How to use AI to reduce the Parameter ID process from weeks to minutes
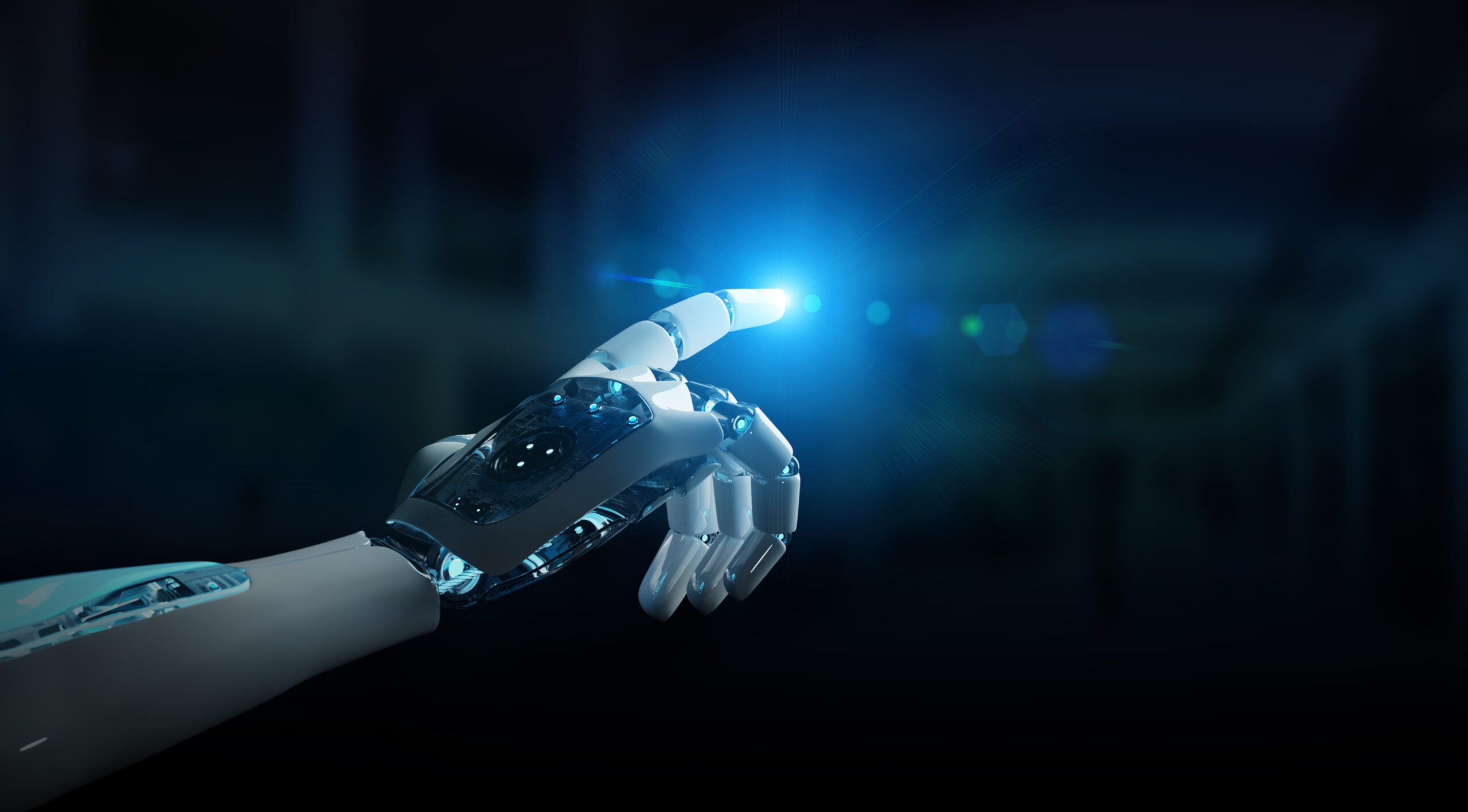
This AI-based parameter ID blog post was co-written with Wouter Vandermeulen, senior project engineer, and Davide Gorgoretti, research engineer, for Simcenter Engineering Services.
The adoption of Digital Twin technology has significantly expanded in recent years. According to Grand View Research, the use of Digital Twins is expected to grow annually by 42.7% from 2021 to 2028.
There are several reasons for this rapid expansion, including the increasing cost of raw material for physical testing, shutdown of physical plants due to COVID-19, and competitive pressure to get products to market faster than ever.
Building an accurate, comprehensive Digital Twin has become one of the main priorities of the mechanical industry. At Siemens, we define a Digital Twin as a virtual counterpart of a real system or process that features all the relevant models and data to mirror its physical twin. These virtual doubles can assist engineers in difficult tasks, such as smart monitoring and predictive maintenance of highly complex systems like industrial plants and fleet vehicles.
The Digital Twin helps engineers in the automotive industry in their decision-making process. It provides a virtual benchmark for evaluating various solutions to meet the desired target performance. As a result, these models must correctly match the behavior of the actual system.
However, building digital models is not exactly a walk in the park.
Your current parameter ID process is outdated. Here’s why.
These virtual models are typically characterized by a vast number of parameters that define the geometry, physical properties, and dynamics of the system. In order to ensure that the Digital Twin will accurately mimic its physical counterpart, all these parameters need to be precisely estimated.
Unfortunately, this parameter ID process is often very tedious and costly. Complex models typically feature dozens of parameters, which require days or even weeks of work to estimate.
For some parameters, engineers must dismantle the system and perform physical tests and measurements on all components. For others, it is necessary to use computationally intensive optimization algorithms. However, each set of physical parameters is specific to the system under test. Therefore, once a new virtual model needs to be identified, the time-consuming parameter optimization process must be repeated from scratch. As a result, parameter identification is a real stumbling block. What if we could also make this process “digital” with Machine Learning?
Machine Learning for parameter ID
Machine Learning is a subfield of Artificial Intelligence (AI) that enables computers to learn difficult tasks and improve with experience without being explicitly programmed. Nowadays, Machine Learning is being employed by the automotive industry for different applications, ranging from Computer Vision and Natural Language Processing and continuing up to anomaly detection and condition monitoring.
Tesla, for example, uses these algorithms for detecting obstacles, road segmentation and controls. Hyundai employs such technology to identify and diagnose auto faults and anomalous sounds.
Machine Learning algorithms can naturally learn complex patterns directly from data and achieve super-human performance in doing so. So how can this help in building Digital Twins?
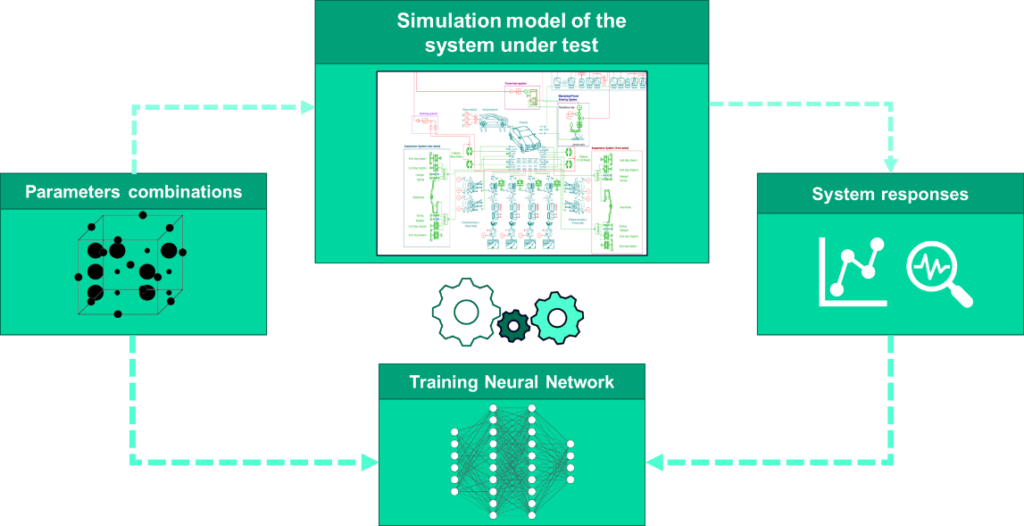
By harnessing massive amounts of simulation data, Machine Learning algorithms can discover hidden relationships between system responses and their physical parameters. As a result, test engineers can be relieved from hours of work spent manufacturing complicated key performance indicators (KPIs) and signal processing routines for highlighting these relations, since the algorithm will be able to figure it out directly from data.
Therefore, it will be sufficient to measure the same responses on the real system and the Machine Learning model will instantaneously and accurately identify the correct parameters configuration without requiring any expensive or intrusive testing procedure. So how does this work? Here is an example.
