What’s new in Simcenter SPEED, Simcenter Motorsolve, and Simcenter MAGNET 2022.1
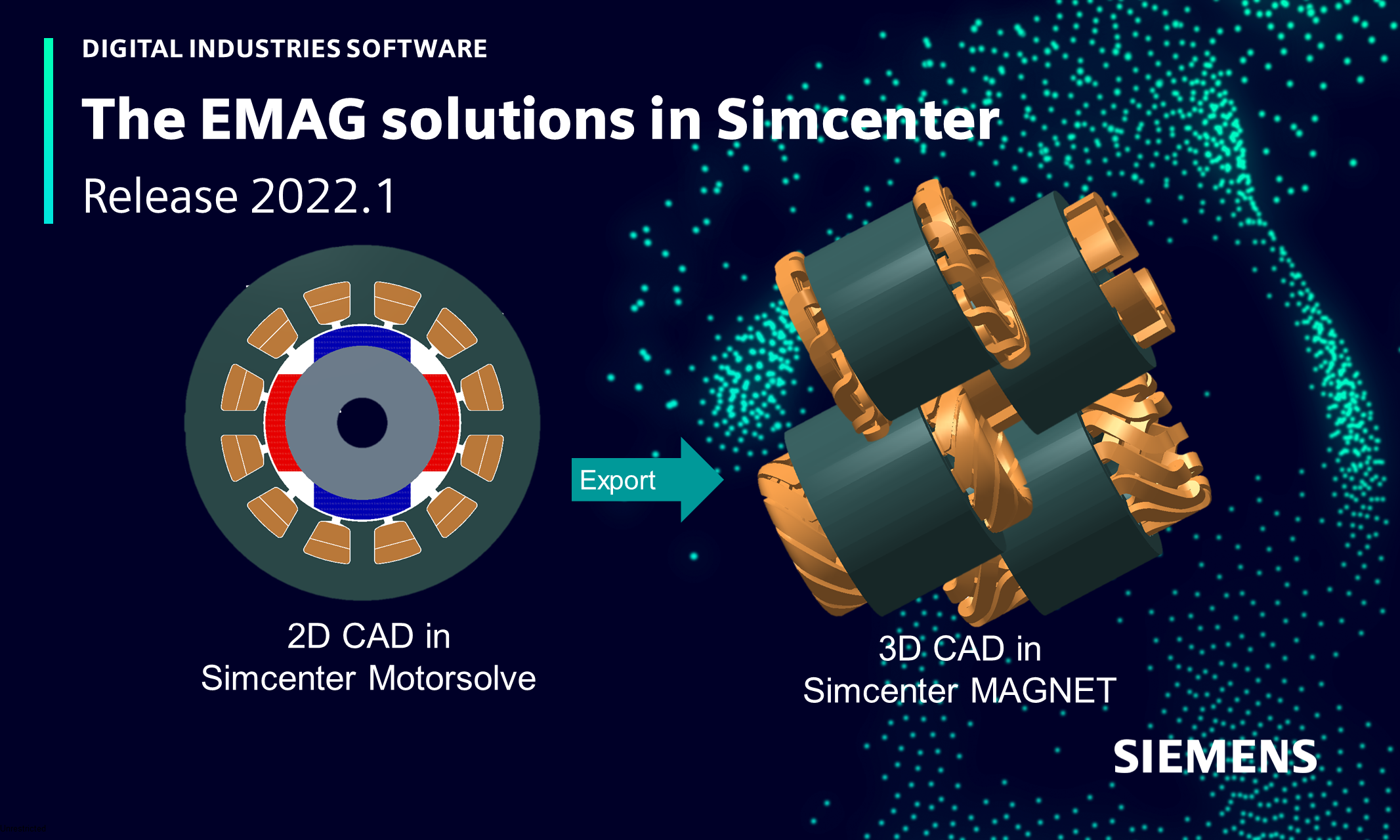
The new updates to the Simcenter electromagnetics (EMAG) solutions greatly accelerate your ability to model complex problems with minimal time and effort. These updates further integrate the Simcenter EMAG solutions together so that the speed benefits of the 2D solutions can optimize the process of a user that needs the physics in a complete FE solver.
