New DFAN (Direct Field Acoustic Noise Testing) as a service to launch in US – Live demo on September 22, 2021
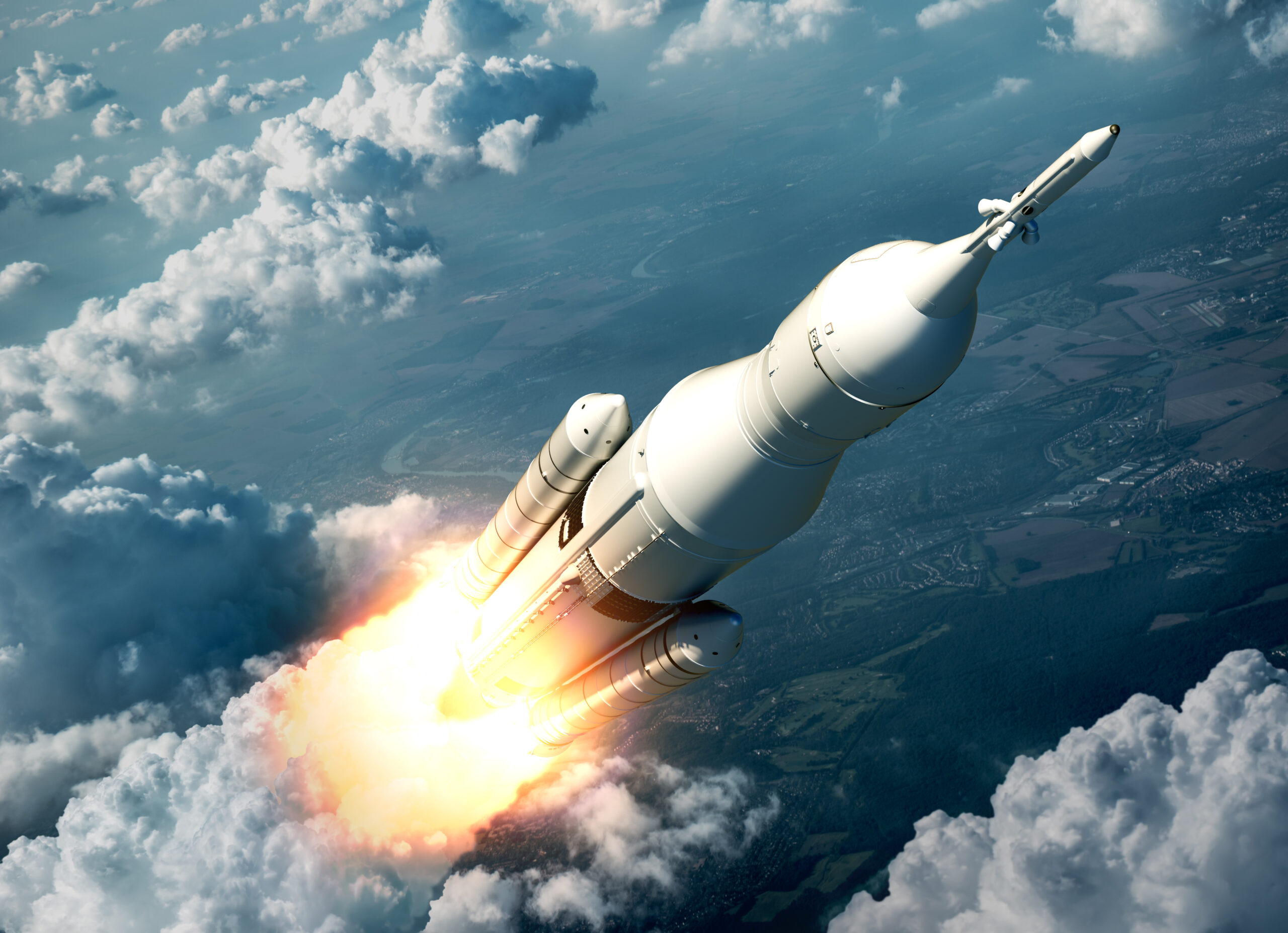
How many decibels (dB) are emitted during a spacecraft launch?
According to NASA, the answer is up to 220 dB. To put this into context:
- A normal conversation is 60 dB
- A vacuum cleaner is 75 dB
- The inside of a subway is 95 dB
- A rock concert is 129 dB
The human ear becomes irreversibly damaged close to ~120 dB. At 150 dB, human eardrums can burst. Above 180 dB can be deadly (hello, Game of Thrones-style death).
Noise at this level produces a hazardous and unstable environment during launch. This can be problematic, not only for the payload itself but also for the sensitive equipment it may be carrying, such as rovers, satellites, etc.
