Peristaltic pump FSI simulation for safer dialysis – Trustworthy from concept to care
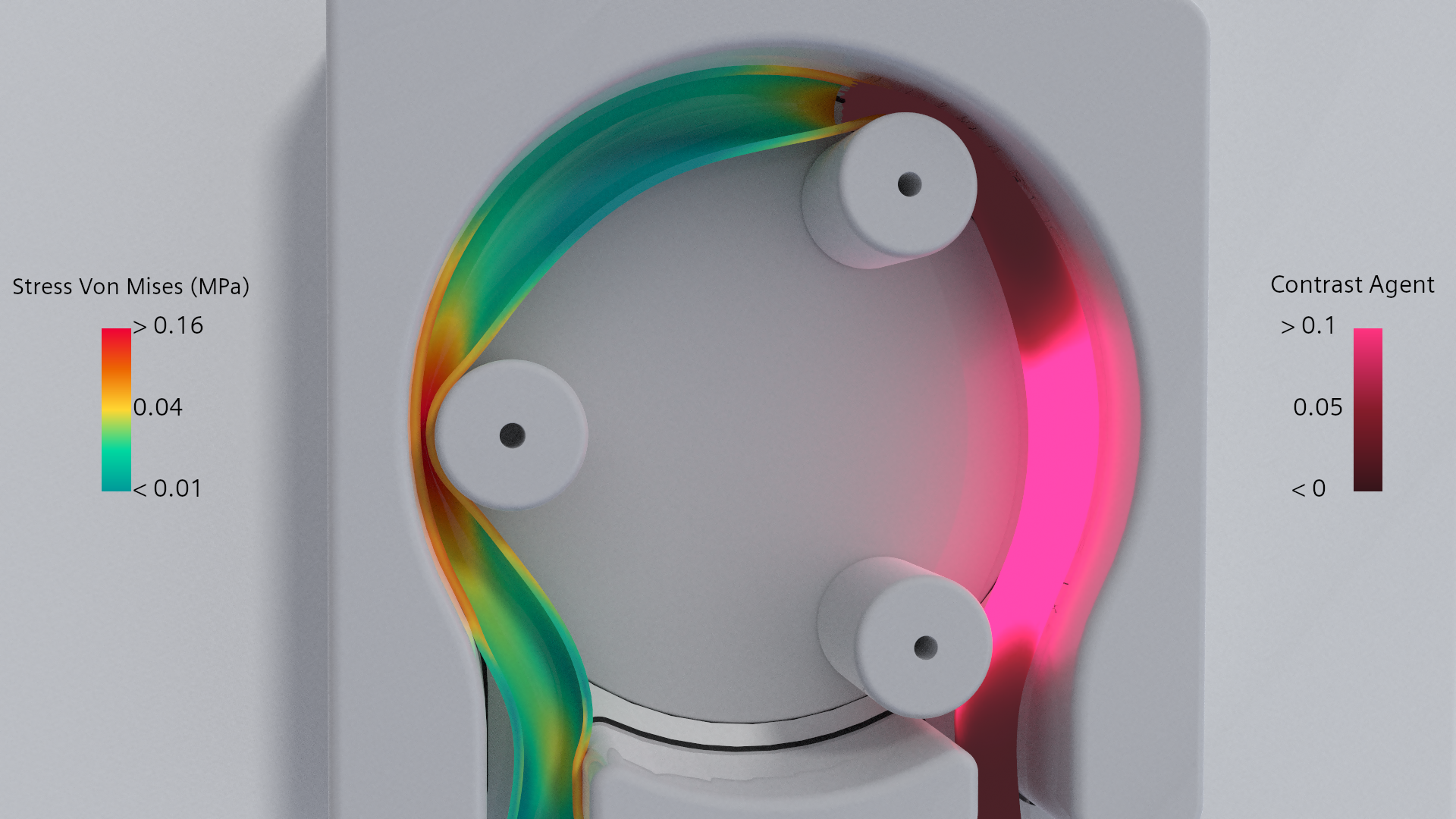
Hardware is hard
Silicon Valley Saying
goes a saying in the Silicon Valley. Let me add this: life-saving hardware, is even harder. Despite all great medical technology humans invented, to date the kidney is the only organ that we have managed to replace permanently with a machine. And while hemodialysis is already a great success and a lifesaver, each session lasts up to four hours, three times a week, for many years, placing a significant burden on patients’ life and safety.
