Shift left in IC design: A holistic strategy for faster, smarter verification
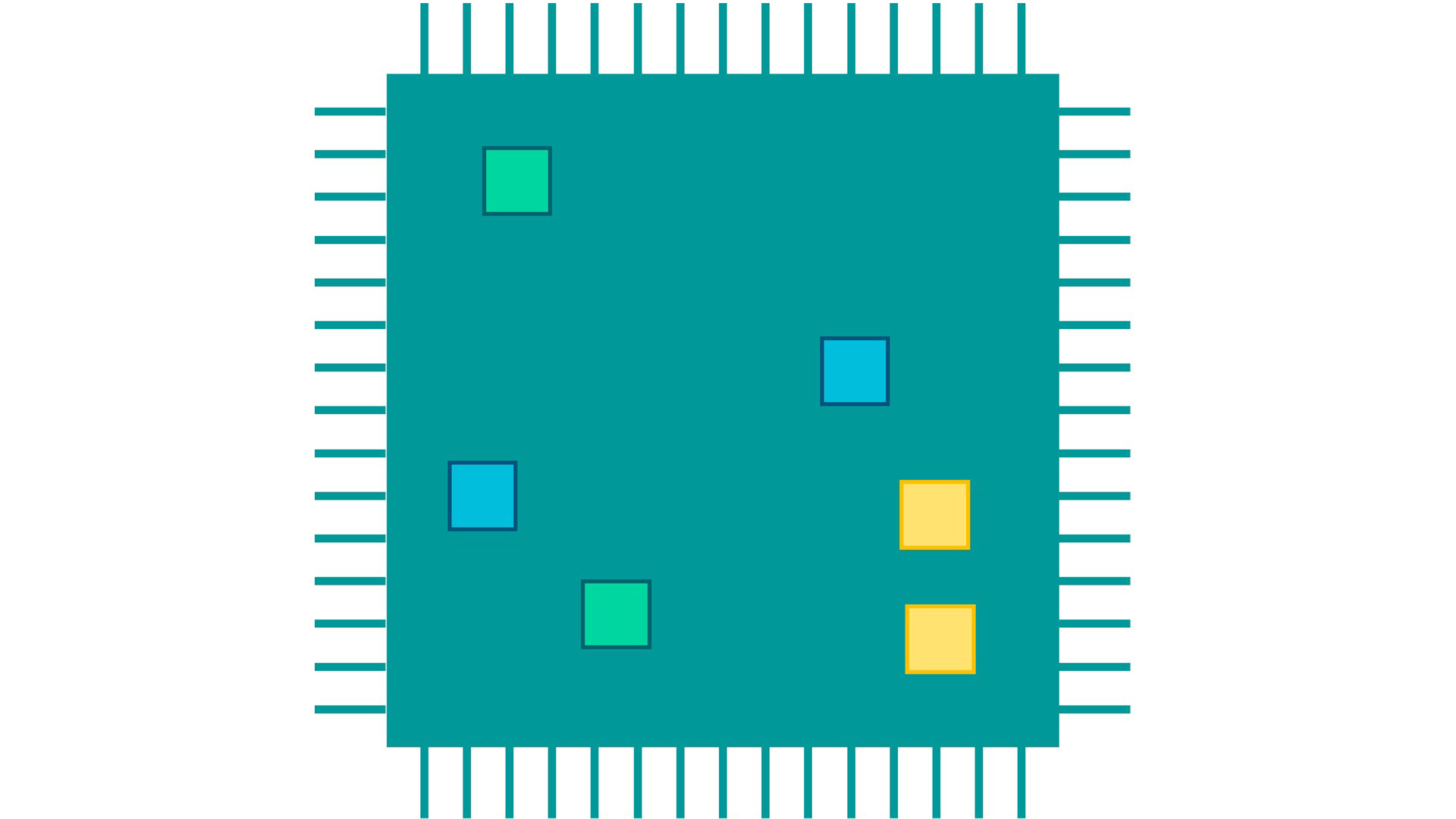
By Michael White and David Abercrombie
As IC design complexity continues to grow, companies are turning to the shift left approach, a forward-thinking strategy that moves critical verification tasks earlier in the design process, enabling faster time-to-market and higher design quality. Initially coined by software engineer Larry Smith in 2001 for software testing, shift left emphasizes the early identification of issues, leveraging automated tools to improve productivity and reduce the risk of costly errors later in the design process. In the IC design realm, shift left is far more than just a trend—it’s a transformative strategy that brings verification and optimization earlier in the design cycle, offering engineers a practical means to meet growing complexity head-on.
