Looking for a three-way catalyst reaction model development workflow?
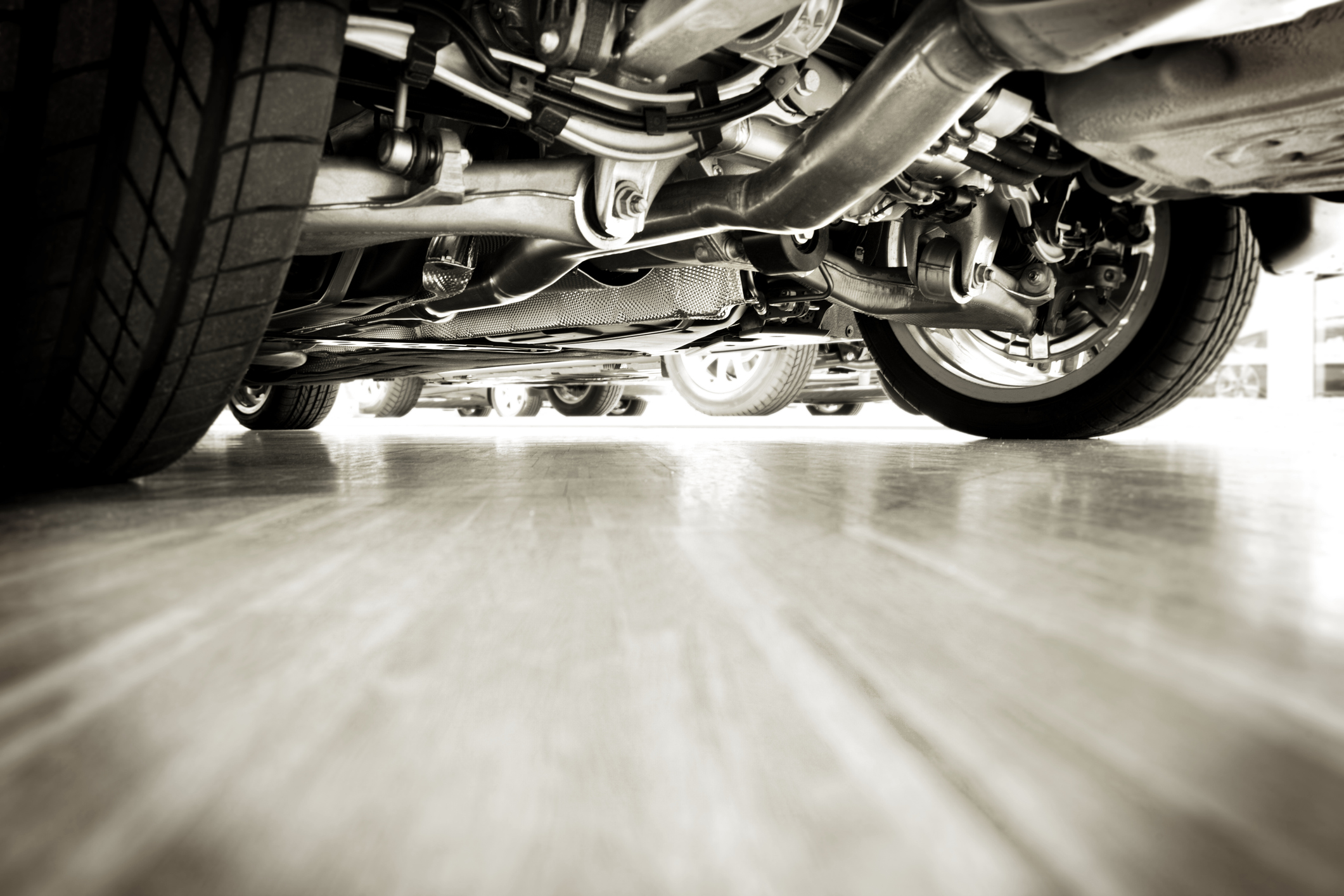
Simulate vehicle emissions in real conditions requires the set-up of a catalyst model with proper reaction mechanism representation. But this is not enough to get close to real conditions as the catalyst model must be put in a vehicle context and hence connected to powertrain subsystems and controls similarly to catalyst real environment.
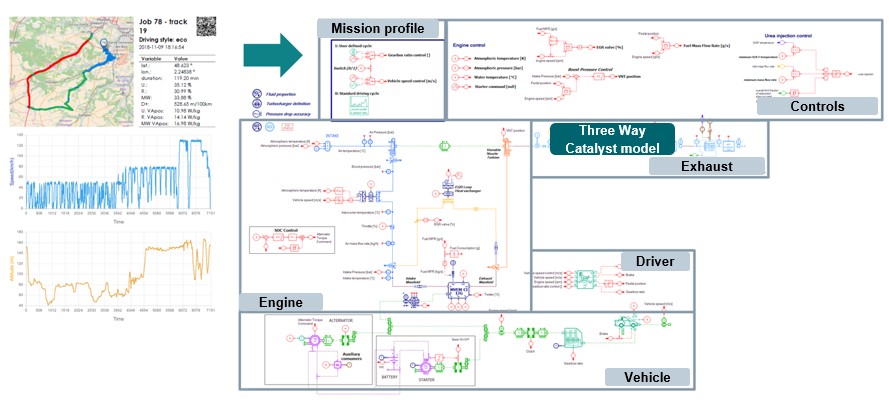
The three-way catalytic converter model should be compatible with system integration requirements. This implies in particular very short simulation times (preferably faster than real time). Hence, when looking for a three-way catalyst reaction model development workflow, we should consider this requirement.
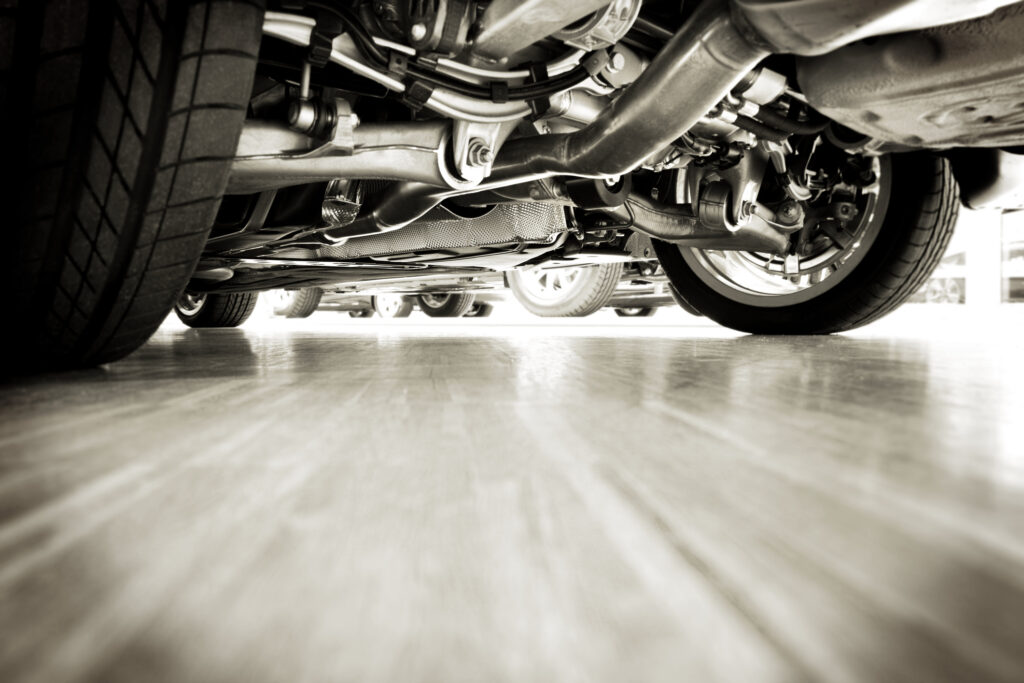
Even if model-based development is a key enabler for the design of vehicles with well-controlled emissions, experimental data remain crucial for both catalyst reaction model calibration and model validation.
What is the challenge of three-way catalyst reaction model development?
Now the challenge in reaction model development is to find the right balance between kinetic model accuracy and computational times… while adapting to modeling and calibration strategy to test data available!
Simcenter Amesim 2020.1 release
In this release, you will discover a three-way catalyst reaction model development workflow with various options depending on the test data available.
This tries to address a commonly raised question when looking for a three-way catalyst reaction model development workflow: how to handle use cases where available test data are not enough to get input model’s parameters?
Moreover, the updated workflow includes an investigation of a globalized reaction mechanism consistent with experimental observations or washcoat composition. The starting point is a core reaction mechanism representative of commercial three-way catalyst common capabilities:
- CO and HC oxidation
- NOx reduction
- Oxygen storage reactions
You can add Further reactions during reaction mechanism identification step. The objective is to get a model with a minimal set of reactions as a pre-requisite to a time and cost-efficient calibration process associated with fast simulation times.
Any tool to help developing this three-way catalyst reaction model?
New oxygen storage capacity computation demo
Three-way catalyst reaction model requires oxygen storage capacity parameter. Corresponding parameter estimation closely depends on experimental tests and catalyst characteristics data.
In case oxygen storage tests data are available, a new demo helps to estimate this oxygen capacity parameter. In this model OSC is deduced from mass balance equations based on oxygen adsorption and carbon monoxide oxidation reactions.
