Clearing the path to innovation through next generation parallel polyhedral mesher
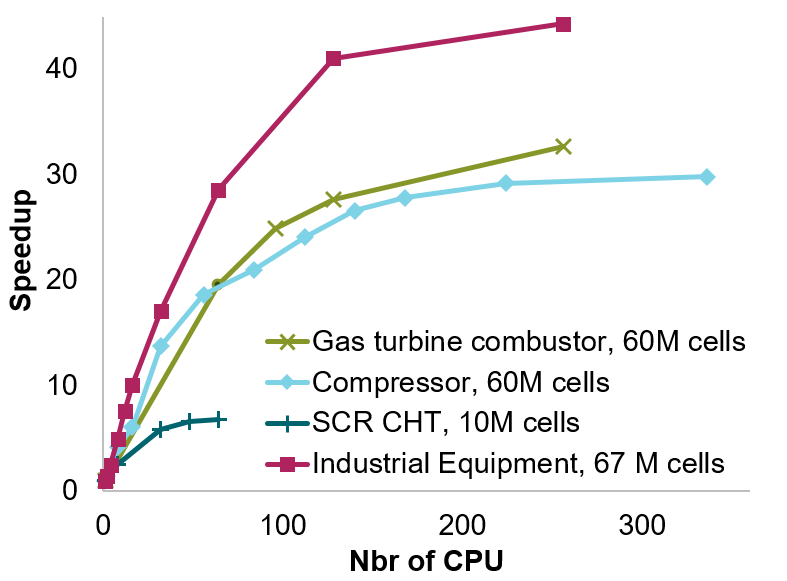
I see the high-fidelity simulations as a way to stay ahead of the demands we know are coming
Zach Hazhen, Martin UAV (see this video)
This quote neatly describes the true value of simulations. To stay ahead of industry trends and competition you need to innovate. To innovate, you need to quickly evaluate 100s of designs, focusing in on the best one, much like ADIADA did when they achieved a record low drag count for an electric SUV through running 600 aerodynamics simulations in Simcenter STAR-CCM+. They managed to reduce the drag by 55 drag counts virtually, prior to building one single prototype!
This type of innovation is only possible if you can obtain high fidelity results quickly. One large component of the simulation turnaround time is the CPU time. The Simcenter STAR-CCM+ solver is very scalable, nicely demonstrated by the almost perfect scaling to 50 000 cores for gas turbine combustion here. This means you can get your high-fidelity results in minutes if you use enough cores. But solver time is not all that needs to be considered; solving today’s complex engineering problems often requires very large meshes. This in turn means long meshing times, and when done in serial, this can take even more time than the parallel solution time, slowing down your path to innovation…
Automated generation of high quality polyhedral meshes has been a key differentiator for Simcenter STAR-CCM+ for 14 years, relieving you of the burden to handcraft meshes. With the next generation parallel polyhedral mesher in Simcenter STAR-CCM+ 2020.1 you can create high-quality industrial all-polyhedral meshes with prism layers faster than ever before!
Speed
See the charts below for polyhedral meshing scalability for a set of industrial cases in Simcenter STAR-CCM+ 2020.1. All meshes produced are high-quality all-polyhedral with prism layers. 60-70M cells cases now scale up to 30-45x faster, with the current record being 44x faster on 256 cores for a 67M cell industrial equipment mesh. For this case 6.2M cells are created every minute, which means the full 67M cell high quality, industrial, all-polyhedral mesh with prism layers, is created in less than 11 minutes! About the time you need to get a nice cup of coffee…
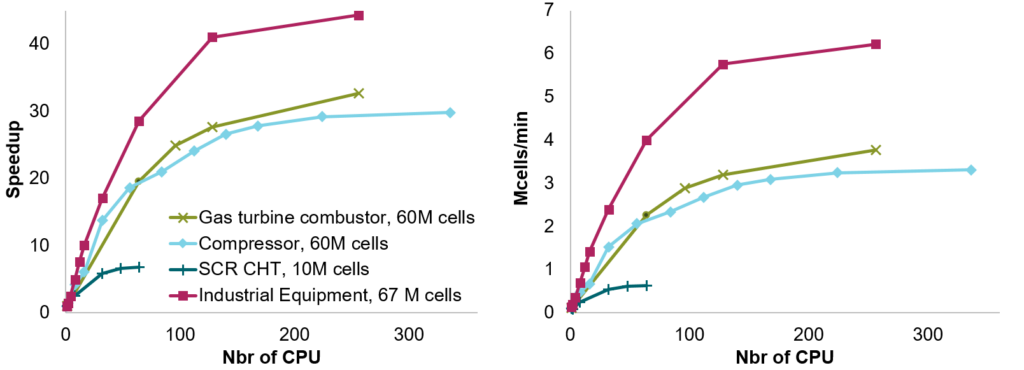
Consistency
Mesh consistency across core counts is key to be able to trust your simulation results. If your simulation results depend on the number of cores you meshed on, you cannot trust them. Therefore, intense focus has been put on ensuring mesh equivalence across core counts, and you can trust that the mesh you create on 32 / 128 / 256 / … cores is very similar to the mesh you would create in serial. This is demonstrated by the following: In a set of 17 industrial cases, 13 of them showed a total cell count difference less than 0.1% across a wide range of core counts, comparing to the cell count produced in serial. The remaining cases showed a cell count change less than 0.9%.
