Reacting Flows and Combustion Computational Fluid Dynamics (CFD) with Simcenter STAR-CCM+
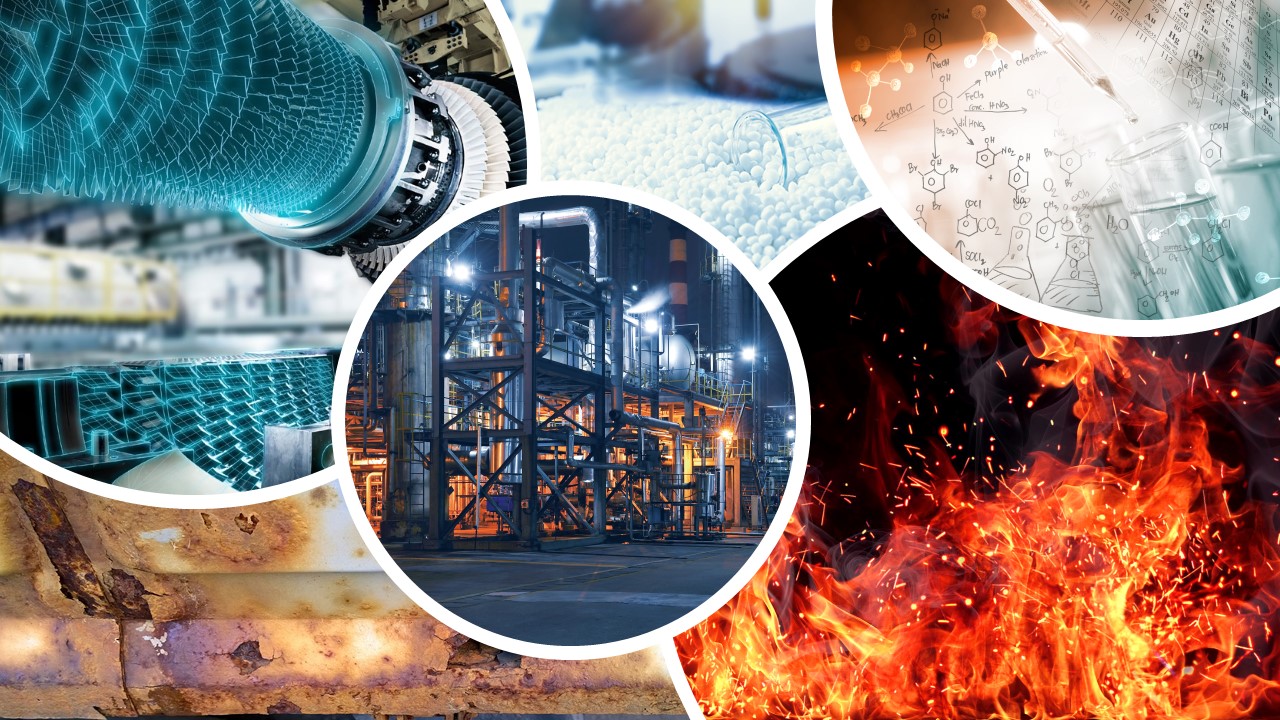
The wide range of reacting flows
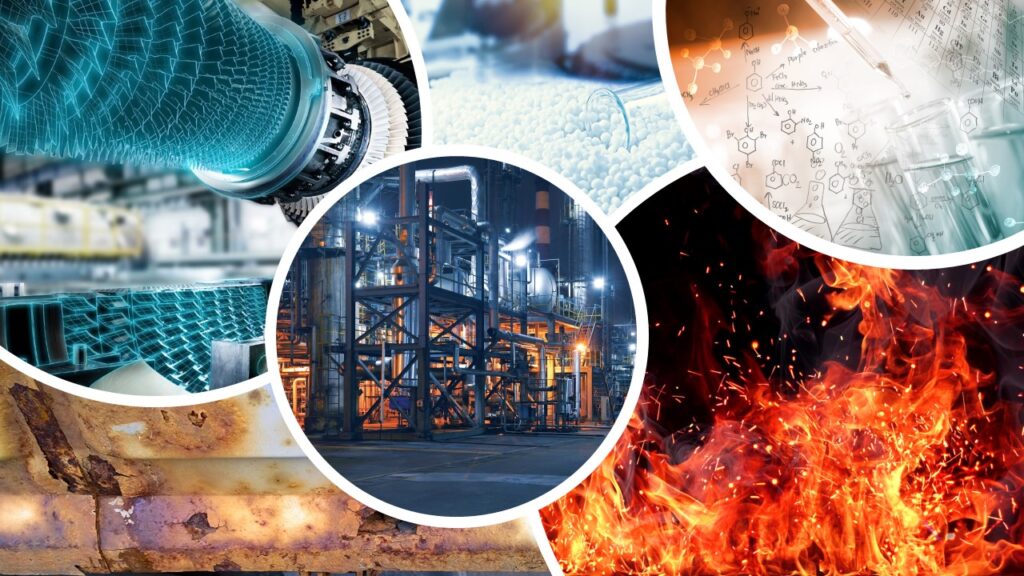
Reacting Flows are all around us. Therefore, it’s no surprise that applications that rely on chemical reactions and combustion are spread across almost all industries.
Gas turbines play and will continue to play a major role in energy production, and even in a less-fossil fuel dependent world their usage with alternative fuels is on the horizon. Likewise, the internal combustion engine will be around for quite some time. And even alternative powertrain systems, like e.g. fuel cells, do depend on reacting flow phenomena.
In fuel production, be it conventional or alternatives like synthetic or biofuels, reacting flows are the dominating factor. Any fuel production, methane reformation, hydrogen production all rely on reacting flows.
