Stop and listen before you build it: Virtual Prototype Assembly and NVH simulation in Simcenter Testlab
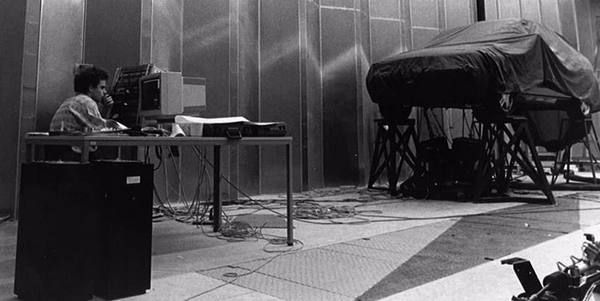
“Things are not as they used to be,” my grandma used to say. And boy, was she correct. Back in the day it was unimaginable to plan a vehicle release without at least a couple of fully tested prototypes.

But what is the reality for NVH engineers now? Not only is their access to the prototype significantly reduced, more and more often they are expected to predict (!) the results based on the availability of the components.
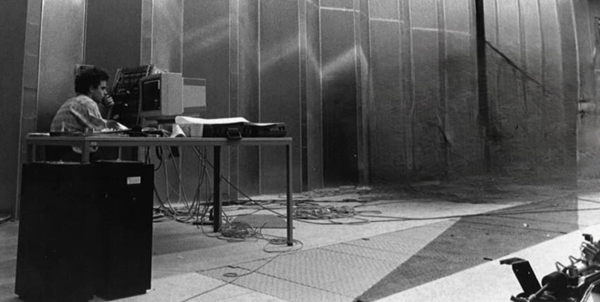
Luckily for Ludo, and all the NVH test engineers that came after him, the 2406 Simcenter Testlab release can help deliver high quality products to the market faster by combining test and simulation results for early NVH predictions.
Simcenter Testlab Virtual Prototype Assembly 2406
With the new update, you can now increase the analysis detail level by saving the connection responses, allowing for more accurate and comprehensive insights. Additionally, utilizing time domain loads, it is possible to perform auralization and post-processing enabling you to fully immerse yourself in your Virtual Prototype by providing a realistic experience. Furthermore, you have the flexibility to define precisely what you want to save from your virtual prototype, ensuring you get the exact information you need. And, with the auralization of your VPA model, you can now simulate and experience different driving conditions with the Simcenter Testlab NVH Simulator offline, further enhancing the realism and accuracy of your prototypes.
Let’s dive in and explore the exciting updates and enhancements this release has to offer!
Characterize
In the context of electrification in the automotive Industry, it is noted that the sound signature of electric vehicles (EVs) is significantly different than vehicles equipped with internal combustion engines (ICE). The EV sound profile is dominated by complex high-frequency tonal orders. As these orders are not centred around 0 Hz, the negative pair of the orders is also present. Starting in the latest Simcenter Testlab release, the Transfer Path Analysis (TPA) workbook in Simcenter Testlab will support offset and negative orders as operational conditions for the TPA analysis, expanding the range of detailed capabilities of the application.

The ability to merge data from both test and simulation is a crucial aspect of virtual prototyping. In order to accurately represent the dynamics of components at connection points, it is essential to properly define the interfaces of these components. On the test side, a widely used technique is Virtual Point Transformation (VPT). VPT has been a part of Simcenter Testlab since the 2022.1 release, and in the 2406 release, we have introduced additional features to enhance the calculation and analysis of this transformation.
With the help of the virtual instrumentation, it is possible to create virtual points based on the CAD geometry. Additionally, it allows for the assessment of the overall and detailed quality of each virtual point’s definition. The success of defining virtual points and acquiring frequency response functions (FRF) plays a crucial role in the results of the substructuring technique employed in virtual prototyping.

Store and exchange
As Simcenter Testlab Virtual Prototype Assembly is implemented in the product development process, several components start to be characterized. To correctly handle all this information locally, in this release a new local library concept is introduced.
With this new addition, users will have the capability to create libraries, making it easier to manage their VPA components. Now, one can conveniently share the libraries with colleagues through the import and export function. Additionally, Simcenter Testlab offers annotation capabilities to further improve the component description, allowing for enhanced collaboration and understanding among team members.
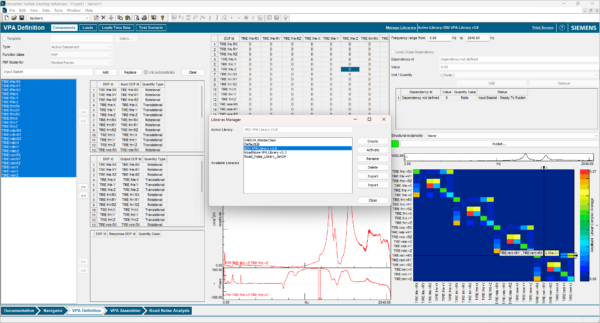
In the context of component modeling, in this release, we expanded the possibility of modeling the loads, with the introduction of loads in time domain. Users will be able to save (or publish, in the VPA terminology) the load components directly in the time domain. This will allow users to perform virtual assembly and prediction directly in the time domain, allowing them to subjectively evaluate the results at target locations and opening the doors for further processing.

Furthermore, for the connector components, it is known that the dynamic stiffness of these resilient components changes with some parameters, such as pre-load, temperature, and degradation over time. Hence, it is now allowed to create and publish connectors with multi-dependencies. The mounts or bushing elements can be created with dynamic stiffness (in function of frequency) per different dependencies, e.g., pre-load.

Assembly
A virtual prototype can generate a large amount of data which can lead to confusion and wasted time as users try to calculate and save data that may not even be of interest to them. To address this issue, VPA assembler offers the option to selectively choose which results they want to save during the assembly definition, streamlining the process and ensuring that only the most relevant data is saved.
For multi-level assemblies, where passive components are present, it is possible to select which interface the data will be saved or both. It is also possible to save the assembled FRFs by selecting the desired interface.
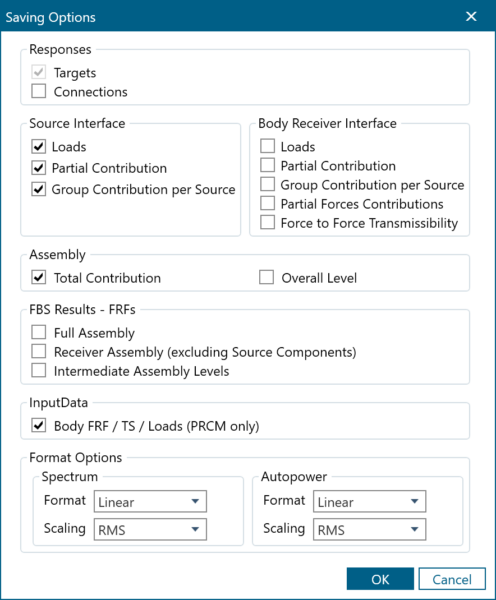
Prediction, analysis and listening
In addition to analysing target locations, it is crucial to consider the various interfaces of the assembly and how vibration levels will respond to the applied loads. To address this need, we have introduced a new feature in this release: the ability to calculate responses at the connection levels. With this enhancement, users can thoroughly analyse and diagnose the assembly at each connection level, taking into account load and transfer functions. Furthermore, it enables the analysis of filtration caused by isolation.

The release of Simcenter Testlab 2406, includes the first release of the Simcenter Testlab NVH Simulator. This first release lays the foundations for the importing of Virtual Prototype Assembly results in the NVH Simulator with the main objective of generating time data from different driving profiles and conditions.
The NVH Simulator will allow the engineer to further develop the prototype with subjective analysis capabilities with Audio Replay and filtering embedded in Simcenter Testlab Neo and the sound quality post-processing capabilities of the process designer.
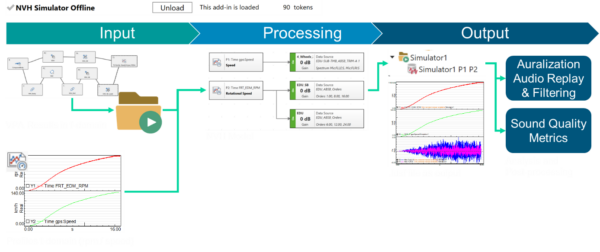
This closes the loop of experiencing a virtual prototype from the components evaluation, the assembly, and the objective and subjective analysis.
Are you not yet convinced if Virtual Prototype Assembly is right for you? Then listen to what the participants of the 2024 Component-based TPA and Virtual Prototyping Masterclass have to say: