CFD for clean air. 3 ways to fight contamination in public buildings, transportation and production facilities

This work is based on a previous blog by my former colleague Prashanth Shankara
Until 2020 Computational Fluid Dynamics aka. CFD for clean air was clearly not something the general public took notice of. But when the coronavirus pandemic spurred the global community into action unlike any other time in recent history, the need for clean, healthy air suddenly became more evident and a bigger matter of public attention than ever and with it CFD made it into mainstream media. And while COVID-19 seems long gone, and with it the public attention, the general need for clean purified air in public facilities, offices and transportation remains an important factor of life quality. But it’s is not only humans that need a certain air quality standard for a healthy living, likewise there are many products for whose production hygienic standards are very high and air contamination can pose a large harm to their respective industrial production facilities.



In this constant challenge for healthy and uncontaminated air, computational fluid dynamics (CFD) simulation can be a crucial asset. CFD simulation software from Siemens’ Simcenter portfolio is used by industry in various applications to ensure air gets purified and we can breathe safely and manufacture correctly performing products efficiently.
3 ways CFD simulations help to ensure clean air
It goes without saying that CFD simulations cannot (and should not) be used as public health guidelines. But CFD simulations, if applied right, can help in 3 ways:
- Understand transport of unwanted human or non-human source exhalations, concentration and mitigation
- CFD simulation offers multiple approaches to model droplets and aerosols and their transport in space and time. CFD simulations can show where these particles travel to, how long they stay in air and what surfaces they impinge on.
- This would generally be useful in a small indoor setting with some sort of controlled airflow (rooms, cars, trains, planes, clean rooms, food production facilities, etc). Outdoors, the number of variables increases and forming any conclusive
- Improve/Redesign indoor environments for safety
- CFD simulations have long been used to understand indoor air flows and design HVAC systems and indoor environments for comfort and safety.
- CFD combined with design optimization can help analyze hundreds of ‘what-if’ scenarios for indoor environments.
- For example, you can analyze multiple venting configurations and air curtains to ensure most of the droplets and aerosols in a room are removed.
- Air purifiers and disinfectants can be designed and arranged to focus on areas of high droplet concentration.
- Design equipment to remove hazardous substances and purify air
- How do you sterilize and purify indoor spaces? Here, CFD simulations can help in designing purifying equipment.
Today companies use such CFD methodologies to predict the spread of contaminating particles, hazardous gases or even viruses in almost anything, from public buildings, like airports, offices, schools or train stations, through public transport, like in airplanes, buses or trains to industrial facilities for wafers, food or pharmaceuticals. The following examples show how Siemens customers have used CFD simulations in the fight for clean air.
CFD for clean air in (public) transport
For the transportation industry (planes, trains and automobiles….ships too), COVID-19 has brought the indoor spaces into greater focus. Since then continued efforts have been made to ensure clean air in any type of vehicle – especially in those that move a large number of people.
Airbus – Understanding cough droplet propagation in aircraft cabin
Siemens and Airbus are using Simcenter STAR-CCM+ to understand the transport of particles/droplets from a human cough in an aircraft cabin.
Using CFD simulations, the team has modeled the transport of cough droplets in an aircraft cabin. The impact and effectiveness of face masks in reducing droplet transmission in an aircraft is modeled too.
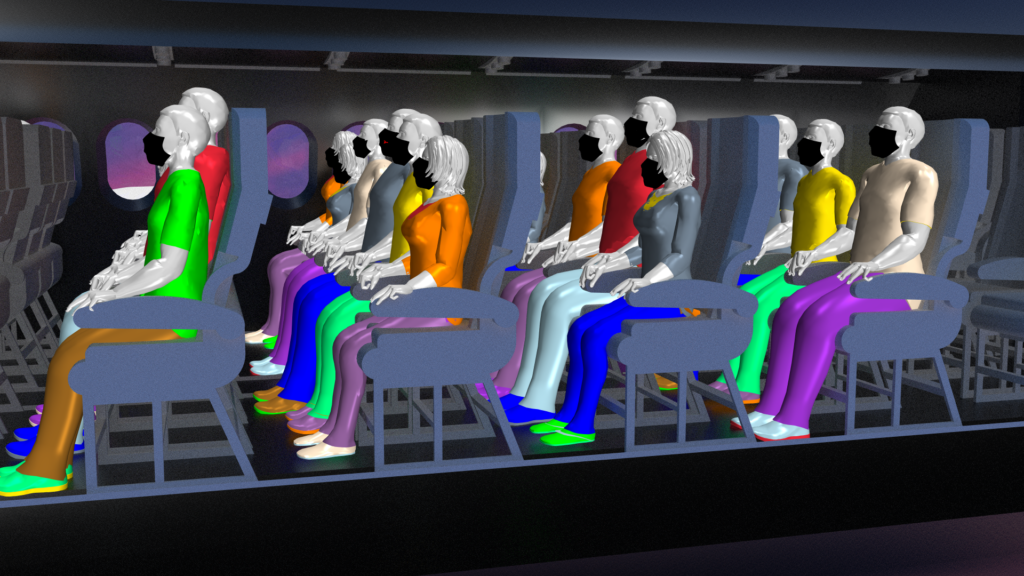
The joint team developed the CFD methodology that tackles three things:
- Simulation of cough droplets from an average human
- Challenges in modeling aircraft cabin environment
- Steps involved in understanding risk of virus transmission from cough droplets
Norton Straw (now element Digital Engineering) – ventilation in trains

