The secret to Smart Manufacturing success | a partner’s perspective
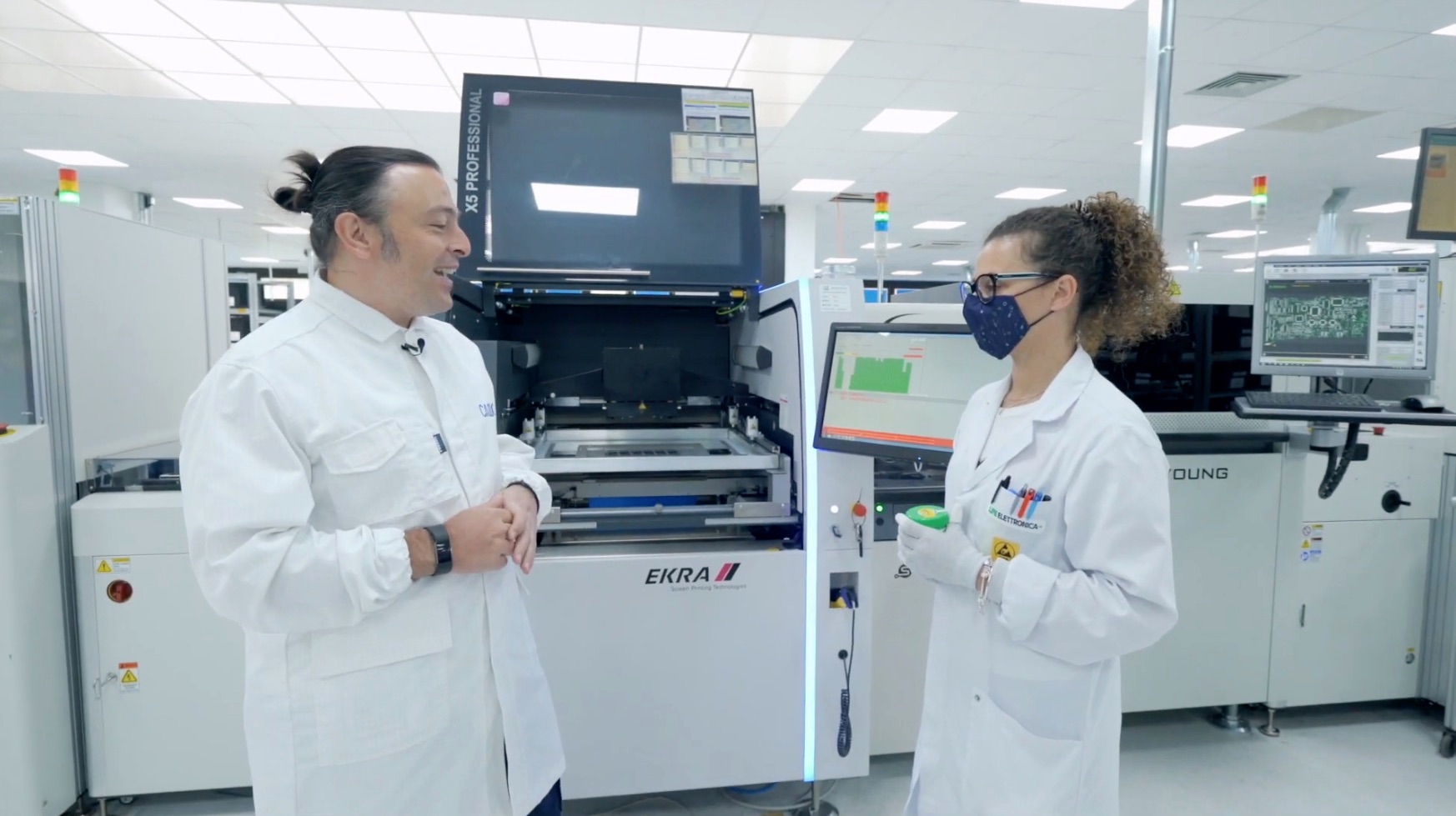
There isn’t just one but many components that contribute to finding a successful smart manufacturing solution while building a long-term relationship with your customer. These are always our goals at Cadlog, a platinum-level Siemens solution partner. One success that stands out is Life Elettronica, an Italian electronics manufacturing services (EMS) customer, which allowed us to implement many different solutions of our portfolio on the shop floor. Read how we approached the challenge and achieved success by implementing Siemens Digital Industries Software Opcenter IoT manufacturing technology.
