Designing For Speed using NX CAD
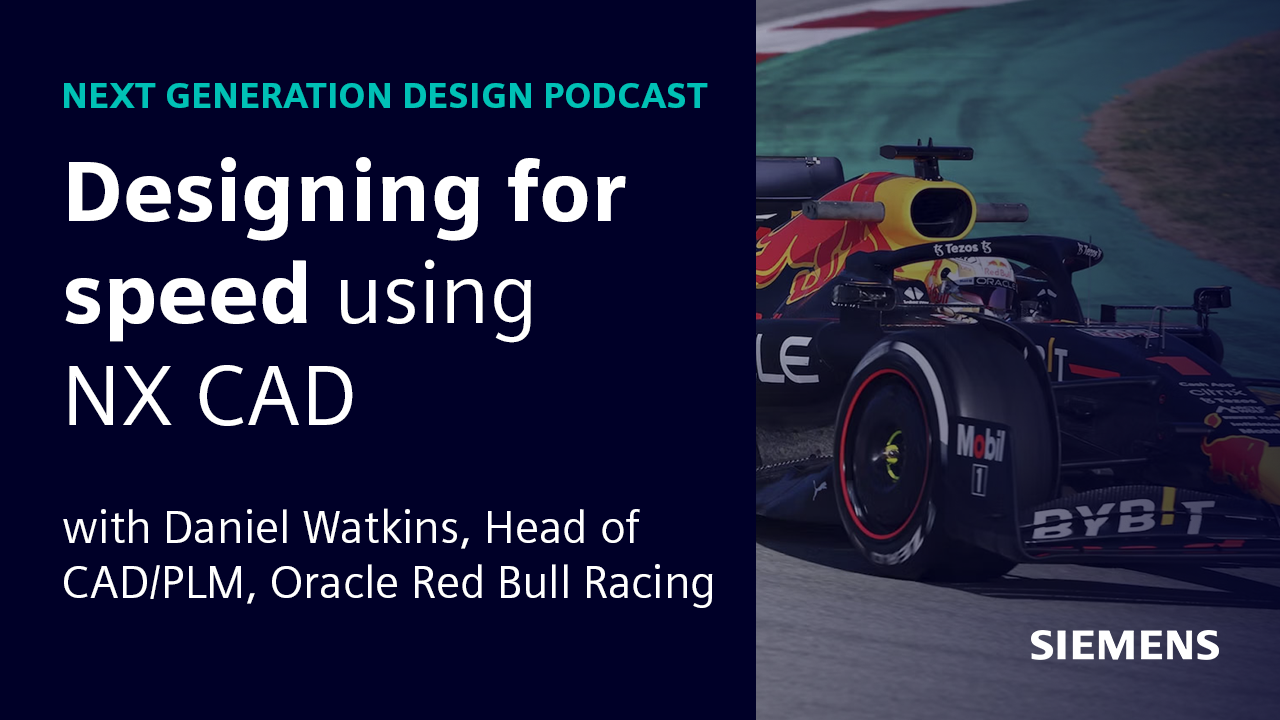
Building an efficient and fast car starts in the design phase. That is why companies make tremendous investments in building a talented design team and equipping them with the best design tools. One organization that has mastered the art of using digital tools to design, test, and validate models is the Oracle Red Bull Racing, 2022’s World Constructors’ Championship and World Drivers’ Championship winners.
On this episode of the Next Generation Design podcast, our host Jennifer Piper is joined by Daniel Watkins, Head of CAD and PLM at Oracle Red Bull Racing. He’ll help us understand the process of designing a championship-worthy Formula 1 car. He’ll also help us understand the role that is played by digital tools such as Siemens’ NX in the design process.
In this episode, you’ll learn why the Oracle Red Bull racing team relies so much on Siemens’ NX and their biggest challenges in designing and improving their car. Additionally, Daniel will dispel a common myth regarding how cars and drivers are managed.
What You’ll Learn in this Episode:
- The steps involved in designing the Oracle Red Bull F1 car
- The suite of Siemens tools the team uses in the design process
- The role played by the digital twin in a car’s design process
- The biggest challenges when designing a F1 car
- The driver’s contribution to the car’s design
We have a digital process that runs from concept to track, and that process relies on that digital twin of the car. So, we 100% model and design everything in CAD.
– Daniel Watkins, Oracle Red Bull Racing
Listen to the Next Generation Design podcast wherever you do podcasts.
Connect with Daniel Watkins:
Connect with Jennifer Piper:
Listen to or read the next episode of the Next Generation Design podcast: The Magic of Software as a Service (SaaS)
Listen to or read the previous episode of the Next Generation Design podcast: The Benefits of Modular Construction
Podcast Transcript
Daniel Watkins: The amount of change that we can push through the business really tallies with the amount of points we can gain. So, we know that if we need to be winning championships or winning races, we need to be able to push change through the business in order to be competitive and be at the sharp end of the race results. So, having the openness of architecture and the ability to customize where we need to is really important because as an F1 team, you can’t go and buy F1-specific things off the shelf — they don’t exist.
Jennifer Piper: Welcome to season three of the Next Generation Design podcast. I’m your host, Jennifer Piper. Today, we’re discussing the ins and outs of the design process at Oracle Red Bull Racing. In this episode, I welcome the head of CAD and PLM at Oracle Red Bull Racing. He tells me about the changes he’s seen in their process over the last decade, the importance that software flexibility has in their success, and he’s dispelling a prevalent myth about Formula One.
Jennifer Piper: Before we begin, let’s meet today’s guest, Daniel Watkins. Dan, can you tell our listeners a little bit about yourself?
Daniel Watkins: Hi, Jen. My name is Daniel Watkins. I am the Head of CAD and PLM at Oracle Red Bull Racing. I’ve been working here for the last 10 years.
Jennifer Piper: Thanks so much for joining us today and welcome to the podcast. Can you tell our audience a little about the background of the Oracle Red Bull Racing team?
Daniel Watkins: The Oracle Red Bull Racing team has been here for about 18 years, and we’ve been partners with Siemens for the entire time. In fact, we were partners with Siemens before we were Red Bull. So, prior to being Oracle Red Bull Racing, we were Jaguar Racing, and before that, Stewart Grand Prix. Siemens was a part of that journey, too. We’re based at Milton Keynes in the UK, wholly based here, with the exception of the fact that we have a wind tunnel about 30 miles away from this site here in a place called Bedford. The main campus here in Milton Keynes holds around 800 staff that work to deliver our car to our two drivers. That’s increasing now because we’re deciding to get into the development of Formula One engines or power units, so that number is going to increase over the next few years as we stand up a new business unit to support that activity.
Jennifer Piper: As you said, you’ve been with the team for the last decade. How have you seen things change in that span of time for the team?
Daniel Watkins: I’ve seen a fair amount of change in that time; the team has been winning; the team has been not winning. Throughout that time, we’ve been partnering with Siemens and using the technology that you guys provide to us to help us get onto the top step of the podium again, which is what we did in the last season.
Jennifer Piper: That’s wonderful to hear. Now, I’d like to jump right into the fun part of your job. What can you tell us about the design process? Where does it all start?
Daniel Watkins: Our design process is, effectively, an iterative loop. We start with a concept, normally, from an aerodynamic perspective. So, that’s probably the most common entry point. And we take that concept from a CAD perspective, and we mock up multiple flavors or variations of that concept. And we do that digitally using the Siemens toolset; NX is the CAD tool that we use.
Jennifer Piper: And what comes next in the process? What are you looking for at this point in the design?
Daniel Watkins: We take the concepts that we come up with from an aero perspective, and we virtually validate those to see which ones will likely yield the best performance, and we use that in a CFD process – Computational Fluid Dynamics – so, a validation of those design concepts. We’ve got a loop in that process that allows us to push 3D models from NX into our CFD process, and that runs on supercomputers. And then we analyze the output, and the best ideas, based on the results that we get, we then take forward to the next stage in our process, which will either be a wind tunnel where we start manufacturing parts at scale — so, we have a 60% scale model of the car that runs in the wind tunnel talked about earlier that’s over in Bedford. And there we analyze those results to see if they correlate with what we find in CFD. And then once we’ve done that analysis and we’ve understood which one of those are best in a physical environment, we would then scale those up to do a full-size car design. And at this point, we’re back into NX again and we’re looking at making the aero concepts able to perform in a real-world function, i.e. when we hit the track. And that means that we’re looking for not just aero performance, but also sort of durability, we’re checking for fatigue that the parts can last. So, here we get into another set of virtual validation tools using FEA, doing FEA analysis to make sure that they’re structurally capable. And again, we’re using much of the Siemens toolset from a design simulation perspective to do that analysis.