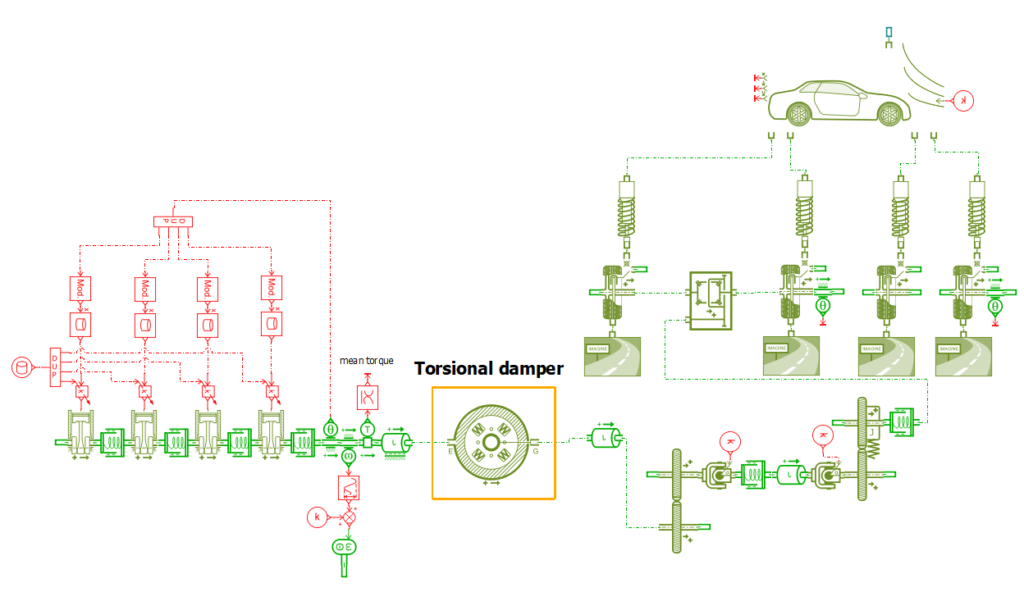
AI-based parameter ID for torsional damper booming analysis
The torsional damper is an essential component for a vehicle driveline. It dampens vibrations from the engine and prevents undesired NVH phenomena, such as booming, which has a negative effect on driver comfort.
However, as a result of the highly nonlinear physics phenomena at play, it is extremely difficult to estimate friction and damping values in the torsional component. The Simcenter Engineering Services team has come up with a solution for this problem: Using simulation data, it is now possible to train a Machine Learning model to identify the exact parameters of the damper from its torsional vibration attenuation.
In order to train the Machine Learning algorithm, the first step is to generate the dataset. This is done by defining an extensive amount of combinations between the parameters of interest, simulating the model for each of them, and retrieving the system responses.
The number of parameter combinations is the result of a trade-off between the total simulation time, which may vary from a couple of hours up to several days, and the desired extent of coverage of the design space. The Machine Learning model is trained to learn the relationship between the responses of the system model and its physical parameters.
The importance of simulation
In order to make everything work, Simcenter’s simulation capabilities are essential. These simulations allow engineers to create many variants of models and calculate them efficiently. While the algorithm learns autonomously, the tasks of selecting parameter ranges, choosing system responses to measure, and designing specific testing boundary conditions are extremely complex, and they require experience and domain knowledge of Simcenter Engineering Services.
Since the dataset is generated using simulation models, the algorithm can be trained before the measurement campaign. Once the component is placed on a test bench, the Machine Learning model will provide the test engineers with an updated model that precisely correlates with the experimental measurements a few seconds after the test:

Why it works
Having an accurate simulation model generated in such a short period of time provides engineers with an essential tool to study the dynamics of the driveline system. This improves engineers’ ability to make accurate predictions and solve potential NVH issues earlier in the development cycle. As a result, OEMs and their suppliers can bring their products to market faster.
The Simcenter Engineering Services team applies this methodology to get an instantaneous identification of driveline components’ parameters. Thanks to these perfectly correlated models, it has been possible to evaluate full vehicle NVH performance in just few minutes after component testing.
