Driving digital transformation in aviation (with capable engineering simulation software)
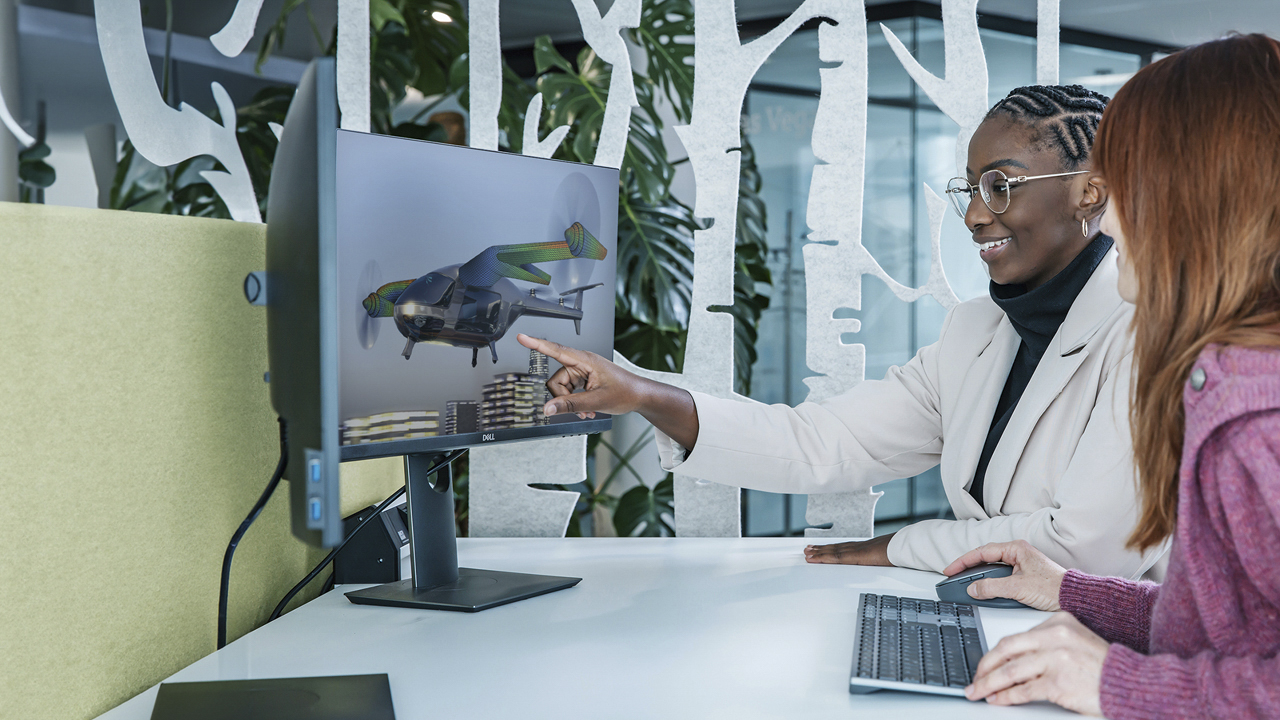
Why is driving digital transformation in the aviation industry crucial?
The aviation industry is continuously progressing, with aircraft advancements becoming more complex. One significant example is the anticipated design characteristics of sixth-generation fighter jets, which include unprecedented digital capabilities, enhanced systems integration, connection with all systems in the mission, advanced stealth airframes, next-gen avionics and variable-cycle engines. Another example is the urgent need to expedite the development of aircraft that are more capable, fuel-efficient, quieter, cleaner, and faster to market, without compromising safety in order to achieve climate-neutral aviation.
However, this complexity often leads to unforeseen problems and delays, impacting aircraft program costs and overall profitability. According to Deloitte, major aircraft programs are significantly delayed by an average of 29.5 months1 with implications on budget and resources. With a 48% average total cost growth2 over the original baseline, budget overruns have a significant impact on the overall program success.
This blog post delves into the advantages of utilising aerospace engineering software to tackle complexity while driving digital transformation. It encompasses various benefits such as exploring designs possibilities with creativity and rigor while mitigating costs, predicting the truly integrated aircraft performance, expediting design processes, combining physical and virtual verification and promoting integration and collaboration. Ultimately, this enables aviation companies to manufacture and operate mission-driven aircraft applications that are optimized for their intended purpose.