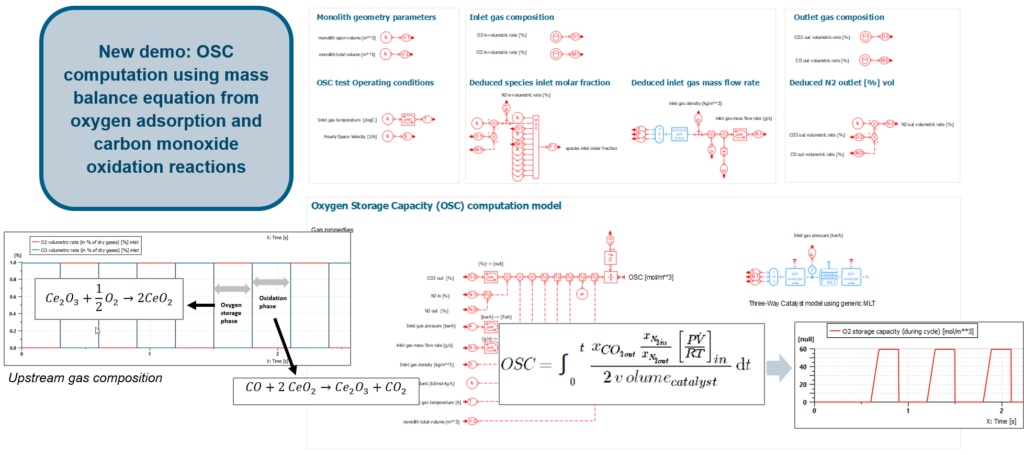
You don’t have access to oxygen storage tests? No worries, theoretical formulas to compute OSC from washcoat and monolith characteristics are also available in the three-way catalyst methodology guide.
Exhaust calibration tool
Simcenter Amesim offers an exhaust calibration tool to easily set up and tune catalyst reaction model with the following 5-step methodology:
- Set the exhaust line architecture
- Set the monolith/filter geometry
- Choose the chemical scheme model (following the updated reaction model development workflow)
- Load and preprocess available test data
- Make use of optimization to automate the model calibration process
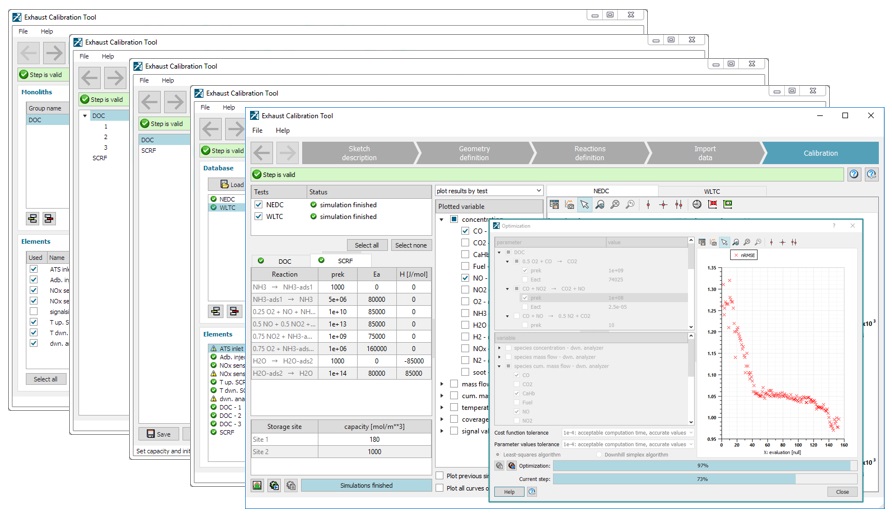
The exhaust calibration tool description is available in this blog post. It offers a versatile environment for the definition of the right kinetic model for your application. Starting from pre-defined reaction schemes, completed with case-specific reactions, you can quickly iterate to get the most appropriate catalyst model for your application.
You want to learn more about the Simcenter Amesim exhaust calibration tool? Then, join the on-demand webinar Optimizing exhaust systems for emissions reduction using simulation.
In addition, this webinar presents how system simulation enables the evaluation of numerous concepts and designs of exhaust after-treatment systems. For example, Paul Boucharel, a technical expert for powertrain system analysis at Continental, explains how catalyst models help to develop control strategies for the global energy management of a powertrain. More info here.
Does this workflow yield to good results?
This updated workflow has proven its relevance through real application cases from key players in the automotive industry. It is introduced and illustrated in the Siemens presentation at the 2020 CLEERS virtual workshop. Actual results from a project with SUBARU Corporation were presented at this occasion. Reaction model results show a good agreement with experiments under stoichiometry, lean and rich operating conditions, for instance. Moreover, the short simulation times match system integration requirements. In conclusion, we can take advantage of broader context with close coupling with the internal combustion engine and its controls. The presentation material is available here.