Solving Electrical Distribution System (EDS) Design Compliance Challenges with Siemens Capital Analysis
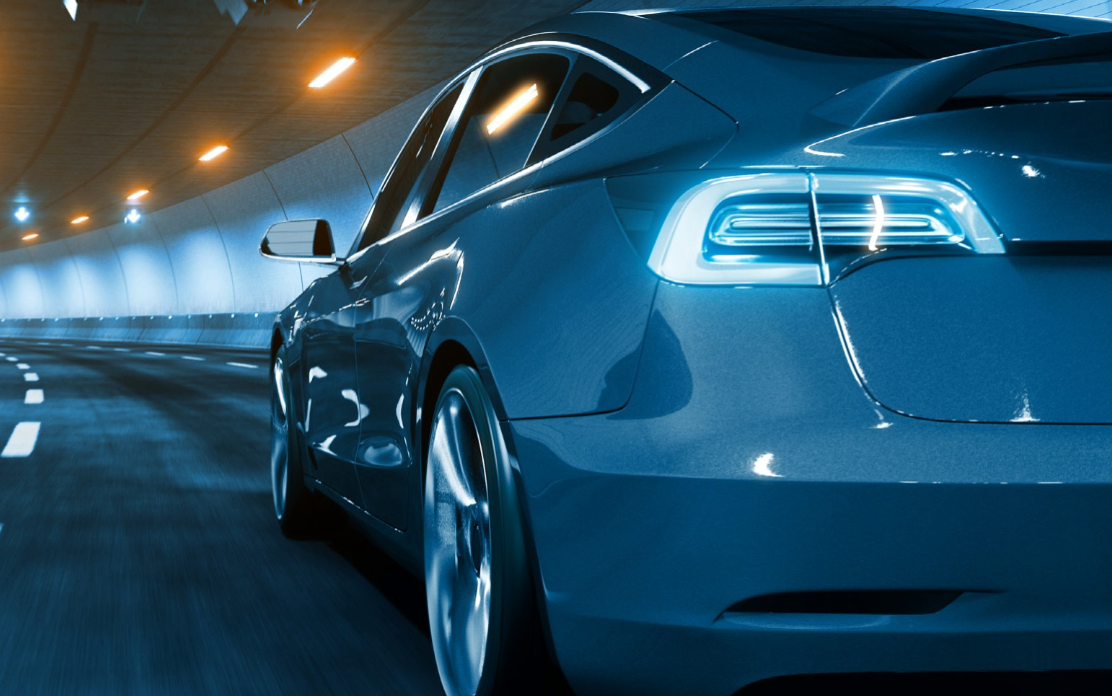
Siemens Capital Analysis empowers EDS engineers to improve their designs and eliminate rework late in the design cycle.
Ensuring safety and cost-effectiveness in modern vehicles is becoming increasingly difficult. Market demands for performance, sustainability and secure personalized services are prompting automotive industry investments in more complex and electrified solutions. The key challenge for automotive OEMs and suppliers is to guarantee the safety of new generation products that feature advanced automated systems and intricate power distribution architectures.
However, the traditional approach to verifying electrical schematic connectivity and analyzing fuse and wire sizing under stress or failure conditions is often a laborious, manual process. This manual approach can be a significant bottleneck, increasing the risk of errors and non-compliance. And this is a serious problem: According to the National Fire Protection Association report released in 2020, most highway vehicle fires were related to electrical distribution design non-compliance issues.
What’s the fix? Capturing EDS compliance expertise into an automated analysis engine, and embedding it into a model-based design environment. In doing so, EDS engineers gain access to insights and feedback early in the design cycle, enabling them to improve design accuracy and ensure compliance with design and safety requirements.
In this post, we’ll take a look at how Siemens Capital Analysis, a powerful component of the Capital software suite for electrical and electronic (E/E) systems development, empowers EDS engineers to improve their designs and eliminate rework late in the design cycle.
Late-stage rework is costly
Developing electrical distribution systems is a complex process, with a lot of moving parts. Traditionally, much of the design analysis has been manual – inspections of physical prototypes occur late in development, resulting in late-stage rework, which is expensive and time-consuming. Correcting issues this late in development can cause massive delays and put the whole program at risk.
Consider an alternative approach – one that avoids last minute changes by shifting design analysis left, enabling iterations early in the development lifecycle. Taking this approach, you can detect errors and bugs prior to finalizing schematics and physical prototypes, when they’re easier and less expensive to fix. The illustration below shows what this might look like:

If compliance engineering expertise can be used to automatically check designs against defined rules and requirements, EDS engineers would be able to analyze and iterate continuously within the design environment, and ensure their designs are compliant before moving into the prototyping stage. The benefits of this approach include reduced costs, improved quality, lower risk and faster time-to-market.
Enter Capital Analysis – a compliance engine from Siemens embeds directly into the Capital Design environment. Let’s take a look at how it works.
Catch issues early with Capital Analysis
Capital Analysis helps EDS designers achieve exhaustive and automatic compliance checks throughout the design and validation lifecycle.

Here’s how the solution works across three stages of design: Connectivity checking, Fuse Selection and Voltage Drop Analysis:
Connectivity checking
During the schematic design phase, it’s critical to ensure there are no missing connections for any of the vehicle’s configurations. EDS compliance experts typically reference connectivity and configuration requirements from several files in different formats. They must manually analyze the design, which can take up to several months – and even the most skilled experts are at risk of missing something.
Capital Analysis works automatically within the Capital Design environment to check connectivity between input and output devices, and ensure the configuration definitions meet the requirements. Within the same schematic design environment, users can initiate the Capital Functional Verifier to assess their designs. This tool loads the design’s connectivity and tests it against a predefined logical sequence. Users have two options for simulation:
- Manually toggle switches to verify simulation accuracy, quickly identifying and correcting issues like logical disconnections.
- Run comprehensive automatic checks and analyze the generated reports, setting parameters for switch and component failures they wish to test. This method evaluates all potential combinations and checks connectivity against the logical requirements, highlighting any concerns for reevaluation.
In either instance, EDS engineers can efficiently identify and address any design flaws before progressing to the physical design.
Fuse selection
Once the project moves to the physical design phase, EDS engineers must make sure the fuses protect the wires in worst-case scenarios. Traditionally, fuse selection involves another manual analysis where compliance experts must analyze the wiring current results, review the components specifications and functional requirements, and recommend design changes.
With Capital Analysis, all the manual work is eliminated. The solution automates analysis by incorporating design and manufacturer data, conducting stress tests and providing design recommendations, helping users to verify and correct their designs in a much more efficient way.
Voltage drop analysis
Let’s move on to another typical task in physical design: voltage drop analysis. Typically, the EDS group must analyze a significant amount of data manually at this stage, including wire thickness, impedance and current. The goal is to ensure that the connectivity design maintains sufficient voltage for all devices to operate within specified input voltage ranges, especially in worst-case scenarios.
Using Capital Analysis, EDS engineers can dynamically toggle switches to simulate specific scenarios and observe the effects on voltage. Alternatively, they can leverage automation within the tool to identify the worst-case scenarios where voltage drops could impair component function. To do this, users simply specify which parts of the circuit to examine by selecting the appropriate switches, and the Capital Components Sizer processes various scenarios and produces a detailed report highlighting any voltage compliance issues. This helps to pinpoint which components fail under specific conditions and make necessary design adjustments to meet voltage requirements.

Design with confidence
Capital Analysis enables engineers to continuously analyze, iterate and improve on electrical distribution designs within the Capital Design environment to ensure compliance, and enhance efficiency and accuracy. By enabling early detection and resolution of design issues, the tool empowers engineers to make informed decisions that not only cut costs but enhance product safety.
In a recent webinar, Chenyu She and Vivi Sun, Technical Product Managers at Siemens Digital Industries Software, provide an in-depth discussion and demo of how EDS designers can use Capital Analysis as part of their Capital Design environment to ensure design correctness and compliance early in the design cycle. Watch the webinar on-demand.