Ride comfort and handling in electric vehicles: The balancing act
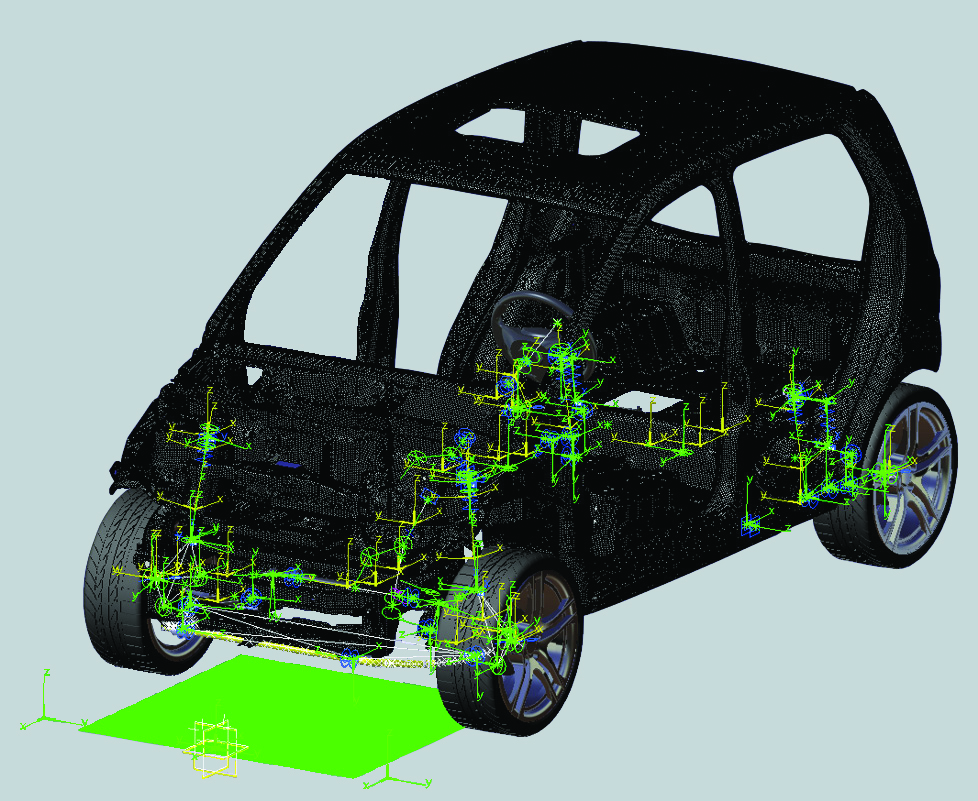
Electric vehicles require a delicate balancing act by manufacturers. When engineers try to increase the ride comfort, ease of handling can be hurt and vice versa. Engineers in the automotive industry use computer-aided simulation extensively to find the right balance between comfort and handling.
However, applying that requires training and extensive knowledge to get the best performance and results. Even with simulation tools, engineers still need to build a strategy that defines metrics and provides comprehensive insight into performance.
Loncin develops motorcycles and engines that prioritize low emissions and high fuel efficiency. The company has extensive experience in developing highly efficient motors, but had limited experience in the electric vehicles (EV) space. Loncin’s first efforts at EV design produced good handling results, but engineers wanted to provide a better driving experience.
Seeking electric vehicles expertise
Rather than invest in simulation tools and learn by trial-and-error, Loncin partnered with Siemens Digital Industries Software for testing services and hardware. The partnership with Siemens helped Loncin achieve its desired balance between ride comfort and handling from the ground up in its electric vehicles.
