Mixture Multiphase – 3 great enhancements that put mixtures at the heart of hybrid multiphase CFD
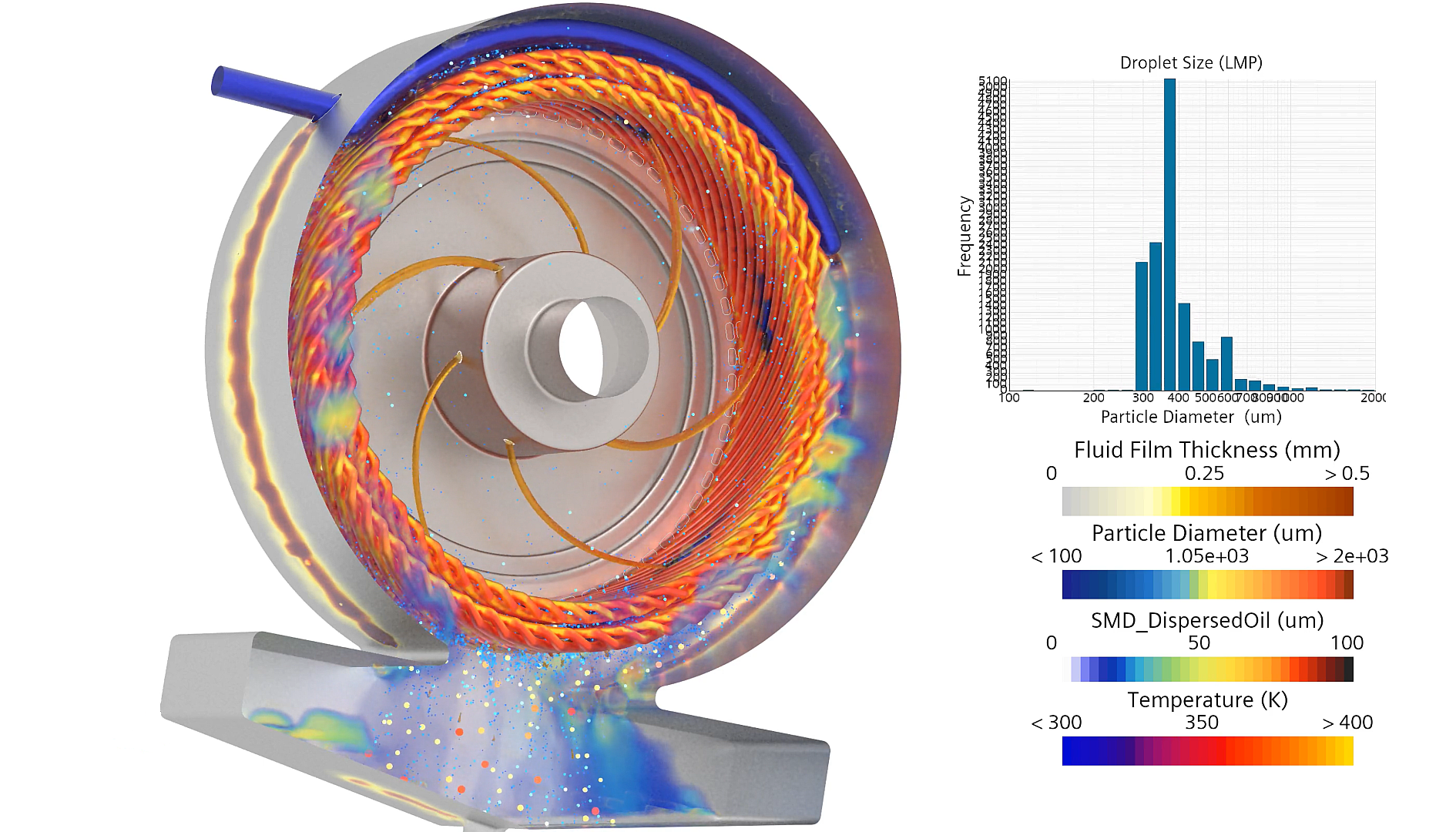
For a new technology to succeed it must arrive at the right time, provide a solution to a real-world problem, and solve that problem better than any other competing technology out there.
That might have seemed like the case when the first electric cars started to appear in the 1880s, at last a less polluting vehicle after the coal guzzling steam cars and carrot guzzling horse drawn carriages that went before. Cities were being electrified and other electric vehicles such as trams became common.
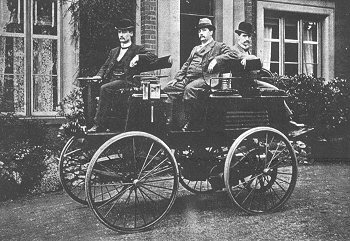
In this environment, the EV started to gain traction at the end of the 19th century (if you pardon the pun), although adoption was limited to US and European cities where electrical infrastructure existed. It was not yet to be the era of the EV however, as the initial rapid growth of the technology hit a wall in the 1920s overtaken by the Internal Combustion Engine and cheap and abundantly available oil. The electric vehicle was relegated to be forgotten in dusty archives, where it lay quietly forgotten for most of the next century…
There it remained, until the elephant in the room that was the climate crisis could no longer be ignored and at last the time was right for the EV.
Of course, electric vehicles are not without their challenges – mainly related to the battery and motor. In our world of Engineering Simulation, battery thermal runaway and e-motor cooling have become very hot topics (literally!). These are simulations that would have been unthinkable just a few years ago due to their complexity both in terms of geometry and Multiphysics.
Consider e-motor cooling for example, it is highly complex due to the range of scales involved. Cooling jets of oil breakup into ballistic droplets and then ever smaller droplets due to the high rotational speeds and interaction with the intricate end-windings. Clouds of droplets of tens of microns or less form mixtures and even foam. Thin films of oil form on many surfaces. In other places oil pools. Oil flows through tiny gaps going where it should not. All of this happening alongside heat transfer and electromagnetics.
Hybrid Multiphase Comes of Age
These complex applications pose new demands of simulation, the tools of the past are no longer sufficient and the time for hybrid multiphase is here!
Individual multiphase models like Volume of Fluid (VOF) and Mixture Multiphase (MMP) were designed for a single multiphase flow regime. The VOF method for example expects everything to be resolved and has no concept of a mixture, whereas Mixture Multiphase expects only mixture and no resolved free surfaces. Pick any one method for these new applications and it will be pushed beyond its assumptions and produce inaccurate results. For this reason, the move to more complex multiphase applications drives a need for hybrid multiphase.
Adding Mixtures to Hybrid Multiphase
In Simcenter STAR-CCM+ 2406, Mixture Multiphase has been put at the heart of hybrid multiphase to enable applications such as e-motor cooling with three great new features:
1. Lagrangian to Mixture Multiphase sub-grid transition model
The first of our trio of features is the ability to transition small Lagrangian droplets to a dispersed mixture phase. It can also be used for bubbles or solid particles, but I will focus on liquid droplet phases here.
Lagrangian multiphase is well suited to modelling large, high momentum droplets that travel in a different direction to the surrounding gas, but when simulating the secondary break-up of droplets, you can end up with a large population of tiny droplets that follow the gas path. This is essentially a mixture and Lagrangian would not be a good model choice.