Exploring design possibilities while mitigating costs
By making effective use of the advanced features offered by powerful aerospace simulation software, engineers can thoroughly explore the possibilities of design, leading to savings and valuable insights. Through simulating various scenarios and variations, engineers can optimize designs and make informed decisions before finalizing the design. When considering the various design stages, such as the conceptual phase (with 10 designs and 100 variables), preliminary phase (with 1 design and 1000 variables), and detailed phase (with 1 design and 10,000+ variables), it is important to note that only a powerful simulation software is designed to support engineers in maintaining their creativity and precision throughout any phase. By utilizing an optimized iterative process, engineers can enhance the overall design process, reducing the chances of delays and expensive revisions. This approach lies at the heart of driving digital transformation in aviation.
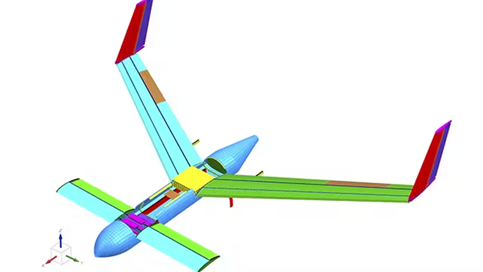
To give some context, Siemens aircraft nonrecurring cost estimation suggests that incorporating advanced engineering software can greatly enhance the analysis cost of an aircraft’s structure. This improvement is exemplified by potential savings of up to $103 million for a narrow-body jet airliner and up to $169 million for a fighter jet. Northrop Grumman, a leading global aerospace company, has achieved remarkable advancements in analysis efficiency through the integration of Siemens Xcelerator business platform and its advanced engineering software, Simcenter. By leveraging a closed loop system that combines analytical models with physical tests, Northrop Grumman has successfully reduced analysis time by 30 to 50%3.
Predicting the integrated performance of complex aerospace systems
Accurately predicting the behaviour and performance of complex aerospace systems is crucial for achieving program success and plays a crucial role in driving digital transformation. Only powerful aerospace engineering software solutions provide tools that enable engineers to create scalable digital twins, supporting mission-critical performance objectives in structures, aerodynamics, systems performance, thermal management, and verification management. By modelling the complexity of these systems and, above all, the integrated performance, engineers can gain confidence in early-stage designs and identify potential issues before they become costly problems.
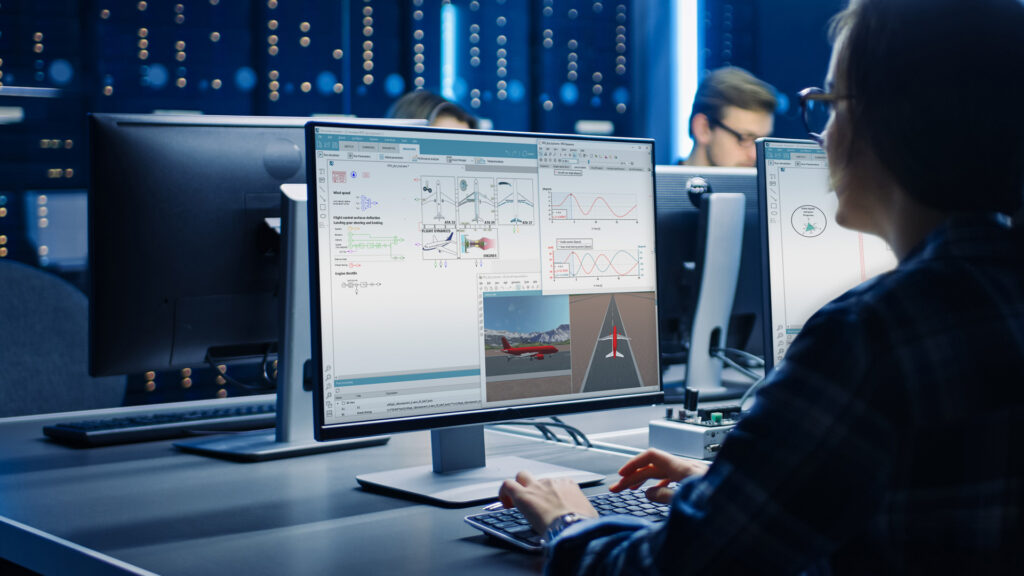
To provide some context, let’s consider the significant challenge of developing hydrogen-powered aircraft. Whether the aircraft is powered by fuel cells or direct hydrogen combustion, it presents a complex undertaking that requires careful consideration and analysis. By leveraging the capabilities of an integrated simulation solution, engineers can quickly and accurately model different components of the aircraft, such as the Hydrogen Storage and distribution system, the fuel cells, or turbomachinery, connected to the propulsion system (fans or propellers). Simcenter allows for testing the integration of these components into a comprehensive aircraft model, providing a valuable tool for designing and analysing hydrogen-powered aircraft systems.