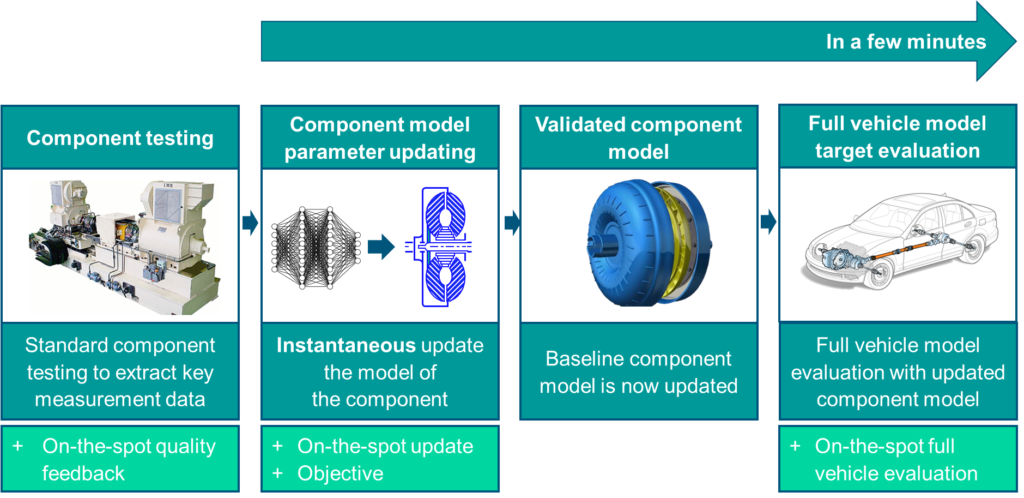
Parameter ID of vehicle models is just one of many examples of how AI can help automotive companies get products to market faster and more efficiently. Having a perfectly validated simulation model is beneficial in several ways:
- It supports design engineers in analysis and improvement of vehicle performance
- It can be employed in a control algorithm for ADAS (advanced driver assistance systems)
- It can be used in virtual sensor framework to predict desired vehicle response and avoid unnecessary sensors
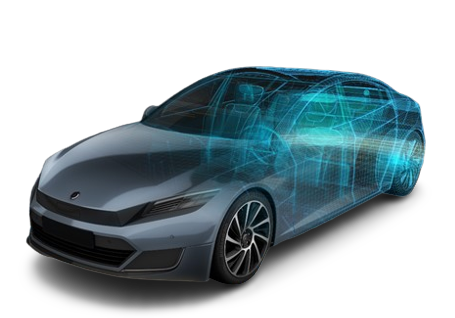
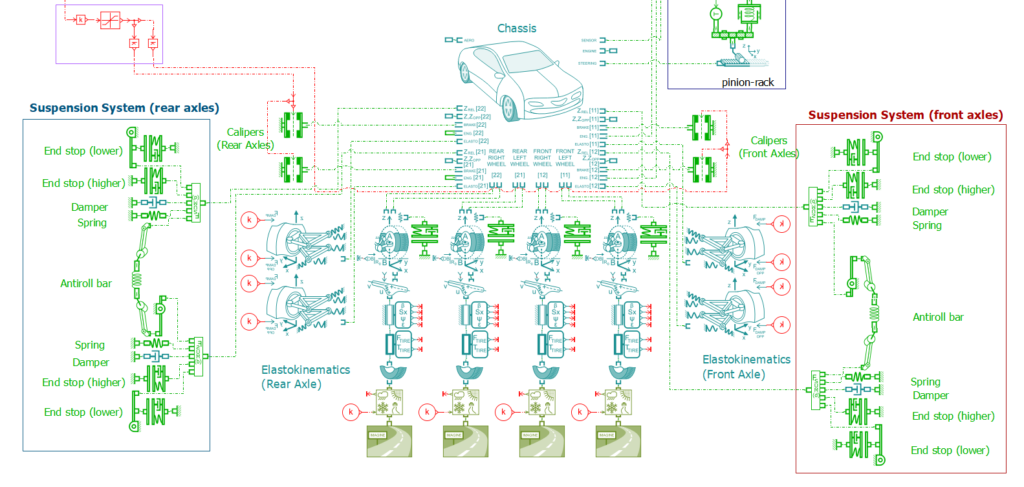
A full vehicle model has hundreds of thousands of parameters that define car geometry, weight, inertia properties, suspension characteristics, and many more. As a car manufacturer, it would be extremely time-consuming and difficult to perform a parameter identification process for every new vehicle model. Using Simcenter Engineering’s AI-based Parameter ID, it is possible to accurately estimate these parameters immediately after the track tests, which significantly reduces the time required. Here’s how it works: