The Benefits of Modular Construction
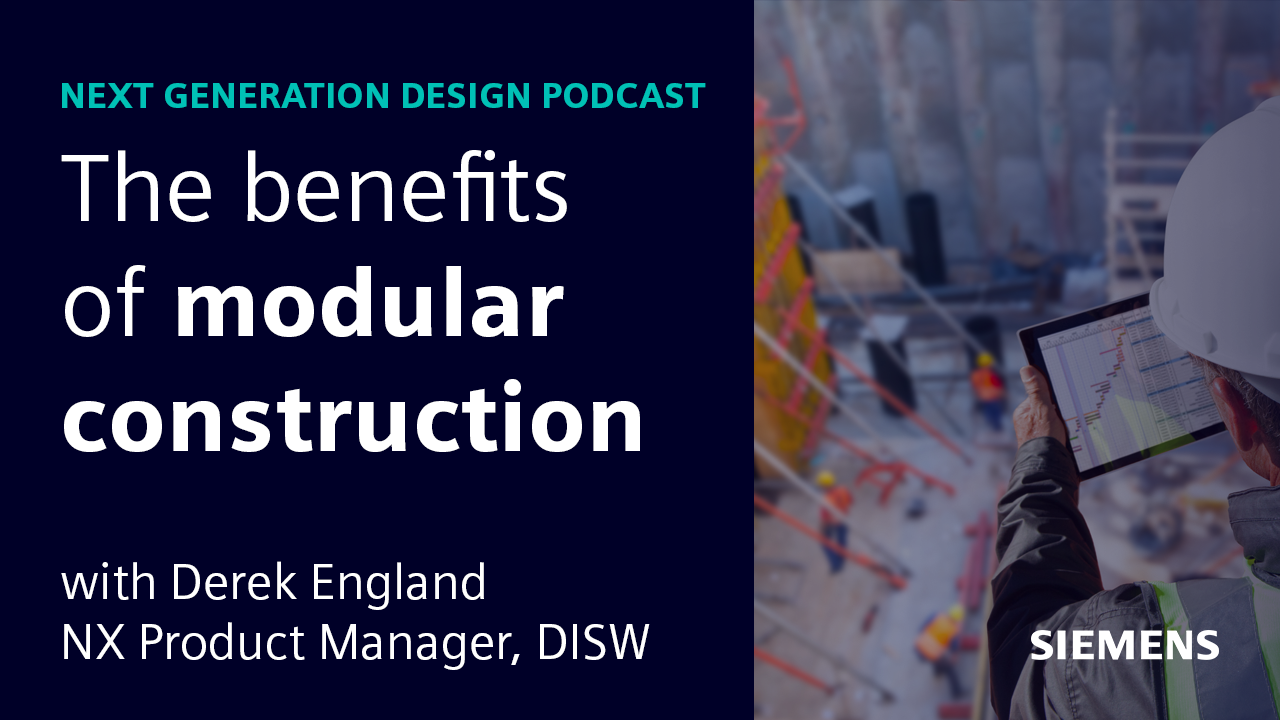
The construction industry is facing a labor shortage challenge that is expected to worsen in years to come. This has motivated more companies and governments to explore modular construction, which is faster and solves the labor shortage problem. Additionally, companies in this space have digitized the design process to make it more efficient and affordable.
On this episode of the Next Generation Design podcast, our host Jennifer Piper is joined again by Derek England, NX Product Manager for AEC and BIM at Siemens Digital Industries Software. He’ll help us understand modular construction and its impact on the industry. He’ll also help us understand the role of Siemens’ NX in this relatively new field.
In this episode, you’ll learn the factors that have led to the rise of modular construction. You’ll also learn about the two types of modular construction and the benefits of each. Lastly, you’ll hear about the benefits of using the digital twin in the building design process.
This is the third episode of a three-part series. Listen to or read the first episode to learn about technology trends in the AEC industry and how an integrated solution can improve productivity with building information modeling, and the second episode to learn how to simplify the design review with collaborative BIM tools.