Three main ingredients
The first and most crucial ingredient of this recipe is the customer. Life Elettronica’s owner, Mr. Riccardo Galli, is very committed to innovation and excellence. To him, “A modern EMS company aims to provide to its customers the highest quality, a proactive service, and full respect of delivery times and competitiveness. It is unthinkable to reach excellence without the help of technology at the shop floor level. This is smart manufacturing for us: to provide our operators and managers with all the mandatory data to make consistent, immediate and proactive decisions to achieve the highest levels of quality, time, delivery and efficiency. Data quality and time are everything.”
Siemens’ technologies make all the difference – and so do people. “We strongly believe in the value of our people, and we keep focusing on it,” said Galli. “We have talented people inside. We just need to create the best environment to enable them to express this great potential we already have.”
Then there is us, the partner, Cadlog. We are not only a provider of software but a real strategic business partner, able to follow step by step the processes with our customers to arrive at the final result of creating a smart factory. Cadlog helps its customers to understand themselves better, and to understand internal processes, flows, and bottlenecks better. Life Elettronica has fully recognized us in this role.
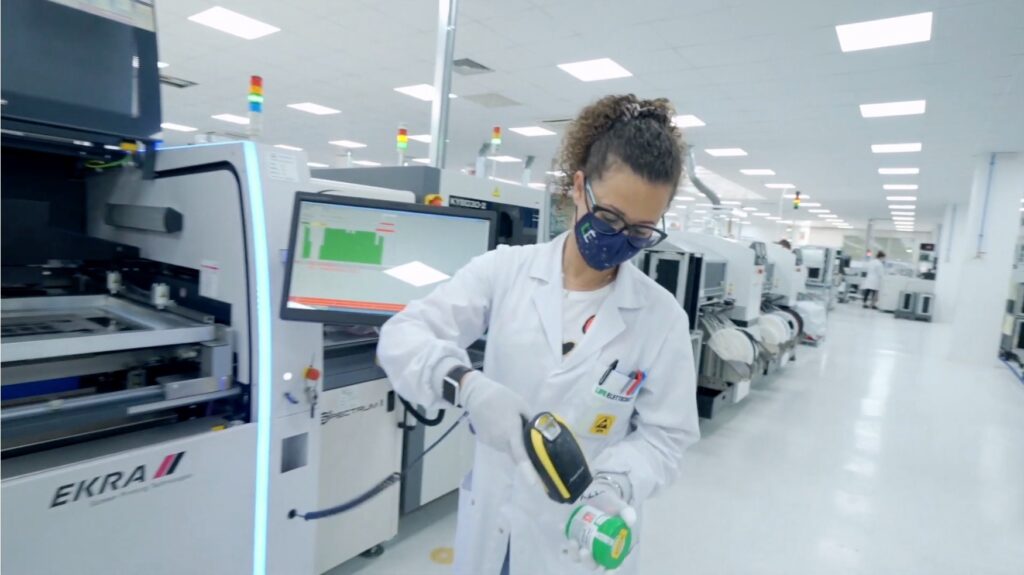
The requirements
The Life Elettronica project started in 2019 with an initial discussion analyzing the requirements and working together to define the two main goals of this Smart Manufacturing activity:
- Improving the incoming material registration process with a seamless process that directly brings all necessary information into the MES database.
- Production data analysis. At that time Life Elettronica collected data into different silos. It needed to break those silos and share all the necessary information regarding production machine tests, machine performance, performance monitoring, etc., within the company.
