6 myths about CFD for ship design
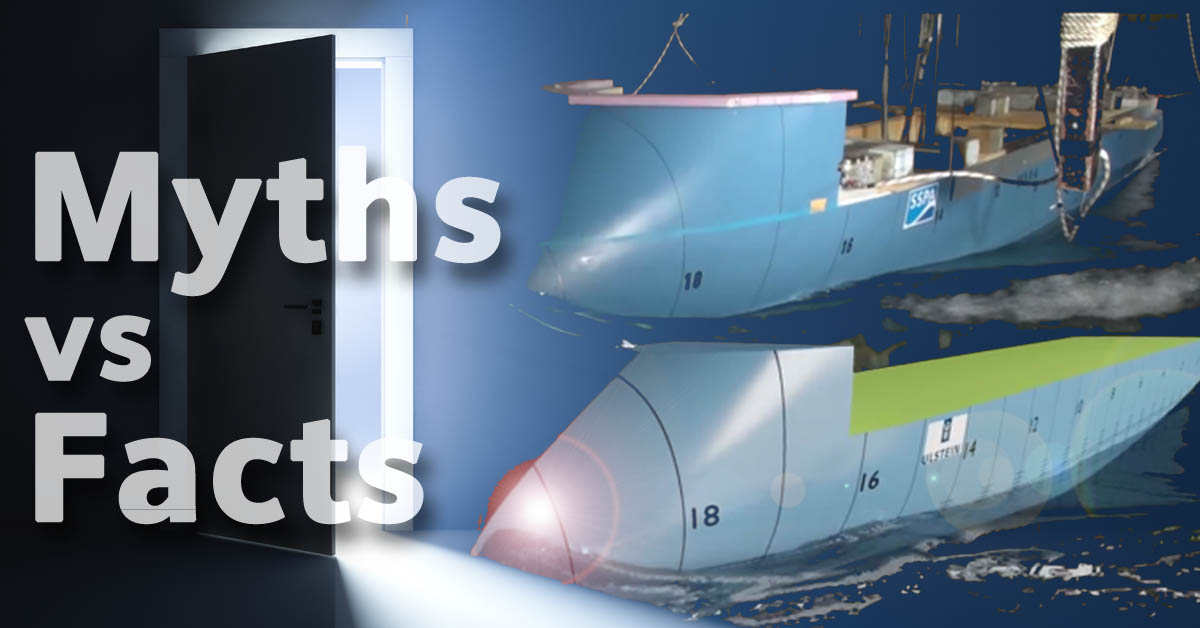
Computational fluid dynamics (CFD) has been used for hydrodynamics analysis and ship design for a few decades now. But many in the marine industry still consider it to be an academic tool, only useful for comparison to towing tank results, or only suitable for very simple cases. Towing tank results are considered to be the truth even though the limitations of this approach are well known. Why is this?
I hear the same arguments against CFD from many people in the industry. But I believe these arguments – or myths – are based on outdated ideas of what marine CFD is and how it can be used in this industry. In this blog I systematically debunk those myths, in the hope of reducing your dependency on expensive model scale testing and opening your mind up to the same opportunities that simulation and digitalization has introduced to other industries.
What is a towing tank?
First, though, some background. The first commercial ship basin was commissioned in 1883. Since then, towing tanks have provided naval architects with a method of predicting the performance of a ship at sea. Both resistance and propulsion tests are carried out in towing tanks. Scaled ship models are either towed or self-propelled through the water. Naval architects use the results to assess hull forms and rate how much power the engine will have to provide to achieve the speed laid down in the contract between shipyard and ship owner.
However, towing tank testing is expensive and time-consuming. Because of this, it is only used toward the end of the design process. Testing is limited to verifying and fine-tuning an established design. The results can’t provide engineering insights early in the design process. This means the data can’t help to drive the design in different, better, more efficient, directions. In addition, any novel solution tested at model scale has increased uncertainty of actual performance at ship scale due to fundamental deficiencies of the scaling process and the lack of statistical data to improve its reliability.