What You’ll Learn in this Episode:
- The meaning of modular construction
- Why modular construction is appealing to customers
- Problems solved by modular construction
- How the digital twin helps modular construction
- Derek describes his experience visiting a modular construction factory
- Modular construction barriers
In modular construction, you can start building before the site is even prepared. You can work in parallel. So, site preparation and construction of the building happen in parallel.
– Derek England, Siemens Digital Industries Software
Listen to the Next Generation Design podcast wherever you do podcasts.
Connect with Derek England:
Connect with Jennifer Piper:
Listen to or read the next episode of the Next Generation Design podcast: Designing For Speed using NX CAD
Listen to or read the previous episode of the Next Generation Design podcast: Collaboration and Coordination of BIM Tools in the AEC Sphere
Podcast Transcript
Derek England: Today, you have to grade the site, you’ve got to pour concrete, and then you build on top of it. Well, in modular construction, you can start building before the site is even prepared. You can work in parallel. So, site preparation and construction of the building happen in parallel. You also are working in a perfect, controlled environment, ideal working conditions, where your tools are right there, your equipment is right there, your materials are right there, under a roof, so your wood is not getting wet, your equipment doesn’t have to get packed up in your truck and transported every day back and forth.
Jennifer Piper: Welcome to another episode of the Next Generation Design podcast. I’m your host, Jennifer Piper. In this episode, you’ll hear the conclusion of our three-part series with Derek England, NX Product Manager for AEC and BIM at Siemens Digital Industries Software. In our final chat with Derek, we’re discussing modular design and the trends, implications, and solutions it may hold.
Jennifer Piper: Derek, before we begin, can you please give us a brief reintroduction?
Derek England: I’m Derek England. I’m the NX Product Manager for AEC and BIM at Siemens Digital Industries Software. I’ve worked in this industry for about 25 years. I’ve had the opportunity and pleasure to work with some of the most innovative companies in the world and understand their workflows. I’ve had a small part in helping them achieve some of their productivity goals. So, as the product manager, it’s my job to make sure that we understand these workflows and enhance our product to help our customers achieve their high productivity goals.
Jennifer Piper: Thank you for joining us once again for our three-part series. In part one, we covered trends in the Architecture, Engineering, and Construction industry as well as what still needs to be done to improve tech integration in the sphere. In part two, we discussed the benefits of collaboration using multi-discipline building information modeling tools in the AEC. Today, we’ll be talking about modular design. Derek, could you give us a bit of an overview of the topic?
Derek England: So, modular design, it’s been in the news a lot recently, at least in my world, it’s been in the world a lot. When you first tell people about modular design, they give you that look that’s kind of like, “Ugh!” There’s a stigma associated with prefabricated buildings. Most people equate prefabrication with mobile homes like my grandparents lived in. But you don’t hook it up to a truck and pull modular homes. It’s different than that. And when you see some of the prefabricated homes, offices, buildings, and hotels being built in Europe, they’re beautiful. And there are a lot of economic and sustainability drivers that are putting pressure on construction companies to embrace modular construction. And today, I want to talk about some of these trends, implications, possibilities, and solutions for this space.
Jennifer Piper: As you said, the term “modular design” often has a bit of a stigma attached. Can you break down the term a little more and give us some background on the concept?
Derek England: Traditional methods like stick build, kind of what you refer to, it’s like you pour a foundation, you build up the walls, and you build on a roof — that’s traditional ways. Modular construction is when you construct a building off-site in a factory setting. It’s the same way you would build a plane, train, automobile, or machinery; you build it in a factory. Modular buildings still are built using the same materials and they adhere to the same building codes. They’re stopped to get permitted and approved. So, it’s similar, but you build them in a factory, and then you transport them on a truck or on a boat, and then they get assembled on-site using cranes. Kind of like Lego bricks; just stacking them up next to each other, and you kind of connect them together.
Jennifer Piper: And it seems like that setup would also be a much more efficient way of doing those things.
Jennifer Piper: So, what makes modular construction so appealing to customers? What are some factors that might lead a customer to choose it over traditional construction?
Derek England: There are a lot of reasons why. A key one is just a reduction in the labor force. What some of the analysts have found is that for every two people that are retiring in the construction industry, only one re-enters the workforce force. For years and years, we’ve been telling the kids: “You need to go to college. You need to go to college.” Mike Rowe from Dirty Jobs — he is a big proponent of this, and he says, “We’ve elevated the importance of higher education to such lofty perch that construction jobs are seen as vocational consolation prizes, best suited for those not cut out for a four-year degree.” That’s one reason. We’re not attracting those kinds of kids into this workforce, so that’s a challenge too. And skilled labor is hard to find.
Jennifer Piper: That definitely makes sense. It also seems to be very relevant to what people are calling “the Great Resignation” that’s currently happening among much of our workforce. So, that lack of skilled labor force is leading to major supply and demand issues?
Derek England: I don’t know if you’ve ever done construction or remodels recently. But if you want to find somebody, it’s hard. They’ll say, “Yeah, we’ll get it done in a month.” But it takes months to get it done because it’s hard to keep those people engaged and on-site. The big construction projects, a third of the time on the construction site is just spent waiting for information, material, or equipment. Imagine if you had engineering construction all under the same roof, that would be of great benefit. If you had a question for the engineer, you can walk upstairs and go talk to them.
Jennifer Piper: Other than the labor force issue, are there any other major reasons modular construction might be more appealing?
Derek England: Here in Southern California, we have great weather — you can build houses all year round. But in many places, it rains, it gets cold weather, and it’s frigid temperatures, and it can cause construction delays. And then with regulations now, they want these construction companies to clean up their act. They want to produce less pollution and less waste. Even communities are saying, “We don’t want dust, noise, and light pollution.” You need to be sensitive to those communities as well. I think there’s just a feeling that we’ve been building houses the same way for decades, and we’re not going to achieve new efficiencies without changing the way we do things.
Jennifer Piper: How do you see modular construction being able to address those specific issues that you’ve pointed out?
Derek England: One of the quick and obvious ones is that it’s faster. Today, you have to grade the site, you’ve got to pour concrete, and then you build on top of it. Well, in modular construction, you can start building before the site is even prepared. You can work in parallel. So, site preparation and construction of the building happen in parallel. You also are working in a perfect, controlled environment, ideal working conditions, where your tools are right there, your equipment is right there, your materials are right there, under a roof, so your wood is not getting wet, your equipment doesn’t have to get packed up in your truck and transported every day back and forth. So, that’s a big benefit.
Jennifer Piper: Definitely, I can see how that would also go back to what you’ve emphasized in our previous episodes about collaboration between the various disciplines. What other issues can be addressed?
Derek England: The quality is typically better because you are manufacturing in this perfect environment, and also the quality has to be good enough that you can actually take this room, this module, pick it up with a crane, put it on a truck, drive it across—or put it on a boat, float it across the ocean—and then assemble it again. So, it’s got to be sturdy enough to do that, which means it’s pretty well-built quality. So, that’s another benefit.
Jennifer Piper: And what about in regard to those issues you identified with the workforce?
Derek England: It’s hard to find somebody who can do everything, who can do drywall one day and rebar another day, and concrete or framing. And they’re expensive to find and hard to retain, too, because they’re in such high demand. So, on a production line, you could say, “Okay, I need to hire somebody. This is your job on the construction line.” He’s got one job and he does it every day. So, because he’s doing it every day, the quality is good, too, because he’s a professional at that one task. It’s easier to train them and the quality gets better, too. But the one that I think, for a construction worker, put yourself in their shoes and says, “Okay, I’m driving all over, to different places and locations throughout my city,” or my state, working in all different locations. Imagine if you could just buy a home close to where you work, drive to work within a short commute, not have to work in the heat of the sun or in the cold of the weather, and be able to work in a temperature-controlled facility. How nice would that be? How much would your job satisfaction go up? How much more would you be able to attract new employees?
Jennifer Piper: So, not only is it a place where you’re able to double down and hone your skill set, it’s also a much more stable, predictable job for those employees.
Jennifer Piper: Derek, you’ve explained how modular design may be a solution to many of the issues plaguing the AEC industry today, but I’m curious to know how the digital twin fits into all of this.