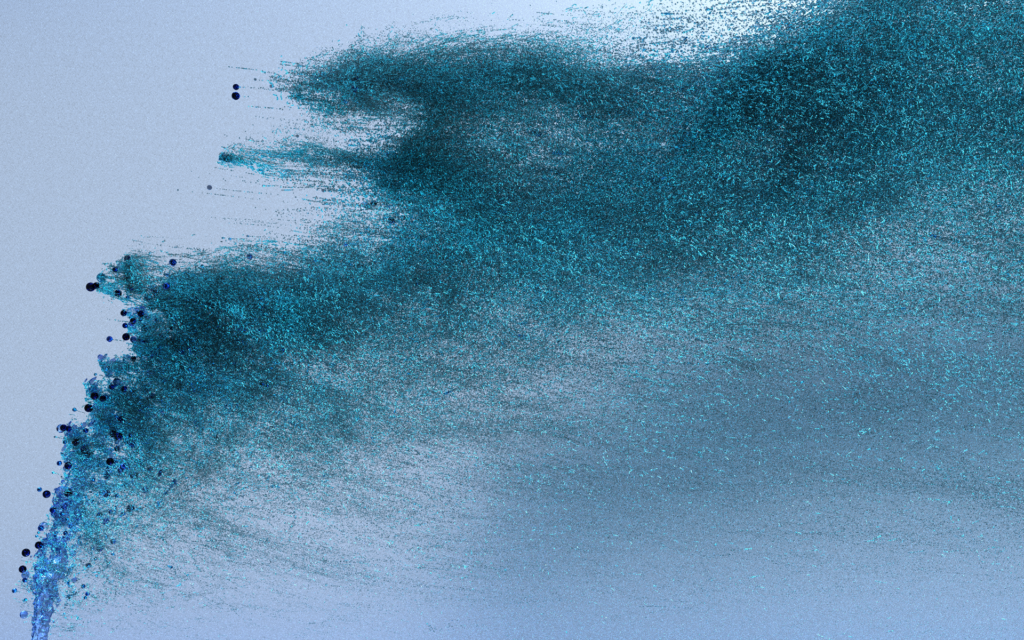
With the new Lagrangian to Mixture Multiphase sub-grid phase interaction model, Lagrangian droplets can be transitioned to a mixture representation in Mixture Multiphase. This allows Lagrangian multiphase to be used only for high momentum ballistic droplets whilst the larger population of smaller droplets is transported as a mixture. This new functionality works with MMP-LSI – a model that combines the capabilities of VOF and Mixture Multiphase, using interface capturing locally where needed and allowing mixtures elsewhere. With this combination, we can now model the full cascade of multiphase scales from the resolved to the sub-grid.
In the example below, we resolve the initial stages of breakup of a jet in crossflow using Large Scale Interface (LSI) modelling, before passing the resolved droplets over to Lagrangian where they continue to breakup into ever smaller droplets. Once the droplets are small enough and traveling with the surrounding gas they are passed to an Mixture Multiphase phase as a mixture. Transition is based on droplet size and Stokes number.
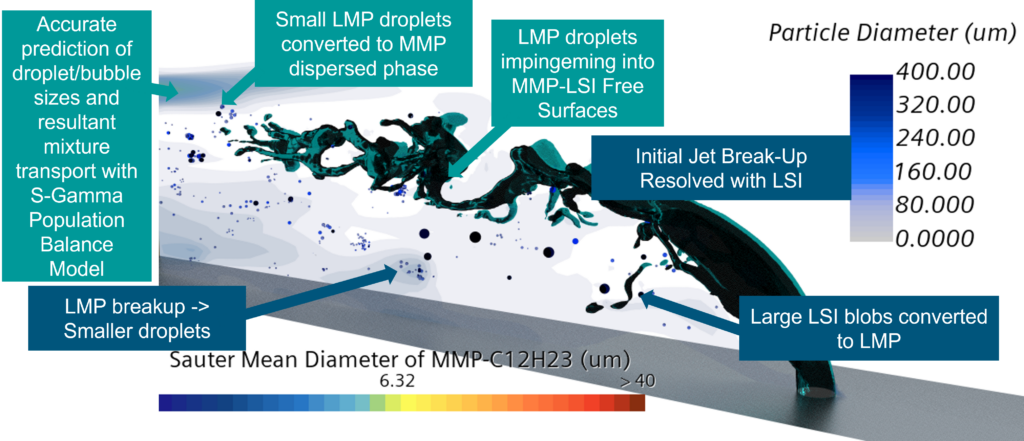
2. Population balance modeling for Mixture Multiphase Large Scale Interfaces (MMP-LSI)
Now we have a predictive route for the size of droplets being produced by the breakup of large bodies of fluid such as jets, we need a method of capturing that valuable data and using it in our simulations.
Droplet size is an important variable in determining the transport of mixtures, and critical for physics such as evaporation or reactions. For that reason, we have added support for the S-Gamma population balance model with MMP-LSI. The S-Gamma model transports a distribution of sub-grid droplet sizes which it modifies every time Lagrangian droplets are transferred. In addition, S-Gamma models the effect of further breakup and coalescence.
This is critical in applications such as e-motor cooling where jets of oil breakup into ever smaller droplets that may be 10s microns in size that are carried with the rapidly rotating air and even whipped into foam.