In the chemical process and manufacturing sectors one finds applications such as glass furnaces, industrial burners and metallurgy devices. Reacting flow processes govern applications such as polymerization and fermentation and many others in the process industry.
The challenges of reacting flow applications
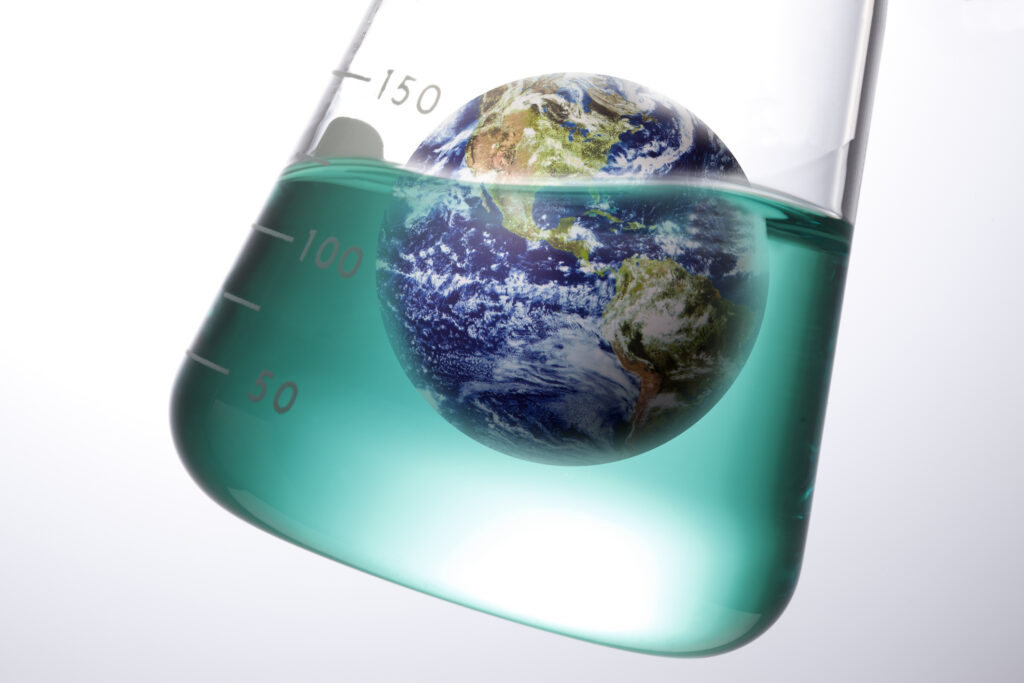
Regardless the application, the technical challenges are always the same:
- Design reacting flow and combustion systems for lower emissions and improved energy efficiency
- Reach operational efficiency through higher fuel efficiency, reduced waste and a higher yield
- Achieve lower design costs and reduce maintenance cost
- Explore innovative systems, including new fuels and hybrid systems, new operating ranges and strategies. This also implies leveraging novel materials and manufacturing processes.