The latter has been one of the key aspects of the project because of Galli’s focus on improving the entire process. That is, to implement a smart manufacturing strategy that uses 100 percent of the company’s resources. including machines, materials, and people.
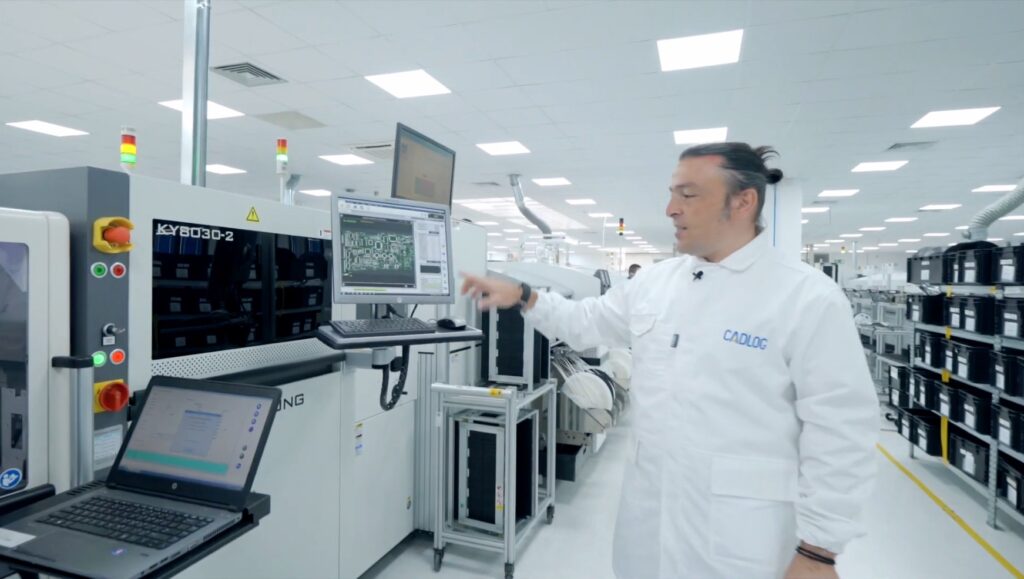
Start with engineering
For an EMS, everything starts with engineering with the data creation for new product introduction (NPI). “Every month we manage tens of NPIs coming from different sources like our R&D department and our various customers,” said Enrico Turri, a technical process engineer at Life Elettronica. “Currently, our first big challenge is to manage the different data formats and different data sets.”
“Thanks to Valor Process Preparation, we can define a standard workflow for each customer with a safer process. With this software we can create a model for the PCB assembly to define and create the documentation, the panel design and the stencil design.”
Enrico Turri, technical process engineer at Life Elettronica
Stencil design is an activity that allows the manufacturer to keep the paste printing process more under control, which is a very critical phase for Surface Mount Technology (SMT). Additionally, Life Elettronica runs Design for Manufacturing checks using Valor NPI to increase the reliability of the process.
Last year, Life Elettronica started using Valor BOM Connector for quoting. Quoting today is a challenge for an EMS because of the current shortage of components. With BOM Connector, an EMS can integrate the data of its ERP system with the data coming from its suppliers and customers. Nowadays this is really an added value application for an EMS like this, that receives a lot of requests of quotations every week.
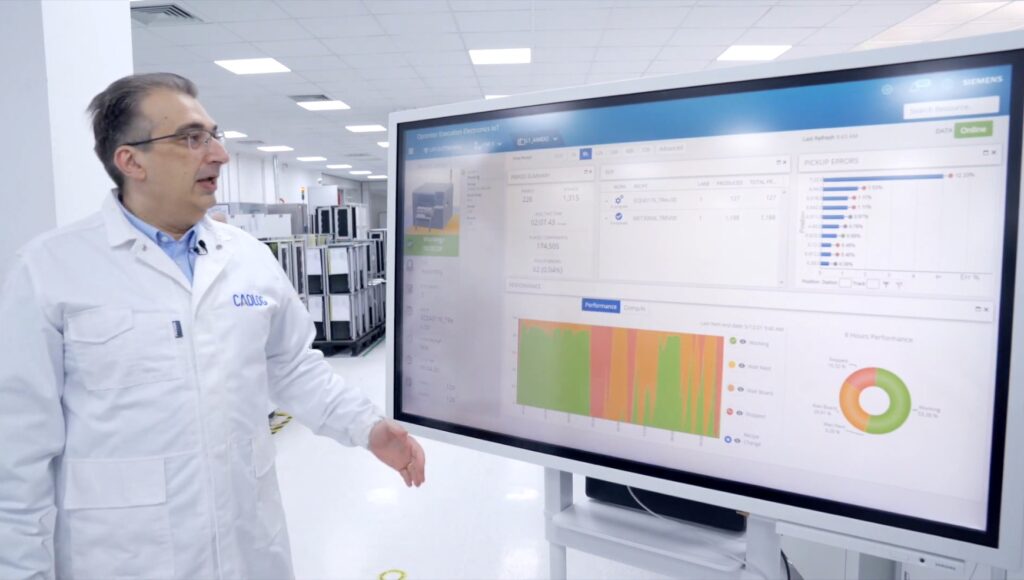
Big changes on the shop floor
On the shop floor, the Cadlog team deployed Valor IoT Manufacturing technology, including IoT devices like the system processing unit (SPU) and the data acquisition unit (DAU) to collect data from the machine for the different processes. Data are collected and used online for real-time information and to run analytics in the Opcenter Intelligence Electronics solution.
One of the areas where Opcenter Execution Electronics proved to be the most useful has been one of the incoming data. On a shop floor like that of Life Elettronica, each day, seventy part numbers are loaded for every single packaging and 200 different IDs are created. All the information related to incoming material like internal part number, manufacturer part number, date code, expiry date, quantities is directly entered in the Siemens Opcenter Electronics database. On the other hand, information about work orders is inserted through another interface to the ERP system. Now, according to Galli, the company doesn’t need a person dedicated to the incoming and moreover, the material is available for production as soon as it is delivered in its warehouse. “The result is an increase in the level of services we can offer to our customers and an improvement to our process,” he said.
Another key area for Life Elettronica is screen printing. It’s calculated that almost two-thirds of the defects after the soldering are related to a bad process of screen printing, due to missing excessive solder, thickness, and other factors. On the production line, the Valor Shop Floor Manager tool checks the soldering paste used during the screen-printing process, verifying the right product internal part number, the respect of the expiration date and the acclimatization time. If this check fails, Valor stops the entry of the board into the machine.
For an EMS like Life Elettronica, which has typically a low volume high mix production, it is important to manage the changeover of the product efficiently. Before the project working with Cadlog, the average setup time was one hour. After two years, the time was reduced to between 8 and 15 minutes. The collection of data made by Valor IoT Manufacturing from the different machines on the shop floor allows the company to control the SMT process, the setup time, and the change-over-time, and establish an improvement action if needed.