See an example of mesh similarity for aerodynamics simulation of a helicopter below. Note the very similar cell volume distribution in serial versus 128 cores, indicated by the pictures as well as the histograms.
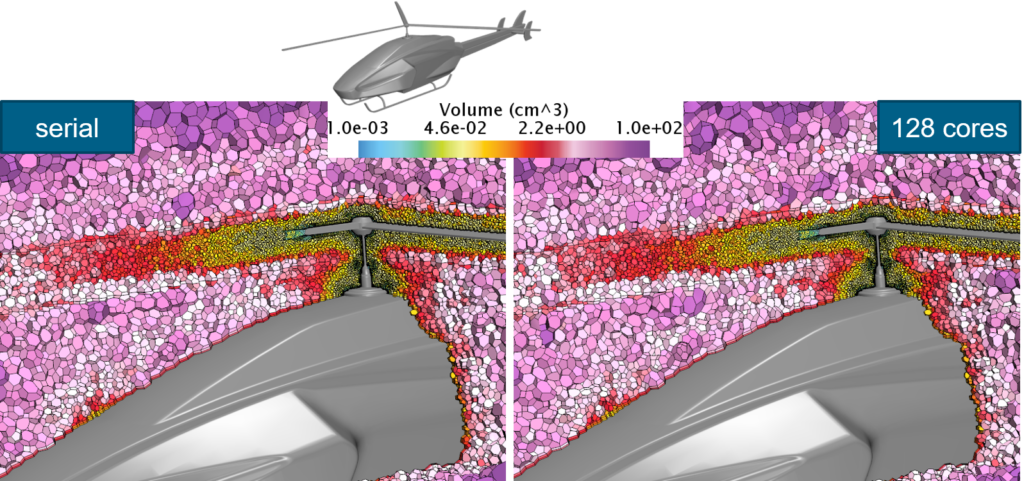
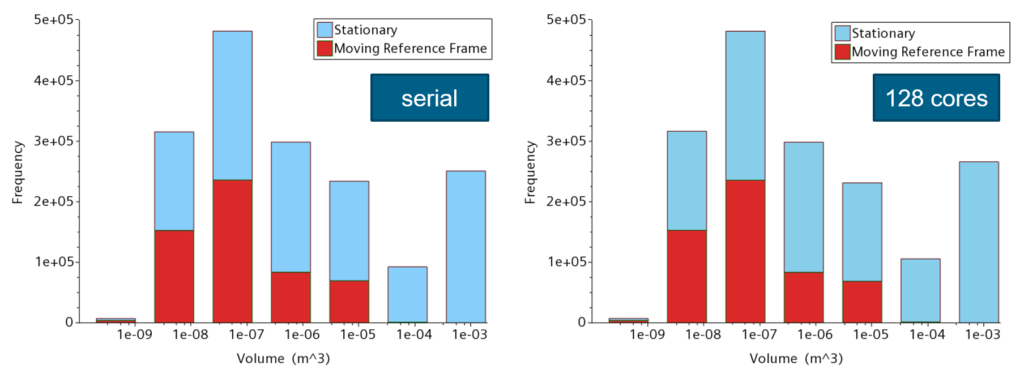
Quality & ease-of-use
Finally, if you are an existing Simcenter STAR-CCM+ user, you will among other things benefit from a smoother, easier to control and more predictable volume growth rate than before in the new mesher. See an example below, where a very smooth growth rate is observed for an underhood flow simulation.
