Simplified model generation for AGV simulation using Plant Simulation software
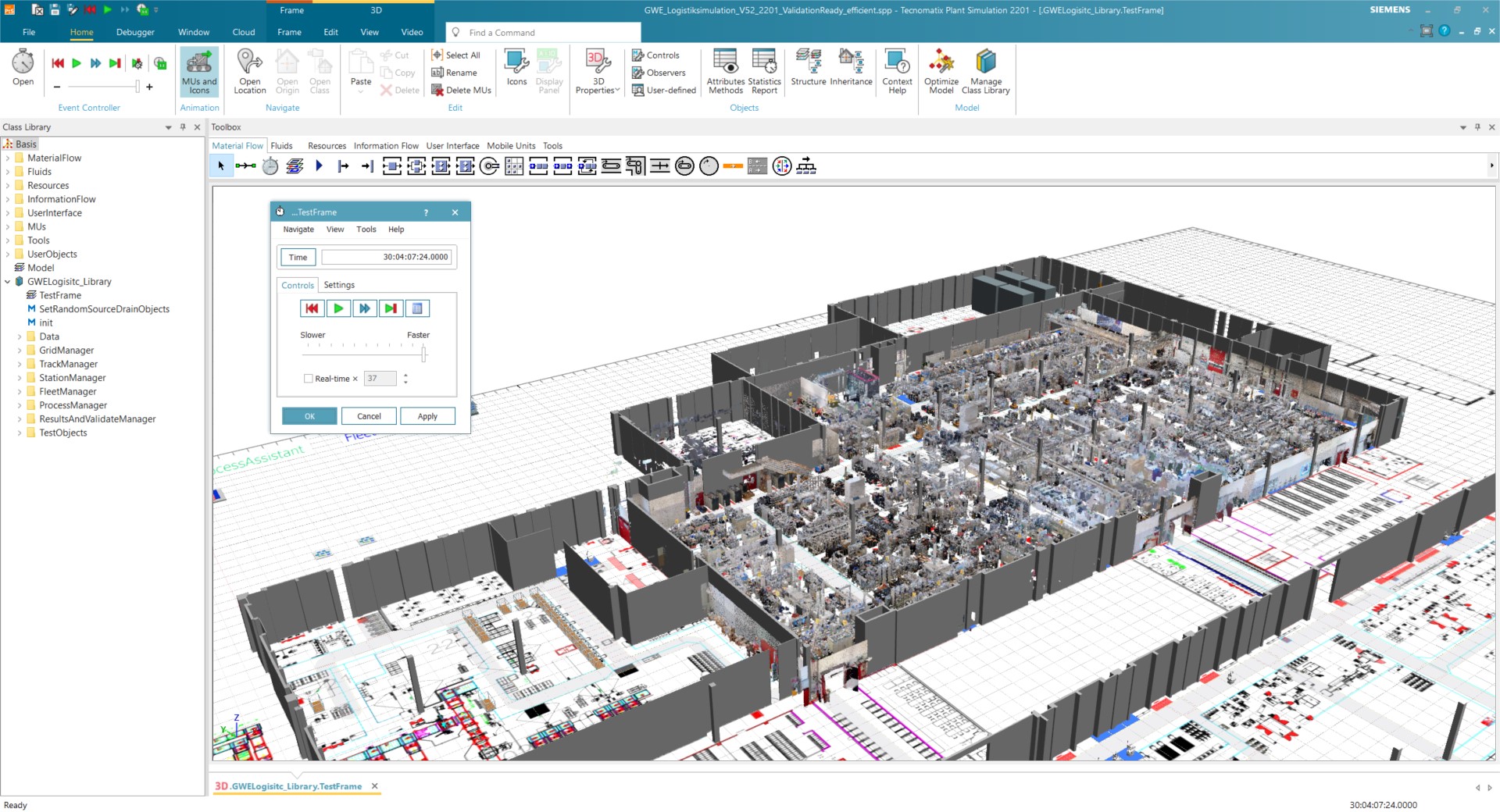
Dynamic modeling at Siemens electronics equipment plant in Erlangen
Lars Schreiber, material flow simulation expert at Siemens AG, will lecture at the 2023 Plant Simulation User Conference, July 13th, Infinity hotel, Munich, Germany.