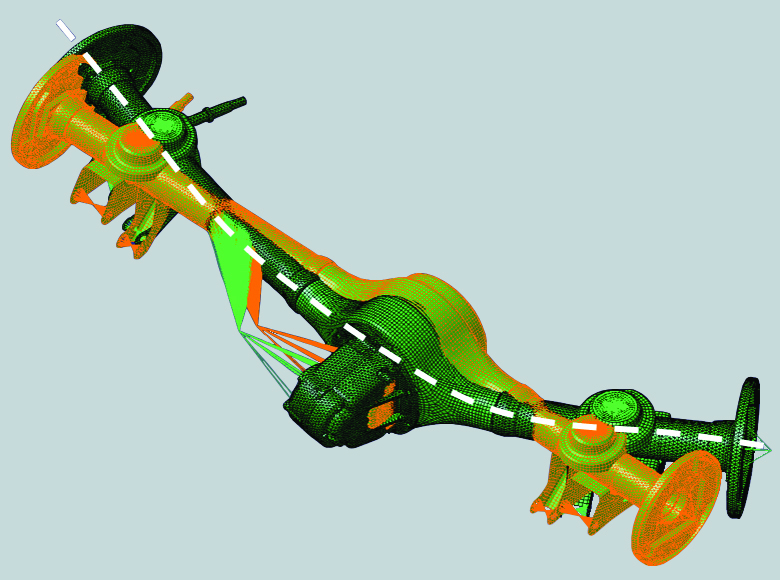
Loncin engineers visited the Siemens office in Italy for an intensive week of knowledge transfer, testing and training with Simcenter™ Engineering.
Defining metrics for the electric vehicles
The first step was to determine how to define the metrics of the vehicle, including acceleration, comfort, and handling. Once the teams determined these metrics, Siemens and Loncin worked together to build simulation models that would enable them to objectively evaluate and optimize the performance of Loncin’s EV components. Simcenter Engineering and the Loncin team worked together on a step-by-step approach for accurately modeling vehicle subsystems, such as suspensions, upper body structural flexibility, and tires, which would be integrated into the vehicle model.
Using the models
After the models were built, Siemens and Loncin performed several iterations in the simulation loop. This started with extensive design-of-experiment (DOE) testing and went all the way to identifying the most effective set of countermeasures. The objective was to understand how changing parameters of the vehicle, such as suspension, would impact overall performance. This enabled the teams to gain a holistic understanding of how the vehicle would behave in varying circumstances.
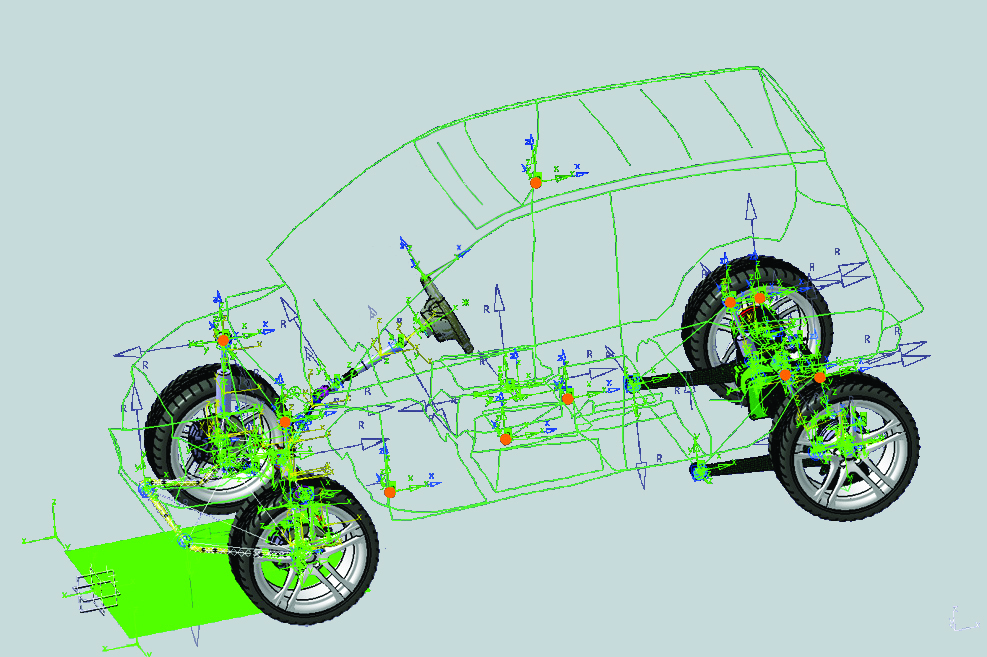
The goal of the Simcenter Engineering team was to not only perform the services requested by Loncin, but also to help them use Simcenter 3D Motion software and Simcenter 3D Nastran® software in the optimal way. Siemens engineers worked with Loncin to teach them how to use the software, process models, view results, and manage models.
“Siemens helped us achieve the perfect combination of experience and tool usage for our electric vehicle,” says Jinwei Liu, the director of the team at the Loncin Institute of Overall Structure and Performance.
Validating the models
Loncin engineers returned to their office after the training and knowledge transfer was complete. Their next step was to test the simulation models they had created with Siemens. They found the simulation models were highly accurate, confirming the simulation tools and methods learned from Siemens matched real-world performance.
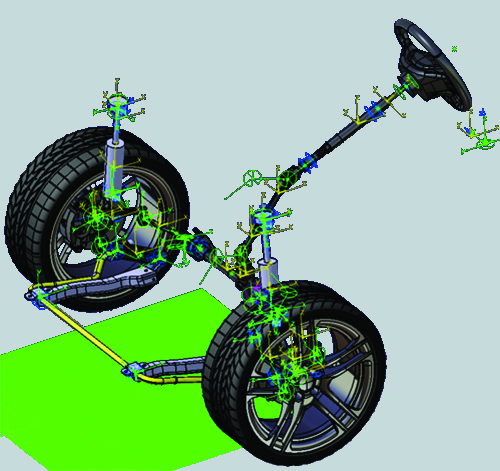
Achieving process optimization
Working with Siemens, Loncin engineers also gained expertise in automotive engineering concepts. The team realized time and cost savings once issues were frontloaded. Their previous strategy had been to act at the troubleshooting level, which is often too close to time-to-market. This enabled them to develop a better design for the chassis and body at an earlier stage of the development process and achieve multi-attribute optimization.
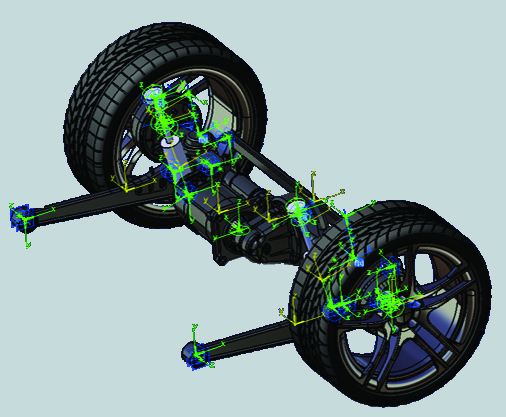
This project also confirmed it is possible to achieve faster and more streamlined troubleshooting by building accurate, detailed CAE processes. The most reliable results stem from the accuracy of the model’s input data. If accurate input data sets were not possible, the vehicle model cannot be used to predict the vehicle behavior. But it can still show trends and provide knowledge about the overall vehicle performance.
“Thanks to our partnership with Siemens, we were able to achieve a 15% improvement in ride comfort,” states Yang Lin, manager of the chassis NVH group at the institute.
“We will continue to study the technology learned from Siemens. We hope to have the opportunity to learn from the team and cooperate with them again in the future,” says Mingchao Zhu, manager of the powertrain NVH group at the institute.
You may also enjoy:
- MAB in engineering: A Hyundai Motor Company case study
- Excellence in electric vehicle NVH at Karma Automotive
To get in touch with Simcenter Engineering, email us at engineeringservices.sisw@siemens.com.