Derek England: The digital twin starts back in engineering. Today, it kind of starts in engineering. So you have the design, and that data goes all the way through to construction. One of the big benefits, like we talked about, is that the digital twin can all occur in one building, basically — the design and construction are all in one facility. So, it really helps so that when you have an issue on the factory floor, you can walk down there, show the engineer what’s going on, and say, “This is why your design stinks.” And then they could say, “Oh, yeah, I didn’t catch that.” So then they could go back and immediately make a change. In a typical process, they would just make that change on-site, the designer would never know about it, this next design would have the same mistake again, and you would never find that. So, this helps with that loopback structure for the digital twin to improve that.
Jennifer Piper: Can you tell us a bit about what those modular construction assembly lines look like? How do they function?
Derek England: They vary wildly. The very high-end ones—some of the ones they’re building now—they’re highly automated with robots and CNC machines. You can see the robots welding steel cages, cutting, sawing, nailing, and things like that. So you look at it and you’re like, “Wow! This really is like an automotive assembly line.” But some modular construction companies have simply just moved construction off-site — it’s just, “I’m still building traditionally with a hammer, wrench, nail gun, and climbing up ladders.” So you haven’t really changed the process or innovated the process; you’ve just moved it inside, which has benefits. We talked about some of the benefits of constructing inside. But if you want to achieve productivity goals like you see in the automotive industry, you need to change the process, you need to automate these things.
Jennifer Piper: That definitely makes sense from a productivity standpoint. What can you tell us about the variations of modular buildings?
Derek England: There are two types of modular buildings: panelized and volumetric. Panelized construction is kind of like assembling Ikea furniture; you get a box and it’s got all the pieces together, and then you build it in your house. You didn’t have to drill the holes, you didn’t have to assemble the hardware and find all the hardware, it kind of came to you all packaged up. So, it’s much easier to put together IKEA furniture than to build it from scratch. So, that’s panelized construction: the walls already have outlets, conduits, and plumbing already inside of them; you just have to connect them on-site. Volumetric construction is where you manufacture the entire room or part of the building. Typically, they’re about the size of a shipping container because that’s what can get transported on roads and ships and things like that. But in both cases, these panels and modules are transported to the site on trucks, they’re unloaded by cranes, and then workers connect all the modular pieces together.
Jennifer Piper: Which would you say is preferable? Panelized or volumetric? Why would someone choose one over the other?
Derek England: Panels are nice because they collapse down flat, so it’s cheaper to ship. But it also takes longer to assemble on-site. You can imagine these panels get assembled on-site. If it’s raining there, they’re out in the rain, connecting all these things up together, they’re getting wet, and they have to deal with that. Volumetric modules are faster to assemble, you just deliver them on-site and place them next to each other. And with volumetric modules, you can have it almost 90% complete, some are shooting for like 95% complete. So, literally, you put it down, you connect it to electricity, and you feel like you’re already in a bedroom or a hotel room. It’s got carpet, it’s got wall treatments, it’s got furniture, it’s got plumbing, everything is already hooked up. So, you can deliver it more on-site. There are benefits like volumetric modules are great for restrooms, kitchens, and stuff like that. But panels can be good for bedrooms and living rooms. And some companies are saying, “Well, let’s use the best of both worlds. We’ll do panelized for the bedrooms, and then we’ll do volumetric for the bathrooms.” And you see that a lot in hotels today. Actually, a lot of hotels, when you go to assemble it, they actually have a whole bathroom in one piece and they just drop it in during construction.
Jennifer Piper: Wow, that’s pretty crazy! So it seems like there’s definitely a method and efficiency to it, unlike any other type of construction.
Jennifer Piper: Modular construction seems like it may just be the way of the future for AEC companies. Can you tell us about any Siemens customers in particular in the modular construction sphere?
