The road to resilience at the point of design: Knowledge
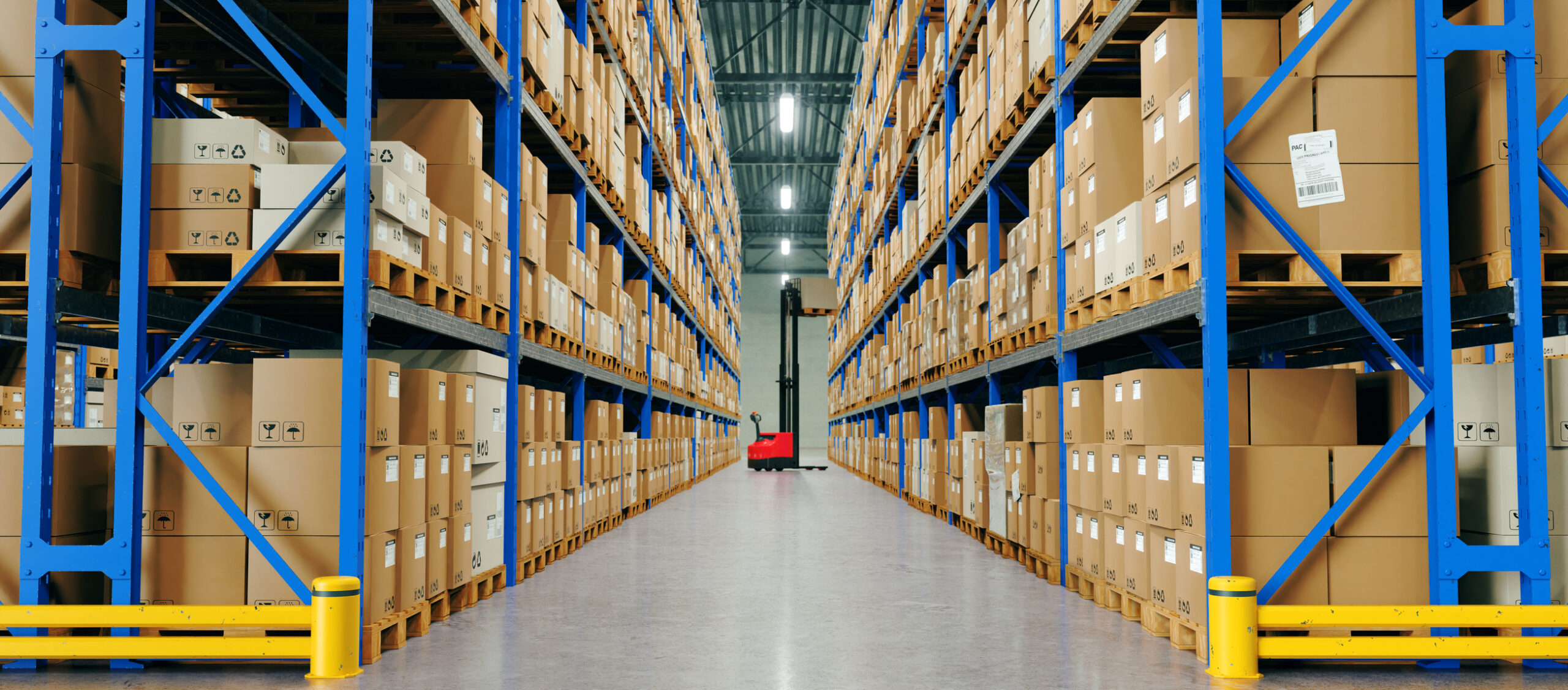
In our third episode of the Printed Circuit Podcast, we talk about how to create resilience at the point of design through a three-phased approach, with the first phase being, knowledge. This phase is about equipping engineers and teams with comprehensive real-time component sourcing data so they can make more informed part decisions when the cost of change is lowest.
Shifting left – what does that look like?