Expediting design processes
Simcenter, is equipped with AI-driven engineering capabilities, enabling engineers to accelerate the speed of design space exploration and driving digital transformation in aviation without compromising accuracy. Such acceleration marks a leap forward in achieving optimal design outcomes based on the integration of advanced AI capabilities and seamless data management functionalities to a progressive and intuitive experience for users across various engineering disciplines. Thanks to an accuracy-aware AI, part of a hybrid-adaptive search framework, Simcenter can learn and enhance the current search as well as learning for future design processes. Such technology offers a significant reduction in design optimization time while maintaining the same design budget, when applicable: engineers can save up to 40% on computational time for lengthy optimizations. This contributes to more efficient program deployment and effectively exemplifies the concept of driving digital transformation.
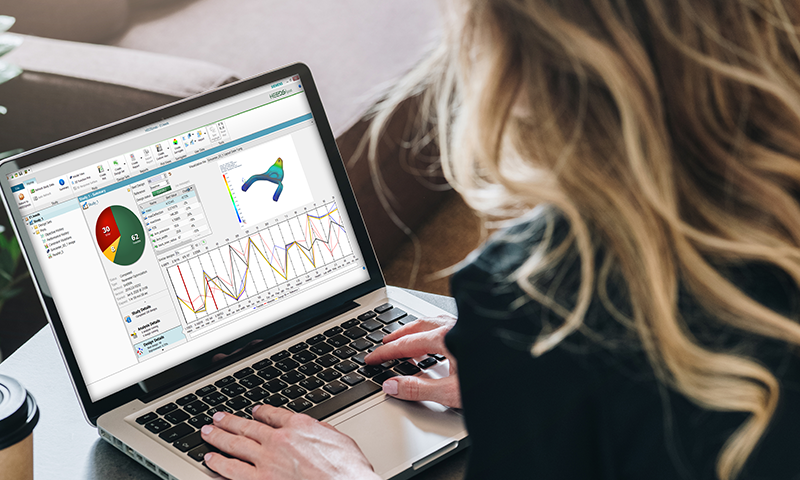
Combining physical and virtual verification
Certifying innovative aircraft programs can be a costly endeavour. According to Archer Aviation CEO, Adam Goldstein, as mentioned in an article on the Flight Global website, the cost of developing and certifying a single aircraft design could reach up to $1 billion4.
Whether it involves advanced air mobility systems, (hybrid-)electric aircraft, or military fighter jets, these programs are highly complex. Incorporating new materials, additive-manufactured structures, electrical propulsion systems, and advanced onboard software necessitates extensive virtual and physical testing to ensure the aircraft’s safety, reliability, and cost-effectiveness.
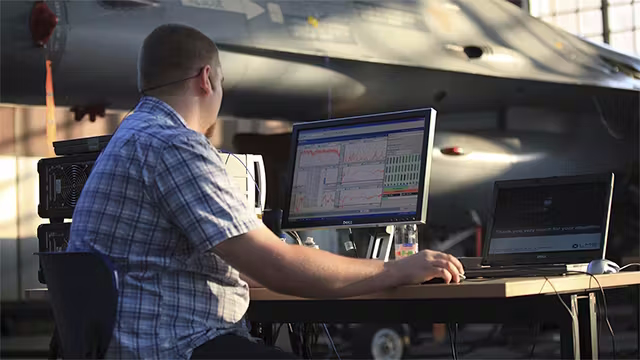
An integrated engineering software solution specifically designed for the aerospace industry can effectively manage the verification process right from the beginning of the program, starting with the definition and validation of requirements. This comprehensive approach ultimately ensures that the structural architecture, sizing, and certification of the aircraft meet the highest industry standards. Additionally, it allows for effective preparation of physical testing while minimizing associated risks.
