Tire model parameterization: A complete revamp of MF-Tool
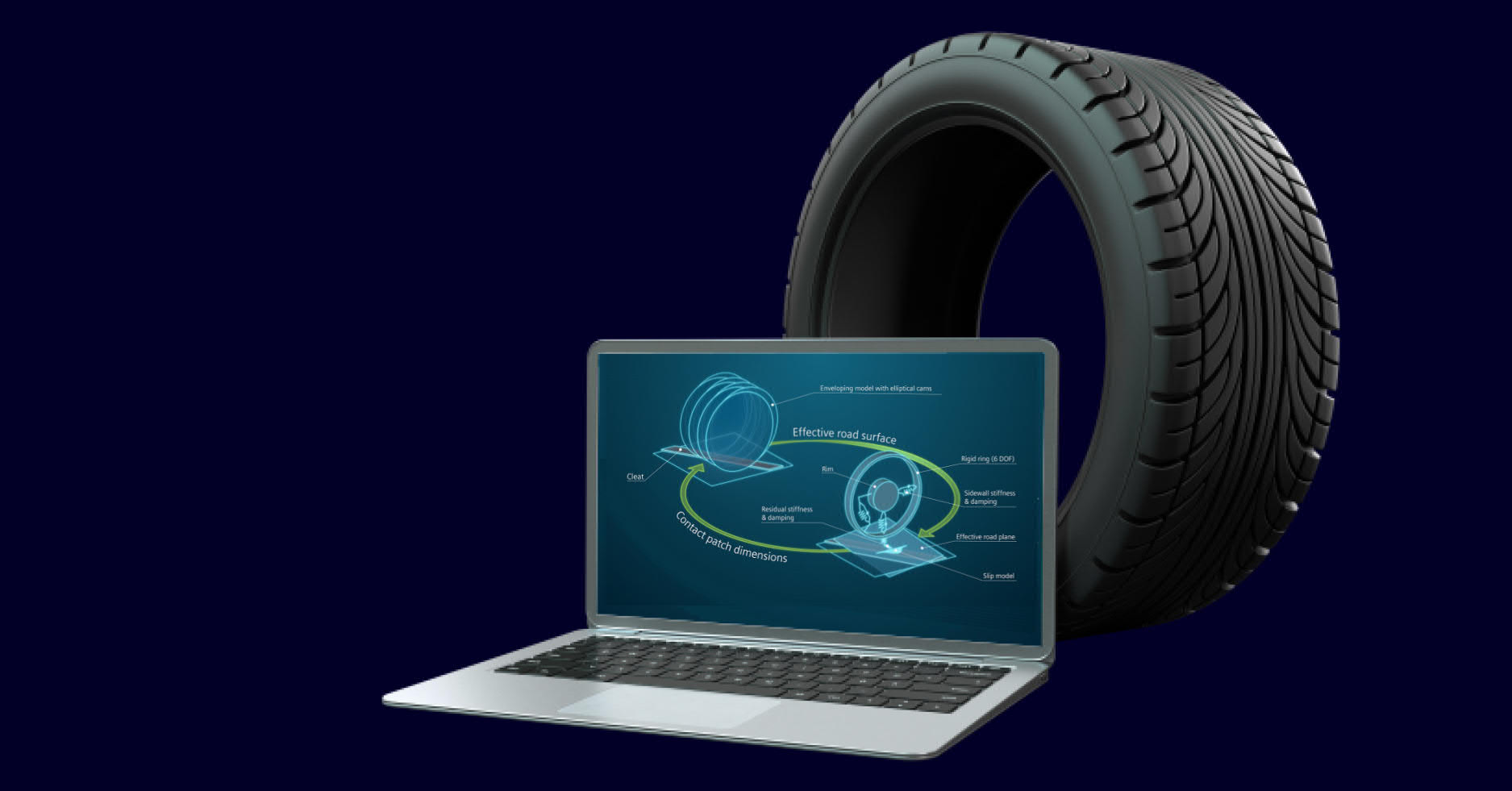
Why do we need a tire model?
Creating an accurate tire model is becoming increasingly important across the industry, as engineers are more regularly relying on virtual engineering to create and launch their new products. They do this to reduce the number of required physical (expensive) prototype vehicles, and to shorten the design process. Additionally, the advancement of simulation tools allows them to solve increasingly more complex problems such as NVH and safety compliance. To help engineers achieve this, Simcenter Tire has significantly updated its tire model parameter identification software, MF-Tool.
