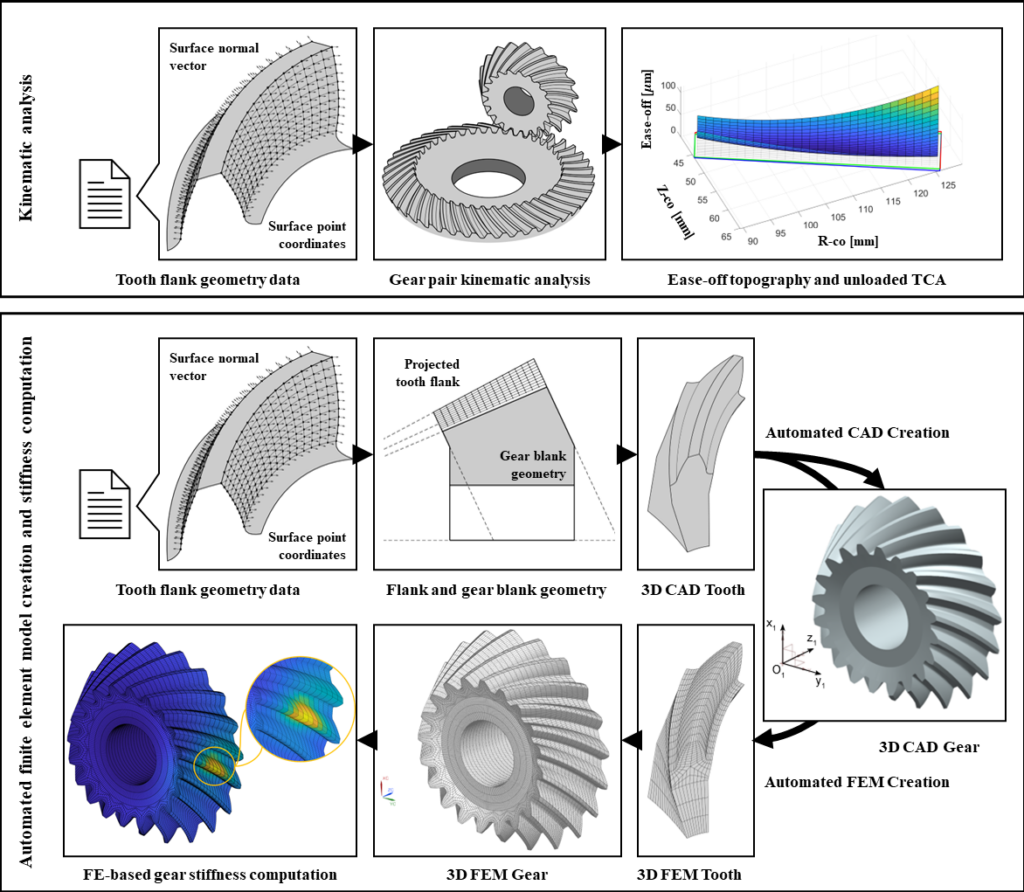
New White Paper: Advancing bevel gear contact dynamics simulation
Beyond the introduction provided in this blog post, we invite you to check out our new White Paper [6] with a detailed description of the new advanced bevel gear contact dynamics simulation approach and its value for your applications. The White Paper addresses the main challenges in numerical prediction of bevel gear contact dynamics by proposing a solution that enables the inclusion of a novel semi-analytical bevel gear contact stiffness model for highly accurate and efficient simulation results. This new stiffness model relies on model order reduction of finite element (FE)-based models to describe the bevel gear tooth and blank deformation, and analytical modeling to predict the tooth contact deformation. The overall process flow is shown in Figure 1.
The proposed methodology is validated further in the White Paper against high-fidelity nonlinear finite element analysis (NLFEA)-based contact simulations to evaluate the predicted transmission error, contact pattern, and contact pressure distribution. Figure 2 presents the results for one of these validation cases, namely the analysis of a spiral bevel gear set where the wheel has a lightweight gear blank design. Not only does the Simcenter 3D Motion gear contact element with FE-analytical bevel gear contact stiffness formulation correctly capture the modulation (of order 3 due to the presence of the 3 holes in the gear blank), but it also turns out this new gear contact element is multiple orders faster than the classic NLFEA-based contact simulations (e.g. minutes vs days), while achieving a similar accuracy level. Finally, two use cases are presented to demonstrate how the methodology enables new insights into spiral bevel gearbox dynamics and NVH performance. More details on all of this are found in the White Paper.