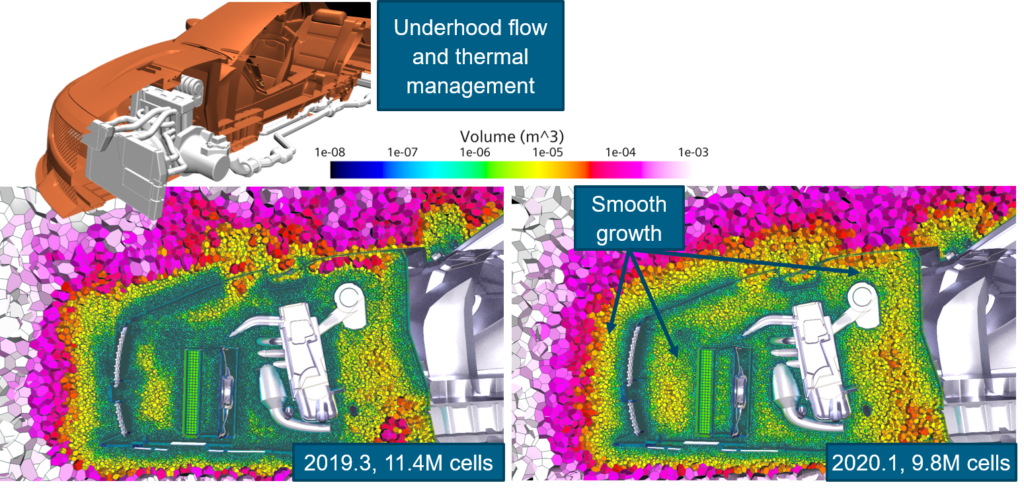
The improved growth rate will often result in a lower cell count than in previous versions, and consequently shorter solver CPU time. See an example of a packed bed reactor below, where the new mesher allows reducing the total cell count from 20 to 16M cells, since it provides a better growth inside the particles, where heat transfer is calculated. This makes the simulation 1.1x faster.
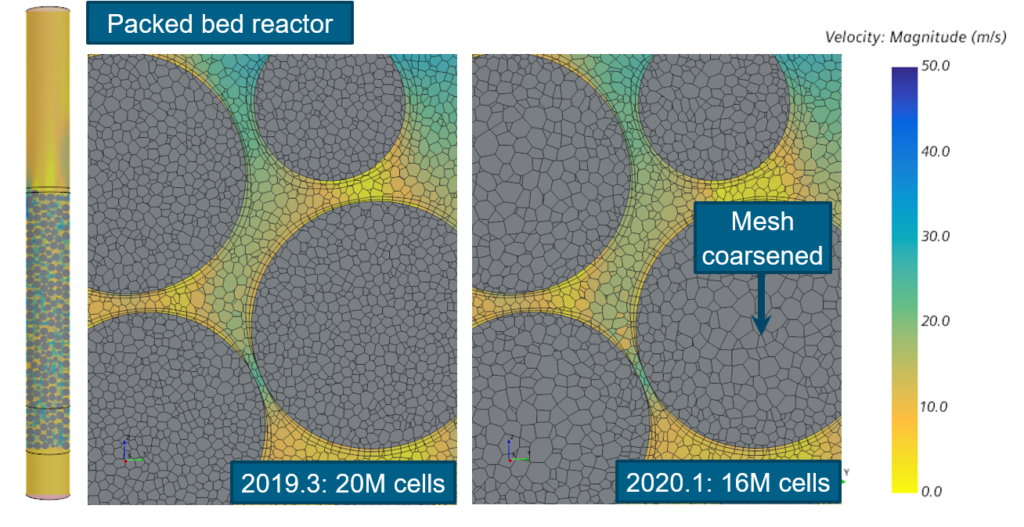
To make your life easier when preparing your mesh, the growth rate from any refinement, such as volume refinement or wake refinement, as well as from surfaces is now controlled using one single parameter. Less clicks, less confusion, less hassle.
To give you a better comprehension of the meshes you can expect to produce in record time, please see the animations below. In the sweep through the simplified underhood geometry, you clearly see the smooth growth throughout the cavities.
The animation below shows vorticity in a mixing vessel. Note the smooth transition between the rotating interface and the surrounding mesh, as well as from shaft and impellers to the core mesh.
All in all, now you can use the award-winning1 Simcenter STAR-CCM+ polyhedral mesher to generate very high-quality 60M+ cells meshes for complex models in as little as 10-20 minutes! Utilize this to stay ahead of the demands you know are coming!
ps. Perhaps you can combine this with model-driven Adaptive Mesh Refinement to get even shorter turnaround times?!
1Simcenter STAR-CCM+ won the prestigious “Meshing Maestro Award” at the International Meshing Roundtable for two years in a row (2017-2018). Last year we came 2nd, after our great colleagues in Simcenter 3D.
Comments
Comments are closed.
That’s good work. Does thin mesher support parallel meshing now? If not, then is the parallel support for thin mesher development in the pipe line and when can we expect it? Thanks.