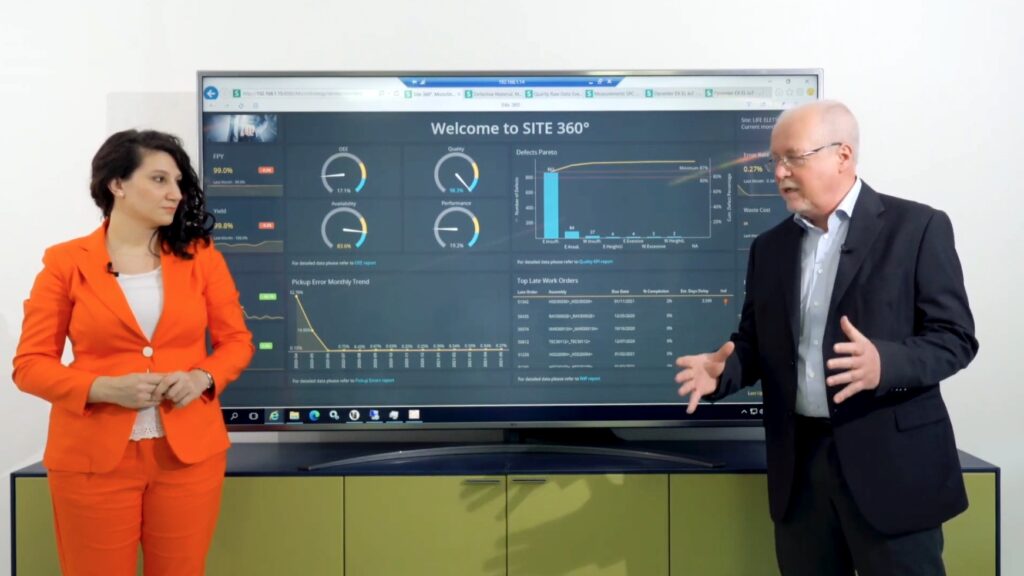
The role of data intelligence
Finally, data intelligence brought another big change in the way this company operates production. Today an EMS needs a magnifying glass that allows it to catch the performance trend details and transfer the company’s strategy to all employees with measurable objectives, initiatives, and activities. Valor provides a dashboard of performance indicators that deliver timely information to improve decisions, optimize processes, and plans. This allows Life Elettronica to work with a proactive spirit.
“Our commitment with the use of Valor is succeeding in monitoring critical business processes and activities, using indicators which generate alerts when performance falls below our target and analyze the root cause of problems by exploring information at various levels of details. The information must be timely and readable, of course. Furthermore, this information can also help manage people and processes, optimize the performance, and guide the organization in the right direction.”
Rosanna Iannacone, Assurance Manager at Life Elettronica
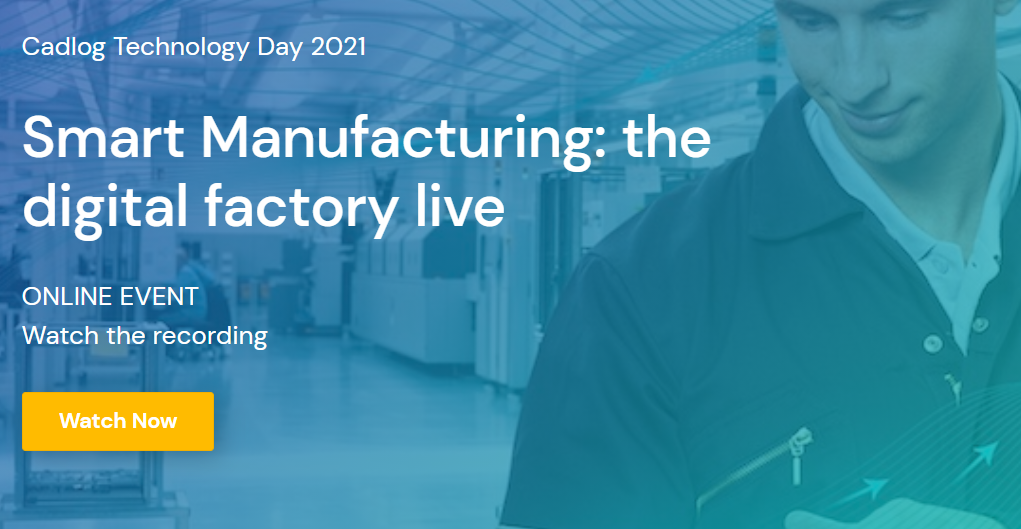
About the author
Alessandro Balboni is the Smart Manufacturing Product Manager for Cadlog Group. He manages the business development for the electronics manufacturing industry focusing on process engineering, manufacturing execution, manufacturing scheduling, analytics, and all Industry 4.0 collateral. With more than 20 years of experience in electronics design automation and professional services management working for large corporations, he joined Cadlog Group in 2013 and holds a significant record of deployments of Smart Manufacturing projects across Europe.