Ensuring functional safety in combo-box architecture
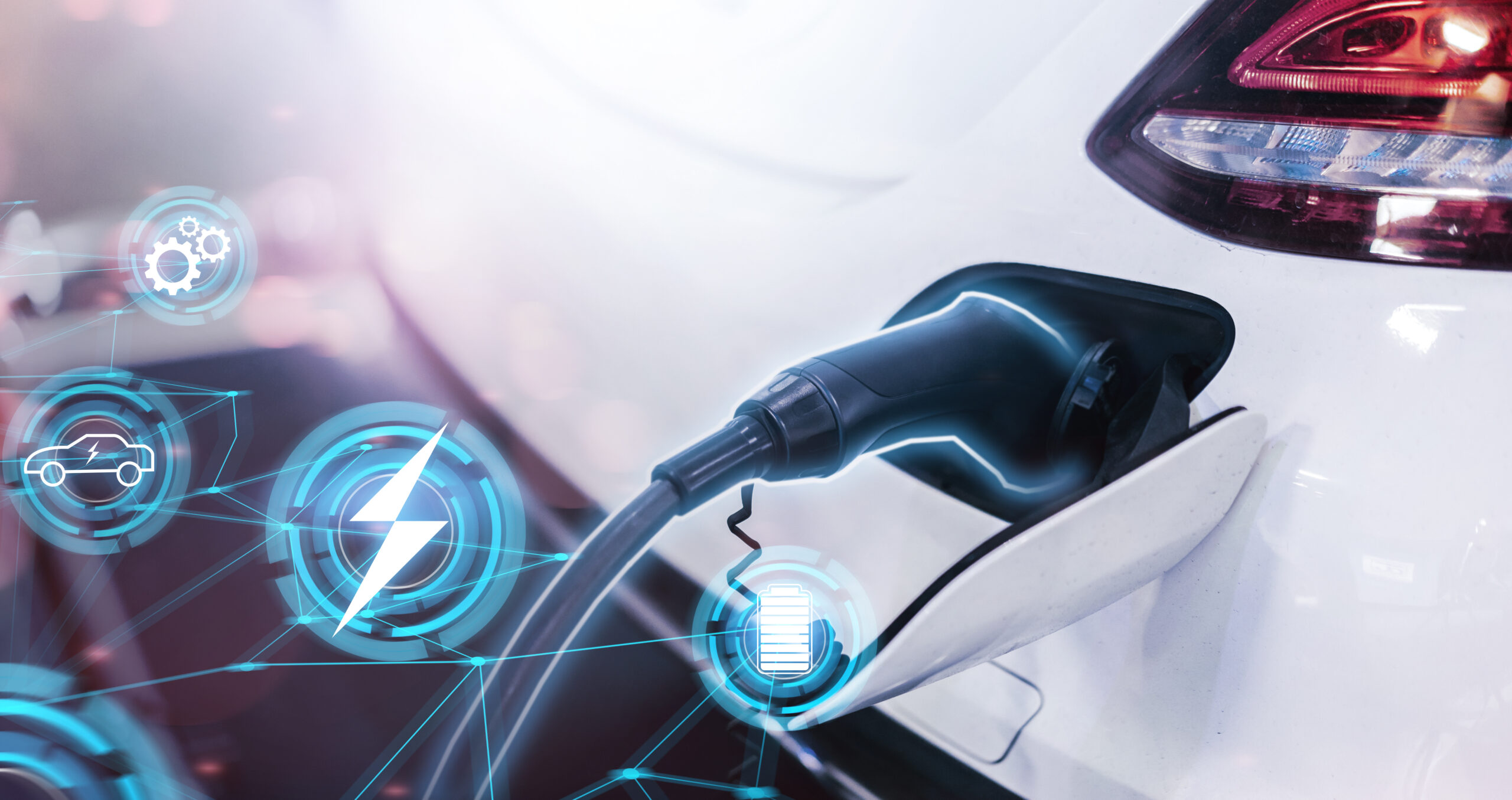
When it comes to increased adoption and popularity, Electric Vehicles (EVs) are on a roll. This is fueled by the public’s mounting interest in combating the impact of climate change, technology advancements and reduced costs. The market for EV is expected to reach a CAGR of 38% by 2024. In fact 450 new EV models will be launched in 2022. Bloomberg New Energy Finance predicts that EVs will reach 10% of global passenger vehicle sales by 2025. After that, predictions continue to 28% in 2030 and 58% by 2040. Add to that the Biden Administration’s commitment to advancing EV infrastructure as part of its massive new infrastructure bill, and we’re looking at some serious momentum.
