Optimizing complex production lines before they are built
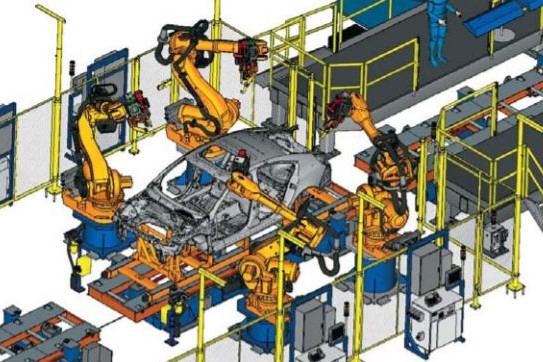
More and more manufacturers realize that to be successful and to quickly and predictably launch new products, the conventional tools used are not enough. Traditional physical commissioning comes with an abundance of risks, costs and time, and even more so if any errors are made that must be fixed or redone.
Consider this. Traditionally, mechanical, electrical and kinematics are all engineering separately in a serial fashion so the function of the line cannot be tested and verified until it is built. Naturally, this contributes to lengthy production disruptions and costly mistakes from having to rework the design. Not to be underestimated are the problems associated with needing different engineering disciplines aligned in their work and iterations, the problems that come from machines not functioning as intended, and the extremely high cost of collisions when robotic mechanism collide with things because the programming wasn’t able to be validated and tested before installation. Virtual commissioning reduces these risks and has several benefits.
Why use virtual commissioning
ADA Computers (ADA) is a Romanian Siemens Smart Expert partner with specializations in NX for Manufacturing and NX for Design. With eight Process Simulate (PS) experts on their team, ADA has delivered virtual commissioning solutions for more than a dozen manufacturers. ADA considers it their job to let users know about the possibilities to move towards digitalization.
Virtually commissioning the manufacturing process allows companies to reduce risk and production downtime by creating a more mature and predictable production process. It also allows for reduced modification costs, a faster launch time that is accurate the first time and verified robots with programmable logic controller (PLC) programs.
Using Process Simulate for virtual commissioning
Using Process Simulate Commissioning, users can simulate and validate automated production lines using actual robot programs and real PLC code, connected to the hardware using a Siemens Simulation Unit or an OPC connection, or connected to the virtual PLC SIMATIC S7-PLCSIM Advanced, thus enabling the most realistic virtual commissioning environment. Process Simulate Commissioning supports two configurations:
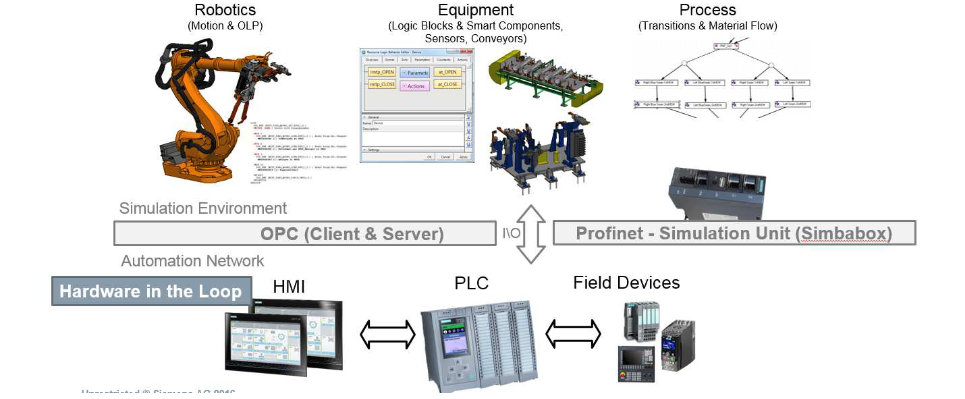
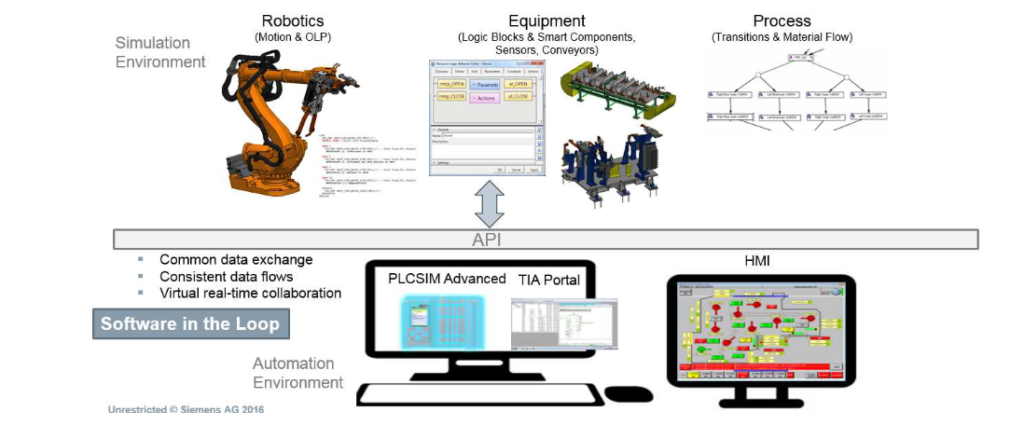
With Sil, the first step is starting the emulated PLC. This digitalizes the equipment used to control the real robotic cell, using PLCSIM advanced. The process supports virtual PLC creation so that the Totally Integrated Automation (TIA) portal and process simulation can communicate.
Then one can utilize the connection setting in Process Simulate which has a wide range of control entities from OPC servers to emulation software. From here, the user will use the signal settings in Process Simulate in conjunction with the Siemens TIA portal to force several signals in order to give the START command to robots.
There are two function scenarios that are simulated in the following video: human safety and starting conditions. The real-world examples prove how process simulation can drastically improve several key competencies including virtual validation of mechanical and electrical components, collaboration between mechanical design and controls departments, reduction of onsite commissioning by roughly 30%, integrated simulation using actual PLC code and hardware, and allows testing and debugging in a safe and collision-free environment.
Contributors: Alex Dinca and Endre Szucs are virtual commissioning and digitalization specialists at ADA. ADA Computers is a Siemens Smart Expert Partner in Romania with specializations in NX for Manufacturing and NX for Design that provides software solutions for product lifecycle management.