Jennifer Piper: What kind of physical testing is involved in the process?
Daniel Watkins: Once we’ve done that, from a full-size perspective, we then commit to manufacturing parts for testing. So, we have a research and development element to what we do as well. We’ve got a lab where we take those parts that we manufacture, we put them into the lab and we test them to see whether the results that we get, again, with the physical part match what we got from a virtual validation in FEA. And if we’re happy, then we start manufacturing parts to go on the car. Because we’re limited on testing, the only time we really get to test any of this is typically when we go racing or at the beginning of the season when we have two test periods before we start the season proper. But in season, that test is normally in the practice sessions before a race weekend. So, the regulations of the sport dictate that you can’t just make parts and then run them on a track.
Jennifer Piper: So, then, what needs to happen to get the final design of the car over the finish line?
Daniel Watkins: We take new ideas and new concepts. Once we’ve manufactured them, we take them to the track, and the first time we ever see them perform is on a practice session – on the Friday of a race weekend. And that’s where we then really understand whether the virtual validation that we have in CFD and FEA then come true in reality when we’re racing around the track. If the results that we see on track are good, so the parts are better, then those parts get to go racing. So, they’ll go racing that weekend. But if they’re not, if they don’t correlate and they don’t give us the performance we expect, then they don’t go racing. But whatever we learn from that, whatever learnings we get, we feed that back into our design loop and we do it again. So, after we’d been racing, we come back the following week, and then we feed that back into that design loop where we go again. So, we then look to improve the parts, and we go round that iterative loop from concept design to virtual validation, manufacture, and then parts go to the race.
Jennifer Piper: Wow, so it really is quite the rigorous process. You talked a little bit about some of the products that you use in the suite of Siemens tools. Can you tell us some of the specifics there?
Daniel Watkins: One of our key strengths or an area that we think we’re really quite good at is the design and manufacture of composite parts — so, a hugely important aspect of any Formula One car and an area of the car that you can often gain most performance on track through bringing better updates to the car from an aero perspective that is typically composite in nature. So, over the last two years, we’ve pushed the digital side of that composite-design element by using Fibersim. Fibersim is a Siemens product as part of the NX toolset, and we really use that to drive the composite manufacturing process. So, we generate the ply layout and layups in Fibersim, and we output that information to help us develop our playbooks. These dictate how we manufacture the parts. And we also use that information to drive our laser ply projection machines that allow us to project a laser onto a mold and then, more accurately, lay up the plies on that mold.
Jennifer Piper: How has the introduction of these machines changed that process?
Daniel Watkins: We used to do this manually. We used to have very skilled guys and girls in computing manufacturing that would manually use drawings and templates to do that. And the introduction of laser ply projection has really, really improved the variability that we would see when you left it to individuals, however skilled, you would get variation. And now it’s super accurate, so we get a very repeatable process, we get very little variation from person to person. And we’ve also reduced, quite dramatically, the amount of waste of carbon fiber that we get as you lay the plies in. Typically, if you’re doing it manually without the help of a laser ply projection machine, then you would overestimate how much carbon fiber you needed; therefore, the waste material that you would trim off would be much more than we see now.
Jennifer Piper: And I assume it must speed up the process as well?
Daniel Watkins: One of the biggest benefits, aside from all those other things, is the speed at which we can do this. We conservatively estimated that we get about a 30% improvement on some of our key parts in the manufacturing process. That really allows us then to hand that time back to design better parts. So, if we can save 30% in our manufacturing process and our manufacturing time, then what that allows us to do is give the engineers that design those parts more space and more time to design better parts — so, better quality, more robust, and hopefully, faster.
Jennifer Piper: I’d like to talk a little bit more about the software you’re utilizing in your process. It sounds like you must rely on the digital twin as part of your design. Can you talk a bit about how that plays into everything?