DFAN helps protect precious cargo
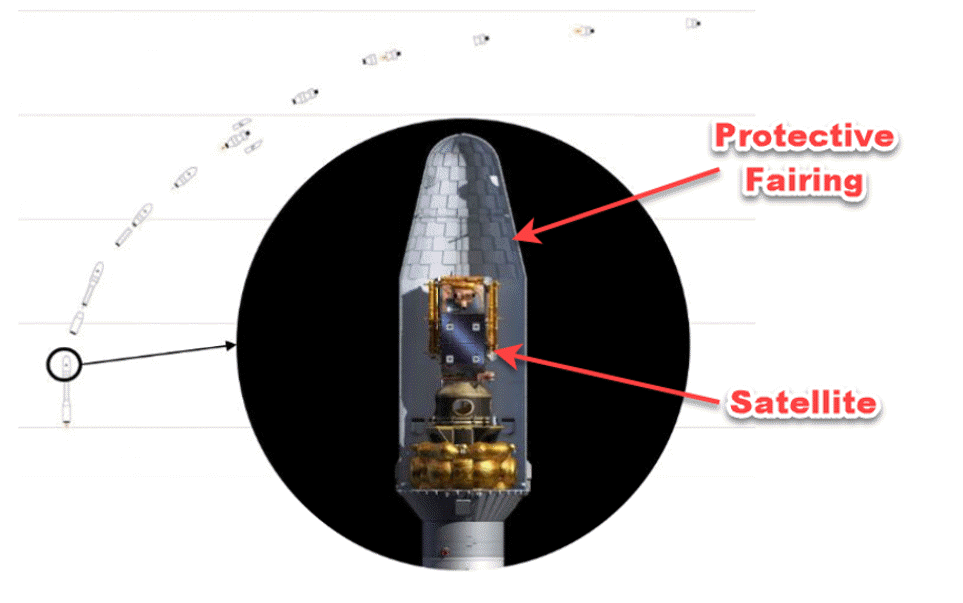
Most payloads that are launched into space are placed at the top of the rocket. Here they are provided with a protective fairing, but this is often not enough for the delicate structural and electronic components from the harsh conditions created at launch. Engineers need to perform extensive testing before launch to understand if the payload can survive the noise and vibration loads.
Direct Field Acoustic Noise Testing (DFAN) is a physical test method that replicates the vibro-acoustic conditions that a spacecraft and individual components will experience at launch. DFAN is performed by surrounding the rocket with speakers and subjecting it directly to the same noise level it will experience at launch.
This is much more cost-effective than traditional acoustic testing methods, which require a dedicated facility with reverberant rooms. While these rooms provide very reliable results, they are extremely expensive to build. If a company does not have these facilities, they must move the spacecraft to an available chamber (in some cases even to a competitor’s location), which adds to the cost, complicates the logistics, and increases the chances of damage.
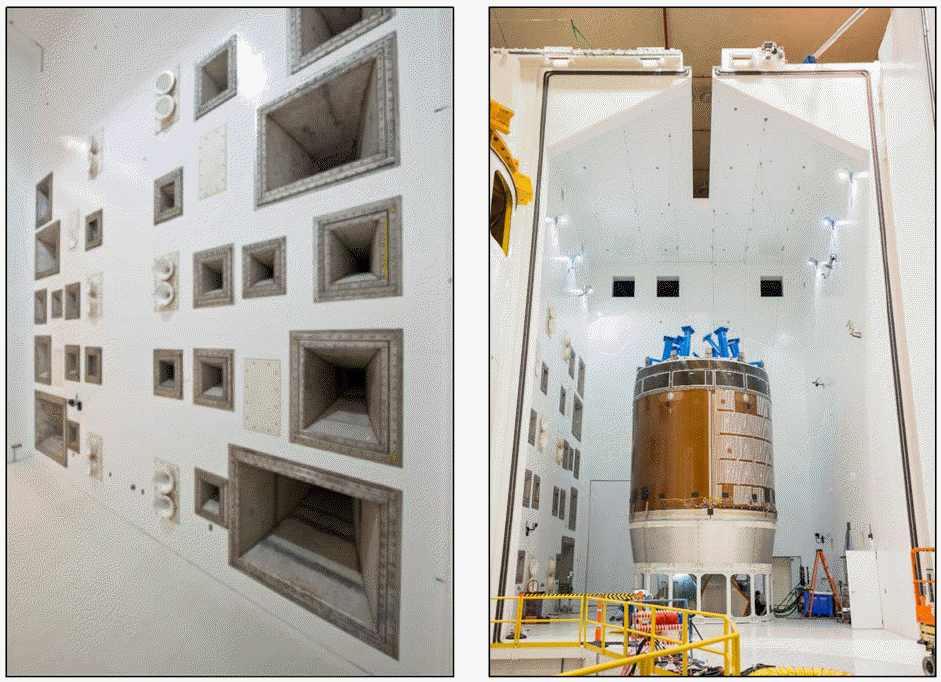
DFAN sounds like a pretty great alternative, right?
While DFAN is a highly accurate, lower-cost alternative to traditional testing methods, like any technology, it is only as good as its practitioner. When misapplied, DFAN can be inefficient and expensive.
The main challenge that companies face with DFAN is variability in the test arrangement and possibilities. For example, typical questions include:
- How many speakers are required?
- How should the speakers be configured?
- How many control microphones are required?
If these are not answered before testing begins, engineers may discover that there is not enough acoustic energy due to too few speakers. Alternatively, they may find out that they invested time and budget into too many speakers.
DFAN can also be a costly endeavor, particularly since it is not a system that most companies will use every day. Therefore, it is often safer and more cost-efficient to procure DFAN testing as a service.
DFAN as a service
The Simcenter Engineering team at Siemens Digital Industries Software has developed a DFAN as a service capability to address these challenges. Incorporating both test and simulation, the Simcenter Engineering team will soon provide and manage all aspects of DFAN testing.
DFAN testing setup
Hardware setup, MIMO control, and data acquisition and analysis are typically the most challenging aspects of DFAN testing. By performing this testing as a service, Simcenter Engineering frees up valuable engineering time for space companies. It spares companies the cost of investing time and budget into a DFAN system.
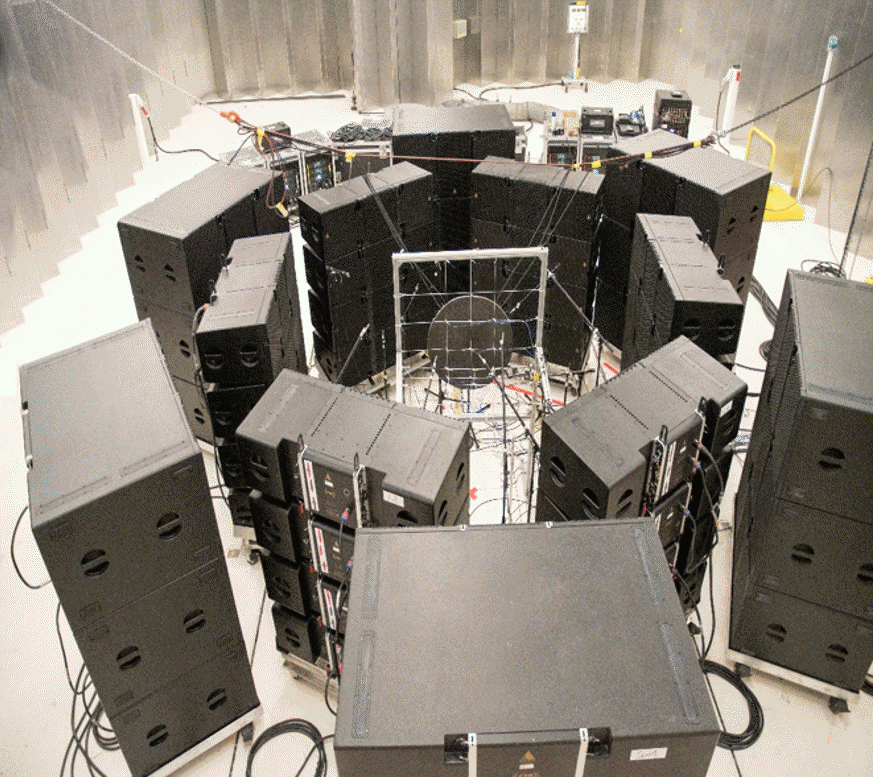
As part of this new offering, Simcenter Engineering provides:
- All aspects of speaker array set up and tear down (configuration/pre check and rigging) – utilizing industry proven loudspeaker/amplifier systems.
- DFAN-experienced personnel ready to support different system configurations.
- Simcenter SCADAS MIMO Random Control System (acoustic control module).
- Increased efficiency and safety thanks to unique test-based pre-test analysis for optimized control channel selection.
- Collect pressure, acceleration and/or strain gauge response using standard Simcenter Testlab and Simcenter SCADAS hardware.
- Hardware and software safety shutdowns for DUT protection.
- Onsite concurrent data processing and analysis (time history and frequency data).
- Thousands of channels of data acquisition hardware and transducers available in inventory.
- More insights in the dynamics of the structure by performing operational modal analysis on measured acceleration response data (optional).
Numerical pre-test analysis
Using Simcenter 3D, Simcenter Engineering experts can determine the appropriate speaker and microphone configuration to meet Device Under Test (DUT) acoustic loading requirements. This includes the speaker arrangement, position of the test item, and reflectors as needed and helps improve the uniformity of the acoustic field. Setting this up in simulation reduces the number of iterations that would need to be done through physical testing, which significantly reduces the time and cost of DFAN testing.
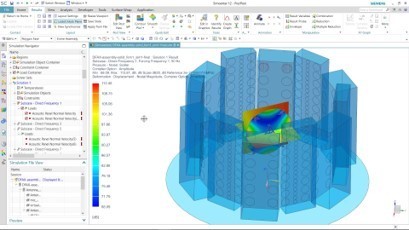
Attend the live virtual demo!
On September 22, 2021, Simcenter Engineering will present a demonstration of DFAN as a service. The event will be held live and also streamed virtually for those who cannot attend in person. If you are interested in attending this free event, please email paul.deacon@siemens.com or albert.prosuk@siemens.com.