Derek England: One of them that I’m familiar with is Max Bögl. They have a modular construction facility just north of Munich. They’ve been doing it for a while now. Back in the 2017-2018 timeframe, they wanted to invest in a plant for serial production of modules for multi-story residential construction. The room modules, you can stack them. And I was there and I was like, “How high can you stack them?” And they’re like, “Like six or seven stories high.” So you can stack these things on top of each other like Legos and they’re self-supporting, you don’t need to have an exterior frame to support the weight; they have that support built within them. And then they have all kinds of different layouts and configurations.
Jennifer Piper: That sounds pretty incredible. What do those modules actually look like in a real-world setting?
Derek England: They’re all about the same size, but some will have a wall missing here or cut out here. There are just lots of different modules to choose from, but all kind of the same size. So, when I went to go visit them, it’s just like a production line; there are 16 different stations, each module stays at each station for 60 minutes, and then it moves to the next one. Sounds a lot like an automotive production line. Modules are delivered on-site and assembled on-site. These particular ones are about 80% fabricated, so you’d still put the flooring in and some wall treatments and things like that. But it dramatically shortens the time needed. And when you go to on-site, it’s all inside. Because they’re using standard modules, they’re able to put them together in different ways. It was fascinating to see some of them have one wall missing or two walls missing. So, they actually had on-site an example of one of them. It was pretty cool. It comes all preassembled, it’s got the sinks and the walls. It’s one of the reasons why they chose our software is because these particular things had requirements for concrete, electrical, and plumbing. And then they wanted to document it, and then they wanted to run right down to C and C. So, they wanted a tool to do all of this. And the current set of tools that were all kind of disparate, they couldn’t go fast enough, so they really relied on our software to deliver it. One of the customers said, “Max Bögl selected Siemens tools because they could not achieve their efficiency goals with other AC tools.”
Jennifer Piper: It sounds like it’s a very comprehensive system in terms of addressing that collaboration between disciplines.
Derek England: Yeah. It was the integration between all the different tools that was the big benefit, instead of designing in one system and throwing the electrical stuff over the wall and designing the plumbing in another system and throwing that over the wall. They designed all in the context of each other and made changes in the context of each other.
Jennifer Piper: It sounds like it’s a very comprehensive system in terms of addressing that collaboration between disciplines.
Jennifer Piper: Yeah, they decided to build their whole headquarters using this system. It was in the process of being built so I haven’t seen that yet. But the goal was that they were going to design their new headquarters using this. But they did have one on-site, and it was like a two-story office building. I thought, “Oh, you’d go in there and I’d be able to say, ‘Oh, here’s where one module ends, and here’s where the other one begins, and this is how they connect together.’” I kept looking around trying to imagine, like, “Okay, where does one stop and where does one start?” And I couldn’t figure it out. You can stack these things in different ways. They don’t have to be perfectly lined up right on top of each other, they can stack perpendicular to each other. It was really fantastic. And I think that’s one of the challenges that a lot of architects think like, “Oh, I don’t want to do modular construction because I can’t be creative enough. It’s going to be boxy.” But what they’re finding is those who are embracing it, find the opposite. A lot of the times with homes, the exterior is just a little bit different; they put up bricks instead of rock or stucco or something like that. So, you’re really able to achieve a lot of flexibility in the way it looks. And then inside, I found that you really can be pretty creative and get the benefits of modular construction, but also have the creativity to design something unique and custom for their customers.
Jennifer Piper: To be able to have that level of creative freedom while prioritizing productivity must be a huge draw. I’m sure they were pleased with that aspect. What other feedback have you heard?
Derek England: The process they set up, they’re really on the forefront of this. One of the associate partners from Porsche Consulting came out and looked at this production line that I saw and they said, “The Max module concept is revolutionary. It combines standardization, individualization, and industrialization in a single product for construction sites at a uniquely high level of quality.” So, they’re getting noticed. And you’re going to see more and more people embracing modular design but there are some hurdles to go.
Jennifer Piper: So, it sounds like modular design may have some very real effects on the current process of construction. What kind of impact do you see it making on the current US housing crisis?