Creating and then using a tire model normally consists of three steps, as seen in figure 1, and explained below:
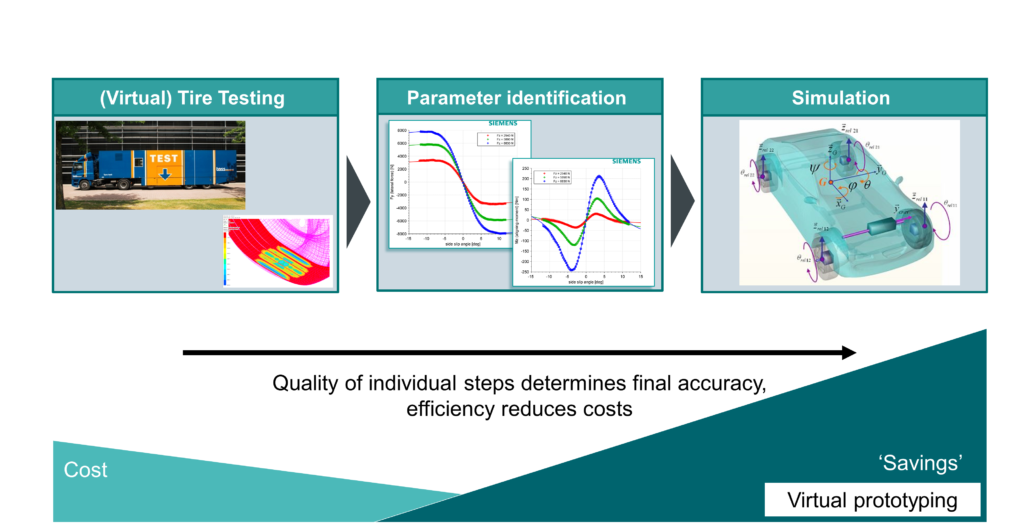
1. (Virtual) Tire testing
You must first collect test data for the specific tire for which you would like to create a model. This is often done by driving the tire on a test rig – e.g., the Siemens outdoor test trailer, see Figure 1 – under a wide range of conditions. An engineer achieves this by measuring and recording the forces and moments the tire experiences during the test. Alternatively, simulations via a Finite Element Model (FEM) can replicate tire tests (although these are often less accurate).
2. Parameter identification
A tire model is then fitted to the test data. A popular tire model used widely across the industry is Siemens’ MF-Tyre/MF-Swift. The model is a parameterized set of equations: by identifying the model parameters based on inputted test data, the model can closely replicate the tire performance.
3. Simulation
The resultant ‘Tire Property’ (TIR) file contains a parameter deck. By loading this deck into the user’s vehicle simulation environment, which includes the MF-Tyre/MF-Swift tire model, an engineer can virtually replicate the specific tire’s performance.
The cumulation of all the individual steps is the prerequisite to ensuring the quality of the resulting tire model. Hence, tire model parameterization is an essential element of a tire modeling methodology. The Siemens software that performs this parameter identification is MF-Tool.
MF-Tool 2022.1: A complete revamp
With a revamp of the MF-Tool product in the 2022.1 release, the Simcenter Tire team significantly contributes to increased user experience and robustness. The new tool consists of a graphical user interface (GUI) and a fit kernel (see Figure 2).
GUI designed for tire modelling
The GUI is developed within Simcenter’s own Testlab software. Testlab provides a very powerful environment for data handling, sharing, processing, and visualization.
Typically, a tire fitter engineer has a preferred fitting methodology finetuned to the measurement protocol. This might include defining specific fit steps, fixing/unfixing parameters, customizing parameter boundaries, etc. Creating such a bespoke ‘recipe’ every fit session can be tedious and take up time that could be better spent. In MF-Tool 2022.1, the user can create fitting templates to load when starting a fit session, thereby streamlining the process.