Therefore, any company and industry whose business model relies on reacting flows has a clear objective. They need to make sure they optimize their products and processes for maximum efficiency with minimum investment. And all this under increasing competitive and legislative pressure. This implies the ability to handle continuously increasing complexity and to turn this complexity into a competitive advantage.
Addressing the challenges through reacting flow modeling
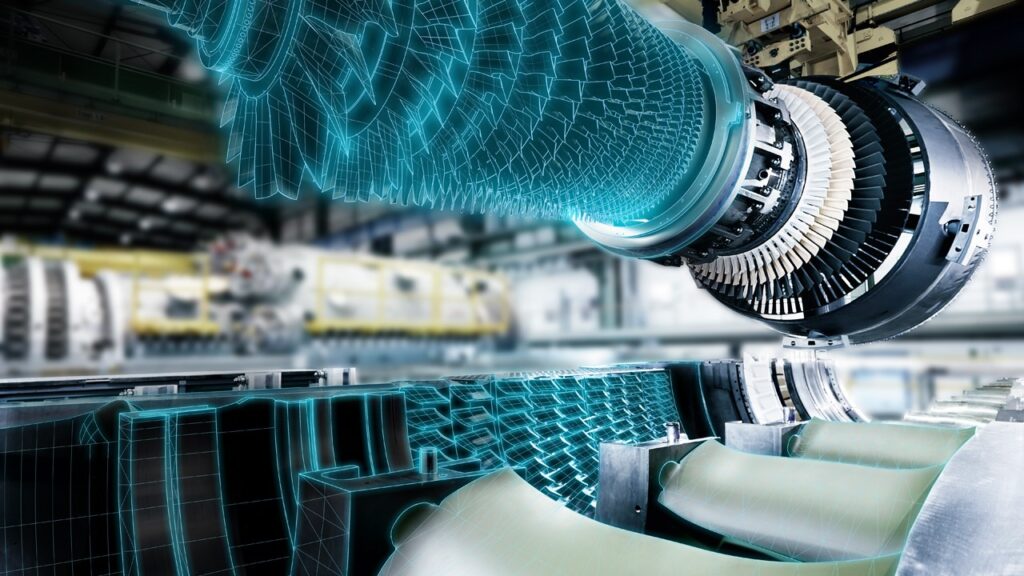
The key to achieve this lies in the rigorous establishment of a digital twin. Modeling and simulating reacting flow and combustion processes and systems allows for high fidelity performance predictions prior to making any cost intense real world prototyping and testing. This enables companies to come up with superior reacting flow systems in unbeaten turn-around times.
Today companies leverage such high fidelity predictions to design better combustion systems including
- flame dynamics
- heat transfer and thermal wear
- emissions such as NOx, soot, CO and other
For other reacting flow systems it is important to analyze of various reactive flow concepts to predict
- yield
- conversion
- selectivity
- undesirable conditions to those
For fast cost efficient system development it is key to explore many design variants early in development. Targets of such design exploration studies range from optimizing flame shape and location through minimizing solid component temperatures to the reduction of emissions and maximization of performance efficiency.
