Robots? Not in my backyard!
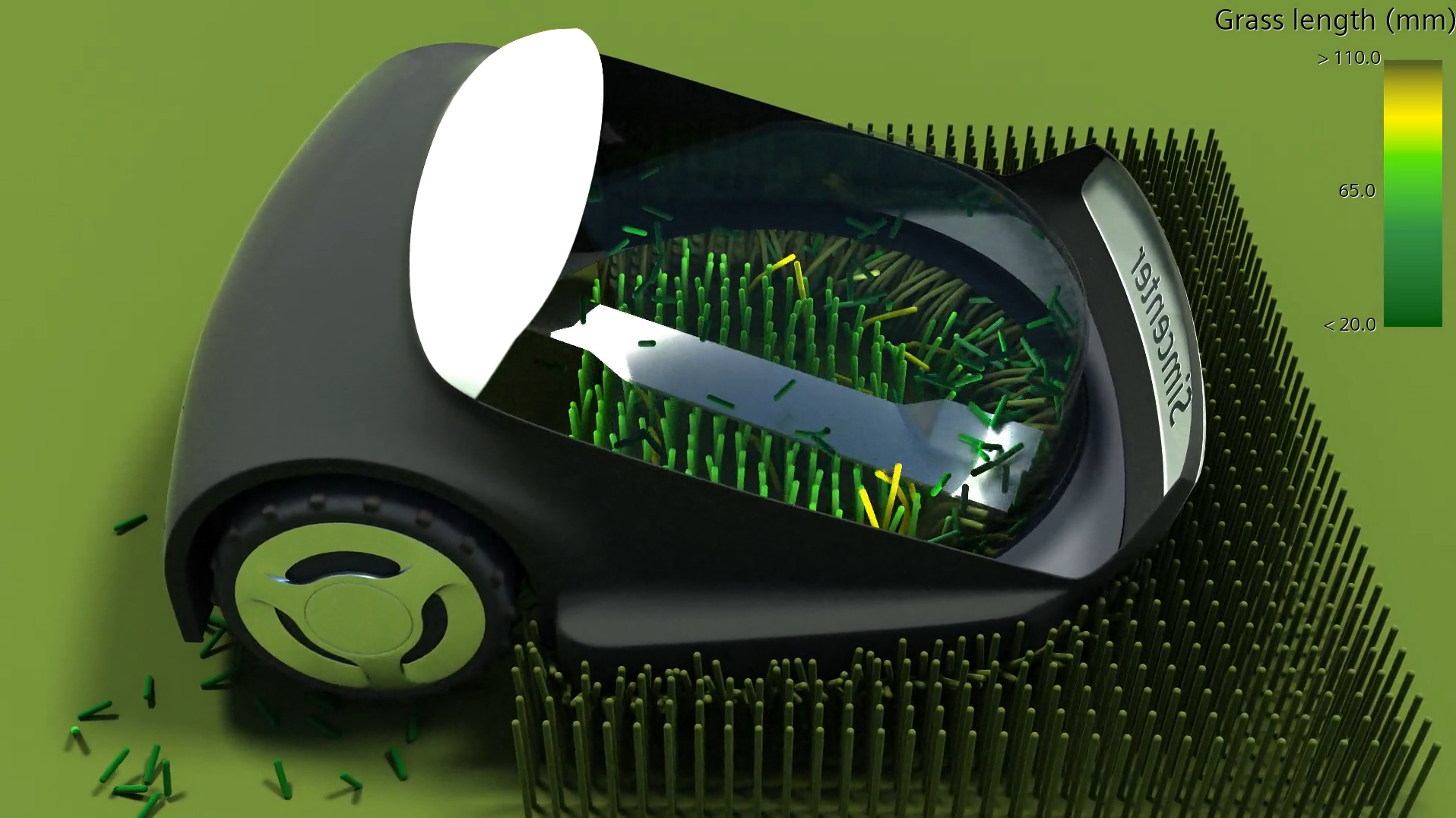
When the time came to recycle my old gasoline-powered lawn mower, I decided it was time to switch to something more environmentally friendly. Although fascinated by the capabilities of robotic mowers, I rejected this option for three reasons:
- My lawn is littered with fallen twigs, pinecones, and leaves in autumn, which creates challenges for robotic mowers.
- The higher cost of the robotic mower compared to other battery-powered lawn mowers.
- I like pushing the lawn mower, and I would miss the activity if I switched to a robotic one.
After careful consideration of the landscape of my yard, my budget, and the type of lawn mower I was looking for, I settled on a traditional manual-push lawn mower with a long-lasting accumulator.
But as I was comparing robotic and manual lawn mowers, I was struck by how much grass-cutting technology has changed over the last century alone. The technological advancements in the last ten years are owed in large part to the exponential growth in computer modelling and the digital twin methods. I hope the trend continues so the robotic lawn mower, more capable and affordable, will be my top choice next time I upgrade.
The demand for fast and accurate DEM simulation
But my lawn – in all honesty – is just a playground. And cutting grass may be considered as cosmetics. However, on a global scale, efficiently cutting organic material is critical to feed billions of people. Today, agricultural equipment manufacturers need to make better and faster design and manufacturing decisions in order to meet the demands of feeding the world sustainably.
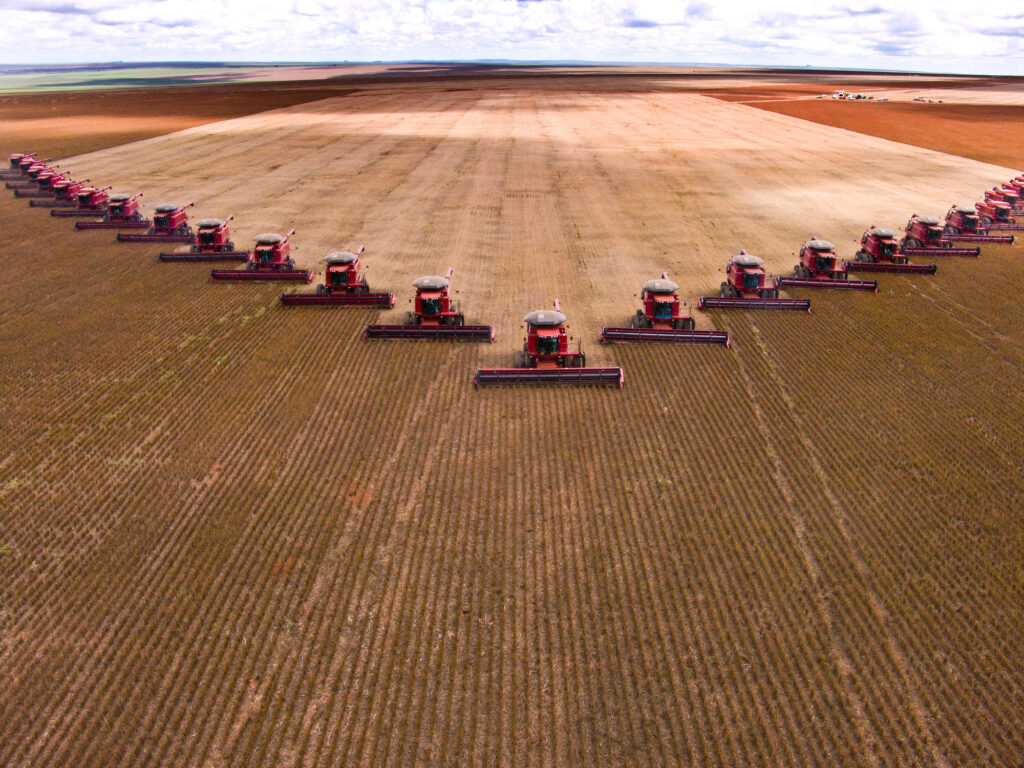
But, before we go big, let me start in my own backyard. So, how do you optimize the grass-cutting process without endless trial and error (I only have one lawn and one new mower)?
The key is DEM simulation.
Grass and any kind of crop can be treated as particles connected to the ground. Each grass blade is modelled separately using the Discrete Element Method (DEM simulation). They yield when applied defined stress – which results from the impact of a rigid body moving; in this case, the mower blade. After being cut off, the grass blades. or any other organic fibre, behave like bulk material – another typical use case for DEM simulation! That way, engineers can even optimize the mower blade to counter the wear of millions of grass blades – or to withstand tons of pinecones lying on the lawn.