Derek England: It takes a long time to build houses or to convert office space into apartments and things like that. There are a lot of challenges to do that. I was just at a town meeting and the governor of California says, “We need at least 6 million new units in California.” And then he just distributed and said, “In my little town, you need 6000 units, and you need 6000 units.” And he just distributed and said, “Everybody, you need to take this on.” And they’re saying, “We don’t have the road infrastructures. We don’t have everything.” It’s really challenging to do this. But as far as building them, they know they can be faster. Max Bögl, I think on their site, they said they can build 20 units and can be ready for residents in just 90 days. Imagine being able to say, “I need 20 units, and I can do it in 90 days.” In 10 working days, you can assemble 60 of these modules together so you could build big apartment complexes as well. So, I think you’re going to hear more and more about modular design in the news as a way to address the urgent housing market shortage. I think urban planners are going to wake up and just say, “Okay, it’s not going to get any better, we’ve got to do something different.”
Jennifer Piper: It seems like more recently the construction process has reached extreme lengths, so I imagine this could be a great solution to that problem.
Derek England: A company that builds hotels, lots of hotels, a major hotel chain, and they were saying, “10 years ago, you could build a five-story hotel in about 10 months. Now, it’s twice as long.” It’s just math: there are half as many people to build, so it’s taking twice as long. And it’s not getting any better. It’s not like all of a sudden, they’re hiring a lot more people, it’s going to get harder and harder. So, just because of the workforce shortage, you’re going to have to see a change.
Jennifer Piper: What are some of the barriers you see that might prevent the large-scale adoption of modular construction
Derek England: It takes a lot of capital to build a facility like this. So, I build this facility, I can pump out these modules that look like this. After you get done with that project, maybe somebody else comes in and says, “I want the modules to be a little bit different.” Now you have to do all the retooling. Getting enough people to say, “Okay, this is what I want to do,” and getting that flow of orders coming in is hard. And every single time they want to make a change, innovation has to happen. We’re still learning how to do it better. We don’t have CNC machines to run chop saws. So, now we need to do that, so let’s invent that. That’s a big challenge; just to do the innovation.
Jennifer Piper: Can you tell us any other major issues you’ve identified?
Derek England: I was surprised to hear about this is that I’ve been working with lots of companies in Germany, and they hadn’t really highlighted this issue. But here in the US, local regulations and inspection is a huge challenge. So, you imagine, “Okay, if I’m going to build modular houses, where am I going to build them?” You’re not going to go to New York City where it’s the most expensive to get labor, you go somewhere else, where land is cheap and it’s easier to hire people, and the cost of living is lower so that you can pay people a fair wage, but less. And let’s say you say, “Okay, I’m going to build this modular house or modular construction in Mississippi. And then I’m just going to drive it across a straight line over to Florida.” And then you say, “Okay, I’m going to install this in Florida.” And inspectors are like, “Hold on. Wait, wait, wait! I can’t permit this. How do I know that your electrical wiring is done right?” The plumbing guy is like, “Yeah, how do I know your piping is correct?”
Jennifer Piper: So, that difference in state regulations sounds like a major issue, then
Derek England: It’s like, “Okay, please tear out that wall so I can see the electrical or the plumbing.” And it’s like, “Well, wait a minute, we built it like this in a module, so it’s not easy to do that.” And some companies are kind of like, “Oh, well, we’ll build in little panels so that they can inspect them.” But how do you do that for 50 states? 50 different states, 50 different regulations — it’s just not sustainable. So, where you see modular being successful is places where they have a big enough market to support it. So you see some in California, which is a big enough market to support it; you see it in Germany, and then the Nordic countries because there’s higher acceptance, and then you only have to meet one standard and just sell within your own market.
Jennifer Piper: Well, it’ll be interesting to see how hurdles like this are tackled going forward.
Jennifer Piper: Derek, looking to the future, what place do you see for modular construction?
Derek England: I have a friend who’s in construction and he’s one of the managers over a huge homebuilder, and he said, “They’re just watching and they’re just waiting.” And they know we’re at a tipping point and it’s really close because they can’t keep going the way they’re going, but they also know that it’s going to be hard to make this change. So they’re just waiting for that tipping point. He’s not sure when it’s going to happen, but it’s close. We just don’t have the workforce to do it. Danny Forster from Danny Forster & Architecture, he’s been working to build modular hotels in New York, this big project. The benefits on paper were there. It was really clear that there were benefits to doing this. He’s working with Warren Buffett to streamline some of those regulations, and Warren Buffett was on board to do that. But in the end, they had it manufactured overseas, they got caught up in the shipping, they got delayed at the port, and all the schedules got thrown off because the modules weren’t showing up in time.