Computational fluid dynamics (CFD) software for reacting flows
A key player in the family of simulation methods to address these challenges is computational fluid dynamics (CFD). Yet there is a number of major requirements to a computational fluid dynamics (CFD) software to truly enable engineers to design future reacting flow systems:
Comprehensive suite of reacting flows and combustion models
The first requirement is a comprehensive suite of high-fidelity combustion and reacting flow models: For that Simcenter STAR-CCM+, the Multiphysics CFD simulation software from Siemens Digital Industries Software, offers a wide range of industry-relevant, accurate and fast CFD models for single and multiphase reactions.
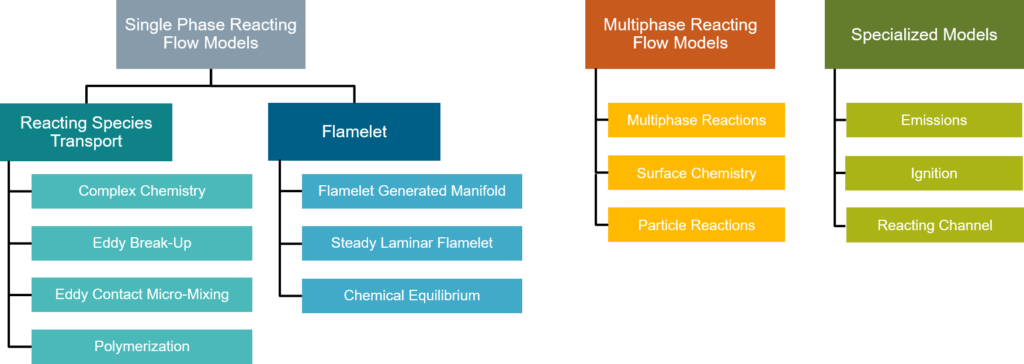
Industry-relevance
With a wide range of reacting flow capabilities Simcenter STAR-CCM+ is able to serve all industries across the whole spectrum of applications. A wide but carefully selected range of industry relevant combustion, emission and electrochemistry models is available. Users can select the appropriate model combination for the application or for the goal in mind.
Combustion systems
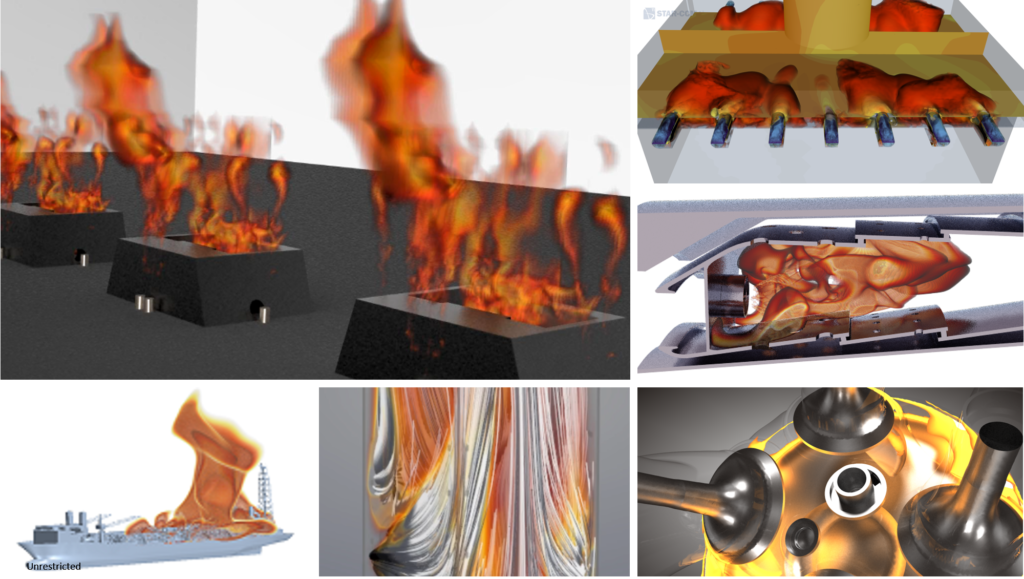
Gas turbines, internal combustion engines, industrial furnaces, fires, they all require the accurate modeling of flame physics and chemistry. For each level of accuracy and anticipated turnaround time there is an appropriate solution in Simcenter STAR-CCM+:
An Eddy Break-Up or the more accurate flamelet model may be appropriate to determine the flame location and temperature profiles in a furnace. For ignition or CO emissions, complex chemistry is probably the best choice. For accurate flame positioning in RANS, TFC and CFM flame propagation models are available. Coupled with model-based adaptive mesh refinement this allows for highly-efficient but accurate flame predictions. The dynamic thickened flame model enables accurate flame positioning in Large Eddy Simulations.
