4 Myths about AI in CFD
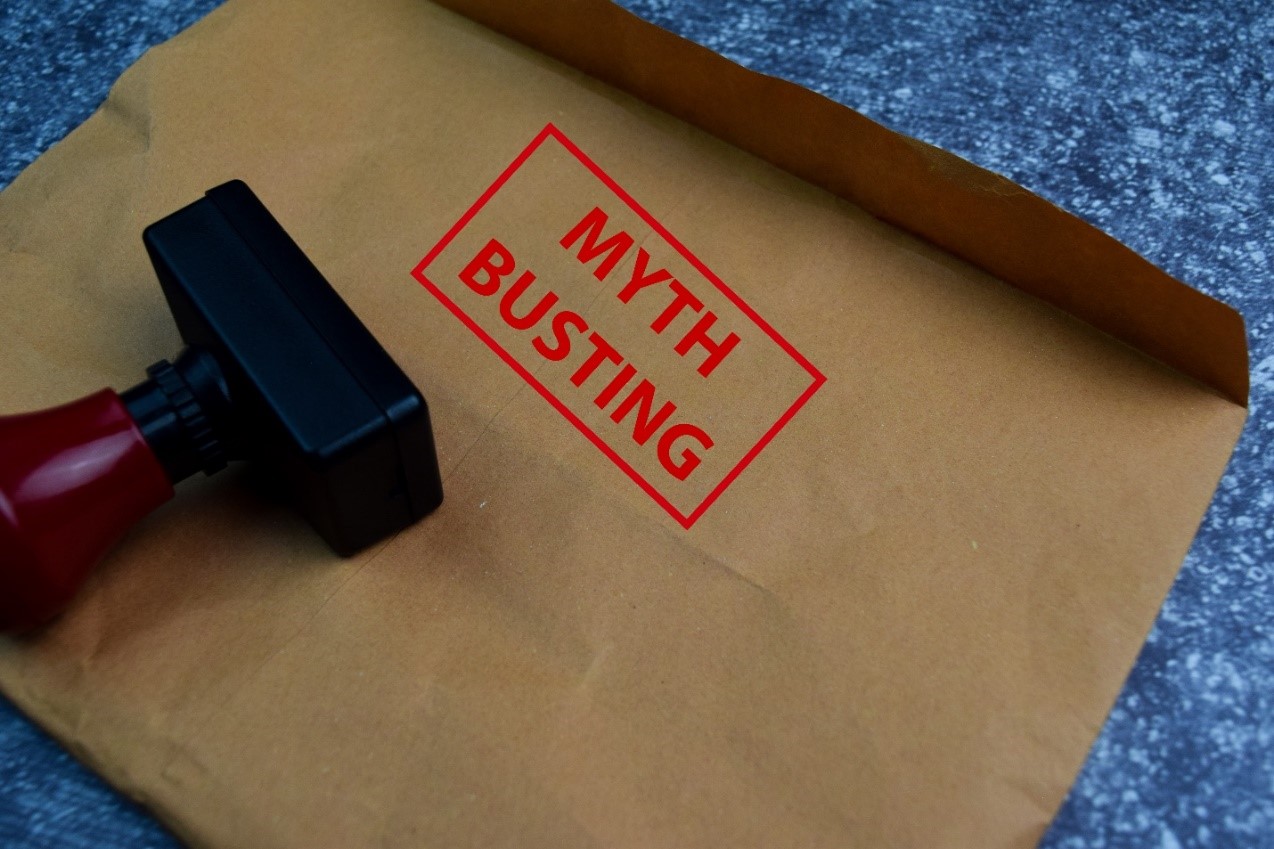
This blog was co-written with Krishna Veeraraghavan, Project Manager for Simcenter Engineering Services.
As Artificial Intelligence (AI) has become more ubiquitous in our everyday lives, so too has confusion about what it is and what it means for engineers. The definition of AI and the role it will play in future product development is often dependent on who you ask.
“The development of full artificial intelligence could spell the end of the human race.”
— Stephen Hawking (2014)
“Artificial intelligence would be the ultimate version of Google. The ultimate search engine that would understand everything on the web.”
—Larry Page (2000)
“Nobody phrases it this way, but I think that artificial intelligence is almost a humanities discipline. It’s really an attempt to understand human intelligence and human cognition.”
—Sebastian Thrun (2013)
So, what is AI exactly? For the purposes of this blog, we will focus only on the role of AI in CFD. We will also clear up some common myths around AI in CFD. But first, let’s establish some basic definitions.
(Before you begin reading, please feel free to share your thoughts on the state of AI in CFD by completing a brief survey).
What is AI?
AI is a multidisciplinary topic that enables machines, devices, and computers to think and make decisions in a way that would seem intelligent. AI helps machines and programs make smarter decisions by learning and improving in an iterative process based on the information they collect.
In the future, AI in engineering may focus more on collective intelligence. In this scenario, engineers and computers may work together in feedback loops to identify problems and develop solutions that can make the design process and systems work more efficiently. This would enhance the capabilities and contributions of the engineers.
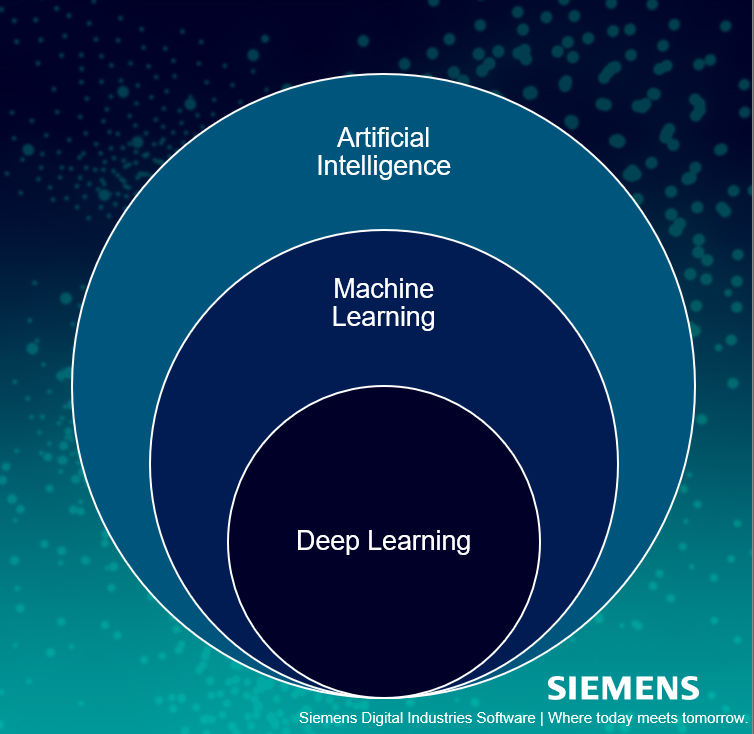
Collective intelligence
Collective intelligence refers to ways that data and technologies bring people, machines, and computers together to achieve outcomes that were previously beyond our expectations. Psychologists define collective intelligence as groups whose general ability is to perform well not on a single task, but on a wide range of different tasks. This is possible to achieve by combining human intelligence and machine learning.