So why is the marine industry still so focused on physical testing, when other industries are now focusing on virtual prototyping and CFD? Let’s take a look at some of the main objections and why they are wrong.
Myth 1. Marine CFD is complicated: only a specialist can run simulations
Ten years ago this myth was probably still true. Back then, building a CFD mesh was a specialist job that involved as much art as it did science. And running the CFD software required specialist knowledge to set it up correctly for marine simulations. Not any more. Over the past decade we’ve worked hard to incorporate all of the best practices required to develop a numerical towing tank simulation into a set of automated templates that anyone can use. Some people call that “democratization”, but we think that it’s just common engineering sense. Simulation should be accessible to everyone who needs it.
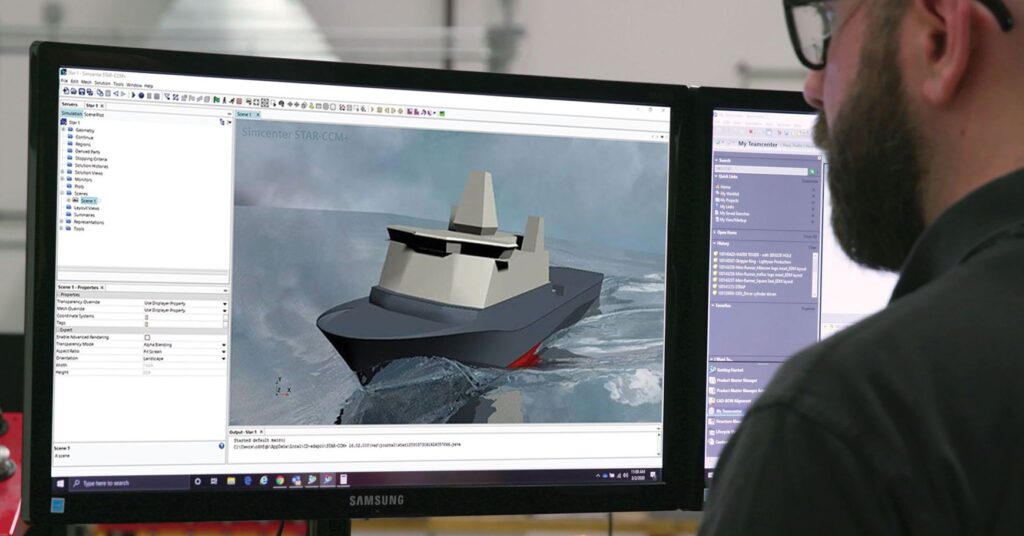
And we also have a tool specifically designed for naval architects. Simcenter STAR-CCM+ Hull Performance Workflow provides a dedicated user interface for simulations of ship motions in calm water. The menus guide you through each step to set up and run a hull resistance simulation, from CAD import and specification of single or multiple speeds in one session, to automatically generating a PowerPoint presentation report with images and standard towing tank-like results. You can try this yourself as part of our 30-day free trial for marine CFD.
Myth 2. Towing tank measurements are more accurate than CFD results
This myth is usually used by people who don’t want to move away from their comfort zone of towing tank tests – they know and trust those results, and don’t want to consider CFD as an alternative. Bear in mind that towing tank data is not the truth, though some people treat it this way. It is a long-standing source of information in the industry, but it is just an approximation to actual ship performance, with inherent problems with accuracy. Both experiment and CFD have established ways to quantify the possible errors. Good reports will include error bounds for both methods – if they are not there, ask why not!
CFD actually has several inbuilt advantages which reduce uncertainty, and importantly, human error:
- 100% repeatability – every time you run the same simulation the result will be the same.
- 100% consistency – if different people or companies run the same CFD model the result will be the same.
