6 inspiring applications of CFD software for vehicle water management
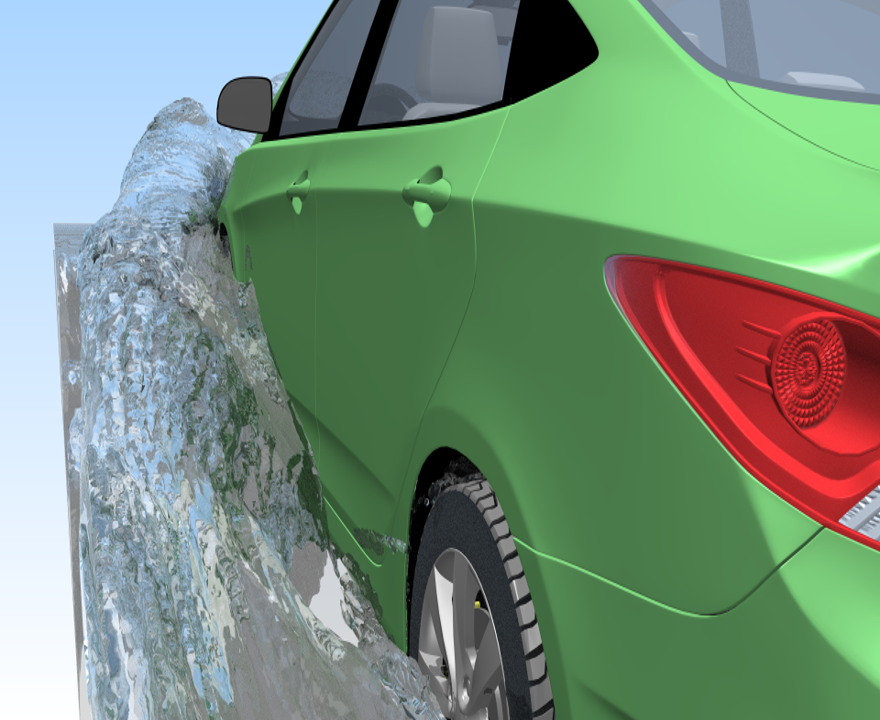
This vehicle water management blog post was co-written with Jay Masters, CFD Program Manager, Simcenter Engineering at Siemens Digital Industries Software.
While visibility in the rain and snow is important for traditional vehicles and drivers, it has become even more crucial with the increase in autonomous and electric vehicles. Engineers are now being tasked with new, more complex challenges:
- How much water is present on or around a vehicle’s sensors?
- What does another vehicle look like to my vehicle’s sensors?
- How is driver visibility?
There are also several variables involved that will determine how well an engineer will be able to address these questions during the development phase. In this blog post, we will explore some common vehicle water management challenges that companies today are facing. We will then showcase 6 ways the Simcenter Engineering and Consulting Services team has used Simcenter’s suite of CFD software to solve these challenges.
First, what are the challenges associated with vehicle water management?
Weather
Unless you’re in a place where it’s sunny 90% of the time, weather can be a fickle friend. For testing situations such as electric vehicle wading, it can be difficult to perform real-world, outdoor testing. What if it doesn’t rain on the day that you planned to perform a wading analysis? What if the pond that you’ve been using for wading analysis has frozen over?
Sensors only work when they are clean
Autonomous vehicle sensors can be negatively affected by seemingly mundane factors. A bug, bird dropping, or spot of dirt can render a sensor completely blind.
Even if you can install something to clean the obstruction, it is possible to overclean a sensor. What if you replace the gas engine in an autonomous or electric vehicle with a full tank of sensor cleaning fluid? This would negate the benefit of removing the gas tank from the vehicle.
Pedestrian safety
In autonomous vehicles, camera soiling can also cause visibility issues. This can lead to pedestrian safety issues or it could cause the system to become disabled. Either way is not an ideal scenario for a driver. The below video (courtesy of the Simcenter Prescan team) shows an autonomous vehicle attempting to park in the rain and the possible result if a pedestrian walked nearby.
Windshield design
An obvious solution to the issues above would appear to be that the sensors should simply be placed behind the windshield rather than in front. Sounds easy enough, right?