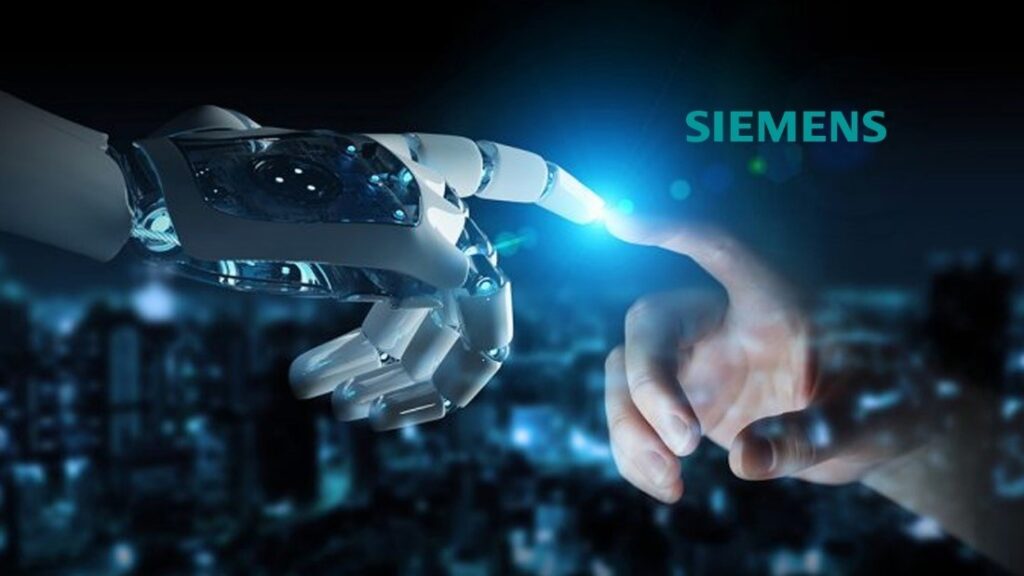
Machine learning
Machine Learning (ML), a subset of AI, is a self-adaptive algorithm that uses statistical algorithms to build and train systems and models. These systems and models will have the ability to learn and improve without being explicitly programmed to do so and can make predictions or identify hidden patterns in the data. Two types of machine learning widely used are supervised and unsupervised learning. All supervised learning will fall under either regression or classification problem. Input data for both cases can be numerical and categorical. Below are some general guidelines on which techniques are useful:
- Regression techniques, when output data is numerical and yields a continuous response (e.g. temperature response)
- Classification techniques, when output data is categorical and yields a discrete response (e.g. grille or not a grille, good design, not a good design)
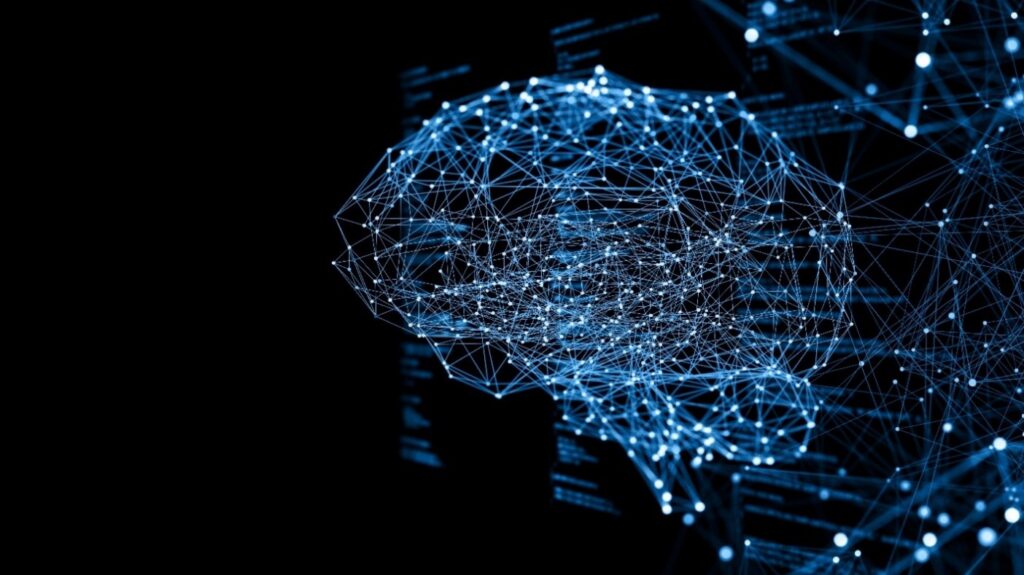
Deep learning
Deep learning is a subset of machine learning. Some of the most frequently used deep learning networks include convolutional neural networks, auto-encoders, transformers, and generative adversarial networks (GAN). Deep learning utilizes hierarchically organized artificial neurons to process data for extracting higher-level features from the raw input and for achieving machine learning objectives. Deep learning is distinguished by its use of many layers of artificial neurons and, consequently, a large number of parameters and hyperparameters. Optimizing hyperparameters can have an impact on the training of machine learning algorithms (a few examples include number of clusters in clustering algorithms, Bayesian optimization, gradient-based optimization, etc.).
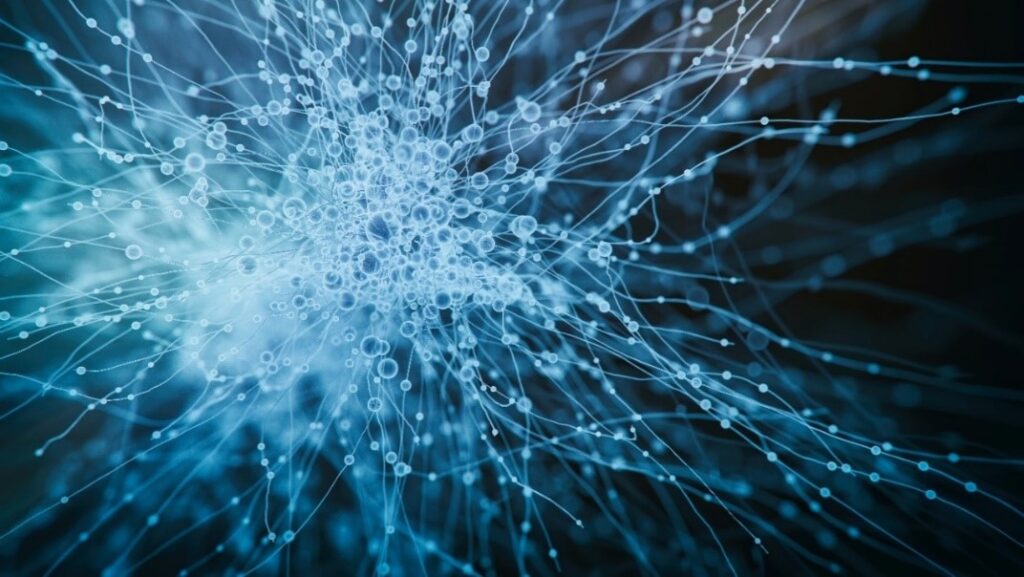
Reinforcement learning
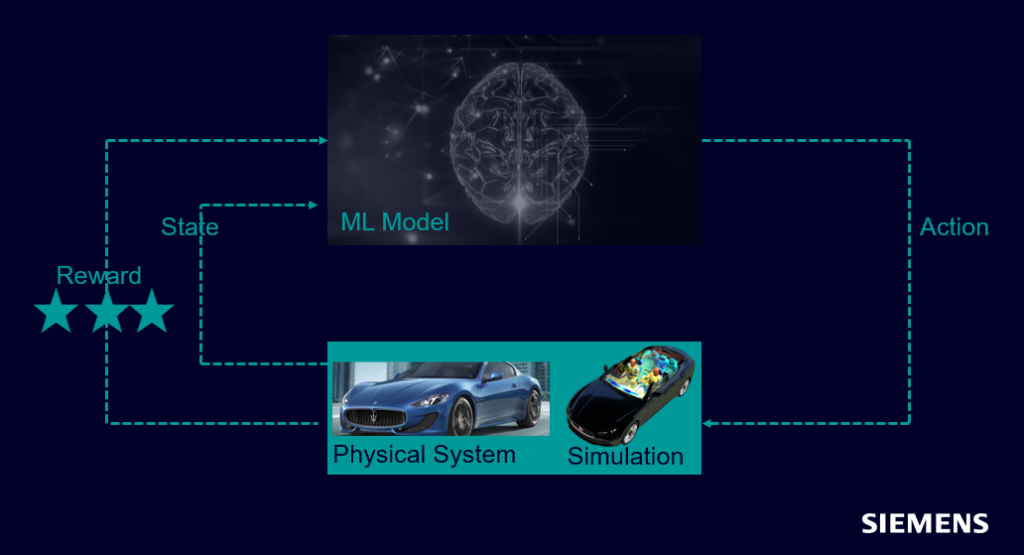
Reinforcement learning is one of three basic machine learning paradigms, alongside supervised learning and unsupervised learning. It is focused on finding a balance between exploration (of uncharted territory) and exploitation (of current knowledge) in order to obtain rewards. Reinforcement learning is learning what to do – how to map situations to take desired actions to maximize numerical reward signals. Reinforcement learning is the training of machine learning models to make a sequence of decisions and control actions to achieve a goal in an uncertain and potentially complex environment.
4 myths about AI in CFD
Now that we’ve established some common definitions, let’s do some myth busting.
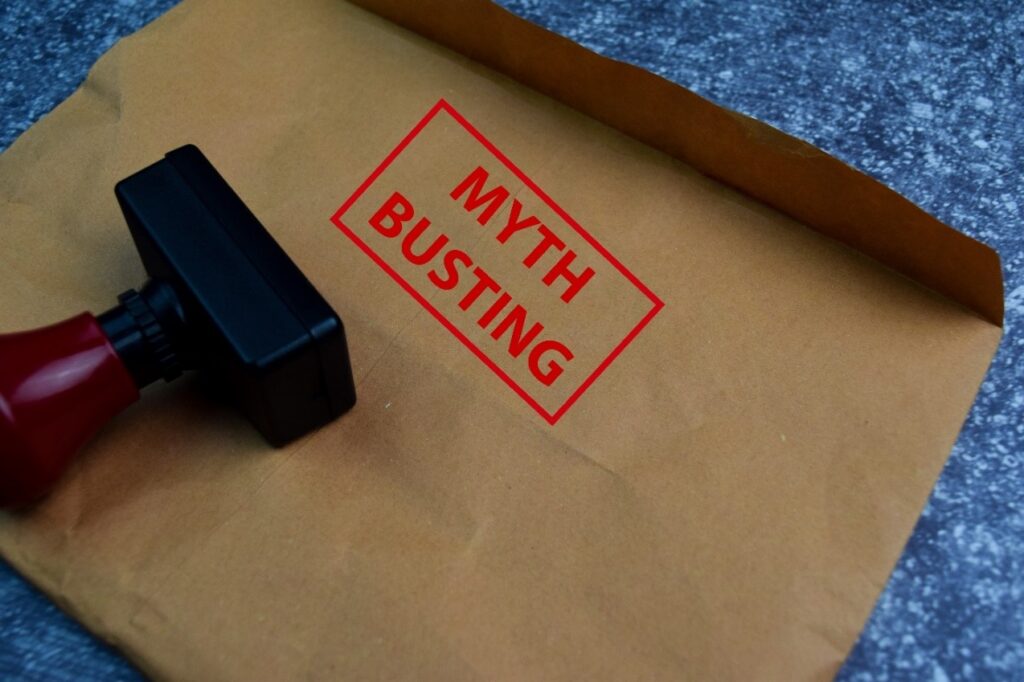
Myth #1: Numerical models are the only solutions available to solve difficult engineering problems. AI is not accurate enough to be a good fit for CFD and engineering problems.
Reality: Thanks to new technological advances, AI/ML solutions now exist that work well on subsystems with very minimal prediction error. Groups such as our very own Simcenter Engineering & Consulting Services have worked with customers to use AI/ML in design predictions to minimize CFD simulations.
Myth #2: Data science is easy and there are open-source tools that companies can use.
Reality: Generic machine learning algorithms cannot handle customer-specific engineering problems. Different applications require different machine learning algorithms and further problem-specific refinement (for example shape detection techniques). Although there are widely available image recognition algorithms, companies must develop an in-house shape detection algorithm to detect various shapes or components of a vehicle.
Myth #3: AI doesn’t require people to run it.
Reality: The value of AI lies in its ability to augment the capabilities of computer engineers and domain experts. By performing the monotonous and repetitive tasks, it helps engineers focus on solving more complex problems using CFD tools, such as Simcenter STAR-CCM+, to generate more meaningful simulation data for future predictions.
Myth #4: The more data, the better.
Reality: AI in CFD needs smart engineering data, such as Key Performance Index (KPI), relevant to the problem, to succeed. Our Simcenter Engineering Services group uses feature engineering technologies to achieve data reduction from simulation data to enable AI to deliver high-quality solutions.
Value of AI in CFD
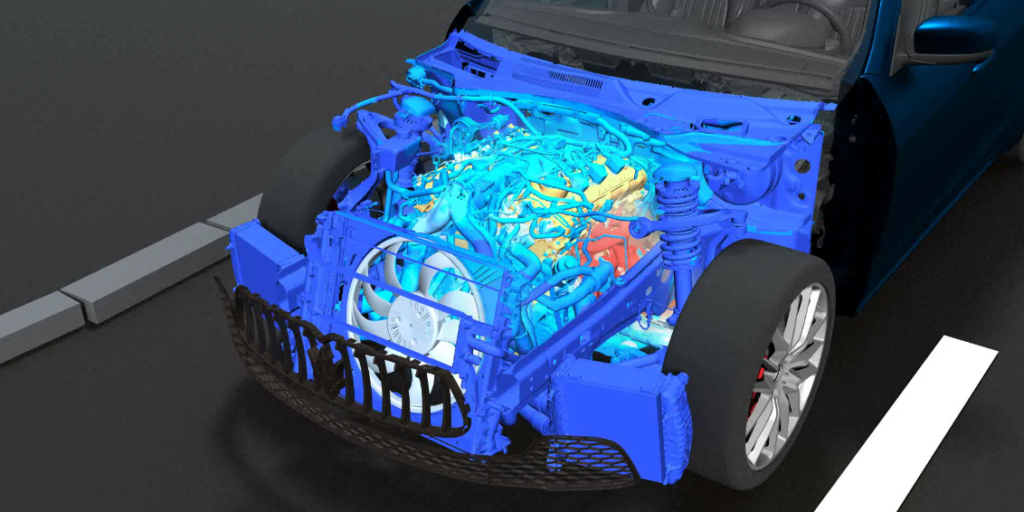
AI has transformed technologies in every industry. Applying AI to CFD applications can be a strategic asset to companies, as it can help reduce costs and create new differentiated values. AI-driven smart solutions offer substantial benefits to CFD engineers, designers, and analysts:
- Reduce computational, design program, and operational costs by creating more designs per simulation at a faster turnaround time
- Reduce the process and program development turnaround time with ML based surrogate models and smart AI driven workflows to expedite turnaround time
- Enhance the accuracy of simulations by flagging anomalies and providing knowledgebase workflow assistance in the CFD process. This includes CAD, physics modeling, mesh settings, and postprocessing.
- Improve product performance and efficiency by creating an ecosystem to simulate, predict, and optimize the product in a seamless way
- Provide knowledgebase workflow assistance in CFD
If AI in CFD is so great, why aren’t all companies taking advantage of it?
Implementing AI, particularly for a niche technology like CFD, can present some operational challenges for companies, including:
- Database management: Building and maintaining simulation and design database is a monotonous and expensive process which involves alignment of IT with various engineering groups. Engineering groups themselves are often disconnected, so the required coordination with an additional department can be a hindrance.
- Extracting feature engineering data & training the data for AI in CFD: There is a lack of required data science skills to extract desired features, build and train the data set for integrating ML techniques with CFD, CAE simulations and for design predictions.
- Talent: Delivering AI capabilities in CFD, designs and simulations require talent in machine learning, deep learning techniques and CFD skills.
What’s the solution?
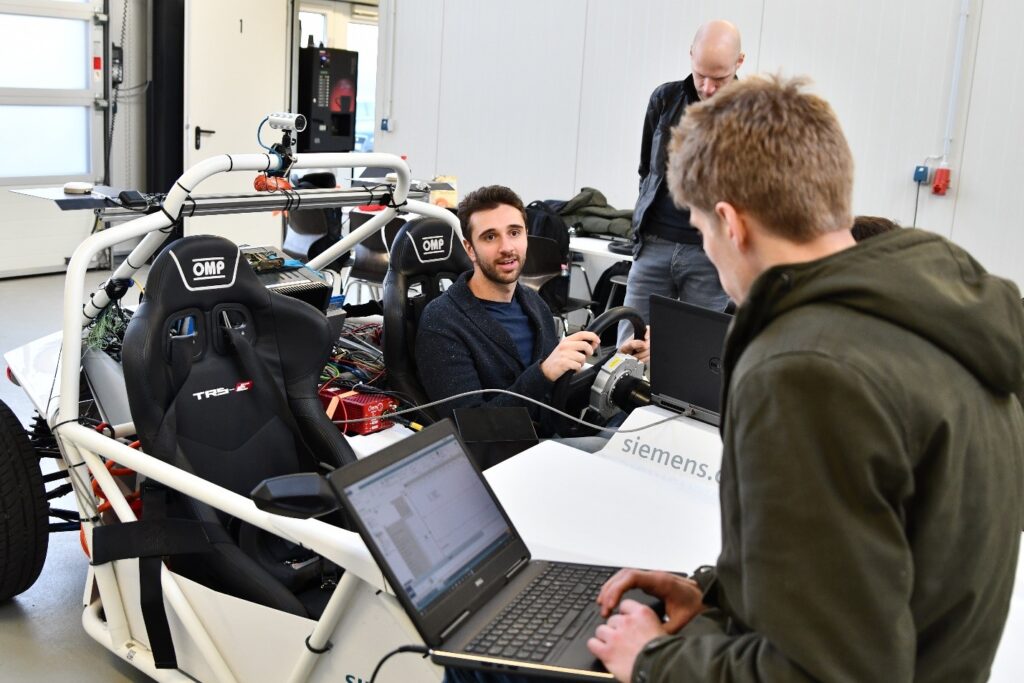
The Simcenter Engineering Services group at Siemens has developed AI solutions for CFD to solve these and other AI-related problems that companies are facing. These solutions enable companies to:
- Connect CFD with AI and multi field science to assist engineers in:
-Multi-physics design exploration studies
-AI-enabled control actions to enhance product performance - Drive innovation in designs and simulations by enhancing their digital twin capabilities. This is done by developing and deploying customizable AI solutions.
- Realize successful transformation for AI in designs and simulations by providing:
-Domain knowledge
-Build and train ML models with CFD and multi-science data
-Access to deep learning and ML techniques
Going beyond CFD
Industrial solutions for AI in simulations have been developed with the Siemens groups including model-based systems engineering, predictive analytics, physical testing, and system simulation engineering. These synergies allowed the Simcenter Engineering Services team to leverage domain expertise and deliver value that goes beyond CFD by focusing on AI/ML and statistical techniques that address what customers need in addition to what they want.
Real-world applications for AI in CFD
Our AI in CFD is focused on collective intelligence where humans and machines can work together in a closed loop ecosystem. This makes the engineering design process more efficient and helps engineers design and improve the performance of the system. A few examples of engineering problems that can be solved by AI solutions are listed below.
Predict discrete temperature using ML
For engineers responsible for thermal management, regression techniques can be used to develop a prediction algorithm based on input data (such as numerical/categorical) and output data (numerical).
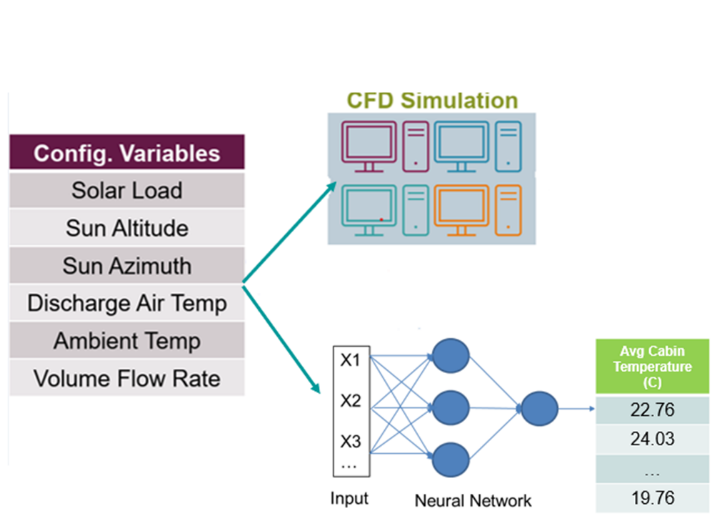
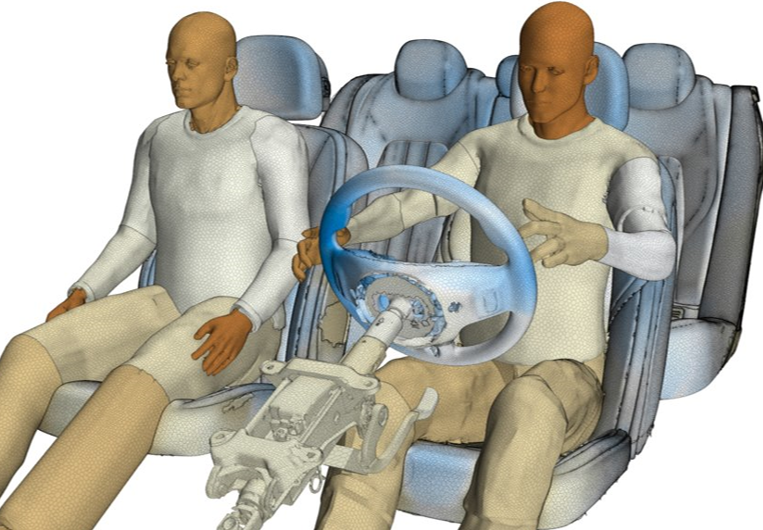
In the above example, the Simcenter Engineering Services team trained a neural network to predict the average temperature of a vehicle. This was done using 500 random samples out of 600 data samples generated by Simcenter STAR-CCM+ for various combinations of operating conditions. The KPI (temperature) was extracted to train the model. Out of the 600 samples, the team used 500 for training, and the remaining 100 were used to predict the accuracy of the model. Out of 100 data samples, 72 samples had less than 1% prediction error (difference in predicted temperature – actual temperature) and 28 samples had prediction error in the range of 1 to 1.66%. The maximum prediction error in the model was 1.66%, which corresponds to the temperature difference of <5 ⁰ C.