A UK Rolling Stock Owning Company (Trains, for readers from the rest of the world) contacted Norton Straw (now element Digital Engineering) to help minimize transmission on-board the trains. Using CFD simulation with Simcenter STAR-CCM+, the engineers at Norton Straw analyzed the airflow in the train cabin resulting from many mitigation strategies – windows open, plastic shield between passengers, different ventilation air flow, etc.
The simulation results, also presented with Simcenter STAR-CCM+ Virtual Reality (VR), helped the manufacturer assess the ventilation effectiveness of different cabin configurations
UES/USAF – Evaluating biological agent transport in aircraft


How do you identify bioaerosol contamination hot spots in a medical aircraft and confirm decontamination after exposure?
UES, Inc. partnered with the US Air Force Research Laboratory’s 711th Human Performance Wing (HPW) to find the answer using Simcenter STAR-CCM+. Simcenter Engineering Services helped the team to simulate a cough from an infected passenger in a C-130 Hercules aircraft with multiple passengers.
The results from the CFD simulations will be used in guiding improved procedures and sampling strategies for bioaerosol detection and surface decontamination. This helps the US Air Force make critical decisions regarding transport of infectious patients.
CFD for clean air in buildings
Another area where CFD simulations can be of great use is immobile indoor spaces where again the airflow and ventilation can be controlled.
HOLT Architects/ME Engineering – Creating safer office spaces with CFD
HOLT Architects, in association with M/E Engineering, published some interesting results on their strategies for reducing airborne transmission of viruses. M/E Engineering are well known for their expertise in CFD modeling. Using Simcenter STAR-CCM+, they have helped HOLT architects study droplet transmission in their Ithaca, NY office. This study and the redesign of the ventilation system is helping employees work safely in the office.
CAD models of the actual office space were used. When COVID was at its height CFD simulations of multiple coughs with and without a face mask were analyzed with Simcenter STAR-CCM+. The analysis considered office arrangement, furniture, air flow patterns, barriers and location of people. Even if masks in office spaces are a thing of the past again, this kind of environment-specific cough simulation can help redesign HVAC and indoor ventilation systems. The smaller the space (and indoors), the lesser the variables that control droplet transmission.
What if an infected patient coughs? What if the HVAC system is changed? What if a window could be open? Where to face sterilization/disinfection devices? Just some of the questions that CFD can answer here.
JB&B – CFD simulations show opening windows is key to healthy schools
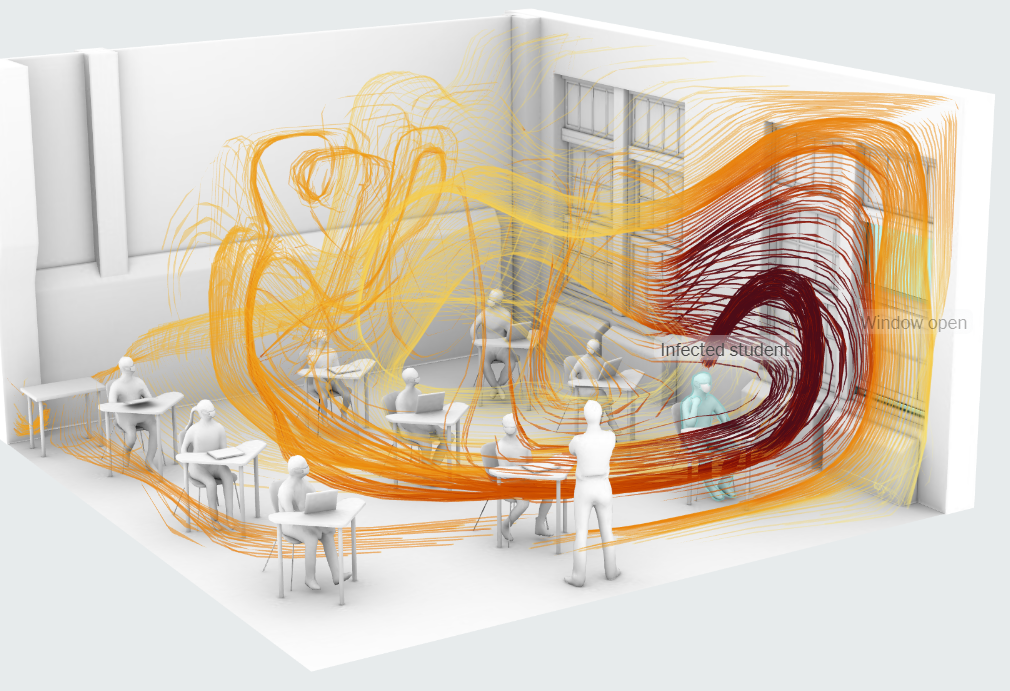
Jaros, Baum & Bolles (JB&B), an engineering consulting firm, worked closely with the New York Times to show how schools can reduce COVID-19 exposure in classrooms by opening windows. The engineers at JB&B used CFD simulations to show how contaminants from an infected student circulate in a classroom for three scenarios – windows closed, windows open and with a fan and air cleaner installed.
The story in New York Times is a must-read and is a brilliant visual representation of how to generally keep infected contaminants to a minimum in a classroom setting.
CFD to design sterilizing and purifying devices
Excelitas Noblelight – Developing UVC air purifiers with CFD simulation

Excelitas Noblelight GmbH has been developing specialty light sources since the invention of the quartz glass lamp in 1904. Light, whether ultraviolet (UV), infrared (IR)or middle wave range, is at the heart of everything they do. The company has harnessed the power of light to solve a wide range of challenges in the manufacturing and process industries. With the help of CFD they also design and manufacture consumer products like the Soluva® air purifier, for removing airborne viruses from healthcare settings, public transport and classrooms. Engineering simulation is not only used during the product development phase, but also to understand the best way to deploy products in the field.
We use CFD simulation to help our customers understand their processes and where to locate our UV or IR emitters to make them most effective.
Dörte Eggers, simulation engineer at Excelitas Noblelight
Norton Straw (now element Digital Engineering) – Novel air sterilization device
In a similar fashion, abovemnetioned Norton Straw (now element Digital Engineering) used Simcenter STAR-CCM+ to develop a novel concept of air sterilization device. Using CFD simulations and design optimization, the company has designed a small, light and energy efficient sterilization device. The device won the Innovate UK Covid Response Grant. The easily manufacturable device is currently being produced with additive manufacturing. Treating the recirculated air in indoor environments with such an air sterilization device is a solution for rail, automotive and building applications.
Right: Velocity contours inside a plate and fin heat exchanger inside the award-winning air sterilization device. CFD simulation using Simcenter STAR-CCM+

CFD for clean air in production facilities
The application of CFD for clean environment does not stop at providing healthier environments for human beings. Also production lines of products that require high hygiene and material purity standards need to be kept free from hazardous gases, particles, mist or dust.

FS Dynamics establishes a CFD method to assess contamination in lithography machines

At the 2024 Realize Live Conference Europe, CAE Simulation Consultant FS Dynamics presented a high fidelity CFD methodology to assess contamination in lithography machines a key production facility in the Semiconductor Industry. Their work addresses the longstanding challenge of contamination modelling in lithography machines with a moving wafer using Computational Fluid Dynamics (CFD) simulations. Traditionally, the morphing and remeshing technique had been employed for capturing wafer motion while assessing airflows and contamination routes, despite its inherent slowness due to the remeshing bottleneck. FS Dynamics developed a refined methodology that leverages the overset meshing technique, a previously overlooked approach due to assumptions of its unsuitability for contamination modelling with low contaminant species concentration. Exceeding expectations, the novel CFD approach not only proves to be suitable for contamination modelling with moving wafers but also turned out to significantly reduce the computation time, enabling faster development cycles and more agile design iterations for super-clean Lithography machines.
Creaform Engineering uses CFD for contamination-free vaccine filling lines


The design of cleanrooms for manufacturing vaccines and other medications is precisely the topic of one of the articles in our Life Sciences Special Report, a compilation covering a range of applications of CFD, from medical device design to pharmaceutical manufacturing processes. In that article, companies Creaform and Laporte collaborated to perform a highly-detailed simulation of a cleanroom for vaccine manufacturing, to gain predictive insight to complement the traditional smoke tests in the process of cleanroom commissioning. The CFD simulations were used to demonstrate the effectiveness of the aerodynamic barriers and ensured proper flow path around non-sterile components of the machines. As pointed out in the article, “Not only was the regulatory compliance of the cleanroom at stake but with the high production rate of the line (hundreds of vial fillings per minute), contamination would represent a considerable financial and time loss because it leads to the waste of vaccine doses.”
Clean Air uses CFD to virtually test fume cupboards

Fume cupboards are essential for laboratories that generate airborne hazardous substances during experiments, processes and scale-up. They are designed to capture and remove gases, vapors and aerosols to reduce the risk of exposure to a safe level. In the 30 years that Clean Air Limited (Clean Air) has been designing, manufacturing and installing fume cupboards, protecting people has always been its priority. One of Clean Air’s unique selling points is its commitment to lead the fume cupboard industry in environmental safety and sustainability.
Sulfur hexafluoride (SF6) is used to prove the effectiveness of a fume cupboard during testing, but it has been identified as the most damaging greenhouse gas. The equivalent of approximately three tons of carbon dioxide (CO2) is released during type testing, and another ton is released during onsite testing. Most fume cupboards are tested with the on site test, so roughly 1t CO2e per cupboard then 3t per ‘type’ of fume cupboard. To reduce the carbon footprint Clean Air worked with Siemens partner Maya HTT and developed a new process that replaces design testing with computational fluid dynamics (CFD) simulation, ensuring that performance and safety is guaranteed without impacting the environment.
Fighting for clean air with CFD cannot stop at the cleanroom’s door
And while these examples show in an encouraging way how humans (with the help of engineers) have the technology to improve air quality in constrained spaces and closed systems, we have to face that these efforts are merely enough. After all there is an outside world that you cannot avoid. According to WHO data an unbelievable 99% of the global population breathe air that exceeds WHO guideline limits and contains high levels of pollutants, with low- and middle-income countries suffering from the highest exposures.
And so fighting for clean air (also with CFD) cannot stop at the cleanroom’s door.
Comments