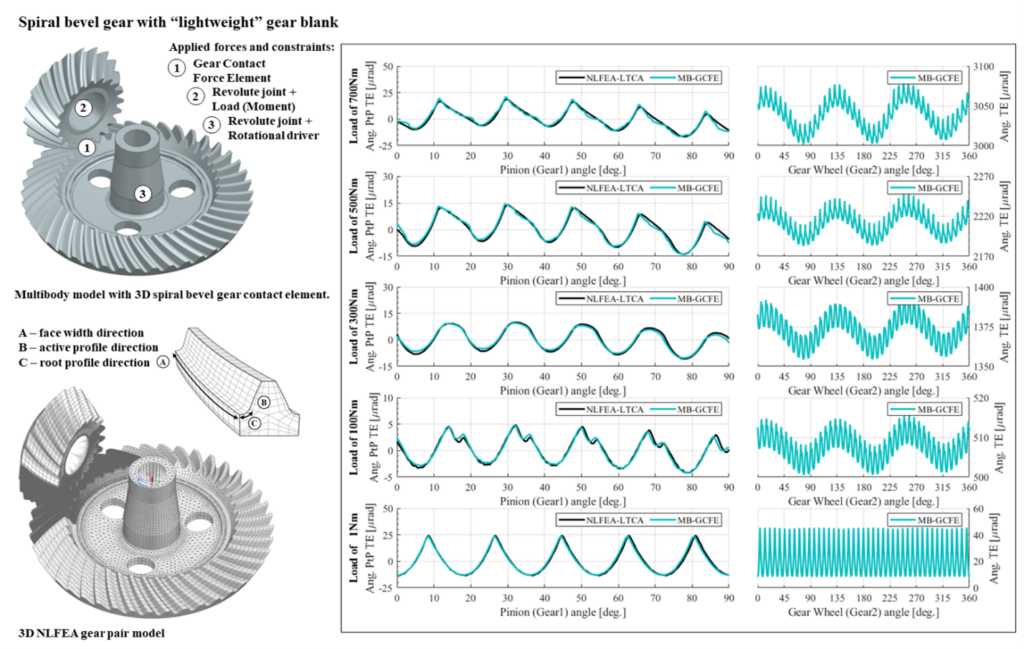
These new capabilities of Simcenter 3D were made available in June 2024, enabling vehicle manufacturers (and other manufacturers that use bevel gears as crucial components in their mechanical design) to predict bevel gear noise and vibration behavior in the design phase, which is crucial to achieving quiet transmissions.
Acknowledgments
The R&D work leading to this publication has been performed in the frame of the VLAIO Innovation Mandate Project “Advanced techniques for system-level simulation of Hypoid and bevel gEAr Dynamics” (“AHEAD”), conducted by Dr. Mathijs Vivet, with industrial partner Siemens Digital Industries Software and academic research partner KU Leuven, project nr. HBC.2019.2177, from 01/09/2019 – 31/08-2022.
References
- Jonas Verhoogen and Jonathan Melvin, “Bevel gears whine no longer due to unseen pressure”, Simcenter Blogpost, January 5, 2022.
- Mathijs Vivet and Stijn Donders, “Mastering bevel gears simulation towards quiet transmissions”, Simcenter Blogpost, September 4, 2023.
- Mathijs Vivet, Ali Rezayat, Jonas Verhoogen, Korcan Kucukcoskun, Stijn Donders, “Numerical analysis of bevel gear transmission acoustic emission using a 3D gear contact force model within a multibody system dynamics simulation environment”, Proceedings of VDI International Conference on Gears 2023, Garching, Germany, September 13-15, 2023.
- Siemens Digital Industries Software, “Simcenter 3D Motion Simulation”, Retrieved 2024.
- Siemens Digital Industries Software, “Simcenter 3D Acoustic Simulation”, Retrieved 2024.
- Siemens Digital Industries Software, “Advancing bevel gear contact dynamic simulation”, White Paper, 2024.