- Actual physics – you can run CFD at full scale, removing the errors associated with scaling up towing tank data.
- Standardized processes – by creating automated, templated CFD processes you can encapsulate best practices and remove human error.
To push you further on this, take a look at this comparison from Ulstein, of their CFD simulation and a towing tank test. Can you tell the difference? But beyond this, CFD gives you more information than a tank test and doesn’t have to be run at model scale – more on this later on.
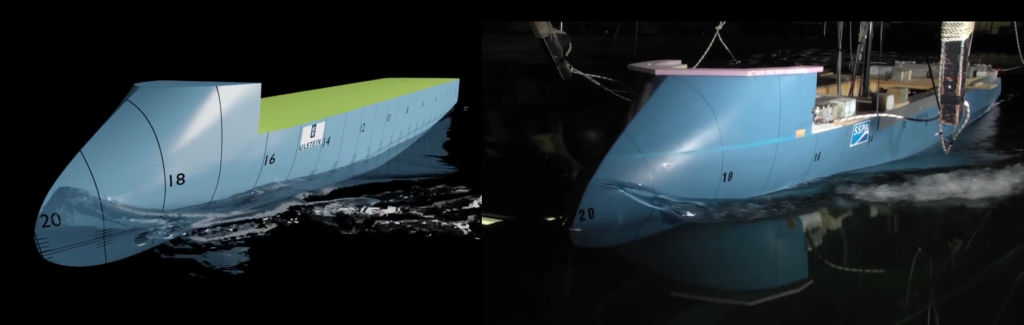
Myth 3. CFD is only used for hull resistance calculations
Nothing could be further from the truth! Hull resistance calculations are the starting point for most people in marine CFD. But the power of simulation is that you don’t have to make your numerical towing tank simulations a facsimile of a real towing tank. In the virtual world it is easy to include the effect of waves for example, or investigate propeller performance, or planing hulls. You can think beyond the basic data requirements and virtually test the vessels on the real-life challenges they face during operation.
Here’s an example from a recent webinar, showing how Cape Horn Engineering simulated a turning yacht, including self-propulsion, and moving rudders and fin stabilizers. This is much more than hull resistance!
And of course, CFD is just one simulation tool that you can use. Wärtsilä use connected Simcenter tools to create a digital twin of a vessel’s propulsion system. Every vessel is unique, so every propulsion system is unique. To ensure optimal performance for each vessel, Wärtsilä uses their ‘opti-design’ approach. They simulate the complete ship hull, propeller, appendages, and free surface using CFD. But they also include a 1D system simulation model of the engine, enabling them to predict not only power but also fuel consumption over realistic operating profiles. Simulation goes well beyond hull resistance!
You can learn more about our portfolio of Simulation and Testing tools for marine in this short video.
Myth 4. CFD takes too long to run. We can’t use it for every project.
The question here is how long is a ‘long time’? These days, you can run a single speed hull resistance calculation on a decent laptop in a matter of hours. Compare this to the weeks that towing tank testing takes. Better still, when combined with inexpensive cloud computing resources you can turn around hundreds of simulations a day. For example, this blog explains how you can run 55 simulations in just 45 minutes (using Simcenter STAR-CCM+ and cloud computing).
For a more detailed argument against this myth, read this white paper which describes how a Simulation-Driven design approach means you can run 500 hull analyses in just 4 days. This means you can examine many different design alternatives, to find the best one for your requirements – in less than one week. And if the thought of all that data feels overwhelming, don’t worry. The analyses are run automatically through HEEDS, Simcenter’s design space exploration and optimization software package. HEEDS presents the results in easy to understand summaries, making it easy for you to see both the big picture and examine individual design results.