Not so much. Doing so would raise a host of other problems for the sensor. The first is the angle of the windshield: windshields are curved, so this would cause a distorted view for the sensor. The second issue is the material of a windshield. Windshield glass is designed with human vision in mind, not a sensor’s vision. A sensor would likely not be able to see underneath a multi-layered windshield.
Don’t blame it on the rain, simulate it
The above example, using Simcenter’s CFD solutions, shows how all these factors can be simulated on a full vehicle. Using simulation, engineers can make informed decisions about where to put cameras, how to protect them, and how they will perform in an endless variety of scenarios.
The Simcenter Engineering team uses Simcenter STAR-CCM+ and Simcenter SPH Flow to model water behavior on vehicles. Below are 6 ways the Simcenter Engineering team has modeled vehicle water management.
Application #1: Electric vehicle wading
In the example above, Simcenter Engineering experts were tasked with simulating electric vehicle wading and predicting dynamic water levels in real time. This is particularly important for electric vehicles because of the battery’s location at the bottom of the vehicle. This simulation also provides a safe alternative to physical testing, or it can act as a stand-in when physical testing is not available (ie if a pond typically used for testing freezes over).
The 3D images show the user where the water is moving, while the 2D images show where the water can accumulate, which would be difficult to understand from 3D alone. Engineers can use this data to determine, for example, where additional sealing may be needed.
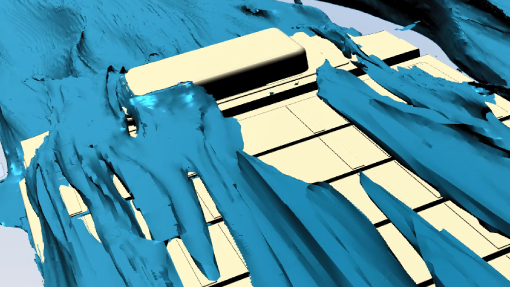
In this example, the Simcenter Engineering team used CFD software to gain a better understanding of wading and drainage time. This allowed them to identify wetted surfaces and drainage issues near the battery underpanels.
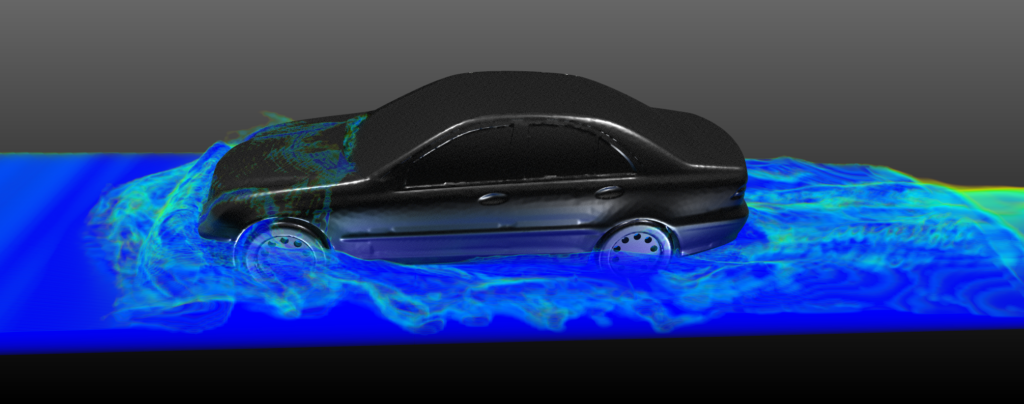
The water height near the front grille and wetted surfaces predicted in the simulation were validated against test site measurements and proved to have strong correlation with physical testing. The CFD surface pressure results can then be used as inputs to a finite element displacement/stress analysis. If needed, results can be provided to the customer in a generic jt-format to be viewed by non-CFD users.
This method has many other applications, including sensitivity studies to analyze impact of car ride height, heat exchange porosity, rain/soiling problems, and much more.