What is shift left in IC design?
In simple terms, shift left refers to moving key verification and validation processes earlier in the design flow. Traditionally, critical verification stages such as physical verification and design rule checking (DRC) occurred toward the end of the design process, where errors could delay production and increase costs. By shifting these checks left in the flow—hence the name—designers can catch and fix errors early, long before signoff verification.
This approach is more than a minor adjustment. It reflects a paradigm shift in how design teams handle the ever-growing complexity of ICs, from system-on-chips (SoCs) to 3DIC assemblies. Companies like Siemens have led the way in developing advanced shift left tools, such as the Calibre® nmPlatform toolsuite, which integrates Calibre signoff-quality checks into early-stage design. This ensures that designs adhere to stringent foundry rules and perform optimally under real-world conditions, well before tapeout.
We also dive into what exactly shift left is in a practical and easy to follow two minute video here Shift left with Calibre – sit back and relax with a cup of coffee to watch!
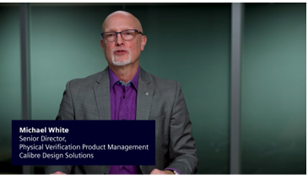
The challenges shift left can battle
The constant climb in the intricacy of IC designs has made traditional verification flows less efficient and more prone to error. When verification occurs late in the design cycle, problems discovered during signoff can require extensive redesigns, delaying time-to-market and inflating costs. For example, when errors in a nearly complete design are detected, designers often have to rework the entire layout, which may introduce new issues elsewhere.
This reactive approach has proven unsustainable, especially as design rules become more restrictive and designs more intricate. Shift left addresses these challenges by focusing on:
- Early detection of critical errors: Designers can catch errors early in the layout process, before they spiral into bigger problems.
- Improved productivity: The use of Calibre signoff-quality verification tools throughout the design flow reduces iterations and overall design time.
- Cost efficiency: By reducing late-stage rework, shift left minimizes the costly back-and-forth of error fixing and validation.
Designers can read more about how this is changing the playing field in our technical paper A game-changer for IP designers: design-stage verification
Key pillars of shift left implementation
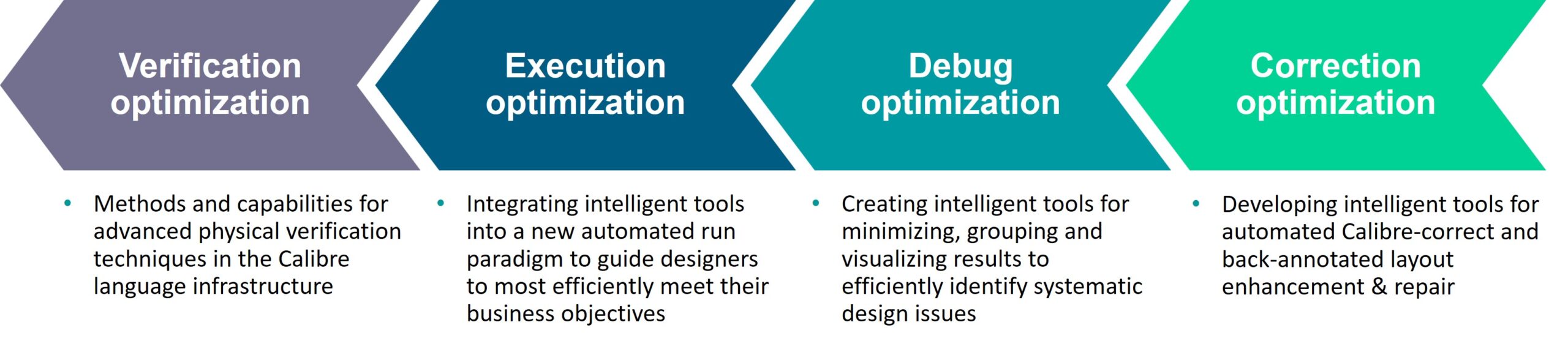
The successful execution of a shift left strategy hinges on four fundamental pillars: verification, execution, debug, and correction. For a thorough look at these pillars, you can read our technical paper The four foundational pillars of Calibre shift left solutions, but in a nutshell they are:
1. Verification optimization
The first pillar, verification optimization, is where shift left shines brightest. By incorporating Calibre signoff-quality checks into the early design stages, engineers can address critical reliability and performance issues well before signoff. Calibre’s tools enable targeted checks for symmetry, early short isolation, and pre-built reliability checks, ensuring critical issues are identified and resolved early. This minimizes the need for later debugging and reduces verification iterations.