Jennifer Piper: So there are still some of those very practical issues to be sorted out.
Derek England: So, on paper, it looked great. You just throw your hands up and say, “One thing we can agree on is the way we build buildings today is dumb.” This is from Danny Forster. He says, “It’s not efficient. We have not innovated or improved in 100 years.” Honestly, what’s really super innovative that’s happened since the time the Romans built roads? There hasn’t been so much innovation. We’ve just hit that wall where we need to really do something innovative just strictly because labor force, but then you’re going to see a lot of fringe benefits with improved quality and improved speed of construction. It’s going to happen. It’s just a matter of time, I think.
Jennifer Piper: Will modular housing eventually be a more affordable option for consumers?
Derek England: Today, they’re more expensive. On paper, it’s supposed to be cheaper because you have a small site—100 feet by 75 feet or something like that—it’s tiny, where do you have lay down area? Where do you put your wood? Where do you put all your construction materials if you’re building a high-rise in the middle of a city? Imagine if you just had a crane there and you’re just delivering stuff on site, and you’re just stacking these modules on top of each other, you don’t need that lay down area. So, for situations like that, it makes a lot more sense. But then when you look at my friend who’s building houses here in Southern California, you can really almost set it up where it’s like, “Okay, every day, I’m going to have one house complete.” And it’s almost like an assembly line: “This house is done, this house is done, this house is done.” And you just do it like, “This is the task for this guy on this day, and then he does the same task the next day.” They are able to simulate that pretty well in California. But in other areas where you got remote locations and you don’t have access to the workforce or you don’t have good weather and things like that, it’s going to be slower adoption. So, it’s not feasible today in the particular market where I live, but in other markets, you’re definitely going to see a need and adoption.
Jennifer Piper: Before we wrap up, are there any other big innovations on the horizon that you’d like to tell us about?
Derek England: So, this is something that we’re excited about, I’ve been working on it for a while — a new product that’s an add-on for NX. So, our product, NX, has traditionally served companies that do planes, trains, automobiles, and stuff like that. And lots of OEMs, if you’re designing a product for construction, there’s a good chance that that product was designed using our software as well. So, if you did door hinges, locks, or foam boards and stuff like that, it could have been designed using our software. But that hasn’t traditionally been used to actually design the buildings themselves. So we’ve had several customers that said, “Hey, we do electrical substation, and 95% of the stuff you see in the substation is all your product, it’s all NX. But we need a four-wall building. That’s it. So, what do you got?” And we’re like, “I got nothing. Well, you can design it using traditional tools.” They’re like, “No, that’s not really what we want. We really want something that’s like to build buildings.” We started hearing this over and over again, there’s just a need. The guys who design a missile, they also needed to redesign the missile silo. What do you use for that? So, this digital twin you’ve asked about, you want to capture all of that together. You don’t want just dispersed between lots of different tools. You’d love to have this digital twin in one integrated environment. So, what we see is the need to have the ability to design a building in context of other things. So, that’s our initial target market right now; we imagine engineering will come in and say, “Okay, we know we’re going to have a digital twin. We know we want to have a building in context of other things. We can use this new product, NX, for BIM.” So, it’s getting released at the end of the year. I’m super excited about releasing it. I’m excited to get feedback from our customers as well.
Jennifer Piper: Well, that sounds like it has great potential. Thanks so much for joining us. It’s been a pleasure speaking with you in this three-part series.
Jennifer Piper: Thank you again to Derek for sitting down and talking to use through the conclusion of our three-part series. Thanks also to our listeners for joining us today. Join us next time for more discussions about the latest in design innovation and software applications. I’m your host, Jennifer Piper, and this has been Next Generation Design.