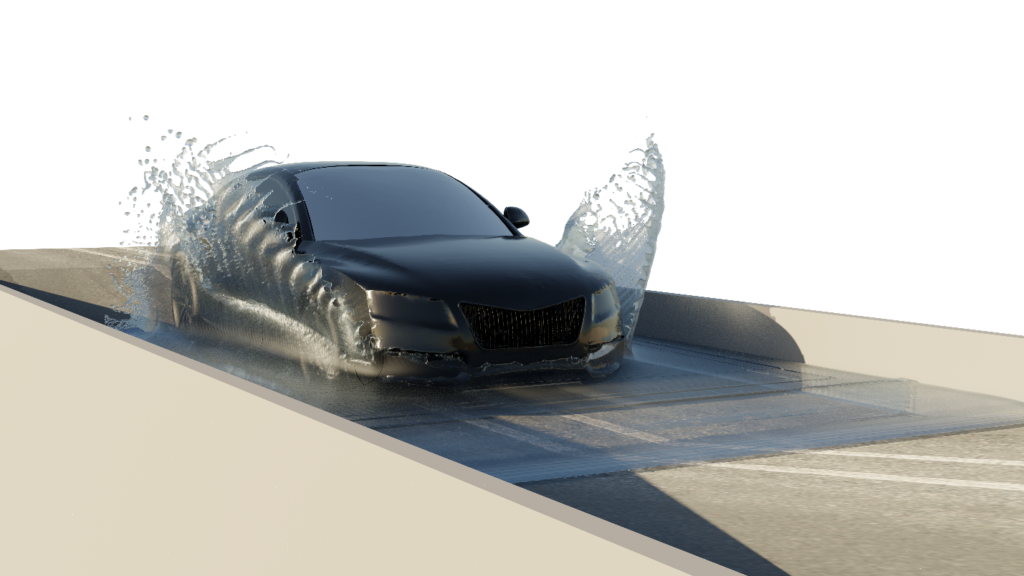
Application #2: Sensor cleaning analysis
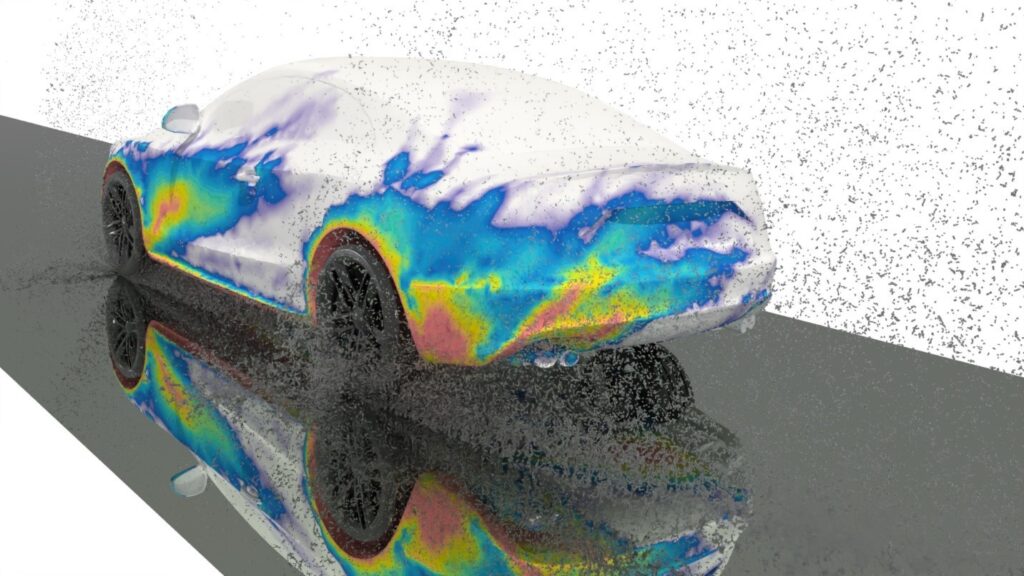
The study of sensor cleaning is still in its early stages. However, Simcenter Engineering recently partnered with a customer to simulate the spray cleaning of a LiDAR lens for autonomous vehicles. The team needed to predict spray behavior and impingement patterns on the LiDAR sensor’s window.