But the industry still faces a big challenge – extending driving range. To maximize EV performance, all six components of an EV powertrain system must work in sync:
- The DC converter
- Inverter
- E-motor
- Charge control
- On-board charger (OBC)
- Battery Management System (BMS)
Frankly, that’s not as easy as it sounds. There are significant architectural challenges and considerations at play.
While traditionally, all these components have been housed in separate controllers, the weight of packaging materials, redundant hardware and wiring for each separate component can have a significant impact on overall vehicle performance. That’s why manufacturers are beginning to leverage integrated powertrain design, or what’s known as a “combo box” architecture.
Challenges of the combo-box architecture
In a combo box, two end-equipment components – for example, the OBC and the DC-DC converter – are combined and share resources. This can include, for instance, the control and cooling systems and the power stage. Integrating powertrain components in this fashion enables a more compact design. This in turn can reduce maintenance, improve power density and reliability and optimize costs.
However, there are some considerations and challenges to the combo-box design. When systems are integrated, they may fail to meet certain requirements for noise levels, manufacturability, and functional safety. Critical system components such as the BMS and the Inverter are subject to Automotive Safety Integrity Level (ASIL). This is a risk classification system defined by the ISO 26262 standard for the functional safety of road vehicles.
For example, the BMS must keep the EV’s battery functioning properly, and it does this by monitoring the charge, health, environment and other parameters, then taking action to correct any issues or isolate malfunctioning battery cells. The Inverter is essential for driving the E-motor and determining the EV’s speed. If something goes wrong with either of these components, drivers and anyone on the road are at risk. To that end, they must be fail-safe.
And so, when you combine any component that must be fail-safe with another component in a combo box, ASIL qualification is required. To achieve this level of functional safety, a microcontroller and an AUTOSAR stack with multicore support and AUTOSAR basic software (BSW) are essential.
Take the multi-core approach to ASIL compliance
Siemens’ Capital VSTAR is an AUTOSAR environment for integrating, testing and analyzing software for EVs that covers the entire AUTOSAR development cycle. The solution supports both arms of AUTOSAR’s multi-domain, layered system model, integrating into MCAD, PLM and ALM systems to deliver truly integrated system development. Because it’s a multi-core solution, Capital enables software distribution to address performance and safety challenges during EV system design.
In a combo-box design, Capital VSTAR distributes the functions of both components across multiple cores. For instance, when combining the OBC and the DC-DC converter in a combo box, you can place the OBC in core 0 and the DC-DC in core 1. That way, it’s easy to make a component fail-safe to meet ASIL requirements:
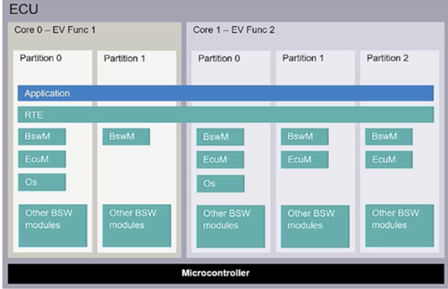
Additionally, the multi-core capabilities help to reduce the CPU load resulting from inter-core communication by splitting the COM modules between the cores and moving the SWCs, MCAL and other relevant components to the same core. In this way, Capital VSTAR addresses performance issues, reduces vehicle weight, and optimizes costs, all while enabling ASIL compliance.
Capital VSTAR supports functional safety use cases for all ISO 26262-defined levels (ASIL A to D), as well as mixed critically integrations though software partitioning.
Tackle the challenges of EV software development with confidence
As consumer expectations for extended driving range, maximum performance and low cost continue to drive innovation in the EV market, new design and architectural challenges will emerge. Siemens’ Capital VSTAR is at the forefront of addressing these challenges.
Read our whitepaper, “Overcoming the Challenges of Electric Vehicle Embedded Software Development,” to learn how Capital VSTAR helps to enable system engineers to work within an AUTOSAR-aware environment and addresses challenges around performance, security, functional safety, and charging requirements during EV systems design. Additionally, visit www.siemens.com/autosar for more content and resources about our automotive solutions.