That said, I wanted to explore if I could use the new structural modelling capabilities which are accessible through Simcenter STAR-CCM+, to help to help improve blood pump design, making dialysis machines safer and treatments less stressful for each patient. Read on to discover how some of our new features in our Simcenter STAR-CCM+ 2406 release, along with its best-in-class fluid-structure interaction simulation capabilities, helped me achieve this goal.
Perfecting hemodialysis
Approximately 3 million people worldwide receive hemodialysis treatment, resulting in about 1.3 million treatments per day. While generally regarded as a safe procedure, malfunctioning or improper handling of dialysis machines can lead to serious harm to patients, posing a long-lasting, constant risk to their health.
Many injuries or complications are linked to incorrect blood mass flow, where too little or too much blood is drawn from the patient, making the treatment ineffective or causing the patient pain or even making them faint during treatment.
The blood flow rate is specifically tailored to each patient’s need, considering factors like weight, size, blood pressure and viscosity, and overall health.
Blood circulation from the patient to the dialyzer is managed by a roller pump, a type of peristaltic pump that uses rollers to compress and release a flexible tube to move the blood through the tube. The blood flow rate created by the pump varies with the material, length and size of the tubing as well as the quality and type of the vascular access. Proper occlusion, ensuring the tubing is fully compressed by the rollers, is also essential to move the correct volume of blood without slippage. It is crucial to consider all these factors in the pump’s design process, validating it against a wide range of scenarios to ensure optimal blood mass flow and safety for each patient.
Dialysis Machine. Source: NAGWA
In my mind, a simulation setup with fluid-structure coupling is the ideal tool to manage this intricate mix of mechanical, physical and patient-specific factors and to ensure that the design works well in any situation.
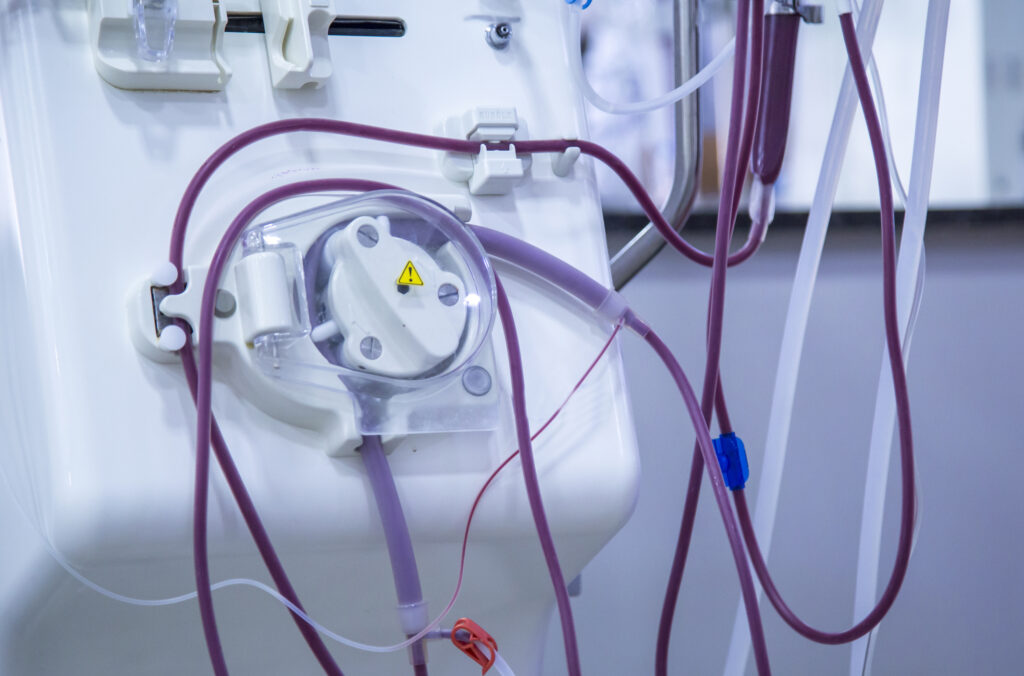
The challenges of peristaltic pump FSI simulation
Simulating peristaltic pumps by including both the fluid and solid domains in one simulation set-up offers significant advantages. This integrated approach makes it easy to not only see how changes in tube thickness affect strain in the tube, but also how these changes, in turn, influence blood pressure and mass flow.