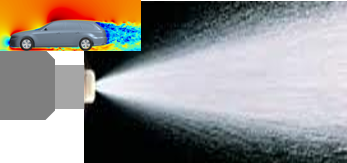
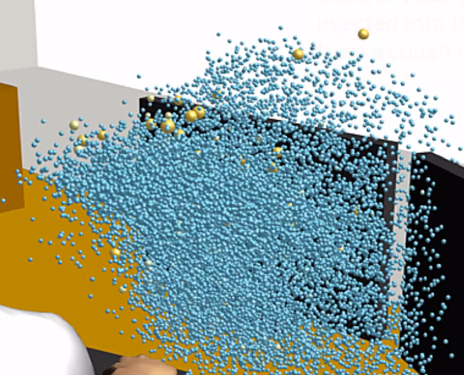
The primary atomization and secondary breakup were modeled within Simcenter’s CFD software. The primary droplets were tracked using Simcenter’s blob detection framework, and adaptive mesh refinement was applied to reduce modeling and simulation time.
The results of this study allowed the customer to take advantage of a detailed spray submodel that could be integrated into the full vehicle airflow model, with cone angle computed at every time step. Not only does this give the customer much more insight into the spray cleaner’s behavior, but it will also aid them in their mission to build a comprehensive vehicle water management program.
Application #3: Cowl drainage/run-off
Another area of interest to engineers looking to optimize vehicle water management is avoiding water accumulation in the trunk. Not only can this accumulation be annoying to car owners, but it can also accelerate corrosion in doors and frames.
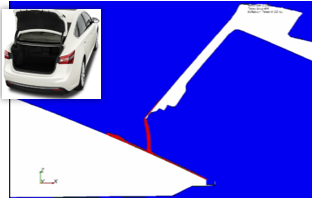
The Simcenter Engineering team used Simcenter to track water patterns on a vehicle’s surfaces. This allowed them to monitor thin film runoff and predict where the water would travel or pool. Additionally, simulation was used to compare results for different size drainage holes.
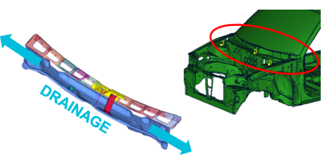
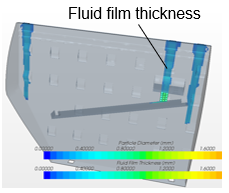
The results of this simulation helped the team optimize water channeling and sealing geometry to avoid water accumulation near the trunk and prevent corrosion. The simulation had high correlation to physical test and will help make sealing against water in vehicles more robust.
Application #4: Wiper/A-pillar analysis with spray
Wiper blade analysis is another area of vehicle water management that can benefit from the use of CFD software. The Simcenter Engineering team worked with a customer to predict the impact of rain or spray on driver visibility and identify pillar channel runoff issues.
Multiple techniques were used in this analysis:
- Modeling droplet impact on windshield
- Modeling fluid film edge stripping from droplets
- Film-to-VOF: Conversion-based on local volume fraction in the cell
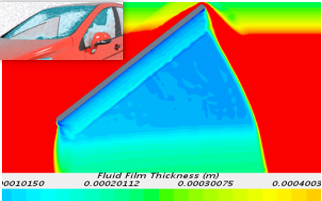
The software enabled engineers to account for fluid film on the windshield, pillar, side mirror, and side window, helping them identify pillar channel runoff issues. Additionally, the wiper motion was modeled in order to help the team evaluate different wiper blade designs.
The Simcenter Engineering team was able to reach an ideal blade design after analyzing complex seal geometry, wiper motion, and spray in Simcenter. Additionally, they identified critical sensitivities to contact angle and surface tension, which was also critical to blade design.