A dedicated set of combustion models is available for internal combustion engines, including the popular models ECFM-3Z and ECFM-CLEH.
Multiphase reacting flows
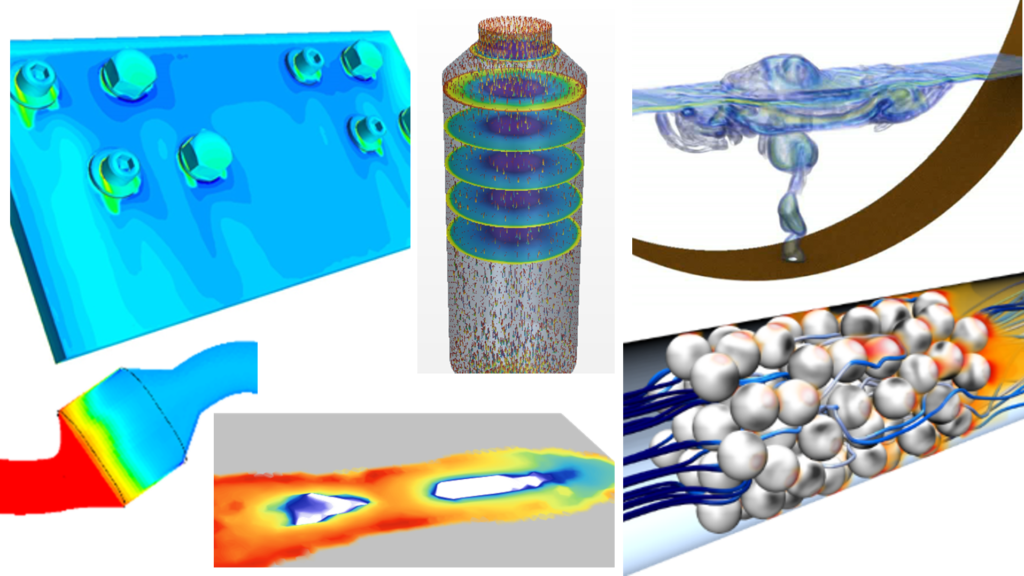
Simcenter STAR-CCM+ includes the capability to combine chemical reaction modeling with various types of multiphase flows.
Reactive flows can be coupled with Eulerian multiphase and Volume Of Fluid (VOF). This allows to simulate reactive bubble columns, metallurgy, trickle bed reactors, fluidized beds or glass furnaces etc.
Simcenter STAR-CCM+ furthermore allows for surface reactions for catalytic reactions e.g. in exhaust gas aftertreatment systems, such as SCR systems or DPFs, or packed bed reactors for e.g. methane reformation. Reactions in liquids or between liquids and gases can be used e.g. for deposit formation in SCR systems or the prediction of corrosion. Finally the modeling suite covers particle reactions with Lagrangian and DEM particles for coal combustion, biomass combustion etc. Furthermore a dedicated model for polymerization exists.
Reacting flows and multiphysics simulation
Beyond that, thanks to a single integrated environment and solver reactive flows can easily be coupled with multiphysics simulation, like heat transfer or radiation etc. The former includes conductive and convective heat transfer with a coupled solid-fluid energy solver for accurate temperature calculations, used e.g. for turbine blade cooling optimization. A smart multiple time-scale workflow allows for highly efficient CHT simulations. Radiation allows for both surface-surface and participating media radiation and particle radiation.
Accuracy
We test all respective reactive flow models on a continuous basis using a comprehensive and state of the art set of validation cases. The validation suite covers both generic, well characterized academic benchmark cases as well as validation in real industry scenarios.
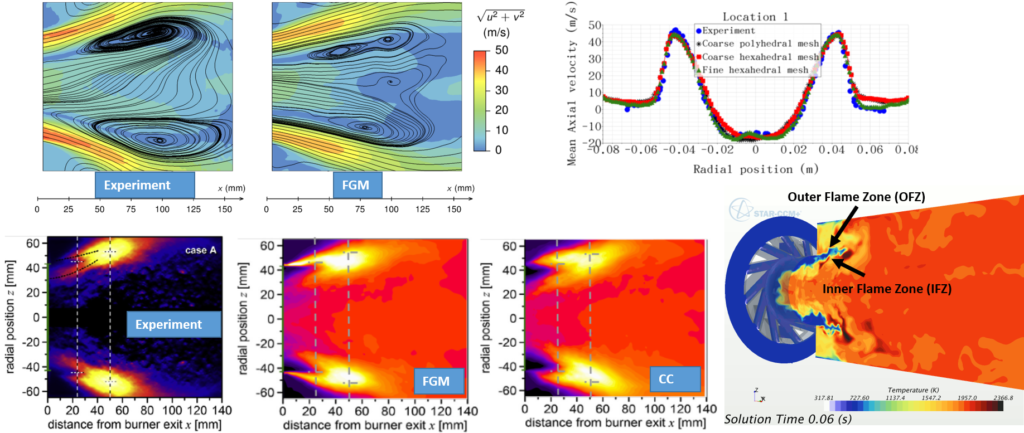
With accurate tabulation methods flamelet models give a quick and accurate solution for combustion within the flamelet regime. Complex chemistry is available for combustion that is not statistically steady. A highlight of Simcenter STAR-CCM+ is the availability of higher order numerical schemes. This makes the solution less dissipative and thus more suitable for LES combustion.
Speed and performance
Calculations need to be fast enough to allow for design optimization or quick evaluation of different designs. For this Simcenter STAR-CCM+ includes a wide range of combustion models with different level of accuracy depending on the need. The complex chemistry solver includes acceleration techniques such as clustering, Dynamic Mechanism Reduction & ISAT, as well as sparse solver for large chemical schemes. Finally, Simcenter STAR-CCM+ includes an efficient PISO solver, which, coupled with combustion, gives quick and effective LES combustion simulations.
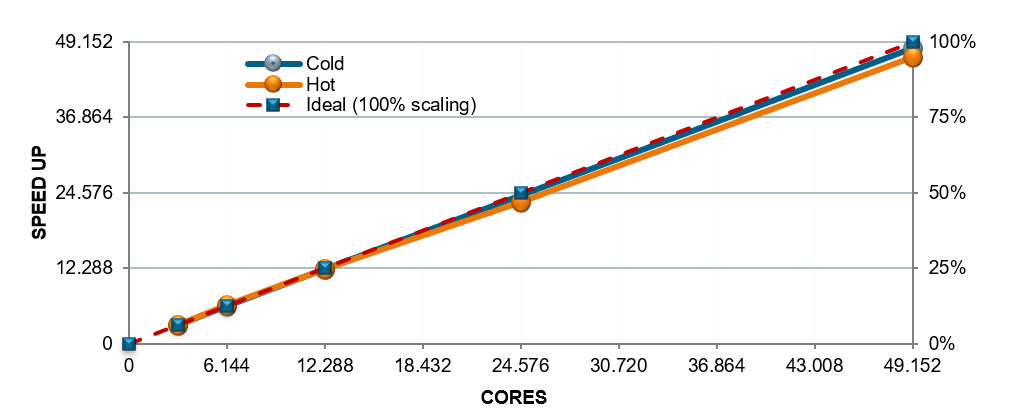
Fully Integrated Workflow Automation
But handling complexity does not stop at handling the physics with high-fidelity. In today’s computer aided engineering another key is handling complexity of geometry and conditions. Only a streamlined robust and repeatable workflow allows simulation engineers to focus on what really matters, and that is analyzing the results rather than wasting their valuable time with problem set-up and troubleshooting.
For this reason Simcenter STAR-CCM+ offers a fully integrated automated workflow to easily change design in the CAD and re-do the full mesh – run – analysis loop for a new design. This is available through an integrated environment including every required step within Simcenter STAR-CCM+.
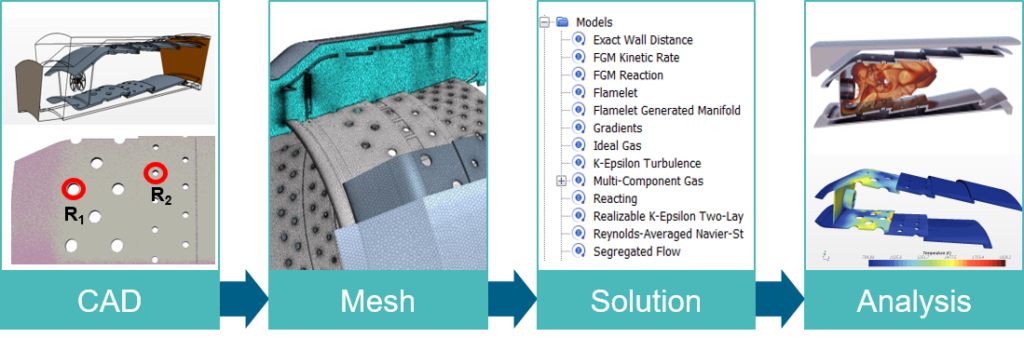
Parametric Models and CAD handling
enables easy and automated changes of design, which in turn enables design space exploration. Since Simcenter STAR-CCM+ includes both a built-in parametric 3D CAD tool and bi-directional connectivity to external CAD/PLM tools, it enables this functionality while providing flexibility in choice of CAD tool.
Flexible and robust meshing
is required to cope with the automatic design changes done in a design space exploration. When the CAD is changed, the mesh needs to adopt automatically. This is realized in Simcenter STAR-CCM through the fully automated meshing process.
For combustion cases model driven adaptive mesh refinement offers the possibility to automatically refine the mesh in areas of e.g. high temperature gradients, close to the flame front as in the burner picture below.
Embedded Automation
Simcenter STAR-CCM+ offers the ability to generate intelligent fully embedded workflows mitigating the need for any external scripting. Using automation enablers of tags, filters, parameters and operations users can easily built simulation templates for consistent re-usage and process automation.
Intelligent Design Exploration
Building upon this fully automated and streamlined workflow the built in Design Manager allows you to explore 100s of designs with ease from within Simcenter STAR-CCM+.
Powerful data analysis
To properly interpret the results you also need access to powerful data analysis. This is embedded in Simcenter STAR-CCM+, so you don’t need to use an external tool for effective postprocessing. As an example, data focus can be used to understand complex interdependencies or highlight areas of e.g. inefficient combustion with high emission formation.
The one-stop solution to improve reacting flow and combustion systems
Ultimately those companies that manage to virtually predict and understand the real-world behavior of their reacting flow systems will have a significant competitive advantage. Simcenter STAR-CCM+, part of the Simcenter portfolio from Siemens, offers a full-suite of high-fidelity simulation tools to bring innovative reacting flow solutions to market faster. With an accurate digital twin , many of our customers are already lowering development cost and time while bringing better combustion systems to market.
Listen to Rene Braun from B&B Agema on their approach for gas turbine and combustor design
In a totally different area of reacting flows, Cordessa is leveraging Simcenter STAR-CCM+ multiphysics and reacting flow capabilities to fight corrosion. A billion dollar business.
To find out more about the details of the Combustion Capabilities in Simcenter STAR-CCM+ read this factsheet