To overcome the challenge of designing better agricultural and process engineering products in shorter development cycles several capabilities are required for improving computational time and accuracy of particle simulations. Engineers need to leverage the following features to improve the speed of DEM simulation while maintaining sufficient accuracy:
- A Meshfree DEM simulation workflow for applications where the coupling between particle flow and fluid flow can be neglected.
- A Flexible Fiber model with improved fiber particles constructed by connecting a number of identical cylinders, bonded end to end. This solution is computationally more efficient, for bending and axial stiffness of fibers, than modeling fibers using the Particle Clumps model. In the traditional Particle Clumps model, one grass blade particle was defined as an assembly of spheres connected through bonds, and thus need more elements to model the same length grass blade.
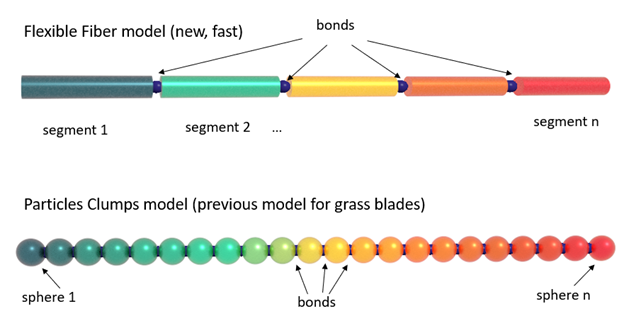
- A Flexible Fiber model that is compatible with Meshfree DEM simulation workflow. The benefits of the Meshfree DEM simulation, such as simplified workflow and faster simulation for applications with the complex motion of parts, apply also to simulations with flexible fibers.
- An essential feature for lawn mowing is that fibers actually break. Common breakage models for particle clumps like the Simple Failure model and the Constant Rate Damage model need to be applied to cylinder-cylinder bonds as well.
The exciting news is, that Simcenter STAR-CCM+, as a multiphysics CFD solution offers all these DEM simulation capabilities and features today. However, there was still one remaining inherent issue with the fibers in meshless domains…
Grass swaying stops without the wind
I grew up in the city but, as a kid, I spent many summers out in the countryside with my grandmother who lived in a small farming village. Something that fascinated me, every time I came to visit, was the way people cut grass with scythes. Although I do like a bit of manual effort, that is too much hard work for me.
Still, there was something so hypnotic about watching as uncles and older cousins took to swinging their curved steel blades at the vast, overgrown fields. All around them, the tall grass would billow in the wind which reminded me of rolling waves in the ocean. But as my family worked through the field, using rakes to push the cut grass into the heaps, the waves would disappear. The tall grass turned into short grass, and the rolling effect would stop.
Long blades short – in Meshless DEM simulation without coupling to Computational Fluid Dynamics (CFD) there is simply no physical effect to stop the blade from swinging. No air drag dampens the movement – as it does in the real world. When I used DEM simulation to optimize grass cutting, I found myself paying attention to the way flexible fibers, representing tall grass, oscillate. The latest Simcenter STAR-CCM+ release 2210 can now capture the effect of the velocity damping in oscillating fibers. And hence adds the one missing piece to the puzzle of realistic fibre motion and cropping physics.
The video above illustrates the difference between fibers without and with damping. The DEM fibers are attached to the horizontal plate and subjected to the initial deformation. The simulation was done using the Meshfree DEM simulation workflow, which implies no coupling to a CFD. As no fluid is simulated, there is no medium inducing drag on the fibers. The plot for the maximum fiber segment velocity as a function of time confirms the unattenuated swaying of fibers without damping physics. The yellow case with damping physics shows an overall reduction of the velocity with time.
It also shows that higher-order harmonic vibrations of fiber segments exist in the case without damping, but it is eliminated in the case with damping. These results mean, not only more accurate behavior of fibers with damping, by reproducing the real effect of oscillation energy dissipation through internal friction. This also more stabilizes DEM
simulations with an effective mechanism for preventing the relative displacement of segment ends at each bond between segments.