Regression techniques can also be integrated with control systems. Using CFD data, engineers can train the regression model, use it to predict values of relevant variables, and then take corrective control actions to achieve the desired target and improve performance (for example, based on the battery range remaining). Additionally, the model can predict the energy load and invoke control actions to adjust the cabin temperature accordingly.
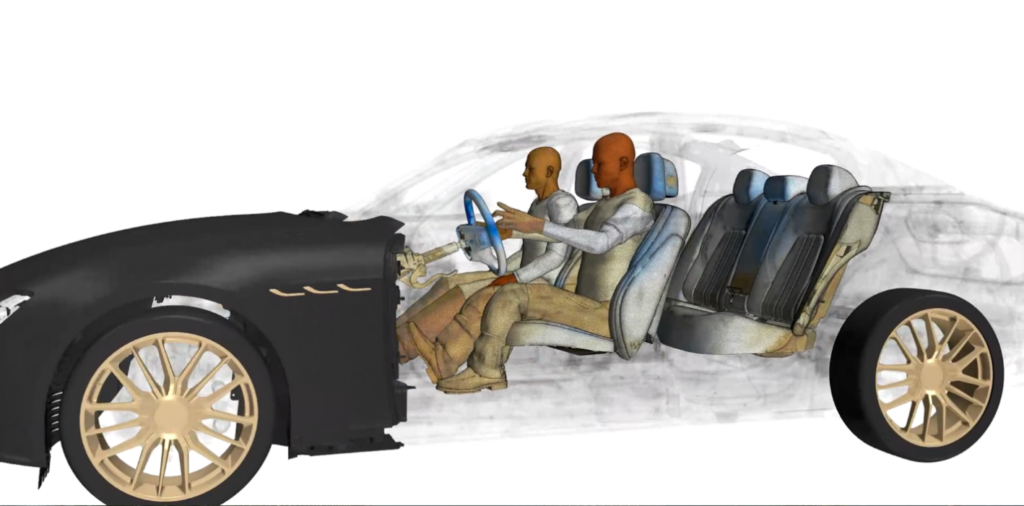
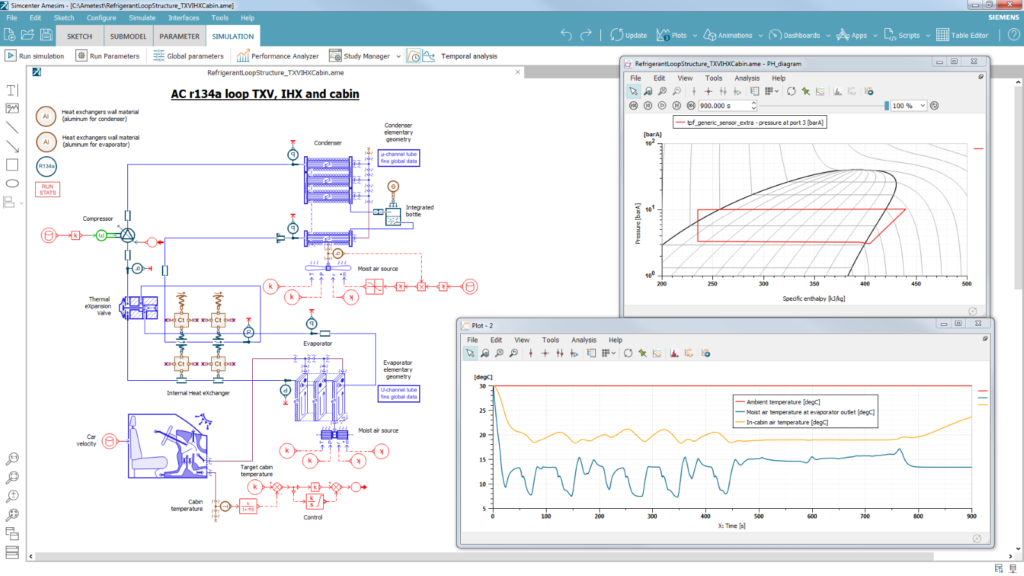
Predict cabin surface temperature using a convolutional neural network
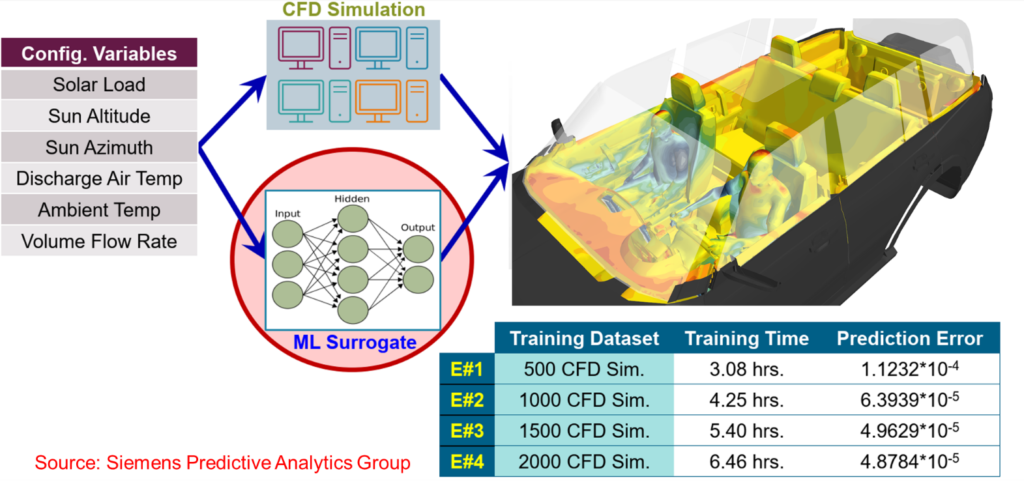
In a similar example, the Simcenter Engineering Services team in synergy with the Predictive Analytics team used data samples to build a convolutional neural network to predict the surface temperature distribution inside a vehicle cabin. In this exercise, a simulation database was generated by running CFD simulations for various operating conditions. While the team tested the application of 500 (Expt.1), 1,000 (Expt.2), 1,500 (Expt.3), and 2,000 (Expt.4) data samples to train the network, the prediction error remained stable. The team tested the accuracy of the neural network prediction with the actual CFD simulation results and found that the results from both techniques matched. We followed the below steps to compute the prediction error:
- Computed the square error between the true pixel value and the predicted pixel value
- Normalized it by the true pixel value
- Computed its average over the entire region.
