The power of a multi-purpose digital twin
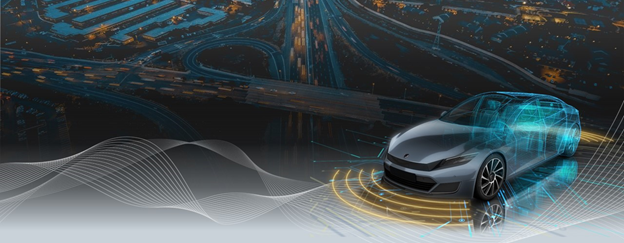
This article is based on an interview with Theo Geluk, RTD Manager for Simcenter Engineering and Consulting at Siemens Digital Industries Software.
The world has gone digital
We are living in an increasingly digitalized world. Today, to buy a new car, you can view options online and pick your favorite without ever stepping foot in a dealership. To order food, you can view local restaurants’ menus online and order with the tap of a finger. To see how a new sofa will look in your home, you need only point your phone’s camera at the desired location and you’ll be able to preview multiple options instantly via virtual reality. Almost everything that once required physical interactions can now be done virtually.
Digitalization in the auto industry
The same digitalization trend is occurring in the automotive industry. Building physical prototypes is time-consuming, expensive, and difficult to perform at scale. There are three trends driving the digitalization of automakers:
- The push for simulation (CAE) driven design
- Model-based development to enable early stage full system performance assessment
- The increasing complexity of vehicle variants
The push for simulation driven design
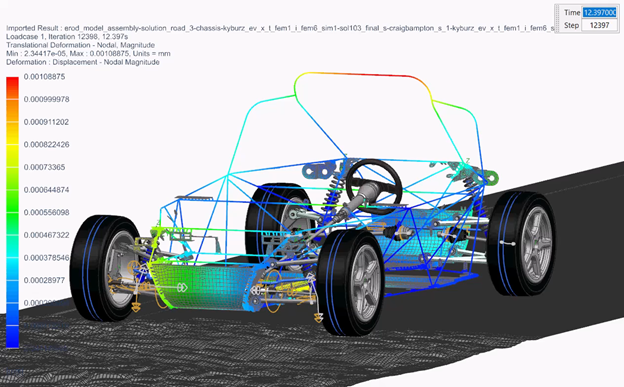
Now more than ever, automotive companies are demanding simulation-based solutions. OEMs and their suppliers need to reduce the number of physical prototypes and transition to building, refining, and testing their products virtually.
Model-based development to enable early stage full system performance assessment
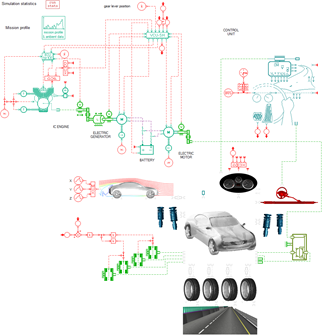
It is becoming increasingly important for companies to be able to assess the performance of a system or component earlier in the development cycle. Model-based development allows engineers to analyze such component or sub-system behavior not just on component level, but also as integrated part of the whole system, on full vehicle performance level.
Increased complexity in vehicle variation
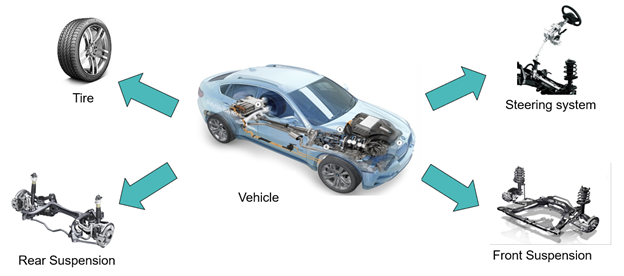
Today there is an unprecedented number of options for vehicle design, including suspensions, body layouts, drivelines, and more. Additionally, OEMs often offer 5-10 vehicle models each. Testing and validation of each variation on every vehicle model poses a significant challenge for OEMs and their suppliers, both in terms of timing and associated costs.
Enter the multi-purpose digital twin… for any car
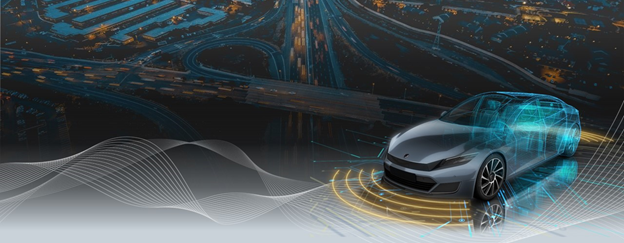
Thanks to advances in the CAE world, it is now possible for OEMs and suppliers to meet these challenges head-on by building a digital twin of their products. However, straightforward access to a digital twin of a full vehicle can still be a challenge. Suppliers often lack access to the detailed vehicle data and test benches, such as for suspension characterization. For OEMs, the large number of vehicle variants makes it difficult to realize the full digital twin for each variant.
Automakers often struggle to efficiently use and deploy the digital twin due to variation in model fidelity and usage throughout their own organization. Most engineering departments are divided into groups, such as vehicle handling, comfort, autonomous driving, etc., and each group has its own preferred way to perform testing for the modelling as well as the required resulting fidelity. This can lead to overlap in work between departments, inefficiencies, and unshared knowledge. The lack of uniformity can also deteriorate the fidelity of simulation models.
Companies may also have difficulties building the models required for a full digital twin in a way that is both time- and cost-efficient. Supplier companies typically do not have the required information in order to build these models. The cost to OEMs to build a model for every variation is prohibitively high.
Despite these challenges, all hope is not lost for automakers wanting to build the digital twin. The Simcenter Engineering team can take any car and turn it into a high-fidelity multi-purpose digital twin. Check out the video below to learn how:
The power of the multi-purpose digital twin
Using a multi-purpose digital twin, companies can analyze multiple disciplines using the same simulation model. By using model identification approaches developed by our team, Simcenter Engineering services can help OEMs and suppliers build the models more easily and in a way that is much more cost-efficient than building from scratch. This approach helps engineers achieve a higher level of fidelity, lower product development costs, increased quality, and a better driving experience for the end-user.
Learn more about how Simcenter Engineering helps companies build the multi-purpose digital twin:
- Managing vehicle dynamics simulation for automated driving
- Demystify on-center vehicle performance
- Design for ride comfort – from concept to validation
To get in touch with Simcenter Engineering, email us at engineeringservices.sisw@siemens.com.