Load Data Acquisition with Simcenter SCADAS RS
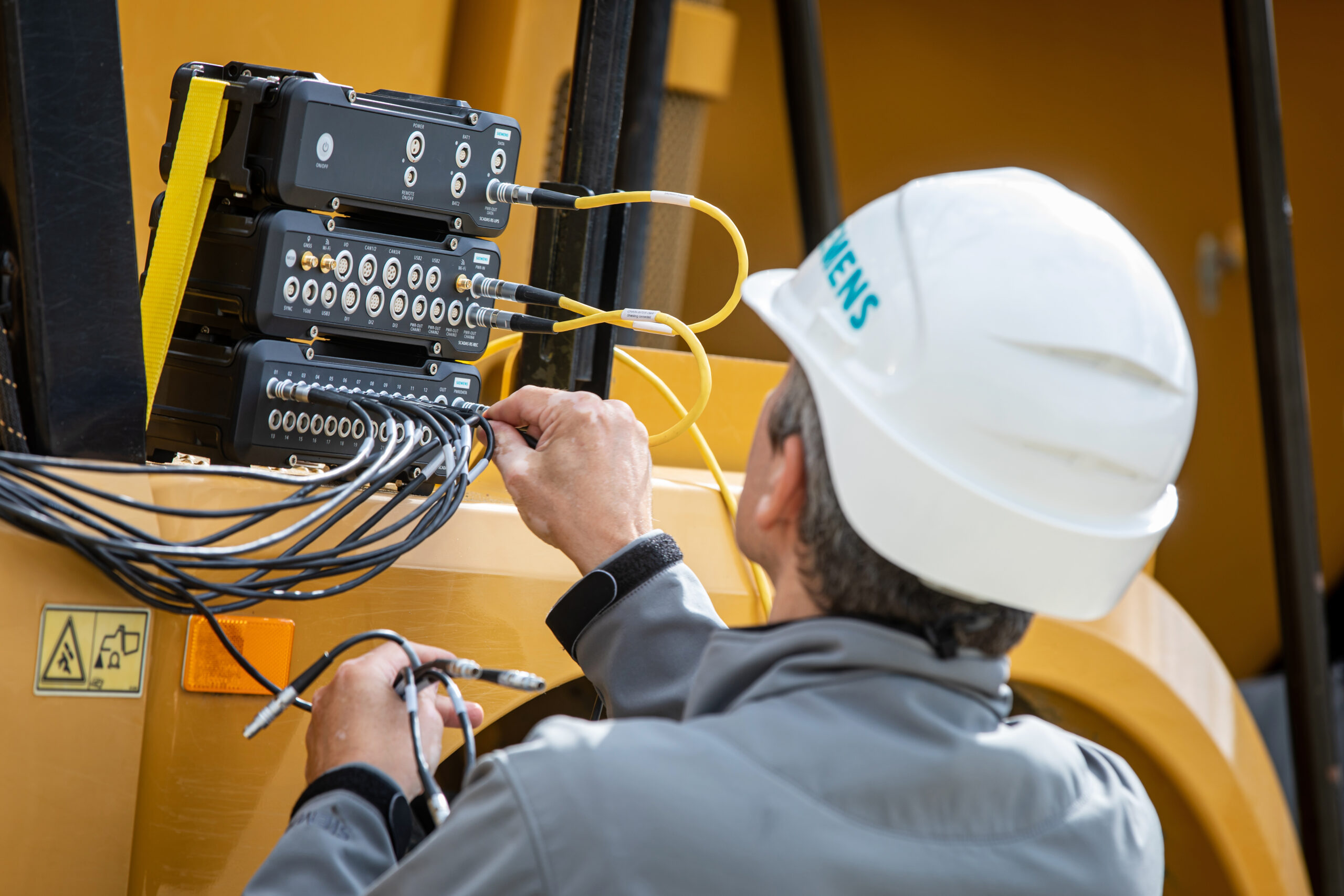
Load data acquisition is a challenge that many OEMs are confronted with when assessing the performances of their complex machines. Especially in the Heavy Equipment industry and in Off-highway applications, engineers have to conduct such measurements campaign in very demanding conditions, with extreme levels of temperature, vibration, and dust.
To support them in this, last year we launched the Simcenter SCADAS RS acquisition system, which is specifically designed to overcome the challenges of testing in harsh environments.
Let’s take a look at the new enhancements coming with the recent Simcenter Testlab 2206 release.
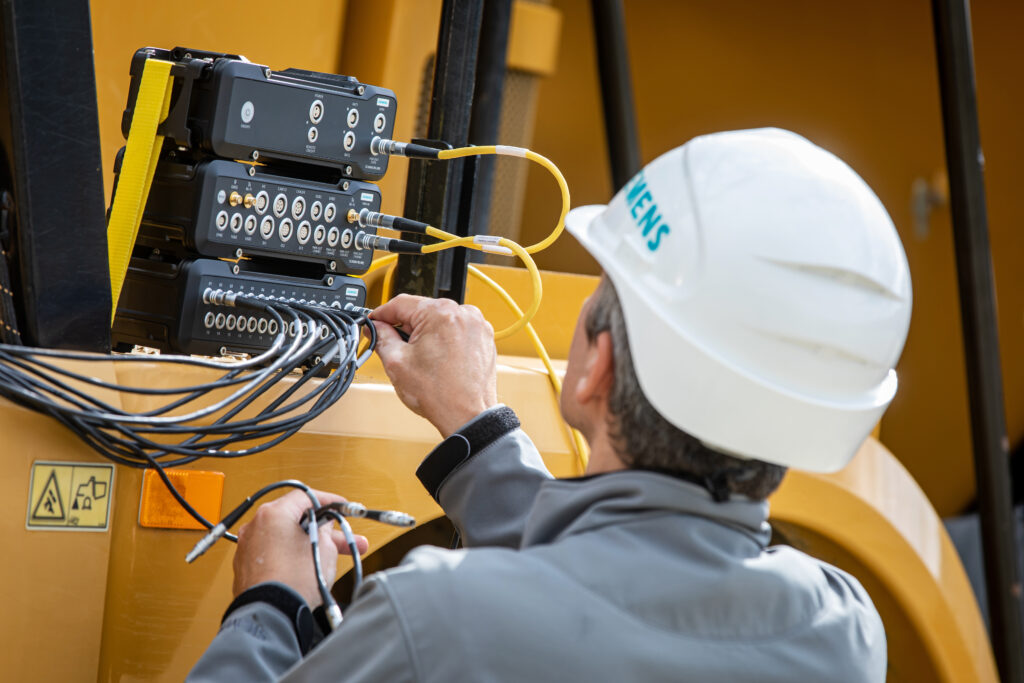
Rugged Series
Simcenter SCADAS RS is not just one simple recorder, it’s a rugged data acquisition system with specifications complying with the most extreme measurement conditions: IP66/67 rating, a wide range of operating temperatures, and high shock and vibration levels. You can use the Simcenter SCADAS RS to take measurements at your desk or in a laboratory environment, but the benefits of this system become clear when measuring operational loads in real-life conditions. Freezing or hot temperature, rain, mud – nothing will stop Simcenter SCADAS RS from recording data.
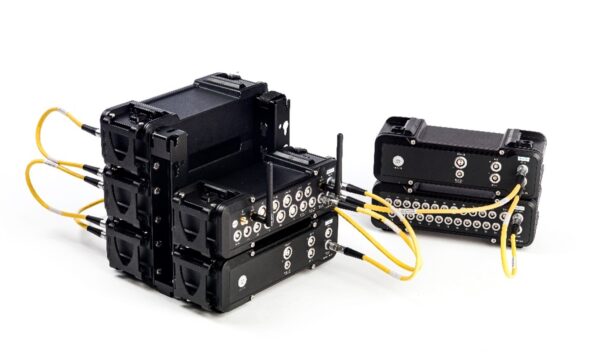
Distributed system
Simcenter SCADAS RS is extremely flexible. Its measurement units can be assembled as one single box or distributed on larger structures under test, even over hundreds of meters. Bringing these units as close as possible to the instrumented sensors massively reduces the cumulative length of all sensor cables and results in better signal quality. These measurement units are powered by UPS units (Uninterruptible Power Supply), which guarantee safe power management throughout the day.
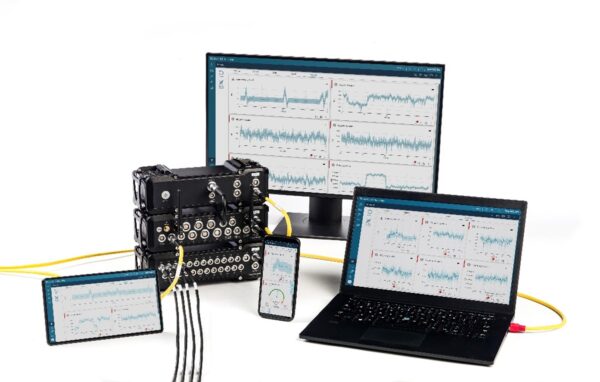
In-field data acquisition
Every Simcenter SCADAS RS system is delivered with all required data collection software. Each measurement unit has its embedded Web application, allowing to instrument a single unit. The Simcenter SCADAS RS Recorder App, which runs on the main unit (Recorder unit), aggregates all these settings from the connected measurement units and allows setting up a complete test, performing measurements, monitoring online data, as well as track-side validation in the field. A user can access this app from any device, from a small smartphone or a bigger tablet to a ruggedized Windows-based laptop, depending on personal preferences and ergonomics in the vehicle.
For bigger channel setups, the Windows-based Simcenter Testlab Recording Workbook can also be used, both for test setup preparation and monitoring of ongoing measurements.
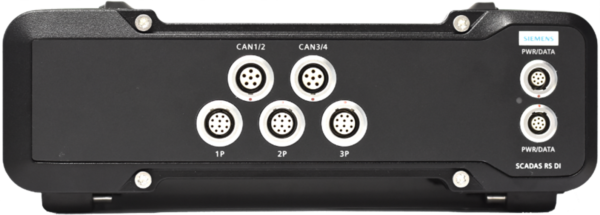
New measurement unit: Simcenter SCADAS RS Digital Pulse & Can Unit (DI)
With Simcenter SCADAS RS we are taking a substantial step in the direction of a more generic data collection solution. Digital data has become an integral part of the measurement campaign objectives as more and more sensors deliver their data via CAN-bus (wheel force transducers, Inertial measurement units, thermocouples, etc.). Therefore, we need to measure multiple CAN inputs simultaneously and handle a bigger amount of CAN channels during and after the measurement.
Every Simcenter SCADAS RS DI unit will extend the SCADAS RS with 9 additional pulse inputs and 4 additional CAN bus inputs. The pulse inputs can be used individually or combined into up to 3 incremental encoders with a sense of rotation and reference pulse. Conversion from pulse to engineering signal, like position, angle, rpm, flow, or any other, is directly executed on the measurement unit itself allowing online visualization via the on-board Simcenter SCADAS Recorder App.
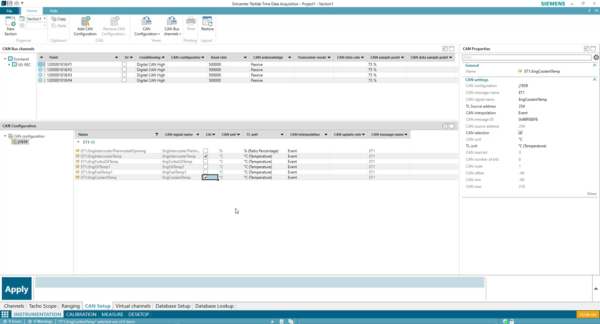
CAN /CAN-FD Configuration
In this new release, we included a file format called SCDBD for Simcenter Digital Bus Definition. The SCDBD file stores the CAN DBC file as it was imported by the user, and will remember all specific user choices like, of course, the signal selection but also the desired interpolation method and sampling rate, the modified engineering units, the modified baud rates and much more. This new approach allows setting and storing the preferred selection for one specific vehicle, or family of vehicles, and using it again and again for multiple campaigns.
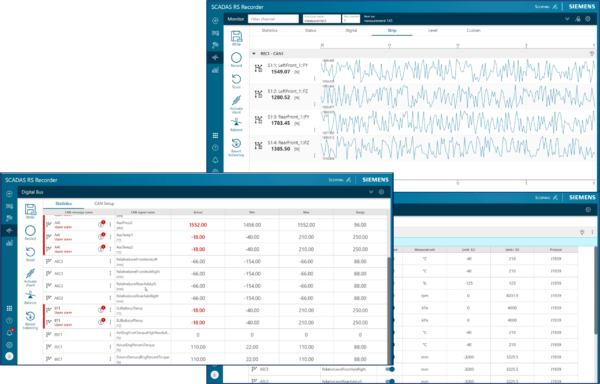
CAN – SAE J1939 extensions
For the heavy equipment and ground vehicle industry, the SAE J1939 standard is very important and is the equivalent of the automotive OBD-2. But the J1939 protocol goes further, as it combines diagnostics and broadcasted signals. It also manages the communication between the main vehicle and trails or equipment. Both Simcenter SCADAS RS Recorder App and Simcenter Testlab Recording Workbook integrate the specific J1939 feature like PGN requests, priority bit masking, and multiplexing.
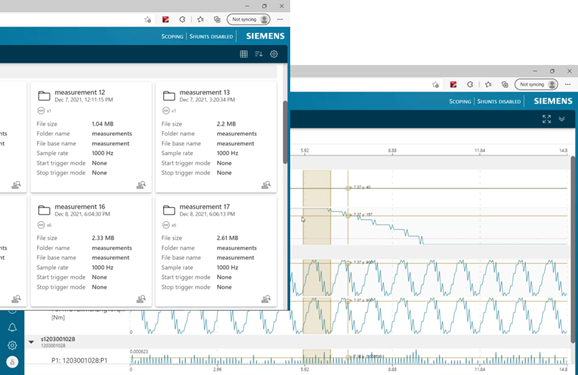
Track-side validation – In-field data validation
With Simcenter Testlab 2206, we made the track-side validation easier and faster. On a proving ground or in the field, it’s important to check the validity of the tests before leaving the measurement location. High-level checks on driving conditions, the number of pre-defined maneuvers, quick visualization of time traces, and overall statistics help to assess if measurements are suitable for further analysis.
This track-side validation can be done with the Simcenter SCADAS RS Recorder App, on your smartphone, tablet, or laptop. All relevant data can be inspected, including the CAN signals which have been decoded online during the measurement. A quick check on the statistics, scroll through the channels, and zoom in on the most relevant time segments of the measurement result in a fast ‘Validate / Reject’ of the measured runs!
Connectivity and full unattended acquisition
Absolutely mandatory when you need to collect data over multiple days of machine operation in the field. Your data acquisition system must be capable to operate autonomously without human interaction. Thanks to its UPS units, the Simcenter SCADAS RS can boot automatically as soon as power is available or when the vehicle is switched on. The system will be up and running – waiting for trigger conditions to start or stop the measurements. These trigger conditions can be complex, such as logical operations on any kind of measurement channels. On top, the same operation can be repeated over and over again, as long as these measurement conditions are met. The driver does not need to perform any specific operation, or even be aware of the measurement system in the vehicle.
If the operator is interested in the status of the Simcenter SCADAS RS, he can simply connect with his mobile device to the on-board Recorder App and check generic measurement info, sensor health status, and details on CAN and GNSS connectivity.
In parallel, an engineer can remotely access the Simcenter SCADAS RS to visualize and validate the data. Even from a different physical location, he/she can take control of the system, download data, start processing with Simcenter Testlab ProcessDesigner, and even request extra measurement runs to the driver.
This tremendously increases resource availability, as both the machine operator and the engineer can focus on additional tasks during the data acquisition.
Real-Time Road-to-rig Interface
EtherCAT has become the standard for the so-called road-to-rig scenario. The same instrumentation is used for both the load data measurements in the field and for the accelerated testing on the test rig. In this context, Simcenter SCADAS RS not only acts as a data acquisition system, but also as a set of signal conditioners for the test rig controller.
This approach avoids long re-instrumentation when moving the vehicle or sub-assembly from the field onto the test rig. And equally important: a single connection from the SCADAS RS ECAT to the test rig controller enables all these channels in the test rig application, without the need to output all sensors to a patch panel via analog cabling! Specific applications call for dedicated solutions
Simcenter SCADAS RS is the answer to many of the challenges arising from test campaigns in rugged conditions. With its enhanced features coming with the Simcenter Testlab 2206 release, it allows you to have a complete solution for testing and validating your machine operation both in the field or on a test-rig.
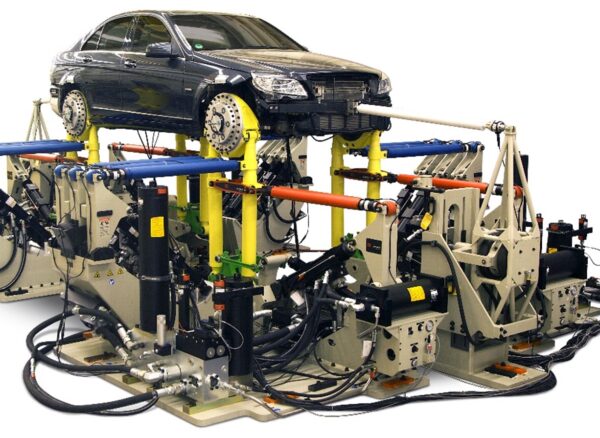
New unit: Simcenter SCADAS RS EtherCAT unit (ECAT)
This ECAT unit enables real-time capabilities of Simcenter SCADAS RS, and provides a digital data output to test rig controllers. The new unit copies the signals of up to four B24 and S24 conditioning units to an EtherCAT bus – so up to 96 channels in total. If you need more, just add an additional ECAT to your setup.
The system is plug & play: when a SCADAS RS ECAT is connected to the measurement units, the active channels of the connected B24 and S24 units are published on the EtherCAT bus, and the EtherCAT master takes control.
A single connection from the Simcenter SCADAS RS ECAT to the test rig controller enables all these channels in the test rig application, without the need to output all sensors to a patch panel via analog cabling!
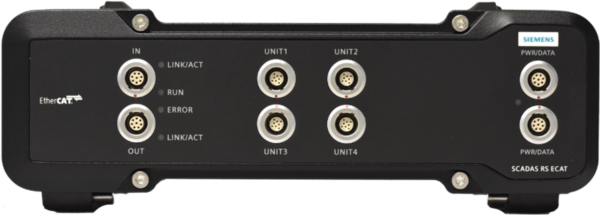
Specific applications call for dedicated solutions
Simcenter SCADAS RS is the answer to many of the challenges arising from test campaigns in rugged conditions. With its enhanced features coming with the Simcenter Testlab 2206 release it allows you to have a complete solution for testing and validating your machine operation both in the field or on a test-rig. New capabilities are specifically designed to make your measurement campaigns go faster and gain efficiency and flexibility in all tasks, from data monitoring and acquisition up to validation and performance analysis.