The road to resilience at the point of design: Optimization
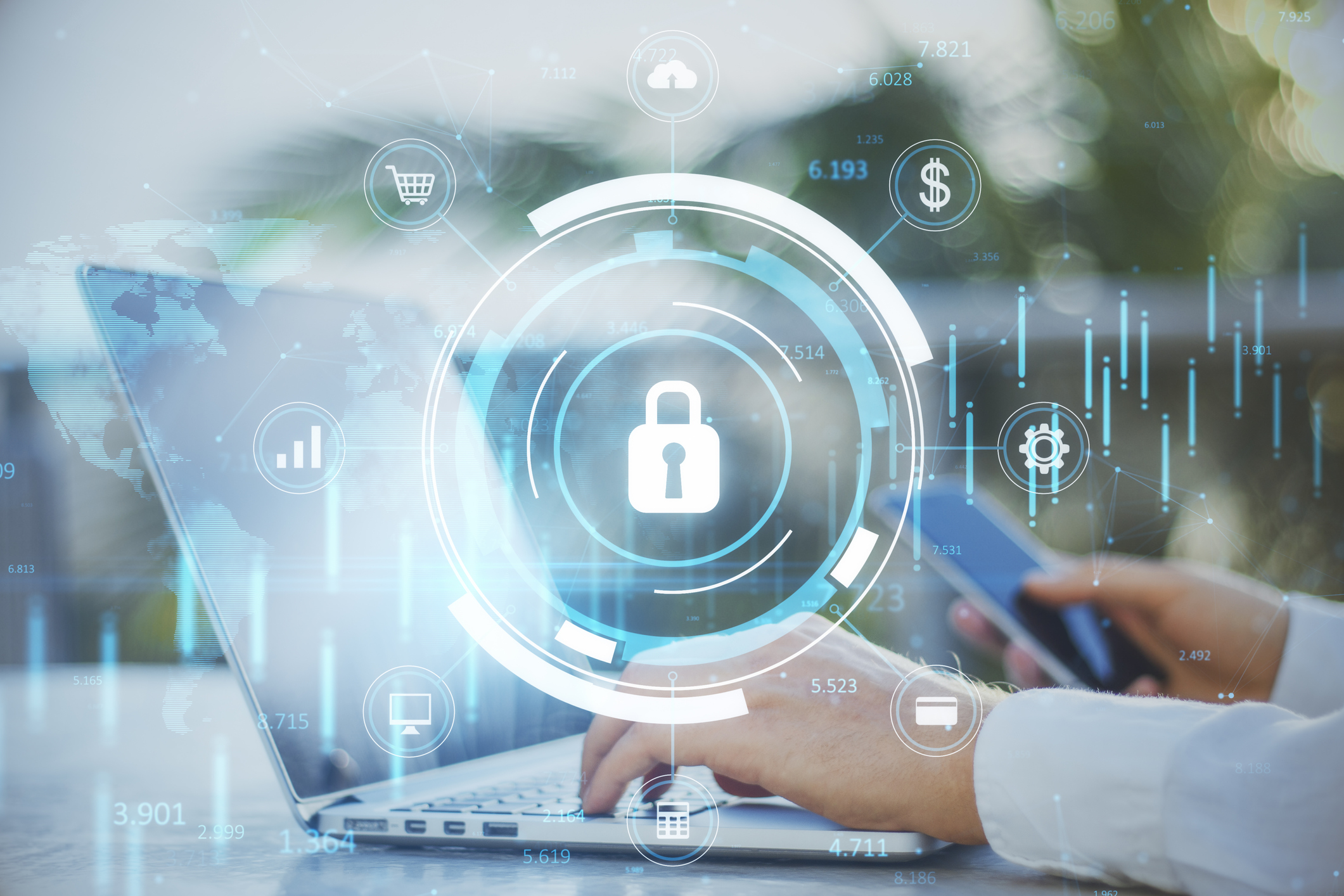
On our last two episodes of the Printed Circuit Podcast, we talked about the road to PCB supply chain resilience, and how we can enable that transformation with the three pillars: knowledge, intelligence, and optimization. Today, let’s dig a little deeper into the optimization pillar.
So, what does Siemens mean by “optimization?” And how does it apply to designing for supply chain resilience?
Legacy drivers
If you look back over the history of the printed circuit engineering industry, cost was really a driver for most businesses. Meaning, what they were looking for from a supply chain perspective was to reduce costs. And that worked well — when the supply chain was relatively stable, you could see cost as being a function of which supplier you chose or which distributor you chose based on the design that you’d already created. However, what we’ve seen over the last couple of years is some dramatic instability in the supply chain. It’s really gotten to the point where the supply chain is brittle and unstable. The only insight that we’ve got into the supply chain today is that this instability is going to continue.