- Equation-based DRC: Enables faster, targeted checking for specific design rules.
- Pattern matching: Identifies problematic layout patterns that could cause errors down the line.
- Embedded AI: Integrates machine learning to improve error detection and minimize verification time.
2. Execution optimization
- To ensure the shift left approach doesn’t slow down design cycles, execution optimization tools focus on efficiency. The Calibre nmDRC™ Recon tool, for instance, streamlines early-stage DRC by ignoring irrelevant errors in incomplete designs. This allows engineers to focus on fixing critical issues first. By reducing the rules and data required, these tools provide faster runtimes without compromising the accuracy of verification results.
In addition, Calibre LVS Recon™ plays a crucial role in execution optimization by verifying the correspondence between a circuit’s layout and its schematic. By integrating Calibre LVS Recon into the shift left approach, designers can catch connectivity and schematic errors early in the design process, reducing the number of iterations needed and preventing costly rework in later stages. Calibre LVS ensures that layout matches the intended design, supporting overall efficiency and improving the accuracy of verification results during the design stage.
This combined approach of early DRC and LVS checks ensures streamlined execution without sacrificing precision, helping design teams achieve faster, more reliable outcomes
3. Debug optimization
Debugging has traditionally been a time-consuming process, but shift left introduces intelligent tools to simplify error identification. Calibre’s debugging tools help group errors and visualize root causes, allowing designers to quickly understand and fix systemic issues. Automated error classification and the use of enhanced waiver processing further reduce manual debugging efforts.
Calibre RealTime Digital and Calibre RealTime Custom both enhance this optimization by providing immediate design rule checking (DRC) feedback directly within the design environment. This integration allows designers to receive real-time notifications of errors as they work, eliminating the need to wait for batch verification runs. Whether in custom or digital design, Calibre RealTime delivers instant DRC results using the same foundry-qualified rule decks used in signoff, ensuring that errors are fixed with confidence and significantly reducing the time required to achieve a clean design.
By integrating Calibre RealTime with other debugging tools, designers can quickly resolve issues as they arise, leading to faster iterations and more efficient design flows.
4. Correction optimization
Finally, shift left tools offer automated correction features that back-annotate layout changes into the design database. The Calibre Design for Manufacturing (DFM) tools like Calibre DesignEnhancer allow designers to apply fixes that enhance both the design quality and manufacturability. This correct-by-construction approach ensures that the design is optimized for real-world performance, without tying up costly design licenses.
The business impact of shift left
For IC design companies, the shift left strategy brings measurable business benefits. By moving critical checks to the early stages of the design process, companies can achieve faster time-to-market, reduce engineering costs, and ensure higher-quality designs. A holistic approach to shift left includes improving productivity through automation and optimizing resource usage.
Benefits of this early-stage verification include:
- Reduced time to market: With fewer reworks and quicker design iterations, shift left can significantly compress production schedules.
- Higher design quality: Identifying and fixing errors early in the process leads to better overall design quality.
- Increased engineer productivity: Automated verification tools reduce manual checks, allowing engineers to focus on innovation.
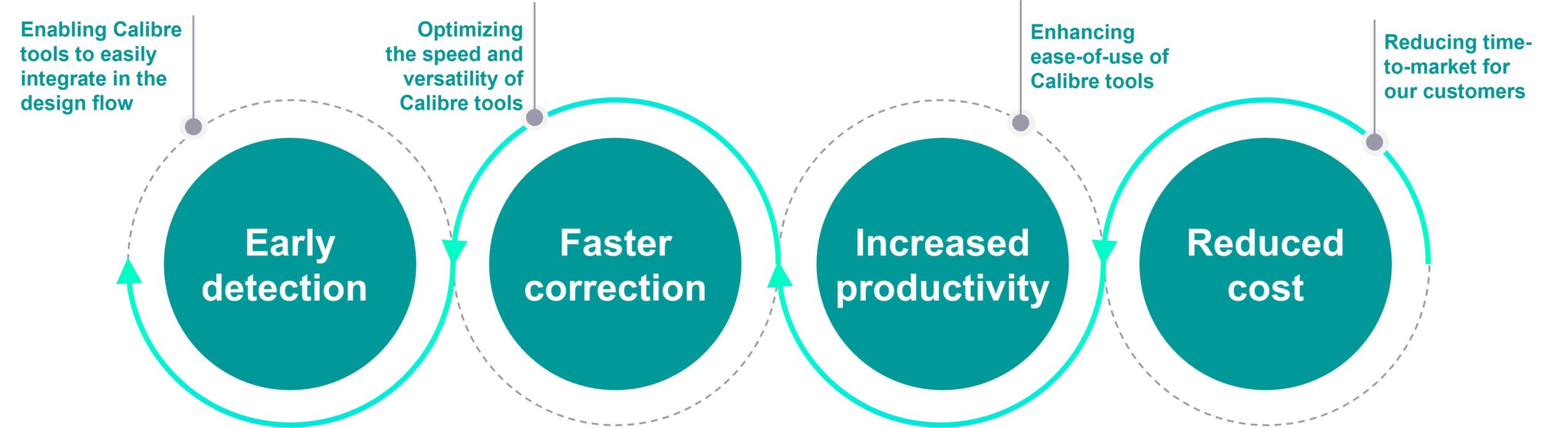
design companies with the greatest value.
Best practices for implementing shift left
To fully realize the benefits of shift left, IC design companies should follow best practices that maximize the impact of this strategy.
- Leverage Calibre signoff-quality tools early: Use the same foundry-preferred verification engines throughout the design flow to avoid discrepancies between early-stage and signoff results.
- Automate wherever possible: Automation not only speeds up the process but also improves accuracy by reducing human error.
- Train engineers on new tools: While shift left offers user-friendly environments, ensuring teams are familiar with the full functionality of these tools is key to success.
- Adopt AI and ML: Take advantage of embedded artificial intelligence to improve verification outcomes and resource efficiency.
The role of artificial intelligence in shift left
As designs grow more complex, traditional verification methods can struggle to keep up. Machine learning (ML) and artificial intelligence (AI) play a crucial role in optimizing the shift left process. By analyzing large datasets and identifying patterns, AI helps improve verification efficiency and resource allocation. AI-driven tools can also provide intelligent debug signals, further speeding up error identification and correction.
- Resource forecasting: AI predicts resource requirements, allowing design teams to plan more effectively.
- Faster setup: ML models reduce the time spent configuring verification runs, improving overall design flow efficiency.
Conclusion: The future of IC design
Shift left is more than a buzzword; it is a proven strategy that has transformed IC design. By focusing on early detection of errors and leveraging cutting-edge technology, shift left allows companies to deliver better products faster and more efficiently. Tools like the Calibre nmPlatform offer the flexibility, automation, and power to fully realize the potential of shift left, ensuring that companies can thrive in an increasingly competitive landscape. You can find a complete suite of Calibre’s shift left solutions with one click right here!
For those looking to improve design quality, reduce time to market, and increase productivity, the shift left approach is no longer optional—it’s essential.