“Show me, don’t tell me” using full-size on-site augmented reality
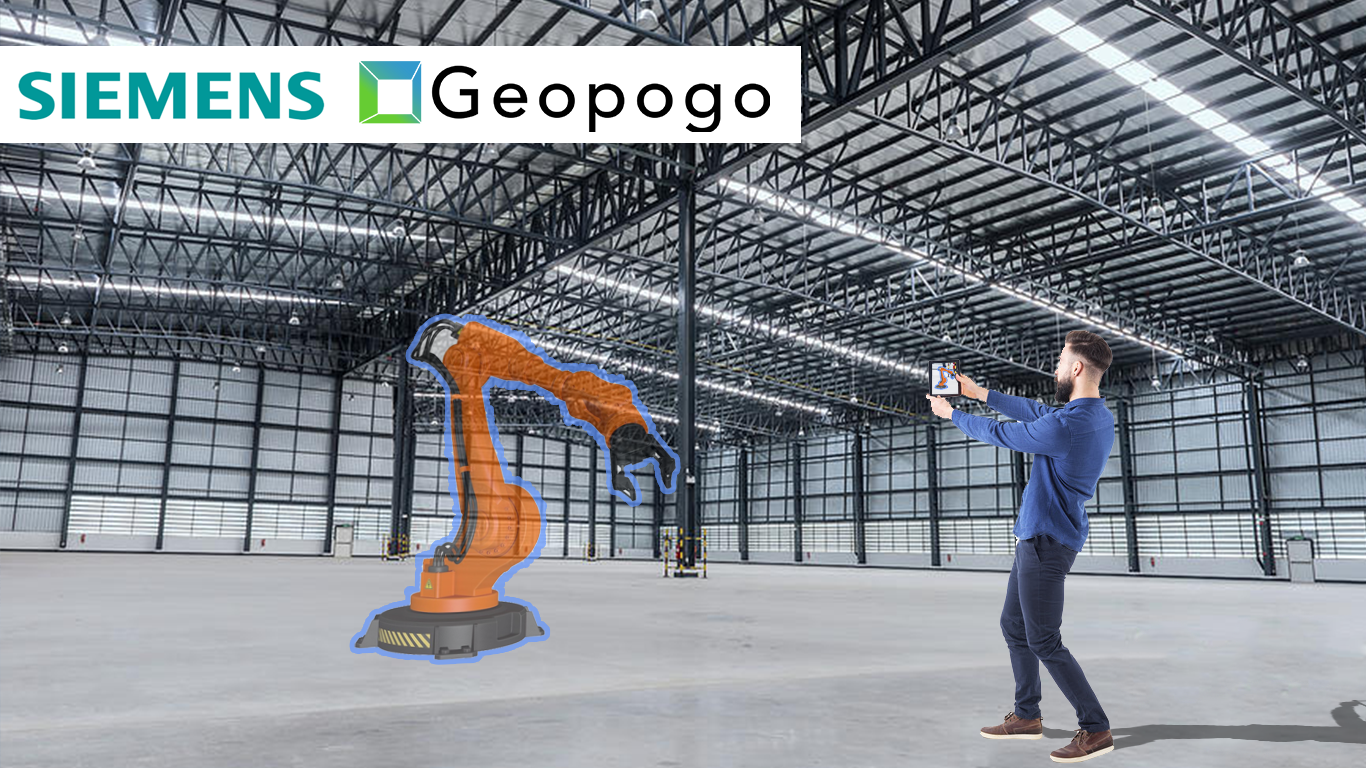
Have you ever heard the saying Show Me, Don’t Tell Me? Spatial design, whether for the interior of a factory, an airplane, the exterior of a new automobile or building calls for the knack of visualizing design ideas in 3D. Professional designers gradually hone their 3D visualization skills and follow a process to translate their ideas into 3D spaces and be able to explain it to their clients. The traditional design process has been updated in recent years with some new tools, like CAD modeling and virtual reality (VR). Unfortunately, the process is often still messier than it needs to be. We now have the opportunity to clean up the design process by bringing Augmented Reality (AR) into the design workflow.
Geopogo to the AR rescue
As a building architect, I have led my team at Geopogo to demonstrate the power of full-size on-site AR to clean up the design and construction process. This new technology allows project stakeholders for the first time to experience the design on-site throughout the design development process. Unlike VR, AR can be experienced on a mobile device rather than with a headset. Additionally, AR has the advantage that it automatically integrates the existing exterior or interior site with the proposed design.
VR requires a much larger 3D model to be constructed if all current conditions are to be included to provide the necessary context.
The way that our AR models are built is simple. We start by taking a few minutes to import a Building Information Modeling (BIM) model, such as an Autodesk Revit file into our software platform and convert it to a Unity-based Geopogo model. Then we use our iOS App to upload the Geopogo model to an iPhone or iPad (or headset if preferred). With the iPhone or iPad (or headset), the model can be set precisely on site for review and approval.
A real-world AR example
A striking recent example of how AR works to clean up the design process is the on-site AR model we implemented for one of the largest global tech companies. The company was set to begin the interior construction of a large commissary facility in Silicon Valley. Despite all of the drawings that had been carefully reviewed and approved by the company’s staff, the company wanted to be confident that the design would work as intended.
When the staff was able to walk through the AR model of the proposed facility in full size with all of the equipment and casework, they discovered for the first time many essential changes that were needed for efficient operational functionality. The company was then able to make the design changes before construction began and proceed with confidence. The company’s project manager calculated savings of $250,000. The company otherwise would have been forced, as the problems were discovered during construction, into mid-construction rework involving utility line revisions and the relocation of equipment and casework. On their next project, the company will use AR through the design process to largely eliminate design revisions as well as construction rework.
AR can help save time and money
Rework has been calculated by McKinsey to be 9 percent of all construction costs, or approximately $1 billion wasted every day in the US. It can largely be avoided simply by reviewing a full-scale on-site model before construction. Before AR, this had to be done with physical mockups, which were expensive to construct and limited in scope, so it was typically not done at all.
What does this all mean for general manufacturing? For the spatial design inherent in the aeronautic, factory, and nautical interiors, it means that there is now a compelling opportunity to present proposed designs clearly to clients, test them in full size as the plan is developed, and eliminate a lot of time-consuming design revisions and costly rework. The savings in time and money allows projects to be delivered faster at a lower price, with more profit. With today’s pandemic-driven economic pressure, the time to start using AR is now. Show me, don’t tell me.
Dave Alpert, MBA, FAIA, LEED AP is the CEO and Co-Founder at Geopogo and an award-winning architect who is now solving design and construction challenges with Geopogo’s AR software. Dave leads a team of designers, software engineers and data scientists. The team works out of the Berkeley SkyDeck technology incubator, which integrates university-driven technology innovation with Silicon Valley investment.
Geopogo is a Siemens Frontier Partner. The Siemens Frontier Partner Program helps early-stage technology startups develop and bring to market breakthrough solutions for 3D printing, robotics, and augmented and virtual reality. Frontier Partners receive access to industry and domain expertise, our portfolio of software solutions, and resources to help companies innovate, scale, and shape the future of product design and manufacturing.