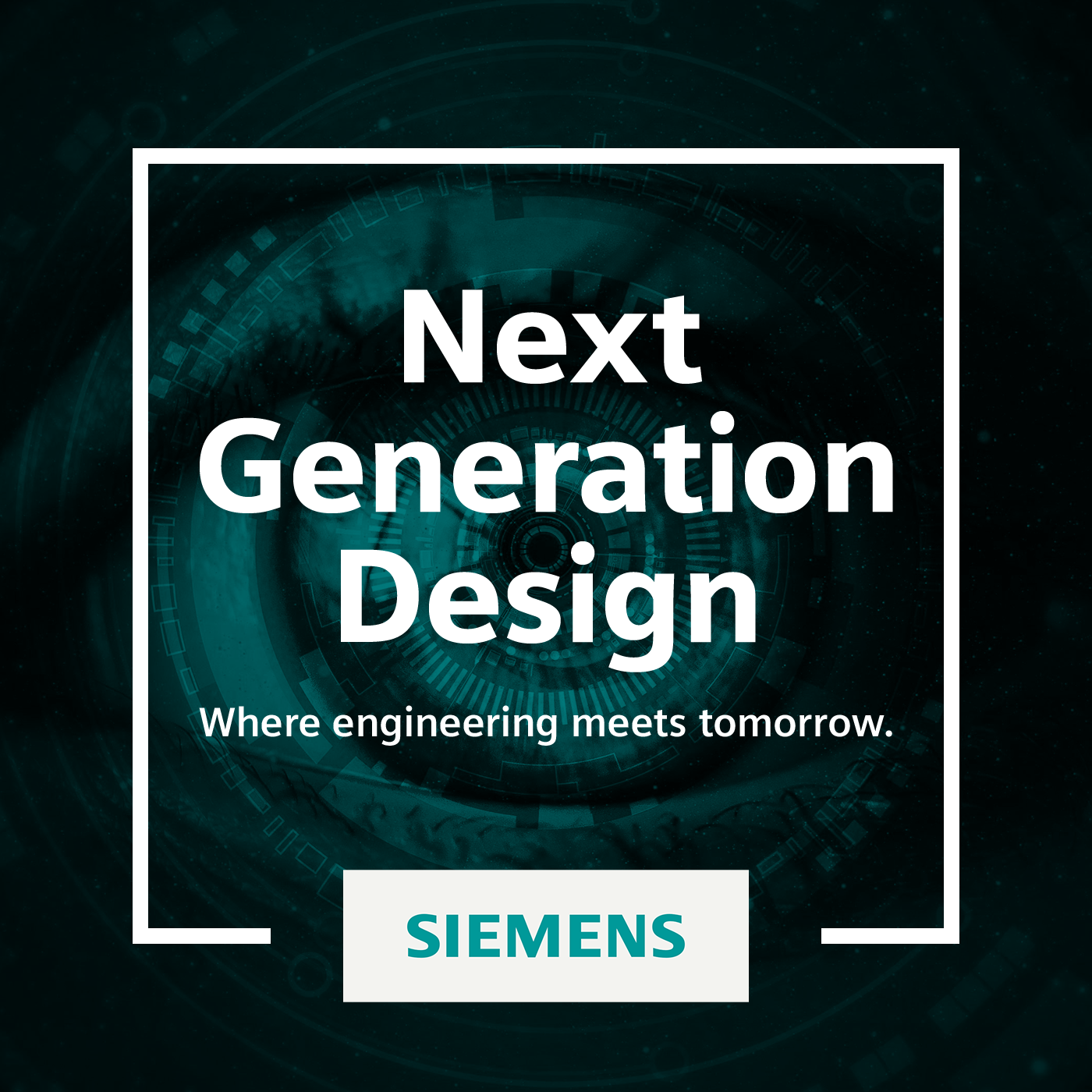
Next Generation Design Podcast
As product engineering tools continue to morph and expand at speeds human expertise may not be able to endure, Revolutionary design technologies that span beyond industry borders, will prove their necessity for companies looking to take over their markets in the future. What will the future of design technologies and machinery look like? What will your digitalization story be? Where engineering meets tomorrow.