In our previous episodes, we discussed the need to shift left or take an “outside-in” approach. Decisions need to be informed by global business and supply chain conditions on the ground, in real-time. So, when we think about a complete supply chain resilient solution, we envision one that seamlessly connects the whole of the design organization with the electronics ecosystem they depend on to bring a successful product to market. What that requires is a much tighter coupling between the design chain—what design engineers and the design organization does—and the supply chain organization within a company.
Real-time component sourcing knowledge
At the heart of the solution is continuously updated, comprehensive, component intelligence. This integrated source of AI-enabled, component data is going to be used to empower better decisions across the entire product lifecycle. That knowledge needs to be available:
- At the point of component research and selection
- At the point of part creation
- At the point of design capture
- At the point of Bill of Materials review and analysis for each PCB sub-assembly
- At the point of the final NPI review
- At the point of sustaining engineering
- At the point of the product end of life
In addition to the real-time component sourcing knowledge from a host of worldwide suppliers, engineers need to be alerted to component risk graded at a single part level, but also at a Bill of Materials level. So, as they’re making part selections, they’re going to know right then and there if that part is even available or if it is obsolete. They can also make that same assessment at a Bill of Materials level. If a part is assessed to be too high a risk, the engineer should be presented with a form-fit/function alternate part, along with the associated ECAD model right at their fingertips.
How do you implement?
Today, the knowledge phase can be implemented directly within our PCB design tools with a supply chain application powered by Supplyframe. It’s cloud-connected access to real-time components sourcing knowledge from approximately 100 suppliers at the point of design entry. You can see component pricing availability, compliance, lifecycle, links to a component supplier data sheets, alerts, and potential risks.
Information right at your fingertips
All of this, today, is at the designer’s fingertips within our Siemens tools. So, you’re designing with external supply chain touchpoints that are equipping you to make the best decisions to positively impact designs downstream. As an example, this information is embedded within Xpedition and PADS Professional Premium. This way, you don’t need to search external websites for information — the component sourcing data is right in front of you when you’re selecting parts for your design. This helps ensure that an obsolete part, or a part with a long lead time, will never be mistakenly designed in ever again.
Designing for supply chain resilience – the payoff
Knowing the parts with the greatest availability in today’s supply chain environment is key. Think about streamlined collaboration between procurement and product development, where a traditional serial handoff process is now concurrent, transparent, and integrated. All it takes is one time where you’re not designing in an obsolete part to make the investment worthwhile.
At Siemens EDA, we really get this, which is why we acquired Supplyframe. The industry is going to see a much better solution now, one that treats supply chain intelligence as being a digitally transformative piece of business. We provide not only a solution but a roadmap that’s going to get companies to where they want to go.
The knowledge phase can be implemented today, and work is underway to enable the next two phases: intelligence and optimization. In our next episode, we’ll dive deeper into the intelligence phase and explore what that will bring to the supply chain resilience effort.
Want to learn more about the knowledge phase on the road to supply chain resilience? Listen to the podcast now, available on your favorite podcast platform.
Expand to see the Transcript
[00:12] Steph Chavez: Hi, everyone. Thanks for tuning in to the Printed Circuit podcast, where we discuss trends, challenges, and opportunities across the printed circuit engineering industry. I’m your host, Steph Chavez. And as a refresher, I’m a Senior Product Marketing Manager with Siemens with over three decades of experience. I’m an industry-acknowledged Subject Matter Expert in PCB Design. And I’m also the current chairman and founding chairman of the Printed Circuit Engineering Association (PCEA). Joining me today is Matt Walsh, a Product Marketing Manager with Siemens. Matt, thanks for being here. Can you give us a quick introduction?