One of the ways customers are trying to handle this is changing the way development teams hand their Bill of Materials (BoM) over to component engineering at certain points. Conducting analysis on whether components are obsolete, what their AVL looks like, and then having that information come back to engineering just doesn’t work anymore in this age of supply chain instability. We see customers saying, “Hey, what was in the supply chain yesterday, it’s just not there today.”
Creating a closed-loop component management system
When we think about optimization as a pillar and how that applies to supply chain resilience, what we’re really talking about is creating a closed-loop component management system, so that we’re no longer operating in silos between engineering, between NPI, and between purchasing or procurement. It means creating a tightly coupled process within the OEM, so that we can really understand the trade-offs between risk and cost in the supply chain at every point from the design right through to the manufacturing.
One of the biggest problems to overcome is the siloed approach. If you look at supply chain information, it’s often contained in an ERP or MRP system, and not completely shared with engineering in a timely way. Often supply chain information gets updated on a quarterly basis. What’s unfortunate in those instances is that when you have separate systems staff, you’re often passing Excel spreadsheets between systems rather than having them truly connected.
Any time you have a manual process, you’ve got the potential for errors. It raises questions like:
- Are you using the right set of data?
- Is the data current (real-time)?
Trusted supply chain
Trusted supply chain is starting to become a key topic as well in regard to supply chain data. Specifically, trust of a single component. We have done a lot of work on creating a digital twin of the component. There is a standard called the JEP30—it’s part of the JEDEC standard, ratified in 2018—that functions as a complete digital model of the components. Now instead of having a model be something like a datasheet and then some files that fly around with that, we’ve got the ability to create this digital view of a component that then we can sign to assure its authenticity.
It’s similar to how we looked at domain names in the past. How do you know that Siemens owns a domain name? Well, it’s because you have an authority that provides a certificate that signs it. So, what we’re looking at today is how we can ensure that all the information about a component that a component manufacturer publishes is trusted. And in a very similar way, trusting it through having a certificate that allows you to establish its authenticity.
Today, it’s almost antiquated to think that all you do is put up a datasheet, and that describes a component, and you don’t really know if all that is authentic or not. It extends beyond that when you start looking at the relationship into the supply chain. If we look at the flow you get a component from a component manufacturer that then goes to a distributor; from the distributor, it goes to an EMS. At every point along that supply chain, at some point, we want to be able to ascertain trust and traceability.
Eventually, we want to be able to get to the point where we can understand where all the threats are in the supply chain, and what the risk of those threats are.
What does it mean for board assembly?
On one level you want to make sure that your components are trustworthy and have visibility into things like ‘country of origin’ information. Then you want to get all that information to shift left so that you’ve got a very high degree of confidence that you can build a reliable product.
Then you want to be able to look at a digital part model that’s trusted, truly know the authenticity of it, and extend that trust into your product. You can then say this PCB is trusted.
The value in knowing where components are used
There is immense value in knowing what components are used within your portfolio of products. If you do identify counterfeit components, now you’ve got visibility into the supply chain to understand where that threat may have arisen. And now that you’ve identified this component, you can manage recall situations that are hugely expensive. If you can really target a recall down to a specific module or sub-module, that’s of absolutely tremendous value.
How to verify components
Siemens EDA is investing a lot in the component digital thread. We’re trying to create the idea of a very, very accurate digital thread from the component to the OEM, down through the entire component ecosystem so that you can track that right down into manufacturing and product. We’re right at the start of this transformation. Today, there are hundreds of millions of data sheets just flying around, so this is going to be a huge transformation for the electronics industry. And when we get there, we’re really going to see this fuel a new level of productivity and security for the industry.
Want to learn more about the optimization phase on the road to supply chain resilience? Listen to the podcast now, available on your favorite podcast platform.
View the episode transcript
[00:13] Steph Chavez: Hi, everyone. Thanks for tuning in to the Printed Circuit Podcast, where we discuss trends, challenges, and opportunities across the Printed Circuit Engineering industry. As a refresher, I’m a Senior Product Marketing Manager with Siemens, with a background as an industry-acknowledged subject matter expert of PCB design, with over three decades of experience. I’m also Chairman of the Printed Circuit Engineering Association (PCA). Joining me today, again, is Matt Bromley, Vice President of Product Strategy and Technology with Siemens. Matt, thanks again for being here with us. Can you give us some background and some introduction of yourself?
[00:44] Matt Bromley: Thanks, Steph. Thanks for inviting me today. Really pleased to be here. I’ve been at Siemens for six and a half years. Before that, I was part of the Mentor Graphics acquisition, and I’ve been in the EDA industry in total for about 30 years now. At Siemens, I’m responsible for a team of subject matter experts and they’re really here to help drive the product roadmaps for all the EBS products. So, what we’re really doing is bringing together the market and customer requirements, helping to solve their complex challenges, and driving that into the product roadmaps. During my time here, I’ve had the opportunity to work with many of our top customers over the years and really understand their challenges. That’s really helped me and my team get great insight into many of the most complex challenges customers have. Particularly more recently around the supply chain and the instability they’ve experienced in the last couple of years.
[01:41] Steph Chavez: On our last two episodes of Printed Circuit Podcast, we’re talking about the road to resilient enterprise, and how we can enable that transformation with the three pillars: Knowledge, intelligence, and optimization. Today, Matt, I’d like to dig a little deeper into the optimization pillar. Can you give us some insight into what Siemens means by optimization? And how that applies to designing for supply chain resilience?
[02:04] Matt Bromley: Absolutely. Maybe before we sort of dive into optimization, let’s just set a little bit of context around the supply chain in the industry. If you look back over the history of the industry, maybe the last 25 years or so, cost was really a driver for most businesses. So, what they were really looking for from a supply chain perspective was hoping they reduce costs. And that worked pretty well — when the supply chain was relatively stable, you could really see cost as being a function of which supplier you chose or which distributor you chose based on the design that you’d already created. However, what we’ve really seen over the last couple of years is some dramatic instability in the supply chain. And some of these are due to geopolitical reasons. Some of them are due to the pandemic. But it’s really gotten to the point where the supply chain is brittle, it’s become very unstable. And it’s almost like it’s definitely the only insight that we’ve got into the supply chain is that instability is going to continue. So, what have we learned from this? If we look at this instability and we see how customers are trying to handle this, one of the things that we see is it’s no longer good enough to have development teams that view the supply chain as handing their Bill of Materials over to component engineering at certain points. Seeing some analysis done about whether or not maybe components are obsolete, what their AVL looks like, and then having that information come back; that just doesn’t work anymore in this age of supply chain instability and almost the changes in the supply chain happening on a daily basis. We see customers sort of saying, “Hey, what was in the supply chain yesterday, it’s just not there today.” When we think about optimization as a pillar and how that applies to supply chain resilience. What we’re really talking about is creating a closed-loop component management system, so that we’re no longer operating in silos between engineering, between NPI, and between maybe purchasing or procurement, but really a much more tightly coupled process within the OEM, so that we can really understand the trade-offs between risk in the supply chain and cost in the supply chain at every point from the design right through to the manufacturing.
[04:22] Steph Chavez: I can definitely attest to that. Especially, with all that I’ve gone through in my career and how we’ve been functioning in silos or the legacy process. When we look at it today, people that are doing purchasing, are they passing their insights over to the engineering teams? Or are they looking at the same systems or separate systems, as I said, working in silos and not sharing information? What have you seen?
[04:47] Matt Bromley: We see a variety, but we definitely see one of the bigger problems is the siloed approach. If you look at supply chain information, very often it’s contained in an ERP system, maybe an MRP system, and that’s shared with engineering, not completely, and also not in a timely way, very often what we’ll see is supply chain information get updated on maybe a quarterly basis would be fairly traditional. So, we absolutely see this siloed effect where information is in different systems. And what’s unfortunate in those instances is very often, when you have separate system staff, as you’ve probably seen, what happens is you’re passing Excel spreadsheets between systems rather than having them truly connected.
[05:30] Steph Chavez: There is a process in place for the most part, but it’s a manual process. And teams that are successful, it’s because you have individuals who are stepping up and doing individual tasks, and not within a cohesive system what I would say what Siemens has to offer in our solution or what we’re doing.
[05:48] Matt Bromley: Well, anytime you have a manual process, you’ve got errors that come into it. Manual processes are error-prone, and that’s one of the hat problems. You’ve got kind of a data resiliency problem: Are you using the right set of data? Whether that be from the design side or the right set of data from the procurement and the supply chain side. And is it timely? I mean, Steph, I’ve been at customers who’ve said, “We did a design, and we thought we could get the components, and the next week, we couldn’t. And the result was we had to do the design again.” So, what we’re seeing at the customer’s is very often engineering is spending a large percentage of their time redesigning existing boards just to meet the supply chain problem. So what we really want to do is bring all that data together — connect it digitally, connect that supply chain digital thread and really shift it as far left as we can.