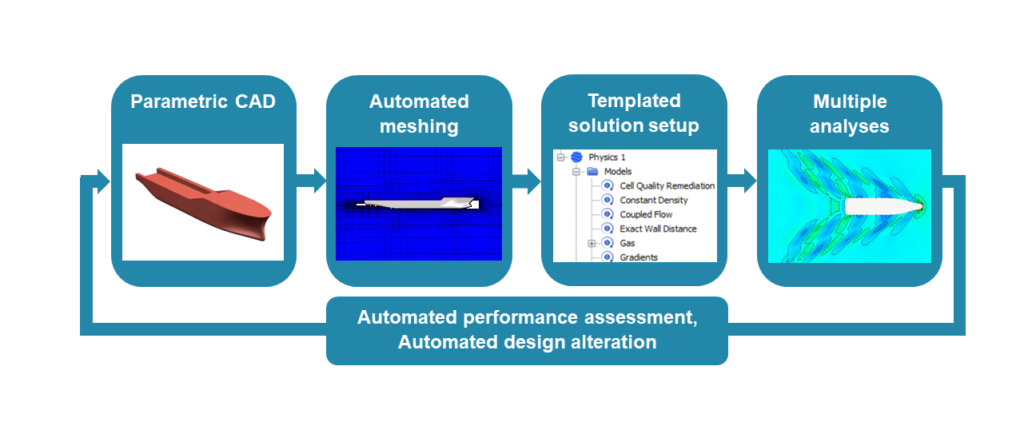
Myth 5. Towing tank tests are the industry standard, CFD doesn’t add anything
The industry standards are changing. For example, NYK Line and Japan United Corporation (JMU) have introduced a new contract guaranteeing propulsion performance in actual sea conditions. This will be verified using data collected during ship operation. Simulation is the only way to predict performance in actual conditions during the design phase. If you need more confidence, take a look at the America’s Cup races. Under the AC75 class rule, physical testing in wind tunnels or towing tanks is not permitted. Instead, the teams design, test and even virtually race the boats using simulation.
By all means run a tank test at the end of your design process – some customers still want this data, and cross-validation of your final design is always a good idea. But bear in mind the limitations of scale model tank tests. Don’t let a tank test be your excuse for not perfecting the full-scale performance of your vessel, which should be the primary objective of any ship design process. Professor Milovan Peric (one of the world’s leading experts in marine simulation) explains the benefits of full-scale simulation in this white paper.
Myths 3 and 4 above should have convinced you that simulation gives insights above and beyond tank test results. I don’t see CFD as an addition to ship design, but an essential tool in meeting today’s design and efficiency targets.
Myth 6. Classification societies won’t accept CFD results
This is not true. All of the classification societies use CFD simulation extensively. They are well aware of how the results can be used in validating ship safety and certification. For example, Lloyds Register has been using Simcenter STAR-CCM+ since its launch in 2004. In this webinar they explain their use of hydrodynamic simulations for vessel performance and safety. Similarly, the American Bureau of Shipping (ABS) has presented their work on automated CFD simulation and parametric design. This way they can run hundreds of simulations per day and rapidly turn around accurate ship design evaluations. And if you want a third example, you can read how DNV used CFD to optimize hydrodynamic hull performance for a new fleet of container vessels. This reduced hull resistance by 36% without reducing capacity.
In fact, the IMO also recognizes the benefit of simulation in assessing ship performance. In June 2021, they adopted MEPC.334(76). This gives guidelines on calculating the Energy Efficiency Existing Ship Index (EEXI) for ships currently in operation. The committee agreed that ship speed-power relations can be calculated using CFD. So all the regulatory bodies are aware of the benefits and uses of CFD for marine applications.
The future of ship design needs CFD
So there you go – 6 myths, debunked. If you have been wondering about the benefits of CFD for ship design, hopefully this blog has helped to answer your questions. And if you have more questions, why not ask in our community, or browse our marine web pages.
Let me know if there are any more myths you think I have missed! When you are ready to take the plunge and try marine CFD for yourself, sign up for our 30 day free trial and see for yourself how you can use CFD in your ship design process.