[00:47] Matt Walsh: I’d be happy to, Steph. Before I get going, I thought this was going to be a video podcast, so I’m wearing a fancy sports jacket to look good, and now I’m hearing it’s just audio. But nonetheless, thanks, Steph, for inviting me to the podcast. I’m really happy we’re doing this. So, I’ve worked at Siemens EDA now for five years in product marketing, and I’m actually responsible for all of our cloud solutions. But interestingly enough, prior to Siemens, I actually worked in the semiconductor industry for over 20 years at Xilinx in their field organization, helping OEMs design their FPGAs. So, during those 20-plus years, I actually witnessed firsthand how information flows from component manufacturers to OEMs throughout the NPI process, and ultimately, through the full product lifecycle for electronic systems. And now, I’m actually able to apply what I learned to help formulate a better connection between the source of components supply on one end to component demand on the design side.
[02:03] Steph Chavez: It’s a great background to bring a lot of knowledge and intelligence to the table for our audience here. In our last episode, Matt, I talk with Richard Barnett. He’s a Chief Marketing Officer with SupplyFrame, a Siemens company. We talked about how today’s infrastructure puts you or the designer at a disadvantage because resilience is not built into the design process. So, how do we get there? Let’s talk about the road to resilience. What do you think we should start with this?
[02:29] Matt Walsh: Fundamentally, I think there’s this huge need to shift left or maybe a better way I’ve heard this term used, and I think it’s a good term, is to take an outside-in approach, where your decisions as a designer, as a design organization, are informed by global business and supply chain conditions on the ground, real-time, right now. So, when we think about a complete supply chain resilient solution, Siemens EDA, we envision one that seamlessly connects the whole of the design organization with the electronics ecosystem they depend on to bring a successful product to market. So, what that requires is it’s going to require a much tighter coupling between what I like to call the design chain—so, it’s what design engineers and the design organization does—and the supply chain organization within a company. So, now you have continuously updated comprehensive component intelligence, which is at the heart of that solution. So, if you think about it, for a design organization, this integrated source of AI-enabled component data is going to be used to empower better decisions across the entire product lifecycle. So let’s walk through it — it’s going to be at the point of component research and selection, it’s going to be at the point of part creation, it’s going to be at the point of design capture, at the point of Bill of Materials review and the analysis for each PCB sub-assembly, it’s going to be at the point of the final NPI review, and it’s going to be the point of sustaining engineering all the way through to the point of the product end of life.
[04:19] Steph Chavez: You’re absolutely right. I couldn’t agree with you more. Especially from my recent experience in the last few years, as we’ve gone through this mess with COVID. And I think “mess” is maybe not the right term, but just having to deal with our dated processes that have always been like a just-in-time approach to now we’re having to adapt to this new normal with the backlog or just the build-up of supply chain and the disturbance within the supply chain ecosystem — how do design teams do this is the challenge. And like I said, I can attest to this, in some recent projects I’ve been on, it’s brutal. And the back and forth of having to take one step forward and two steps backward, it’s a lot to deal with. It can be cashed profit especially if you’re a small mom-and-pop shop trying to survive in today’s day and age. It sounds like a single solution is needed that is fully integrated with the electronic system design platform. That platform must be a breakthrough, especially when we’re talking about breaking through the invisible silos in the organization so you have better cross-functional decisions that can be made, especially during the new product introduction, when upwards of 80% of lifecycle risks and costs are looked in. We need to deploy this through digitally-integrated solutions that will reduce manual interventions, especially when we talk about legacy processes where they seem to be a lot more manual. And believe me, I can attest to that coming from Mil-Aero for the last 12 years or so. It will foster collaboration, it will also improve transparency across disciplines, and will reduce or eliminate respins between design and manufacturing. So, when we take a look at all these, then when we think about a fully integrated solution, it has to cover all this. Am I right, Matt? What do you think about that?
