Spacecraft acoustic testing for upcoming lunar journey
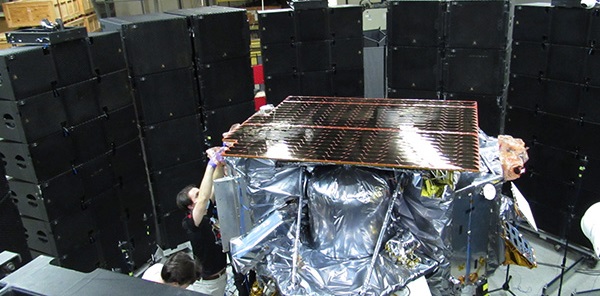
Astrobotic’s Peregrine lunar lander has successfully passed all acceptance tests, including spacecraft acoustic testing. A critical milestone on its path to flight.
Acceptance testing was conducted at the Dayton T. Brown, Inc. commercial test facility in Bohemia, NY. The campaign included sine vibration and acoustics testing and proved that Peregrine can withstand the flight environment of United Launch Alliance’s (ULA) Vulcan Centaur, the launch vehicle for Peregrine Mission One.
“The completion of environmental testing marks a critical step forward in our program. This testing ensured the spacecraft is fully capable of meeting the rough environments it will feel during launch, transit, and landing on the Moon,” says Pete Frye, Mechanical and Fluid Systems Manager at Astrobotic. “Successfully completing this harsh testing shows how much preparation, hard work, and perseverance our team has put into this mission. It takes a great team to complete the testing, let alone to do it without a single issue arising.”
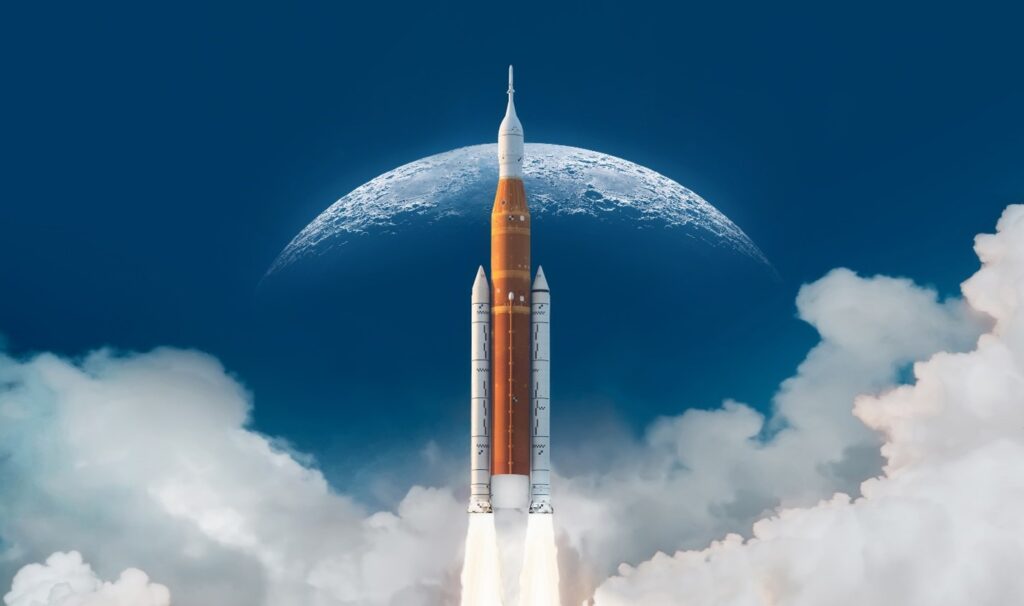
The essentials of spacecraft vibration and acoustic testing
Now, one of the spacecraft verification and qualification tests to be done is acoustics. The noise level generated at launch is not only lethal to humans, but it can also damage the payload. In other words, the whole space mission can be compromised. And nobody wants that!
The overall sound pressure level (OASPL) reaches 146dB inside the fairing (where the spacecraft is tucked up to go to space). This vibration value can cause structural damage and jeopardize the functionality of instruments and subsystems. To give you an idea, 146dB is about 20 times louder than an operating jackhammer… With no ear protection! So, before the spacecraft launch, the large and flexible components of the launch vehicle (for example reflectors, or solar panels) as well as the proto-flight (PF) model, are tested and exposed to high-intensity noise. Engineers can therefore assess their response and ensure they will survive the launch.
The conventional method of payload vibro-acoustic tests, sometimes referred to as reverberant field acoustic tests (RFAT), requires large reverberant acoustic chambers. As the satellites have been launched for decades using this type of test, this methodology is validated, accepted, and part of the industry standards or handbooks.
Direct field acoustic noise testing: a new spacecraft acoustic testing approach
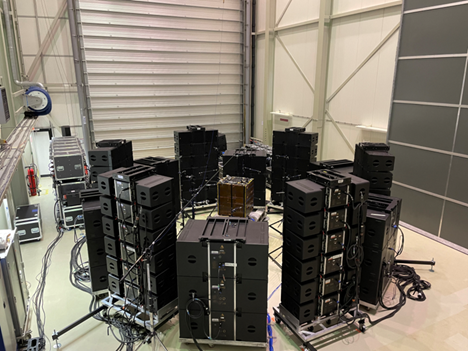
For a purely business reason, companies started to ask the question: “what if we use loudspeakers to make that much noise?” That question was asked almost two decades ago. It took numerous series of tests and many broken speakers to reach today’s state-of-the-art satellite vibration test method.
Based on multi-input-multi-output (MIMO) narrow-band control algorithms, Simcenter Testlab offers today the possibility to generate the required noise level (146dB) and field uniformity for spacecraft acoustic testing.
Of course, once an adequate set of speakers and amplifiers is provided, such a setup requires less cost compared to the investment and running cost of a reverberant chamber.
What’s more, the main added value of the DFAN method is that the sound system can be moved and transported to the manufacturing site. This is a great benefit since the payload doesn’t have to be shipped to the test facility. The economic benefit for spacecraft manufacturers is clear: no need to build very expensive test facilities, no need of moving payload and teams of engineers to a remote test center, and increasingly efficient testing technology.
However, space agencies and launch vehicle producers are still trying to create the necessary guidelines for the industry. As of today, NASA Handbook 7010 is the only document that provides some guidelines.
As this innovative direct field acoustic excitation technology advances, the control algorithms included in Simcenter Testlab MIMO software, part of Siemens’ Xcelerator portfolio, have too. This attracted the attention of satellite OEMs and agencies through Siemens research activities, validation tests, and scientific publications. The European Space Agency (ESA) is now aware of the full potential of this method. Meanwhile, many space subsystems and satellites have already been successfully qualified with this state-of-the-art solution.
Virtual direct field acoustic noise: mitigate risk in acoustic testing with simulation
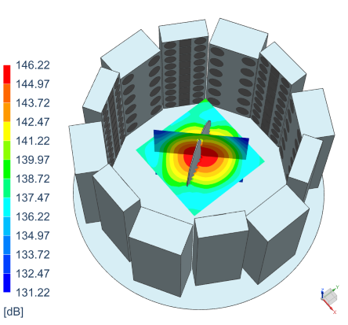
Of course, satellites are very expensive systems with unique payloads. Should something go wrong during the qualifying tests, it can be expensive to mitigate the damage to both the physical satellite structure as well as launch schedules. Digital twins can make a huge contribution by supporting test campaigns before the actual physical test takes place. That is why Siemens has built the capability to design and optimize the setup for a more efficient and safer test into Simcenter 3D. Further research is also underway to reuse the same digital twin models to estimate the acoustic and structural responses online, including in locations where no physical sensors are placed. The idea is to extend the limited data obtained from the sensors during the test with data from virtual channels to enable full-field monitoring.
To conclude, when building your next (or first) satellite, you will have to verify and qualify it for acoustic excitation. Whether you opt for a standard reverberant chamber test facility or proceed with a more versatile and innovative technique, you can count on Siemens’ expertise in being a reliable partner in many projects applying both methods. Learn more about dynamic environmental testing here.
You might also be interested in…
- Webinar | Spacecraft acoustic testing
- White paper | Perform safe and efficient space qualification testing
- Case study | Thales Alenia Space