The new improvements to Simcenter SPEED, Simcenter Motorsolve, and Simcenter MAGNET will help you:
- Model the Complexity.
- Go Faster.
- Explore the Possibilities.
- Stay integrated.
Model the Complexity.
The improved DXF overlay in Simcenter SPEED allows you to automatically see updates to your parameters. With just a few clicks and no DXF reloads, you can create a facsimile of their motor from a template.
The new Step-Skew option for rotor or stator topologies in Simcenter Motorsolve more accurately models the possible manufacturing processes for skew. This new skew method simulates a more accurate “cogging torque.”
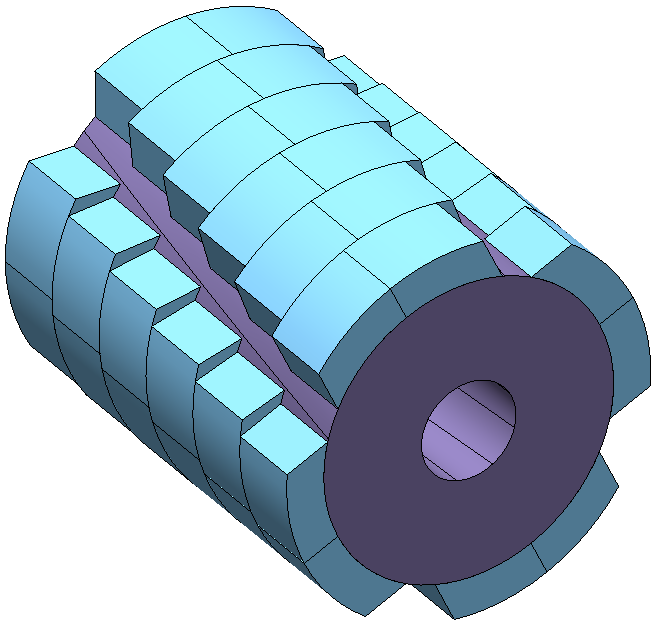
Go Faster.
Start your software and build a new motor design in significantly less time. Creating a new motor is 37% faster due to Simcenter Motorsolve’s response time updates.
Explore the Possibilities.
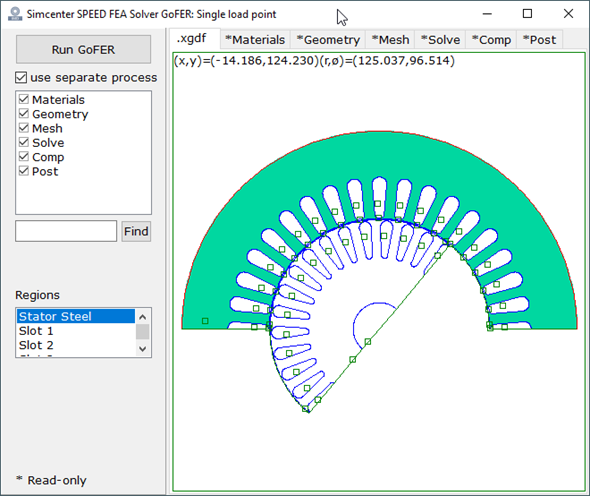
The new preview mode for the FEA calibration in Simcenter SPEED allows you to view your model and make adjustments before submitting the job to the solver.
Eddy currents can induce a breaking effect that can be both desired and undesired. Therefore, it can be essential to model the impact of eddy currents in Simcenter MAGNET.
Accounting for motion-induced “eddy currents” in actuators was not available in Simcenter MAGNET’s previous ROM technology but is now in this latest release.
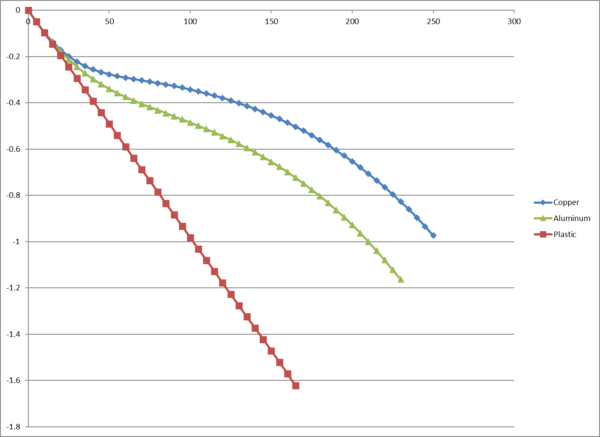
Stay integrated.
It is now possible to complete an EMAG data exchange for computational fluid dynamic (CFD) thermal studies with the improved data file exchange. To achieve this integrate, Siemens made across the EMAG software family including but not limited to:
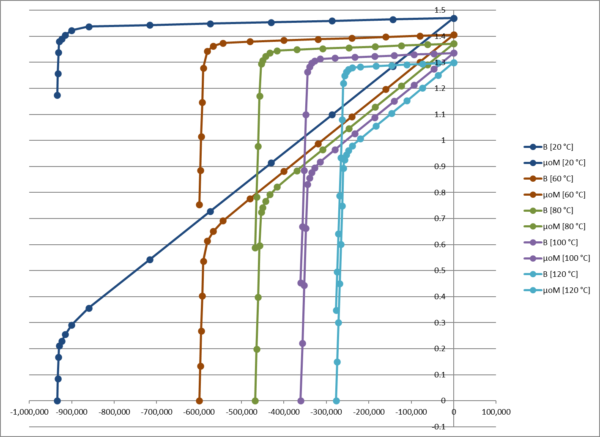
Temperature-dependent data exchange for materials is now available in Simcenter SPEED GoFER’s for Simcenter MAGNET and Simcenter STAR-CCM+. This is helpful because, for the best FEA results, appropriate temperatures and temperature-dependent material properties for each component of the motor are essential.
Similarly, additional coil-side phase winding descriptions have been added to Simcenter SPEED PC-IMD, allowing you to define more detail in your simulation and provide crucial parameters for a Simcenter MAGNET and Simcenter STAR-CCM+ simulation.
Updates that improve your motor’s portability into Simcenter Star-CCM+ are not limited to Simcenter SPEED anymore: the xgdf data exchange format to STAR-CCM+ can now be written from Motorsolve as well. Additionally, the new end winding exports now available in Simcenter Motorsolve make it possible to export Simcenter Motorsolve motors including detailed end winding to Simcenter STAR-CCM+ and MAGNET 3D.
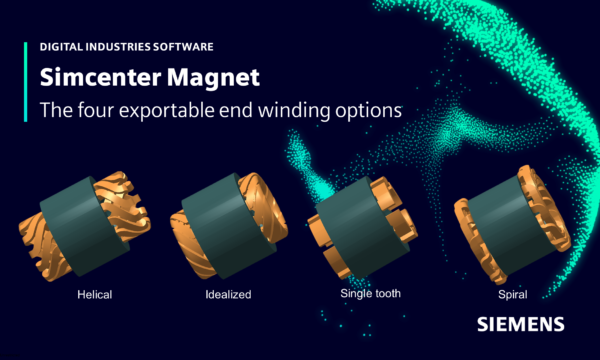
Video Demo
The updated end winding portability allows the user to benefit from the easy-to-use and rapid design tools in Simcenter Motorsolve and then export the results into Simcenter STAR-CCM+. In this video, you are shown how easy it is to modify your end winding design (including Idealized, Sprial, Helical, and Single tooth end windings) and export your design to STAR-CCM+.