[06:41] Steph Chavez: I couldn’t agree with you more and I can attest to that “one step forward and two step backward” approach where we design something and the next meeting, we go to the stand-up meeting or a weekly meeting or a project meeting you go to, you find out that what was available is no longer available. And then you start the gauntlet of the loopback and the redundant loops of “Now I gotta go research parts, research circuitry, is it going to fit? Is it going to meet our requirements? Is it even available today? Who has it? And is the price gone up exponentially where yesterday it was $2, and now it’s $100? Or it’s not available in two weeks or six weeks, it’s available next year, potentially.” It’s amazing how things have changed when we talk about the approach to design and how we’re evolving.
[07:29] Matt Bromley: I was going to say there’s almost a little amusing anecdote. There’s a word that I grew up with in England called gazumping. And what it really was for is if you were buying a house, and you thought you had a contract in place for a set amount of money, somebody could gazump you. And what it really meant is they came in with a higher bid and took that. And I’ve actually heard that used by customers where they thought they had a secure order for a set of components and they said, “Somebody came in and gazumped us.” Literally, came in and took an order away that an OEM already thought they had.
[08:06] Steph Chavez: In one of the recent articles that I wrote, that exactly happened. He is a small business, and he purchases parts, did his due diligence, locked in and secured the PIO, got the confirmation, and everything is good. It’s bad enough, the price went up 10x. But then two days later, as he has moved on to the next efforts as a business owner, he gets an email saying, “I’m sorry, your order has been canceled,” or has been postponed or pushed back. And his delivery date is TBD and he got bumped or gazumped as the term you used. It is brutal. And he is not the only one that has seen this. As you mentioned, it’s getting worse. What do we do about it? Another thing I wanted to bring up or at least ask is I’ve been hearing and reading a lot about trusted supply chain. Can you talk a little bit about that? And what it means in the context of optimization?
[09:00] Matt Bromley: You’re absolutely right. There’s a lot that’s been talked about the trusted supply chain on multiple fronts and it’s really starting to become a very key topic that we’re looking at. It’s a broad topic. I’m sure we could spend a podcast or two just talking about trust, traceability, and insurance. But I think one of the elements that we’re really looking at from a component side is talking about trust of a single component. And what we’ve really done here is a lot of work on creating a digital twin of the component. What we have is a standard called the JEP30—it’s part of the JEDEC standard, it was ratified in 2018—that you can really view as sort of being a complete digital model of the components. And now instead of having a model being something like a datasheet and then some files that fly around with that, we’ve got the ability to create this digital view of a component that then we can sign it to assure its authenticity, very much like, historically, you might have looked at, say, a domain name. And how do you know that Siemens owns a domain name? Well, it’s because you have an authority that provides a certificate that signs it. So, what we’re really looking at today from one aspect of trust is how can we ensure that all the information about a component that a component manufacturer publishes is trusted. And in a very similar way, trusting it through having a certificate that allows you to establish its authenticity.
[10:26] Steph Chavez: Just the other day, I was sitting in a design class, one of the CPD courses, and as I listened to some of the students as they were giving feedback on this particular issue, I was not surprised but caught off guard when one of the students had said—and this is one of the topics in the course—that they were having to pull back a product because counterfeit parts were found and it started to affect the downstream of the functionality of the unit, which they didn’t see upfront, but downstream, they noticed issues. And when they evaluated and dug deeper, they found out they had several counterfeit parts. And they were spending a large amount of money to pull these back and then to replace these parts. So, it’s amazing how the effect of counterfeit parts or the integrity of the parts is now coming into play as well. It just shocks me.
[11:19] Matt Bromley: Absolutely. I think you’ve got to look at it from a couple of angles. One is you’ve got the authenticity of the party itself and whether you’re using a trusted data set. Today, it’s almost antiquated to think that all you do is put up a datasheet, and that describes a component, and you don’t really know if all that is authentic or not. Certainly, as you were pointing out, it really extends beyond that when you start looking at the relationship into the supply chain. So, not only do I get a component from a component manufacturer that then goes to a distributor; from the distributor, it goes to an EMS. And at every point along that supply chain, at some point, we want to be able to get to the point where you can ascertain trust and traceability. And as you pointed out, sometimes you get components that are counterfeit. Other times, it’s a little bit more, let’s say, surreptitious than that, where the real is a real of genuine components, but a couple of them have been flipped out and counterfeits put in. So, eventually, we want to be able to get to the point where we can understand where all the threats are in the supply chain, and what the risk of that is. So, just as an example, not quite in the electronics domain, but recently one of the American fighters was grounded because they found an alloy in it that they couldn’t be certain what the composition was, what the country of origin is. So, things like we don’t only want to be able to make sure that the component is trustworthy, but that entire supply chain is trustworthy. And we have things like country of origin information that’s then accessible at the product level.
[12:53] Steph Chavez: That’s really interesting. That really hits home when you think about that. When you’re designing, do you know what you’re designing? I mean, knowing the process is one thing and knowing your teams but the actual parks that you’re using, it’s really interesting when you dig in deeper regarding the integrity of the part and the reliability as well as what we talked about here, in this particular case, with the signatures are is it validated from the manufacturer? What does it mean in the context of a company when they’re evaluating what happens when boards are assembled? What is your take on that?
[13:31] Matt Bromley: That’s a great question. I think you’ve got this one level, what does it mean for an individual PCB designer supplier? I want to make sure that my components are trustworthy. I want to make sure that I’ve got visibility into things like ‘country of origin’ information, that really builds up on this historic material declaration. How can I get all that information shift left it again so that I’ve got a very high degree of confidence that I can build a reliable product? That’s what I really want to come out of that. And then I want to be able to extend that idea of a digital part model that’s trusted, that I know the authenticity of it, and be able to look at that and extend it into my product. My product, in this case being the PCB, that I can then say this PCB is trusted because I’ve got this hierarchical ledger effect going that the consumer of that PCB can then go off and do the same thing and say, “Hey, I can now tell that my product is trusted.” Because that’s what you want at the end of the day is that the end product is trusted.
[14:36] Steph Chavez: You’re absolutely right. I couldn’t agree with you more on that. Tell me, is there value in knowing where individual components are used in the portfolio of a product? Basically, would you agree that there’s value? Can you extrapolate on that?
[14:50] Matt Bromley: Sort of immense value. And I think you can see that from two ends there. One is, if you do identify counterfeit components, and now you’ve got visibility into the supply chain to understand where that threat may have arisen and you’ve now identified this component, you really want to target the impact. So, we want to target, what do I need, for example, to manage recall situations that are hugely expensive. I mean, if I can really target this what I recall down to a specific module or sub-module, that’s absolutely tremendous value.
[15:24] Steph Chavez: That’s really encouraging, Matt. Here’s my last question: When companies are buying or optimizing using our solution, how will they verify components certification, that a part is not counterfeit?
[15:36] Matt Bromley: We touched on this a little bit. I think you’ve got one idea of this digital twin, this component that we can build. And then because it’s digital, you can sign it, you’ve got an authenticator that signs it, so you got this idea of who of trust a bit, like I said, in domain names today. So, with that point, a company looking at our solution can say, “Hey, is that certificate valid?” And if it’s a valid certificate, then I’ve got some level of assurance that that provider, that supplier of components has completed all the relevant steps that guarantee the integrity of both their internal process and what they’ve put into the supply chain. So I think you get this idea building up over time with greater and greater visibility, not just into the component authenticity, but also into the logistics of the supply chain that go behind that, as this ledger is built up over time.
[16:32] Steph Chavez: Thanks, Matt. It’s very insightful information. This podcast culminates our series on the road to supply chain resilience. Do you have any final thoughts that you want to share with the audience here?
[16:44] Matt Bromley: Thanks, Steph. I think this is great. This has been pretty brief, and we could spend a lot of time talking on a lot of these topics. I think what’s clear is Siemens EDA is investing a lot. What we’re doing in this component digital thread is really trying to create the idea of a very, very accurate digital thread from the component manufacturer right through to the OEM, where that’s used, and the authenticity of that component. And then all the way down through the entire component ecosystem so that you can track that right down into manufacturing and product. We’re really right at the start of this transformation. The process is very historic today, there are hundreds of millions of data sheets that are just flying around. And so this is going to be a huge transformation for the electronics industry. And when we get there and as we see the steps come in place, we’re really going to see this fuel a new level of productivity and security for the industry.
[17:41] Steph Chavez: This is why I love PCB design and have a passion for Printed Circuit Engineering. It’s a truly exciting time to be a part of this industry. And to all our listeners, make sure you tune in to the Printed Circuit Podcast starting in January, where we kick off our new series on PCB design best practices.