Daniel Watkins: We absolutely rely on having a digital twin of the physical car that we see on the track, and it’s pervasive throughout the business. So, we have a digital process that runs from concept to track, and that process relies on that digital twin of the car. So, we 100% model and design everything in CAD. We have a set of virtual validation tools from CFD to FEA. Also, within the manufacturing space as well, where we virtually validate all of our manufacturing tool parts, so that we can have confidence that when we put parts on a physical machine to make, that we’re not going to have any issues on the machine itself. We virtually mock up the assembly of the car. So, that’s available to the guys at the track.
Jennifer Piper: I imagine that mockup must be key when a brand new car is on the track for the first time.
Daniel Watkins: Particularly important at the beginning of the season, when it’s the first time the mechanics are going to have seen this new car. So, we try and provide them a rich set of digital tools where they can see what this needs to look like and how this goes together as they’re seeing these physical parts coming through for the first time. And then, obviously, we capture lots of data coming back off the car. So, the car is a big instrumented device that then feeds us back information about how it’s running throughout the race and then enables us to act on that information and change what we need to do as we go around a track. And then this is all fed back into our key systems, Teamcenter being our PLM system, the core of the design of our car, and that then stores the information that we need in order to design the car and then helps us feedback into that, and then electronically push data around to all of the various people that need it to enable us to make better-informed decisions and act quickly. So, it gives people the ability to act quickly based on the right information being available at the right time.
Jennifer Piper: So that flexibility is a chief factor in your success. How important is the openness of architecture and flexibility of software tools in your process?
Daniel Watkins: I would say that they’re really key to driving the speed at which we’re able to push change through our business. And what we know through being here for 18 years is that the amount of change that we can push through the business really tallies with the amount of points we can gain. So, we know that if we need to be winning championships or winning races, we need to be able to push change through the business in order to be competitive and be at the sharp end of the race results. So, having the openness of architecture and the ability to customize where we need to is really important because as an F1 team, you can’t go and buy F1-specific things off the shelf — they don’t exist because we’ve got some niche applications and some niche use cases. So, being able to extend the tools that we have in a controlled way really allows us to push the productivity of our engineers to another level.
Jennifer Piper: Can you talk a bit about where Fibersim plays into all of this?
Daniel Watkins: Fibersim is a really good example. So we touched on the competent manufacturer and competent design, and the fact that we’re using Fibersim as one of our core tools now. Here we’ve used the NX open toolset to automate some of the key steps that we go through to get to the point where we can provide manufacturing with the information they need to feed their laser ply projectors to the point that what we’re seeing is that a process that would take probably four days to go through manually to get to that point, we’ve automated that down to probably 10 minutes with vendor checking the work. And that’s down to the openness of the toolset that we use and the ability to programmatically take away the tasks that would usually cause engineers to spend more time than we would like on the tools. But what it does do is it gives them the ability to then focus again on the quality of what they’re doing; focus on being engineers or imagineering new concepts, rather than having to work within the tools. NX and Teamcenter are great for providing that architecture for us to be able to do that.
Jennifer Piper: That’s incredible—four days down to ten minutes! That must make a huge difference in the process.
Daniel Watkins: It makes a massive difference. We see the same in the design tools where we can use NX automation and a robust parametric modeling approach to really drive the number of iterations of an assembly. So, take a fruit-weighing assembly, which is probably the most influential part of the aerodynamics on a car, we can really push the design and development of that by, one, through robust parametric modeling within the CAD tools, but also then with automation of that robust model so that we can really churn through designs that we can then send to CFD, that we can then validate virtually and then move forward with. So, it makes a huge difference, probably five or six times faster using the NX open tools than we would be able to do if you were to manually do it. So, it’s significant.
Jennifer Piper: I’d like to move on to the practical aspects of Formula One design. What would you say are your biggest challenges when it comes to designing a car? Are there any constants you tend to run into?