[06:03] Matt Walsh: You’re right on. I think you said a really important statement that 80% of your costs are going to be based upon those decisions that were made back during the NPI process. Some people would say, “Hey, we’re in this new normal phase.” It’s post-pandemic. But I like to think of it as how are companies going to be able to prepare for the next normal. So, what we’re talking about, it’s a solution that really needs to shift left real-time component sourcing insights. So, it’s going to deliver both performance and electrical parametrics to the engineer’s desktop, and it is going to allow them more informed decisions at the point of part selection and at the point of design, and it’s going to allow for a much tighter, more seamless handshake and collaboration between the engineering organization and the procurement organization. And in addition to the real-time component sourcing knowledge from a host of worldwide suppliers, engineers are going to be alerted to component risk graded at a single part level, but also at a Bill of Materials level. So, as they’re making part selections, they’re going to know right then and there if that part is even available or is it obsolete. But they can also make that same assessment at a Bill of Materials level. So, as I mentioned, if a part is assessed to be too high a risk, the engineer will be presented with a form-fit function alternate parts, along with the associated ECAD models right at their fingertips. So, again, if a change is deemed necessary, they’re going to be ready to go. So, it’s this seamless integration between what I had mentioned earlier between what was classical design chain and supply chain that there’s going to be this melding or this merger between those two functions into a much more collaborative cross-functional flow.
[08:06] Steph Chavez: I agree with you that that revolution has to happen and those silos have to come down in order for us to be successful going forward, definitely. When we think about the streamlined collaboration between procurement and product development established, traditional serial handoff process is now concurrent, transparent, and integrated. Fully aligned design revolutions can better manage, adapt, and thrive in the competitive advantage when faced with supply chain disruptions, especially than what we’re seeing today. Ultimately, designing for supply chain resilience can have a significant payoff by translating unexpected events into opportunities for growth. Would you agree?
[08:43] Matt Walsh: I totally agree with what you’re saying, Steph. It all sounds great. And I would say that because there’s been this siloed approach with the way that organizations treat the design process, where again, you’ve got this serial handoff between classical design and classical the supply chain or procurement operation. I see that but where do you think is going to be that path forward to get there today?
[09:18] Steph Chavez: Designing for supply chain resilience can be implemented with three keys to resilient design, which are deployed in three phases, the first being knowledge. The better way to put it as this phase is about arming engineers and teams with a comprehensive real-time component sourcing data so that they can make a more informed part decision when the cost of change is at its lowest. Today, this phase can be implemented directly within our PCB design tools with a supply chain application powered by SupplyFrame, that’s what we can do today. It’s a cloud-connected access to real-time components sourcing knowledge from approximately 100 suppliers at the point of design entry. That’s huge. You’re talking about component pricing availability, compliance, lifecycle, links to a component supplier data sheets, alerts, and potential risks. All of this, today, is at the fingertips — it’s not ‘can be,’ it’s at the fingertips within our Siemens tools. We have this ability today. So you’re designing truly at the point of design with all those touchpoints, those external supply chain test points that are arming the engineers to make the best intelligent decisions that will positively impact their designs downstream. And that’s a key. I mean, would you agree?
[10:31] Matt Walsh: Yeah, I definitely agree. What I like about this solution, I’m very familiar with it and I have very much been a part of it. But what I like about this solution is it’s that seamless integration and the ability to have– again, I’ve been using the term fingertip, but it’s information right at your fingertips where you have access to critical sourcing knowledge during the design process right inside, it’s embedded within expedition and PADS professional. So you don’t need to search external websites for this information because you have the component sourcing data right in front of you when you’re using parts for your design. And that pretty much guarantees that an obsolete part—trust me—will never be mistakenly designed ever again. And by the way, that happens. And I know that sometimes, especially today, it’s maybe not so much on obsolete parts, but it’s on long lead time devices where engineers, at one time, they didn’t know that there was a significant lead time. But today, engineers need to know that there’s a long lead time item so that they can look at alternate devices. So that’s really important. So, knowing the parts with the greatest availability in today’s supply chain environment is really key. And I’m guessing, Steph, that any organization is going to want this type of solution because it’s going to pay for itself many times over because it’s just going to take one time where you’re not designing in an obsolete part or one time where you’re not designing in a part that has a 28-week lead time where it’s going to save you for getting a successful product out the door.