Application #5: Side mirror/window
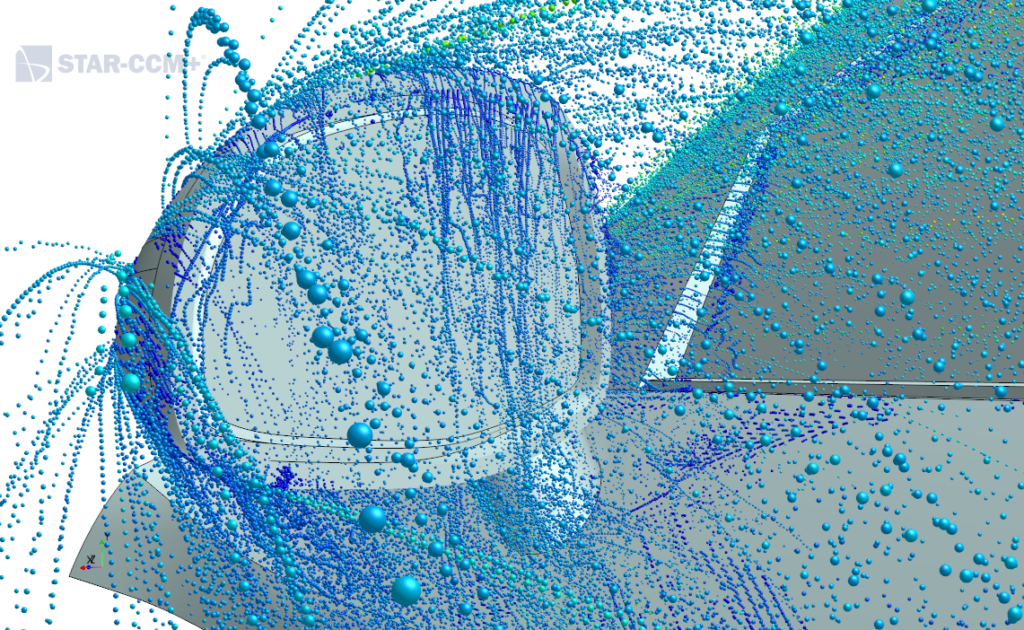
When driving in the rain, aerodynamic pressure forces water to the side windows. Simcenter Engineering experts recently worked with a customer to model the complete multiphase water transport path.
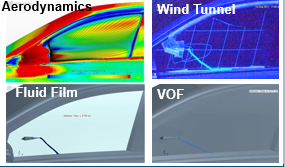
The team used Simcenter to model the droplet, thin film, and edge stripping of the water. The transitions between models were determined by the criteria provided by the customer. The team also simulated variable vehicle speeds and surface tension contact angles in order to provide the highest accuracy possible.
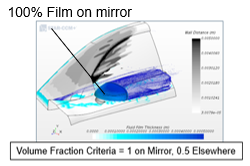
After modeling the full water transport path and comparing the simulation results to wind tunnel testing, the team determined that the best solution would be a pure fluid film on the side mirror to allow for edge stripping of droplets. This study gave the customer an easy solution to their side mirror challenges and dramatically reduced testing time.
Application #6: Snow ingestion
Snow is notoriously complex to simulate in CFD software. Snow’s properties, as well as its droplet shape, make accurate prediction difficult.
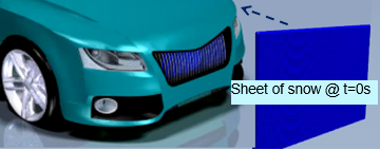
Despite the difficulties, the Simcenter Engineering team worked with a customer to predict snow ingestion and accumulation on vehicle surfaces. Using simulation, the team injected one “sheet” of particles to quickly evaluate multiple designs. This allowed engineers to observe several phenomena:
- Incident snow mass on vehicle surfaces
- Total mass of snow ingestion into intake and HVAC systems
- Impact of grille design variation on snow accumulation
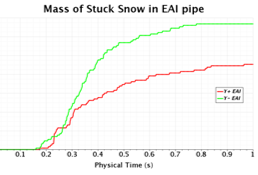
Considering the complexity of the problem, the team was able to perform the one-way coupled analysis in a relatively short amount of time. This study also allowed the team to confirm that qualitative comparison between many design variants is indeed possible when analyzing snow ingestion, and design optimization could be performed in future studies using Simcenter CFD solutions or HEEDS.
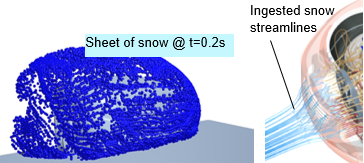
The role of CFD for EV/AV vehicle water management
While the world is still realizing the promise of electric and autonomous vehicles, the Simcenter Engineering and Consulting Services team is helping to make this field safer, more reliable, and more efficient. Using CFD simulation holds significant promise for vehicle water management, especially for AV/EV applications. To learn more, check out the resources below:
- Optimizing vehicle aerodynamics for rain water management at Daimler
- 4 myths about AI in CFD
- Tighter timeframes, tougher requirements, less stress? The argument for 1D-3D co-simulation
If you’d like to get in touch with Simcenter Engineering services, email us at engineeringservices.sisw@siemens.com.