The video below shows the results of using the new fiber-damping physics when simulating the robotic mower in action.
Measure, Analyse, Improve!
In the 2210 release, Simcenter STAR-CCM+ offers new DEM Force and DEM moment reports. Every fiber impact causes a counter-torque on the cutting blade. Engineers can evaluate that to determine power consumption. This new way of postprocessing the particle-wall interactions is easy to set up and provides accurate force results. This is realized by accounting for all particle-boundary collisions during the time interval larger than DEM simulation timestep. Here is the result for torque on the rotating blade obtained:
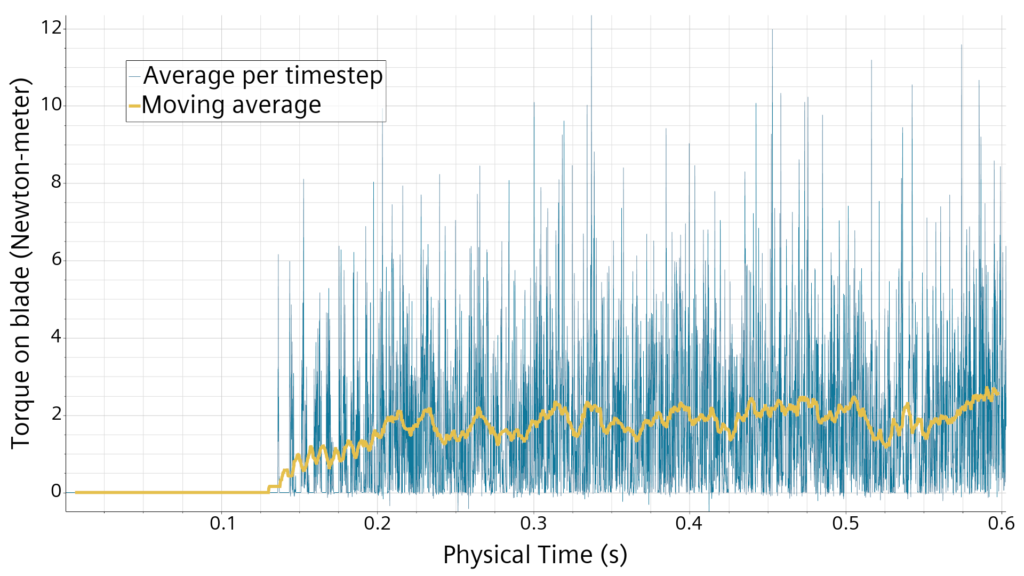
The blue-colored curve indicates the torque on the blade over the time scale defined by the motion solver, 1.0E-4 s in this example. These results are expectedly noisy reflecting the discrete nature of particle-wall collisions. The moving average over the time scale of 100 motion solver timesteps is shown by the yellow curve.
The Robots are Coming. Resistance is futile.
In retrospect, I realize I was also resisting change when I made the decision not to purchase a robotic lawn mower. But resistance is often just the first step to change. I am optimistic about the next generation of robotic mowers. As gardening equipment manufacturers deploy Simcenter STAR-CCM+ 2210, out on October 25, robot mowers might be fit to rip through my pinecone-covered backyard – one day! Pinecones might even be the perfect use case either for polyhedral particles or breakable particle clumps. A “pinecone safe” label on the next mower generation might be the unique selling point that will convince me.
To overcome my second reason against robots, designers will surely find a way to reduce the costs of the next generation by reducing the amount of physical prototype testing. In addition, I might also more readily accept the higher cost of the robotic mower – knowing the benefit of “More time for myself and new DEM simulation features” is guaranteed.
All in all, my resistance seems futile. Robots are coming … even in my backyard!
Discrete Element Method and beyond, Simcenter for the agricultural industry
And for those that have to solve a way bigger problem than cutting some grass in their backyards, Simcenter offers all the capabilities to not just efficiently optimize harvesting processes but to holistically develop productive and reliable farming machines.
At the same time with the Discrete Element Method we do not stop at the agricultural industry! Watch this Simcenter Snippet video to learn more about the capabilities of fully embedded DEM simulation in Simcenter STAR-CCM+.
Comments
Comments are closed.
Nonsense. Present reality.