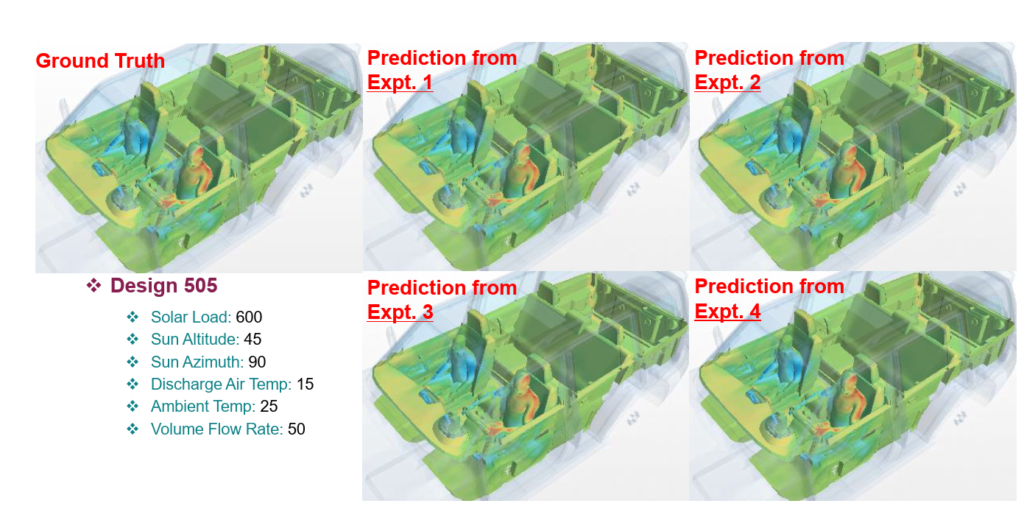
These tests proved to the team that AI techniques can be used for CFD simulations without compromising accuracy. By applying techniques such as those listed in the examples above, companies can free up their engineers’ time and enable them to perform more valuable, complex design and simulation tasks while maintaining accuracy.
Using AI-driven workflow automation to interpret fluid flow at multiple crank angles
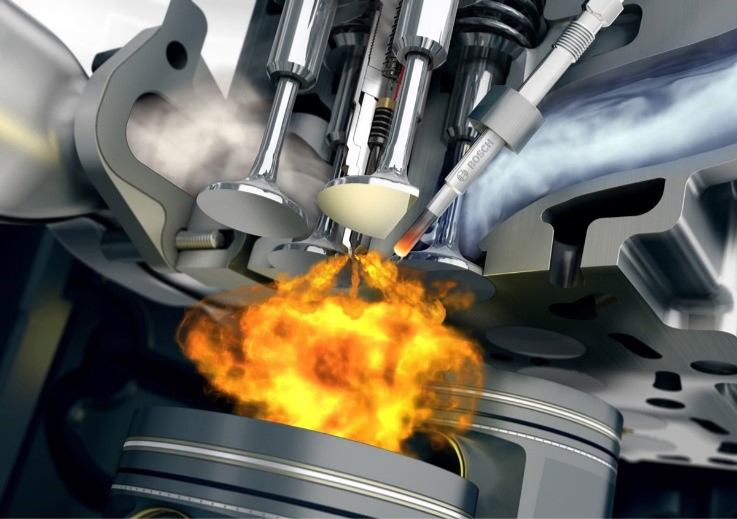
In a recent example, Subaru was looking to identify the link between fluid flow at multiple crank angles to tumble intensity at top dead center. The Simcenter Engineering Services team used flow feature images from in-cylinder analysis in Simcenter STAR-CCM+ to train the deep neural networks and develop an AI-based workflow to predict this tumble intensity.
The team then used feature engineering techniques and deep neural network for data reduction and to extract the flow features for multiple crank angles and classify the sub-features. As a result, the interpretation time was reduced from 10-20 hours using traditional techniques to just a few minutes using AI.
Improve workflow efficiency and better resolution of mesh
Classification techniques predict discrete responses (categorical) based on classifying input data (numerical or categorical). For example, in medical applications, they can be used to classify a tumor as benign or malignant.
For engineering applications, the Simcenter Engineering Services team has used shape detection techniques to expedite data preparation time from CAD BOM to CFD BOM by classifying a component based on its shape and features. This has significantly improved the workflow efficiency of data preparation tasks by replacing a few monotonous and repetitive tasks that are typically done by engineers for CAD preparation for CFD.
For validation and testing, the data was randomly divided into two subsets: one for training and one for testing. We fitted the model on one set and then evaluated the prediction error value (e.g. test the classification for grill and test the classification for not a grill). In this case, the classification problem was for “grille” and “not a grille,” so the training data needed to have grille as well as non-grille parts. A total of 60 parts were used with 12 isometric views for each part. A trained shape detection ML model was ran on the test data, which was not part of the training data.
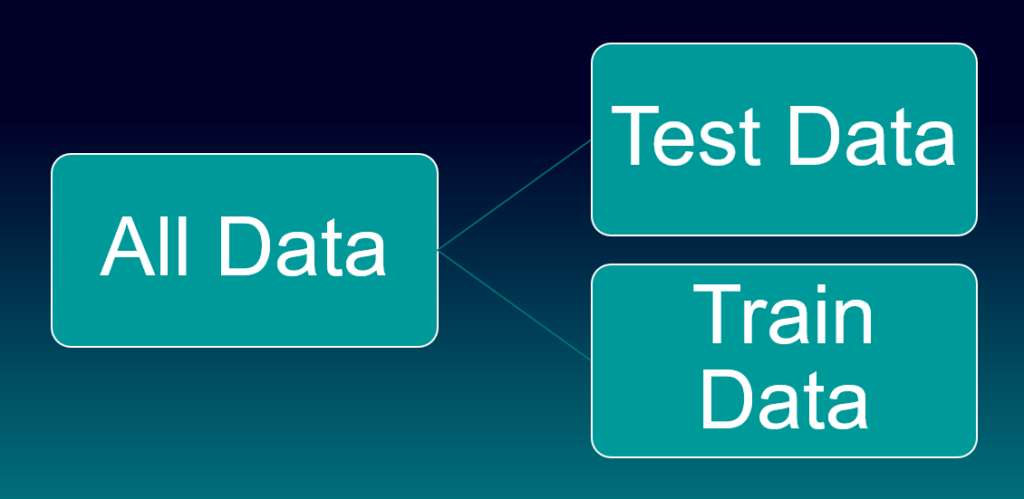
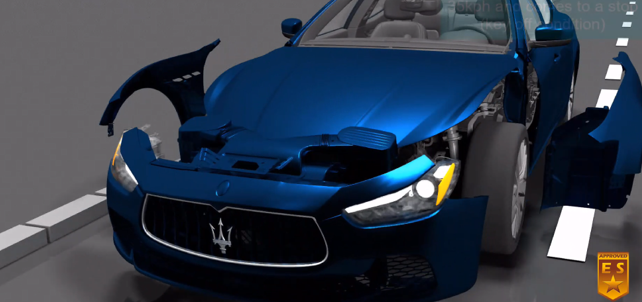
We used confusion matrix techniques to determine the misclassification rate (false positive and true positive rate). For the query “grille,” the shape detection technique had a 98% probability to identify the part as grille (true positive) and 2% probability of identifying not a grille (false positive). For query “not a grill,” the shape detection technique had a 98% probability of identifying the part as not a grille (true positive) and 2% probability of identifying the part as a grille (false positive).
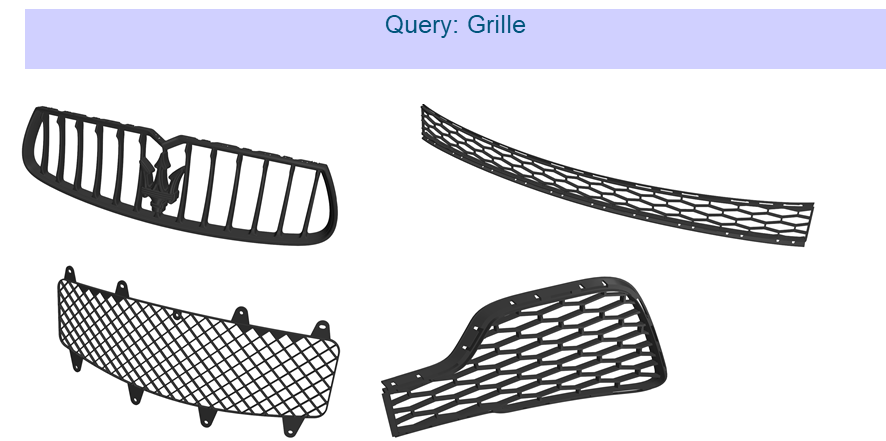
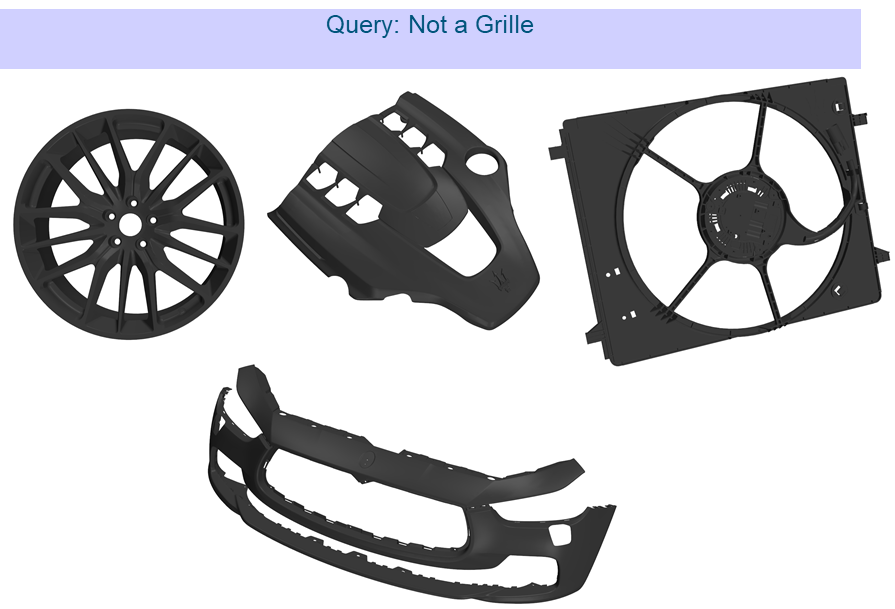
In both examples, our engineers significantly reduced the simulation process turnaround time. This in turn can enable companies to reduce costs and use the time savings to work higher-value initiatives, such as improving product quality.
Identify anomalies and improve performance
Using AI, engineers can automatically flag problematic areas based on a history of simulations.
By using a history of simulation results (images), the Simcenter Engineering Services team has trained a convolutional neural network to identify any deviations from the normal in simulation results. If an anomaly is detected, the neural network automatically flags the areas that should be inspected by engineers. In a recent example, the team used this technology to identify hot and cold areas in vehicle thermal management and cabin comfort analysis.
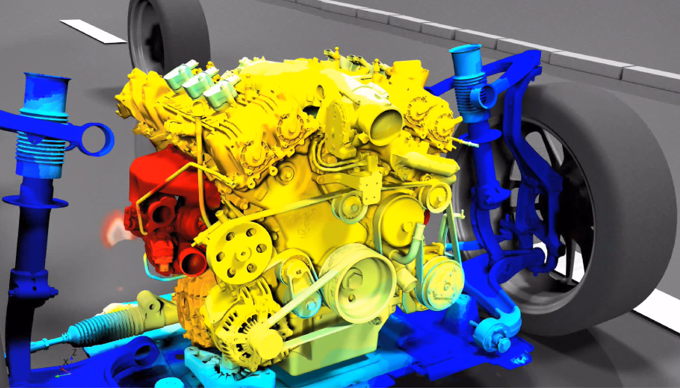
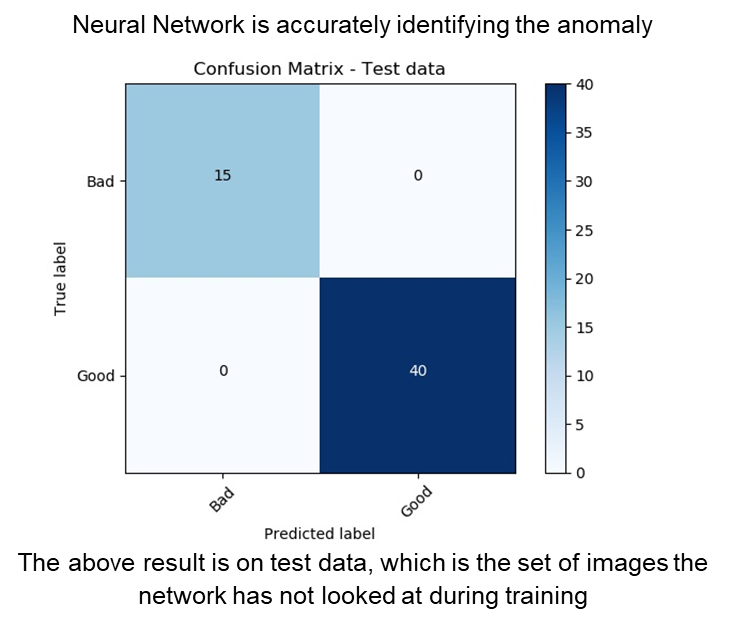
Using this method, engineers can investigate and improve the accuracy of simulations without the need to manually inspect every result. We ran a trained neural network on the test data and used a confusion matrix to calculate the misclassification (true positive and false positive rate). The trained model was able to predict anomalies when used on the test data with very high accuracy:
- The misclassification rate, which is the ratio of predicted (false positive + false negative)/total predicted class was zero
- The true positive rate, which is the ratio of true positive predicted/actual total positive was 40/40 =1
- The false positive rate, which is the ratio of false positive predicted/actual total negative was 0/15 =0
Smart interpretation of simulation results for better judgment calls using AI in CFD
Using clustering techniques, engineers can identify hidden patterns in the simulation data as well as group data in order to make better decisions.
Clustering techniques are the most widely used unsupervised learning. They can be used to analyze enormous amounts of simulation data and formulate stories that allow engineers to reach conclusions faster. For example, stories can be developed about how components will behave during various operating conditions, design configurations, or list correlation between parts (example if parts A and B fail, there is a 70% chance that part C will also fail under certain conditions).
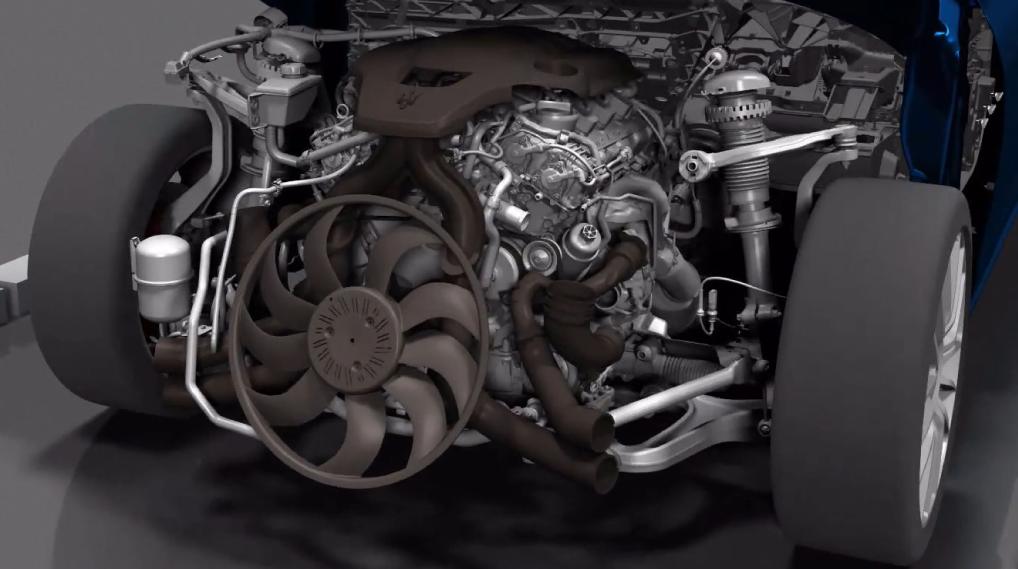
Deep learning network with CFD and control actions
AI in CFD can be leveraged with control actions for efficient energy management, maintenance, and improving system efficiency. For example, using AI in cabin temperature prediction and control actions, engineers can achieve optimal temperatures for efficient energy management. This can also help with battery performance, potentially increasing battery range in some cases.
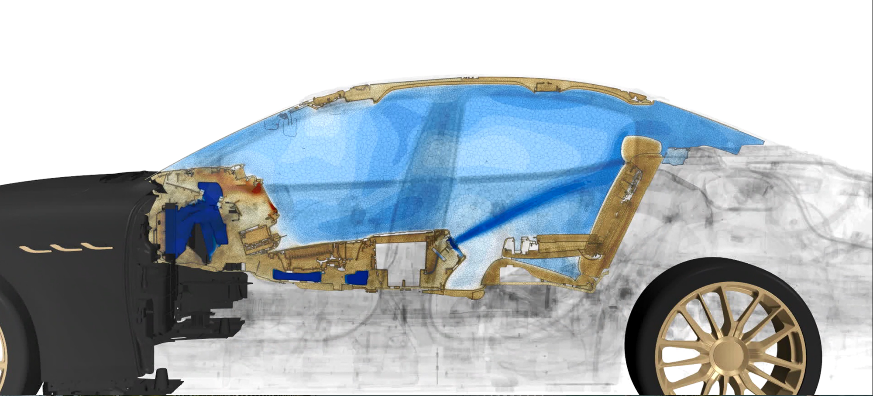
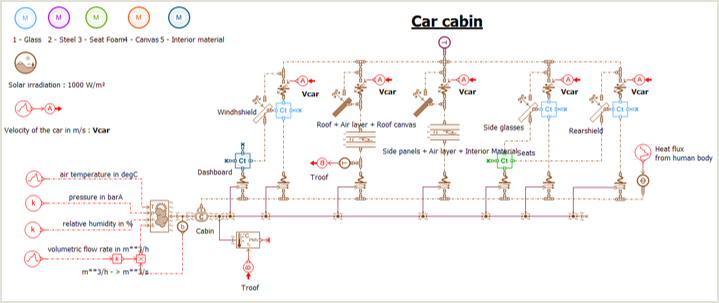
Engineers can also use CFD data from cabin comfort analysis to train neural networks to predict the temperature distribution for a given input. This in turn can invoke AI-enabled controls to change the mass flow rate or vent configurations (openings/directions) to achieve desired flow properties.
While AI is still in its infancy in engineering, its potential is limitless. Just as the Ford assembly line revolutionized automaking by making if faster and less time-consuming, AI has the power to make vehicle development faster and more time-efficient. This will allow engineers to focus more on what they are educated and paid to do: build better products, faster.
In summary, AI is an important tool that all companies need to adopt in order to remain competitive, even in a technical niche area such as CFD. Simcenter Engineering Services can help you demystify and deploy it effectively.
We need your help: AI in CFD survey
What is your view on the role of AI in CFD? Please help us understand the current state of the industry by completing a brief survey.
Learn more about how Simcenter Engineering is helping customers develop successful AI transformation roadmaps:
- Podcast: Exploring the impact of AI in CFD
- How artificial neural networks aid in mechatronic system development
- Process automation: Streamlining simulation workflows
- Monolith AI and Simcenter STAR-CCM+ bring machine learning to CFD simulations
- Discover the power of deploying neural networks and its impact on systems engineering
- Simultelligence
To get in touch with Simcenter Engineering Services, email us at engineeringservices.sisw@siemens.com.
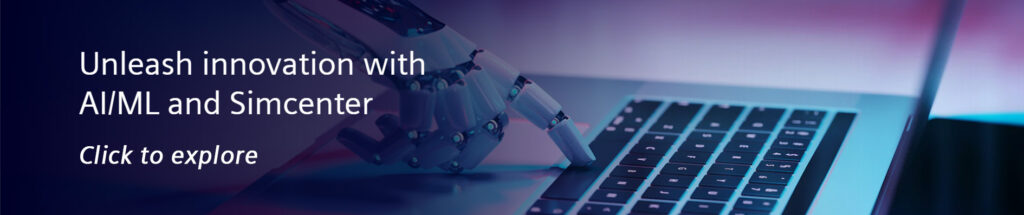