Daniel Watkins: I’d say it’s variable. There are some constants. The constant being rule changes. So, when I say “constants being rule changes,” we invariably get rule changes from season to season, so we almost bank on that being a thing that happens. And dealing with those rule changes can be a challenge. So, understanding what the regulatory body of the sport, the FIA, is saying that we need to adhere to, and then correlating that to a set of rules that we then deliver to our engineers that they can then work within. And we often take those rules that are just documents of text, and we convert them into geometry wherever we can. So, what that allows us to do is bring that textual information into a 3D digital world to give space envelopes or volumes or car mockups that then our engineers can use to help them drive or be mindful of their designs when they’re coming up with new concepts to make fast car, that really makes a big difference.
Jennifer Piper: Have you ever run into any issues with factors like cost?
Daniel Watkins: So, the FIA, again, our regulatory body, has enforced cost caps on the sports for all teams. So, we now have to be more mindful about where we focus our development, so then we have to have more confidence in what we take from a concept to a physical part, which means that there’s a much bigger reliance on our digital toolset so that if we can digitally mock up more concepts, and we can do that faster, and then we can validate those concepts virtually using those same tools, then that means we can have more confidence in the parts that we take forward to manufacture which is often where we incur the biggest cost before we do that. So, NX and the integrated tool sets within the NX portfolio, from design to composite design and manufacture, to the CAM tool — we use NX CAM here to program all the parts — having these things joined up and linked together really helps us push that so that we’ve got a high level of confidence in the parts that come out physically, such that we’re not making things that don’t work because, in an era of cost caps, that really hurts.
Jennifer Piper: So, how far ahead of the design process do you, as the team, get notified of the FIA’s new rules for the season?
Daniel Watkins: Ideally, we’d always like longer, but it’s always tricky because new rules and regulations have to be agreed across all the teams also. So, it’s normally months. And sometimes, less than that. But usually, anywhere between a month and six months that you’ll get a notification. But that’s a lot of work to do still to change what we do. And maybe if we look at the regulations, this season was a new car, completely, ground up, new design, completely different from the last car. The things are the same in the fact that we’ve got four wheels and engine, and a driver in it, and then everything else around that, is pretty different. But even the wheels are different this year. So, we’ve got larger wheels, less tire now, the tire is thinner. That brings its own challenges in. So, we probably got a little bit more advanced notice, but the rules weren’t firmed up till probably late last year, Q3 or Q4. But you take a view on these rules, so you’ll get some time to digest them. And then we’re working on what we know, and then iterating on that as the rules become hardened.
Jennifer Piper: It sounds like your keys to solving those challenges really lie in the tools that you’re using to design and manufacture the car.
Daniel Watkins: The digitalization of our workflows and processes and the tools that we use are really what we need to fall back on now because we’re limited everywhere else: we’re limited on resource, we’re limited on cost, we’re limited on time, we haven’t got more hours in the day or days in the week, we can’t throw people at the problem now. So, we have to look at the digital tools and the processes that surround those to help us drive us forward to still be competitive. And if we can put the same effort into that as we do for the car, then for designing and developing that we do the same with our tools that we use to support engineers, then that really is a key area for us to help us move more quickly. And working really closely with Siemens — Siemens being our longest-standing technical partner — we’re constantly working with you guys to help us look at the art of the possible. So, what’s next? What can we use now from this rich set of digital tools that you have that can then allow us to be better tomorrow than we are today? And that’s really what we’re looking to do every day. And yeah, we rely heavily on the Siemens tools to do that.
Jennifer Piper: Switching gears a little, are there any common myths you hear about the Formula One racing industry that you’d like to dispel?
Daniel Watkins: We often get that we have a favorite driver and the favorite driver gets a different car. I can’t remember or count the number of times somebody has said that. So, you have a favorite driver, and he gets a different car as the other driver, and it’s faster. And typically, that’s absolutely not true. And mainly because what most people miss is that Formula One has two championships: Drivers Championship and Constructors Championship. Whilst we’re trying to win both, the one that impacts everybody here at the factory in Milton Keynes, Bedford is the Constructors Championship, that’s the team one, that’s the one we’re all pushing to win. But everybody outside of the Formula One team, whichever team you’re in, everybody looks at the Drivers Championship as the one but we’re really focused on the team one, so it’s the team one that we want to win. And that means that you need to get two cars round, two cars to the finish. You need to have two cars that score as many points as you can to try and win that Constructors title. So, we really don’t favor one driver over another.
Jennifer Piper: Is there ever a time when there would be two different cars racing for your team?