By utilizing Simcenter, aerospace engineers can streamline the verification process, enabling them to identify and address any potential issues early on. This proactive approach helps in reducing the overall cost and time required for certification, as well as ensuring that the aircraft meets all necessary safety and performance requirements.
Fostering integration and collaboration
With definitive, real-time data available to all, it is possible to trace design intent and decision-making from concept to final certification and back again. Continuous monitoring of key technical performance indicators helps to eliminate integration issues along the way and communication between integrators and industrial partners is enhanced. The Siemens Xcelerator business platform, which includes Simcenter aerospace engineering software, plays a crucial role in facilitating this integration, breaking down silos between disciplines and ensuring seamless collaboration. By enabling teams to work together seamlessly, engineers can streamline the design process, reduce errors, and improve overall productivity. This approach, which lies at the heart of driving digital transformation in aviation, plays a crucial role in achieving successful outcomes.
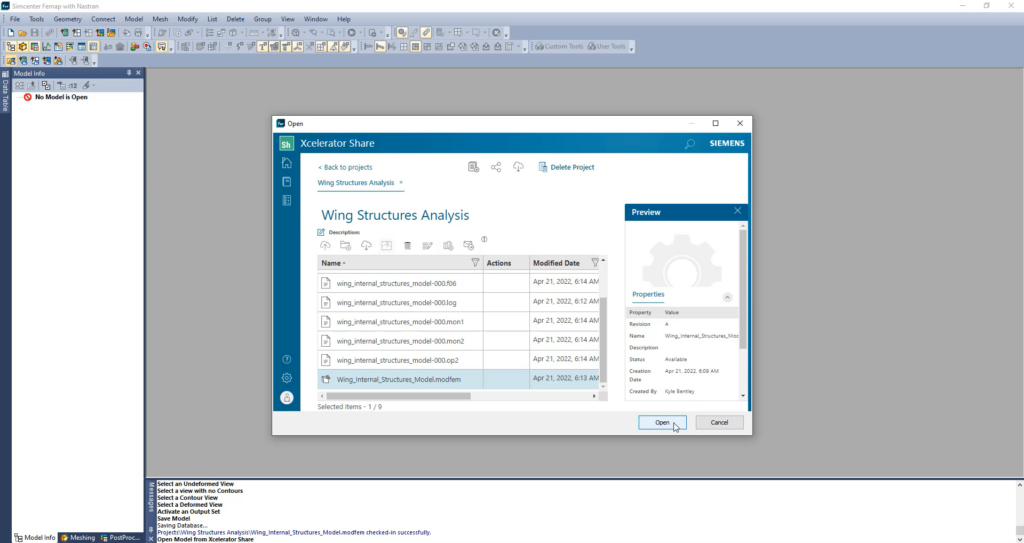
Conclusion
In today’s aerospace industry, where complexity and program delays can significantly impact costs and profitability, advanced engineering software is a vital tool for driving digital transformation. By implementing an integrated simulation and testing strategy, aerospace engineers can accelerate design timelines, achieve performance targets, and ensure successful program outcomes. Simcenter, with its advanced features and tailored applications, is at the forefront of digital transformation in aviation, enabling engineers to model complexity, explore design possibilities, utilize AI-driven engineering, combine virtual and physical testing and foster integration and collaboration. By embracing these technologies, aerospace companies can improve productivity, expedite design processes, and seamlessly integrate digital threads. The digital thread allows for a more cohesive and connected engineering process, beginning with initial requirements and architectural specifications and extending all the way until the aircraft is operational.
- Program management in aerospace and defense – Robin S. Lineberger et al. ↩︎
- Program management in aerospace and defense – Robin S. Lineberger et al. ↩︎
- Automating the design space exploration process to reduce analysis time by 30 to 50 percent ↩︎
- Cash positions increasingly critical for US electric air taxi developers – Howard Hardee ↩︎