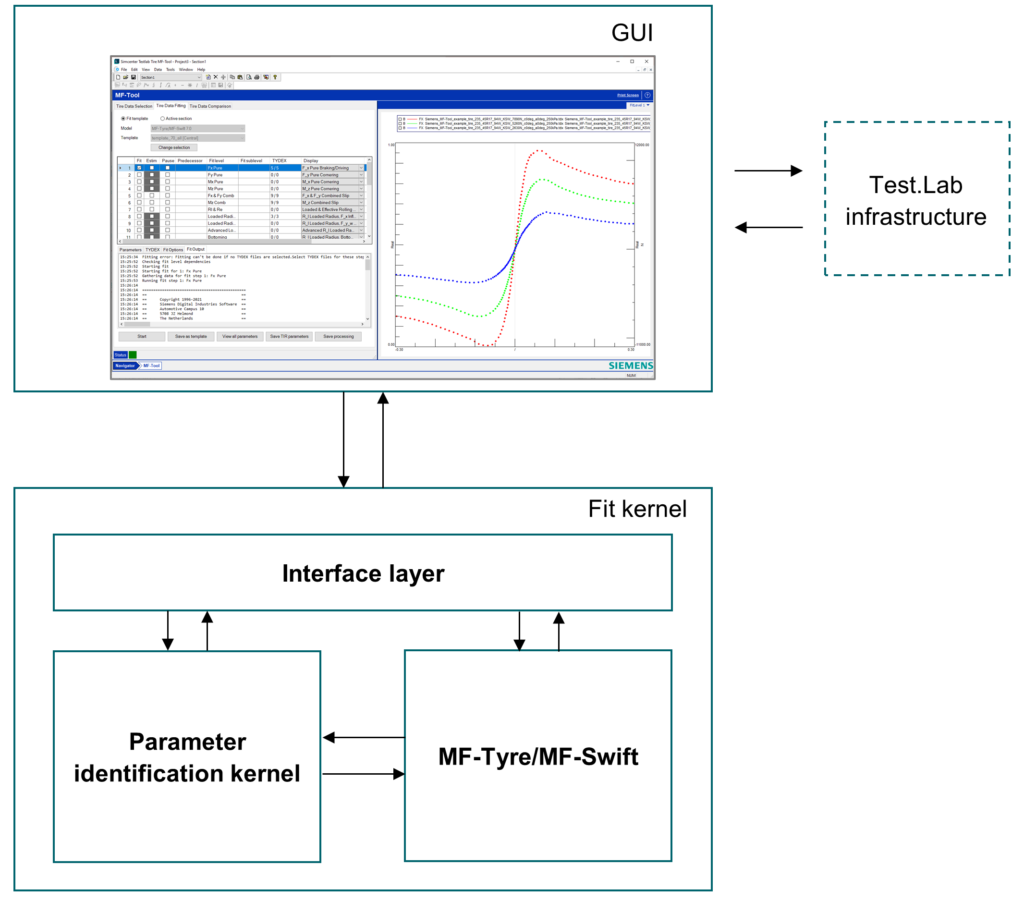
Fit kernel
When tire modeling becomes mainstream in a company, the parameterization of a large number of tire models is required. Manually fitting all these models is a cumbersome task and is more prone to human error than when using an automated process. To reduce such human error, we can use the fit kernel in two ways: with the MF-Tool GUI, or as a standalone executable. The executable comes with a documented interface, allowing customized implementations in dedicated customer processes.
As well as the new GUI and fit kernel, the MF-Tool 2022.1 release includes the parameterization of two new tire modeling features:
Temperature & Velocity fitting
In the 2020.2 MF-Tyre/MF-Swift release, it became possible for customers to include the tire’s dependence on temperature and velocity (‘T&V’) within their MF-Tyre/MF-Swift models. In the previous release, the T&V model extension would need its parameters set internally by the Simcenter Tire team, as the existing MF-Tool does not have this functionality. In MF-Tool 2022.1, this parameterization is entirely at the fingertips of the user.
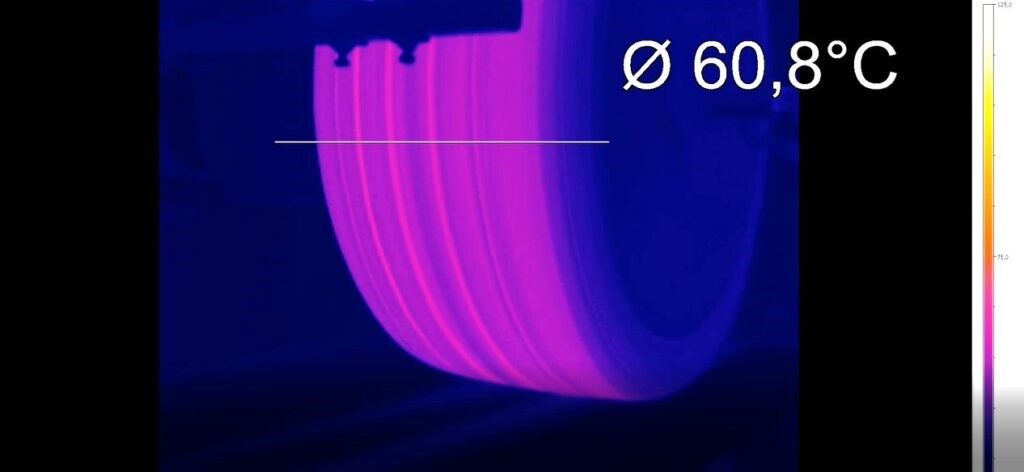
Turnslip fitting for steering system development
Digitizing steering systems is also becoming increasingly important to our customers. We have seen a significant uptake in the usage of our Turnslip modeling capability within MF-Tyre/MF-Swift across the industry. This feature is an add-on to the Magic Formula and can accurately predict the tire forces and moments during low-speed steering and parking maneuvers. Like the T&V fitting, it is possible to identify the MF-Swift Turnslip parameters in the new MF-Tool release.
Conclusion
Simcenter Tire recognizes the importance of providing engineers with robust tire model fitting software. Therefore, we have completely renewed our MF-Tool product and can now provide a flexible, powerful, and user-friendly tire model parameter identification process. In addition to the intuitive GUI and improved fit kernel, MF-Tool 2022.1 comes with several valuable new features, including:
- Temperature & Velocity and turn slip fitting integration.
- Templating of fit (or ‘recipe’).
- Easy data handling and visualization.