[12:21] Steph Chavez: And some recent experience that I’ve had, especially with the negative effect of the supply chain disruptions is that, not just me, but we are seeing parts, their availability going from just several weeks to more like 52 weeks. And in other cases, you’re seeing part prices go from a few dollars to potentially a few hundred dollars. I mean, it just depends on the part, but it is crazy. And I can attest to some of my colleagues especially discussing that PCB West this year, and some other colleagues that are in the thick of designing that are having to redesign over and over because when we think about how our libraries are made up. And it doesn’t matter what ecosystem you belong to, chances are your library was vetted upfront and your parts are stagnated, meaning that there’s no intelligence regarding what is the availability today, there’s no supply chain intelligence. It may be vetted for a five-year span of when is it going to go obsolete or is it available today and will be available for the next 10 years? But it doesn’t tell you with the impact today. So when you think about when EE’s are selecting parts in their design from their master libraries, they don’t have that real-time current up-to-date supply chain intelligence. So they’re flying blind when they’re selecting their parts. And by the time they place them in their schematic and then have a BOM analysis done on them. If you’re doing things in an optimized fashion, you are doing them in the current form, in the current process that we have now today, you’re doing them where you’ve already started your layout. And by the time that BOM analysis is done, it’s too late because, by the time you get any red flags on any components, chances are you’ve already laid out that circuit and now you’ve got to go put a hold on that particular section of the layout. Well, the EE is doing his research to go find new parts; hopefully, he can find a new part. And if not, he’s got to find an alternate circuitry or they have to make a decision whether they just go ahead and take the delay in their product getting to market or they design that feature out. It’s brutal. With this solution that we have, bringing that that intelligence to the point of design is key. And like I told you, I have tested that and I felt that supply chain pain several times over. And it’s not just me, I had a colleague of mine mention the same thing.
[14:50] Matt Walsh: The great thing is that at Siemens EDA, we really get this. Kind of a game changer for us was when we acquired SupplyFrame, we’re really changing the game here, so we really get it. You’re going to see, we’re going to see, the industry is going to see just a much better solution that’s going to tie together this critical operation of really looking at the supply chain as being a digitally transformative piece of their business that companies are really starting to look at. I think they’ve kind of exhausted looking at doing some financial engineering and doing things like that, different go-to market strategies. Now they can start to really focus on or taking a serious look at the supply chain because it’s an area that is ripe for transformation. And I think that we provide not only a solution but a roadmap that’s going to get them to where companies want to go.
[15:57] Steph Chavez: Breaking down that silo of the way that teams have been operating has got to change. And that integration between the supply chain and design, bringing that knowledge to the point of design, that is what is going to make a difference in the companies that get it and that will implement it, they are the ones who will be successful. And the companies that will remain the same, it will be tough for them, it will be tough for them to compete going forward as other companies will take advantage and optimize to the new normal, and that will be the key. So, I see our solution, while the knowledge phase can be implemented today, work is already underway with the intelligence and optimization phases, which are soon to follow. In our next episode, we’ll dive deeper into the intelligence phase and what we’ll bring to the supply chain resilience effort. On behalf of my colleague, Matt Walsh, I’d like to thank you for your time today. Matt, thank you for your insights and for sharing the knowledge today with our audience.
[16:59] Matt Walsh: Thanks, Steph. I appreciate it. Next time tell me that I don’t need to wear a…
[17:04] Steph Chavez: Yeah, absolutely. I’ve got to say, you do look sharp though. So, with that said, I hope this discussion has been helpful in understanding the road to resilience at the point of design. Thank you and I hope you continue to tune in and follow me on the Printed Circuit podcast.