Daniel Watkins: The only exception is if we’ve got a new exciting development and we haven’t had time to make two lots of parts just because some of the timescales are crazy here. We’ve got weeks or days between races, and so trying to get parts designed and manufactured in that time scale is challenging. So, sometimes you’ll see that where we haven’t had time to manufacture two sets, but typically the cars are identical, the difference being, some drivers are bigger and smaller, so their seats are different and their pedals are different, but generally it’s the same car, two cars going around the track.
Jennifer Piper: What role or influence do drivers have in the design of the car?
Daniel Watkins: Well, obviously the drivers are an integral part of the car. So, it’s all a connected system, the driver being in the loop, and he or she will always feed back what they think about how the car is handling or driving. So they will feed back what they feel as they’re driving that car, then we will use that feedback to try and improve the car or change the car. So, it’s not typically a direct design: “Design this part in this way.” But it’s almost indirect: “Well, we’ve put these new parts on the car, and this is how it feels to drive.” So, then we interpret that back, and then that then influences maybe how we set the car up or how we then feed back to the engineers what we think about the design that we’ve just brought forwards.
Jennifer Piper: You’re allowing for that loop of feedback in order to make continuous improvements along the way.
Daniel Watkins: That’s correct. Whilst we’ve used our virtual simulation tools to figure out which parts we’re going to go racing with, when we put them on the car and we see the results of that, the driver’s feedback also forms part of that feedback loop. And within our iterative loop we have a virtual driver simulation. So, we have effectively fancy PlayStations, where the drivers can drive the setup of the car and drive the tracks in that virtual simulator before we go to the track. So, we scan all the tracks, and then we drive the tracks in our simulator, and that forms part of our feedback loop, too. So, that’s feeding into the process as well as the actual driver feedback when they get to race it for real.
Jennifer Piper: So you have actual human feedback as well as that automated feedback. Now, how did the Oracle Red Bull Racing team manage through the pandemic? Were any of your processes interrupted or were you still able to do design work?
Daniel Watkins: Well, like for most businesses and most organizations, it was a massive challenge. We’ve, typically, been a business that people come here to work, so they work on site. And we put a lot of emphasis on internal collaboration, particularly in engineering. So, we colocate all of our engineers, we have a huge engineering office. And we’ve, for years, actively encouraged face-to-face collaboration with people because that’s really the best form of communication. And if you can have those conversations directly with the person two bays down from you, then that really expedites how we’re able to design and develop the car. It makes a really big difference. Even if we’ve got engineers in one building and engineers in another, the fact that you’ve got a gap between them prohibits that a little bit, even with all of the tools we have today.
Jennifer Piper: That must have been a struggle, then, to continue to have that sort of collaboration.
Daniel Watkins: So, it was a challenge for us. But because we’ve, over several years, worked hard on the digitalization of our tools and processes, we were able to quickly spin up the infrastructure that allowed us to support remote working. So, we had some before we started, but it’s fair to say that the pandemic meant that we needed to have an order of magnitude more. So, we were able to do that quickly. The digital tools that we had in place really supported that remote working process. And whilst it wasn’t what we think is an ideal way, it really helps during that period, and still does today. We like to provide our engineers some flexibility, and this allows us to do that. And the digital tools that we have underpin the ability for us to do it. Having our processes electronic — so, all of our sign-off processes are electronic, all of the delivery of information to the various users around the business is all electronic — that then underpins our ability to be able to work remotely in a less disrupted way than some of the businesses would have been able to do. In fact, we think it’s probably a big reason why we were quite competitive last year and it led us to being able to win the championship with Max.
Jennifer Piper: It sounds like you were really able to change and adapt successfully, even with that massive challenge. Congratulations on your success so far. We’re definitely excited to see how it all turns out.
Daniel Watkins: Fingers crossed. When November comes around, we’re still on the top of both championships because that’s where we want to be this year.
Jennifer Piper: We’ll certainly be rooting for you. And thank you for sitting down with us. We’ve gotten some great insight into the design process at Oracle Red Bull Racing. Thanks so much again to Dan for joining us today. Thanks also to our listeners for tuning in to today’s episode. Join us next time for more discussions about the latest in design innovation and software applications. I’m your host, Jennifer Piper, and this has been Next Generation Design.