We can see this model in action in the jet in crossflow example below where the predicted droplet size distribution from the jet breakup can be seen in terms of the Sauter Mean Diameter of the resultant sub-grid droplet population
3. Lagrangian impingement into Mixture Multiphase continuous phase
The third and final feature in our trio is another new phase interaction model – the ability of Lagrangian droplets to impinge into continuous phases in Mixture Multiphase.
In hybrid multiphase simulations the same fluid can be represented by multiple different multiphase models and tracking oil droplets through liquid oil (for example) would make no sense. This new phase interaction allows Lagrangian droplets to impinge into larger bodies of fluid represented by MMP-LSI. Let’s see this in practice – below we have a fountain where the jet is initially resolved as a free surface (LSI) which then breaks up into Lagrangian droplets. The droplets then impinge into the free surface of the fountain’s reservoir, completing the cycle.
Together these features allow us to simulate applications which contain mixtures or within the framework of hybrid multiphase.
E-Machine cooling – A practical application of the new hybrid multiphase method
Previously no toolset existed that could cover all of these multiphase regimes accurately in a single simulation in an affordable way. The marriage of these complementary technologies allows us to accurately simulate applications where before we had to suffer the inaccuracy caused by assumptions, or the expense of a high level of resolution. With hybrid multiphase we have affordable accuracy at our fingertips.
The time is now right to model the complexity of electric vehicles (and other applications) with hybrid multiphase to gain the edge in performance and gain insights into your designs never before possible.
Let’s put these tools to the test to simulate oil cooling of an e-motor.
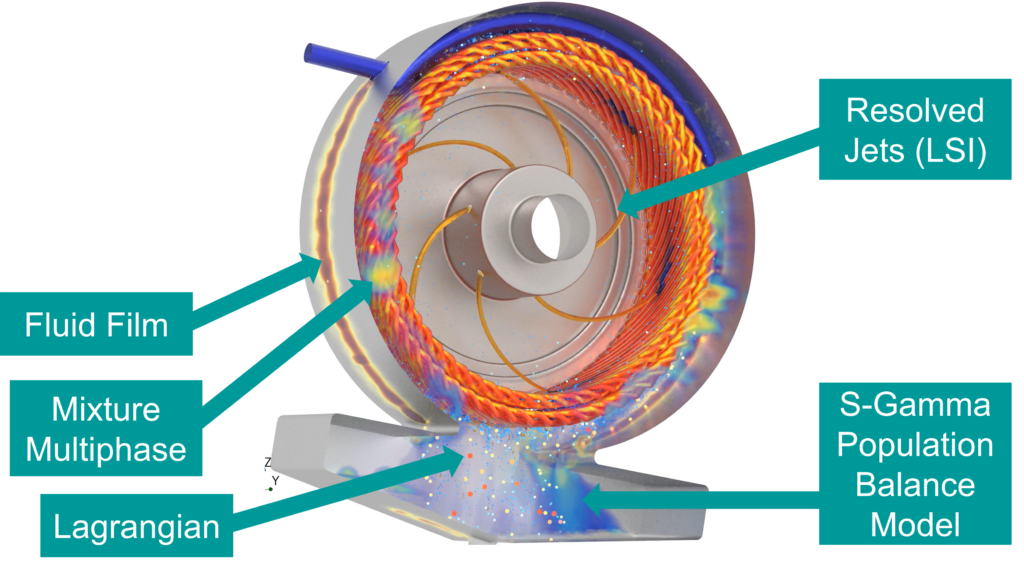
Here we have jets of oil introduced from a rotating shaft which we resolve with adaptive mesh and Large Scale Interfaces (LSI). The jets hit the end-windings cooling them and then break up into droplets. We track these droplets as a Lagrangian phase whilst large enough, but as they break up we convert them into a mixture with droplet population diameter distribution modelled by S-Gamma. Last but not least, we have Fluid Film on the out casing with impingement and stripping between both Lagrangian phase and Mixture Multiphase.
Phew, affordable accuracy! How affordable – this simulation runs on my 12 core laptop! If I want to increase fidelity, I can resolve more with LSI and model less with Lagrangian, Film and MMP mixtures, but however much resolution I chose, I know that appropriate models will be used locally based on my budget of mesh and timestep to give the maximum possible accuracy.
Comments
Leave a Reply
You must be logged in to post a comment.
Hello, could you provide me with the cases of motor cooling published in the start CCM plus 2406 version?