Introduction
Dynamic AGV simulation plays a crucial role in optimizing logistics and production processes, allowing businesses to streamline operations and improve efficiency. At the Siemens Gerätewerk Erlangen (GWE), a pioneering approach has been developed to simplify the process of creating dynamic models for the simulation of automated guided vehicles (AGVs). This innovative method, based on grid blocks within the layout, eliminates the need for expert knowledge, ensuring that the models remain up-to-date and adaptable to changing production environments. This article explores the dynamic modeling approach implemented at GWE and its significance in supporting logistics and production planning.
Lars Schreiber, an accomplished professional in the field of industrial engineering, has been an integral part of Siemens AG at the Electronic Device Plant Erlangen (GWE) since 2019. Holding a degree in Industrial Engineering from FAU Erlangen-Nürnberg, Lars has leveraged his expertise in material flow simulation and served as a key user in numerous production and logistics projects. His proficiency in utilizing advanced software tools like Teamcenter, NX Line Designer, and Plant Simulation has played a leading role in driving digital consistency and innovation at GWE.
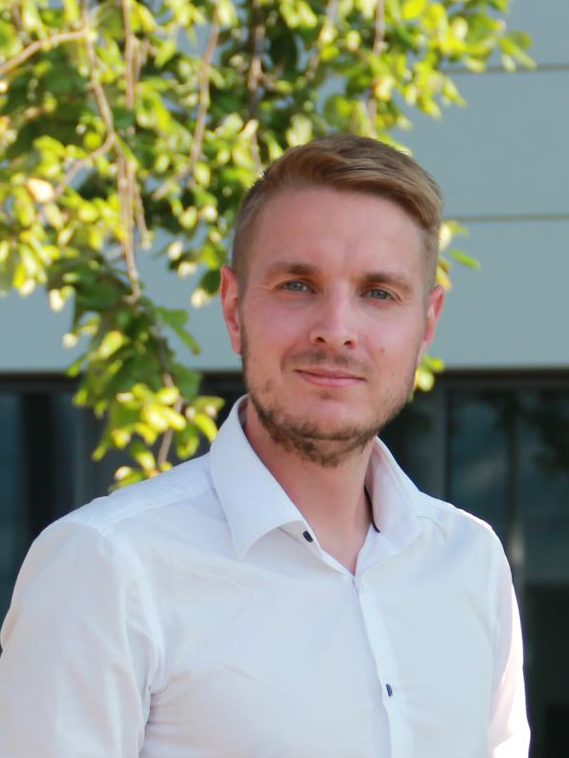
The AGV simulation challenge
AGVs are an essential component of many modern manufacturing facilities, providing automated material handling and transport solutions. However, the successful implementation and optimization of AGV systems requires careful planning, including the ability to accurately simulate their behavior within the production environment. Traditionally, creating AGV simulation models has been a complex and time-consuming process, often limited to experts with deep, specialized knowledge. This constraint hinders agility and responsiveness to evolving production needs.
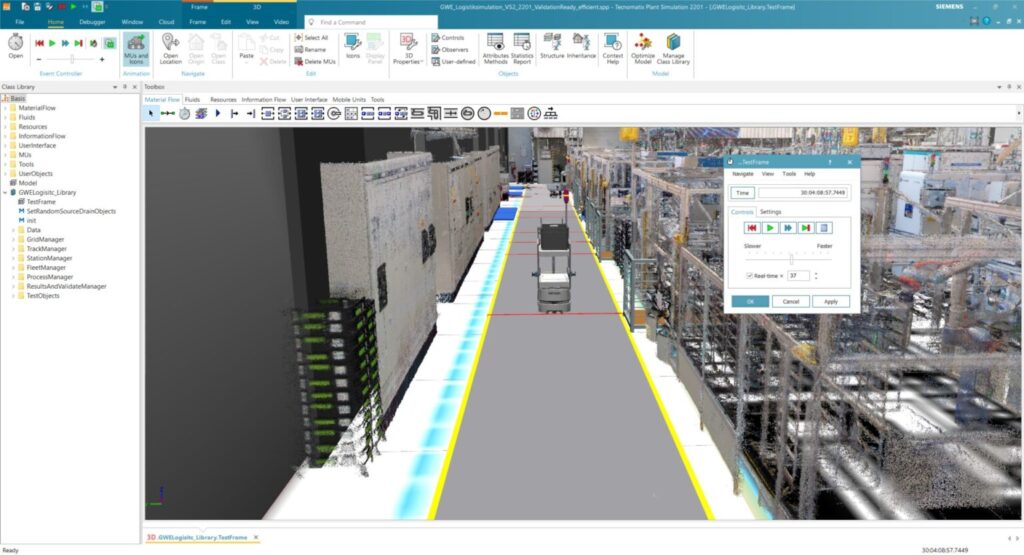
Simplified model generation utilizing grid blocks
To address the challenges associated with AGV simulation, GWE has developed an automatic Plant Simulation software model setup based on predefined grid blocks. This innovative approach simplifies the modeling process, eliminating the need for expert knowledge and enabling dynamic updates as the production environment evolves.