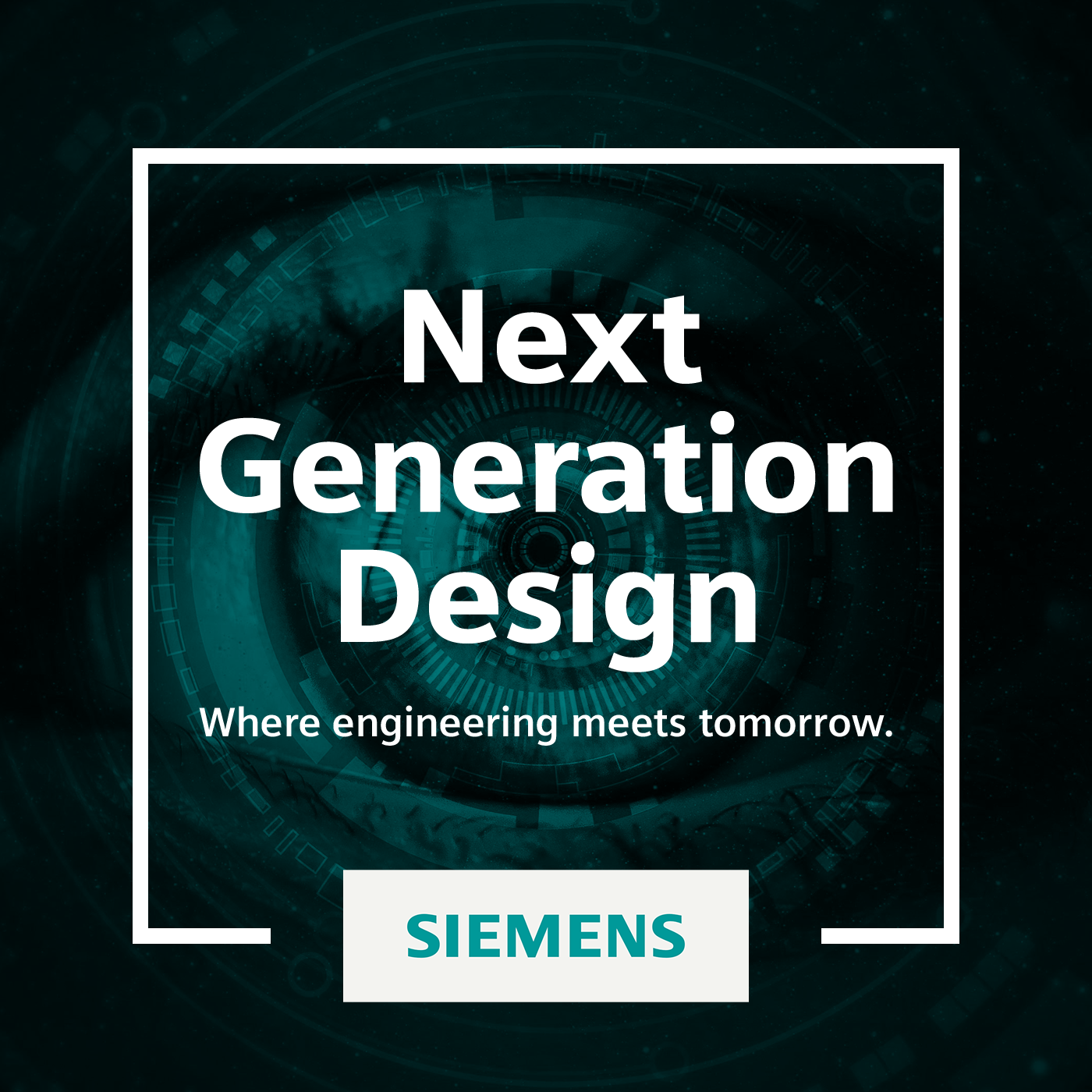
Next Generation Design Podcast
As product engineering tools continue to morph and expand at speeds human expertise may not be able to endure, Revolutionary design technologies that span beyond industry borders, will prove their necessity for companies looking to take over their markets in the future. What will the future of design technologies and machinery look like? What will your digitalization story be? Where engineering meets tomorrow.