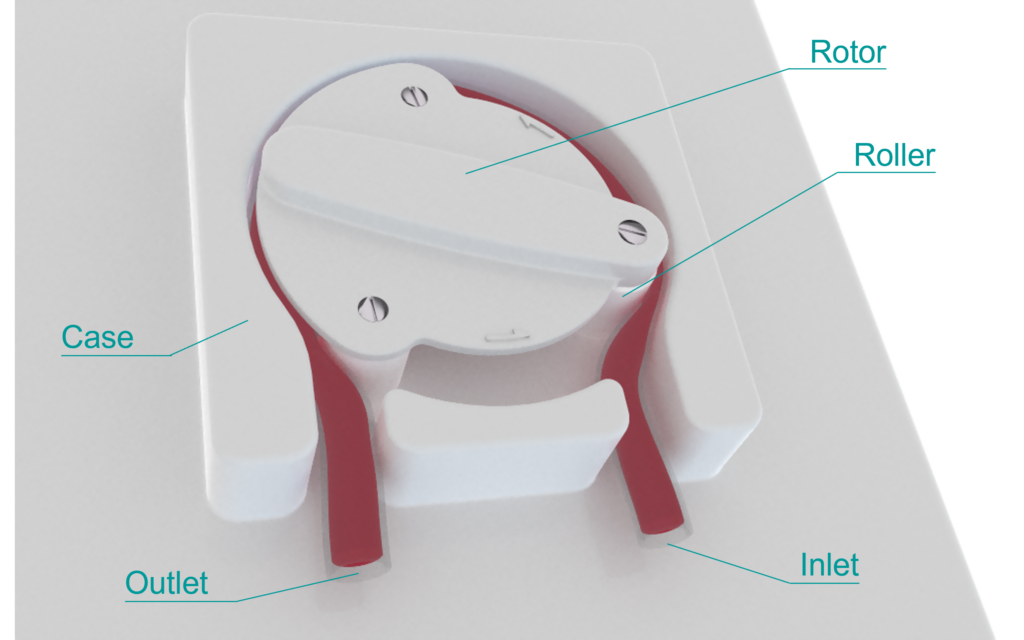
However, simulating peristaltic pumps is more complex than it appears. The significant fluid-structure interaction (FSI) means that the deformation of the tubing impacts fluid flow and vice versa. This requires a tight two-way coupling of fluid dynamics and structural mechanics. The flexible tubing exhibits non-linear behavior due to large deformations and contact.
The peristaltic motion involves continuously moving boundaries as the rollers compress and release the tubing. Accurately capturing these moving boundaries in simulations is challenging and requires advanced mesh evolution techniques and dynamic stabilization methods. The pumping action relies on the rollers pinching the tube against the casing, making accurate modeling of the contact between the roller, casing, and flexible tube crucial. Incorrect contact modeling can lead to inaccurate predictions of the tube’s cross-sections, pump pressures, and flow rates.
Fortunately, Simcenter provides all the tools needed to perform high-fidelity two-way coupled FSI simulations and predict the behavior of peristaltic pumps in various scenarios. And with the mechanical technology embedded in the Simcenter STAR-CCM+ 2406 release, contact modeling has become easier and more accurate, even for the most complex applications.
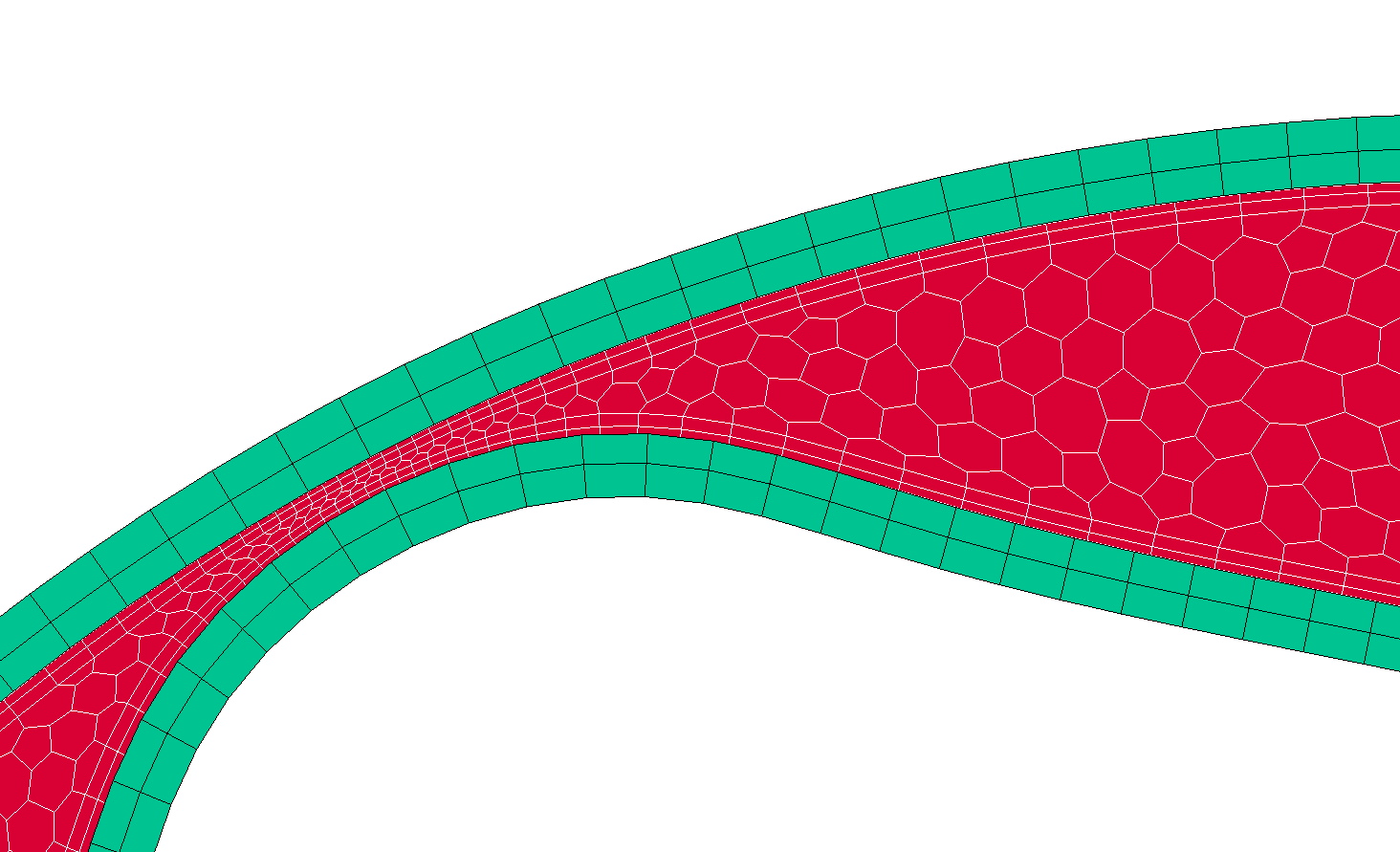
Difficulties of contact modelling
Contact modelling is essential in structural mechanics, but no algorithm exists that efficiently solves all types of contact problems. The optimal solution depends on the type of contact and the required accuracy and robustness.
The structural solver uses the Penalty Method for contact enforcement. This method relies heavily on a user-defined penalty parameter, which controls the contact stiffness, or the pressure generated by contact penetration. While a high penalty parameter can yield precise contact resolution, it also decreases the simulation’s robustness and speed.
Selecting an optimal penalty parameter is particularly difficult for dynamic problems with significant contact changes, such as in this peristaltic pump simulation. The interactions between the blood, the flexible tubing and the rollers that repeatedly go in and out of contact, lead to dynamic changes in contact forces and fluid pressure. A static penalty parameter will cause varying penetration between the tube and the rotor, affecting the fluid cross-section and flow rate. This variability results in inaccurate predictions of the pump’s outlet mass flow rate and poses a challenge to straight-forward peristaltic pump FSI simulation.
The image below shows how different penalty parameters cause variations in the penetration, altering the occlusion of the flexible tube. The graph underneath shows the outlet mass flows resulting from the variations in occlusion and gives an idea of how important correct contact modelling is for the correct simulation of a peristaltic pump.
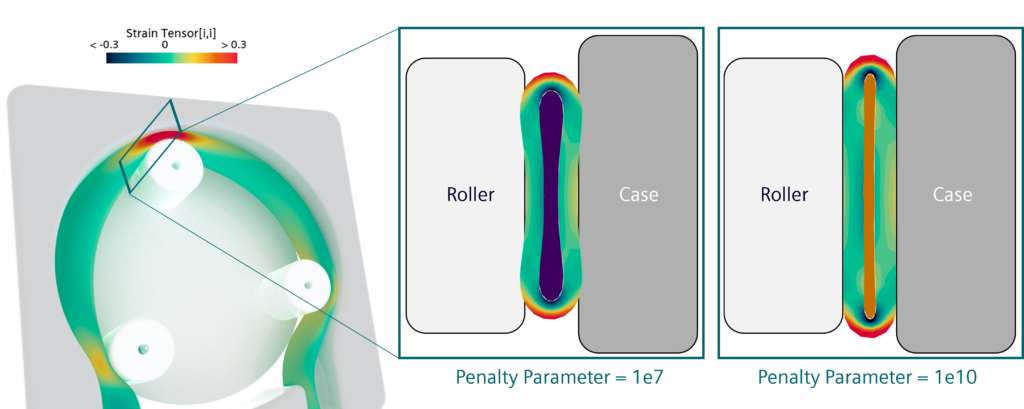

Advanced contact modelling with the Uzawa algorithm
To address the limitations of the Penalty Method, the structural solver now introduces a new contact modeling approach that combines the benefits of the Penalty Method and the very exact but computationally costly Lagrange Multiplier method. This approach is based on the iterative solution of the Augmented Lagrange Method (ALM) using the Uzawa algorithm.
ALM includes an additional augmentation loop in each iteration, updating the contact pressure until the specified contact constraint accuracy is achieved. While the convergence speed of each augmentation still depends on the chosen penalty parameter, the final contact constraint accuracy does not, making it easier for users to control the allowed contact penetration precisely.

With the Uzawa algorithm, contact penetration can be limited to a specific value, ensuring the desired accuracy. The figure above demonstrates how this method effectively maintains contact penetration below levels achieved with a high penalty value, further improving the accuracy of mass flow predictions. This approach eliminates the need for extensive fine-tuning of the penalty parameter and at the same time decreases simulation time by 6%, saving both time and computational resources.
Beyond hemodialysis
With the new advanced contact modelling methods in the structural solver, together with the best-in-class fluid-structure-interaction simulation capabilities of Simcenter STAR-CCM+, designing reliable and efficient peristaltic pumps has never been more achievable.
I am convinced that these simulations will help us ensure that every aspect of a pump’s performance is optimized, leading to safer and more effective treatments for patients. Also beyond hemodialysis, peristaltic pumps play a crucial role in various other applications, from chemical processing to food and beverage manufacturing, where precise fluid handling is essential.
Stay tuned as we continue to refine and grow our FSI simulation capabilities and keep pushing the boundaries for more and more complex applications. And don’t forget to download Simcenter STAR-CCM+ 2406, for precise contact modeling with ease.
Literature:
https://www.sciencedirect.com/science/article/abs/pii/S0924424721001710
https://www.sciencedirect.com/science/article/abs/pii/S0010482523003074
https://www.sciencedirect.com/sdfe/pdf/download/eid/3-s2.0-B9780080877808000723/first-page-pdf