The use of grid blocks allows for a systematic representation of the layout, wherein each block corresponds to a specific area of the production floor. By associating relevant attributes and behaviors with each block, the model captures the movement, interactions and operational constraints of AGVs within the facility. This simplified representation significantly reduces the complexity of the model setup process, making it accessible to a broader range of stakeholders.
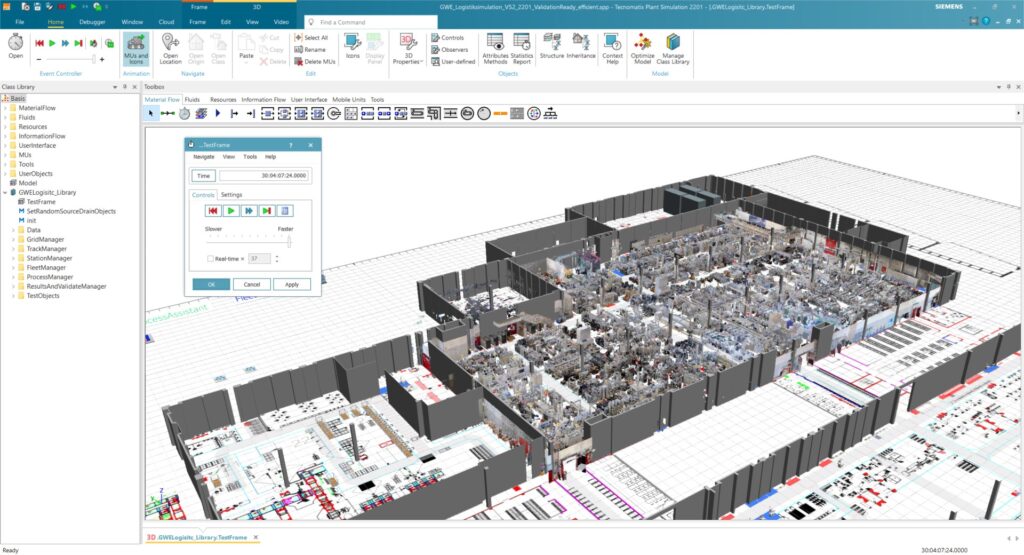
Integration of CAD layout and 3D scans
To enhance the accuracy and realism of the AGV simulation model, GWE integrates the CAD layout and point cloud data created by 3D laser scans into the Plant Simulation software environment. By incorporating the CAD layout, the model aligns with the physical design of the production floor, ensuring that the simulated AGVs navigate accurately throughout the material flow simulation model. Additionally, 3D scans provide detailed point cloud data, allowing for a precise representation of the production environment within the simulation.
Benefits and applications
The dynamic modeling approach based on grid blocks brings several benefits to Siemens Gerätewerk Erlangen.
Firstly, it simplifies and accelerates the process of AGV simulation model generation, empowering a wider range of users to contribute to the optimization efforts. This flexibility supports continuous improvement and enables timely adjustments to production layouts and logistics operations.
Secondly, the simplified model generation ensures that the simulation remains up-to-date, reflecting the latest changes in the production environment. This dynamic aspect enables decision-makers to assess the impact of proposed modifications, such as introducing new machinery or altering production volumes, before implementing them in the real world. Consequently, the risk associated with making changes is mitigated and the overall planning process becomes more reliable.
Furthermore, the AGV simulation models serves as a valuable tool for logistics and production planning. This enables the identification of bottlenecks, optimization of material flow and increased overall equipment efficiency.
Other relevant content: