Aircraft structural design and analysis: how to mitigate nonrecurring costs
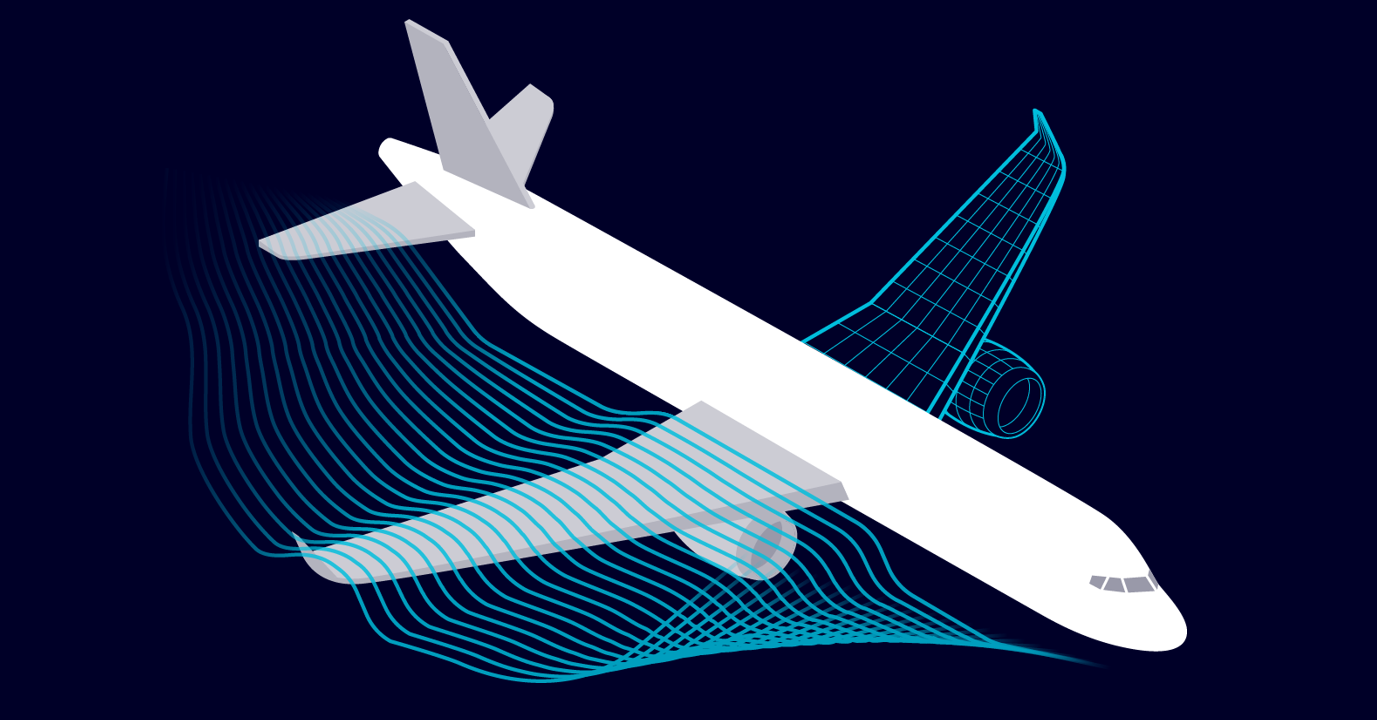
Modern aviation demands innovation for efficiency and sustainability. Aircraft must be lighter, more fuel-efficient, and quickly developed while ensuring safety. Optimized aircraft structural design and analysis processes are crucial to reduce inefficiencies while maintaining airworthiness.
In other words, aerospace engineers are striving to meet several key objectives to enhance aircraft performance and sustainability whether for military, commercial, or general aviation.
The primary focus is to achieve optimal airframe design for efficiency. On one hand, these design goals aim to lower environmental impact and operating costs. On the other hand, it also enables mission-critical aircraft to operate for extended durations at higher altitudes with the same fuel capacity. Additionally, engineers are working to improve weight distribution to optimize the aircraft’s balance and overall performance.
Another focus area is the development of electric-powered aircraft, which presents unique challenges and opportunities. Enhancing battery density and heat dissipation capabilities is essential for maximizing the efficiency and reliability of electric propulsion systems.
Furthermore, the exploration of alternative fuel sources like hydrogen and innovative aircraft configurations such as strut-braced or blended wings is a key objective in the quest for sustainable aviation.
Manufacturers face significant aircraft structural design issues
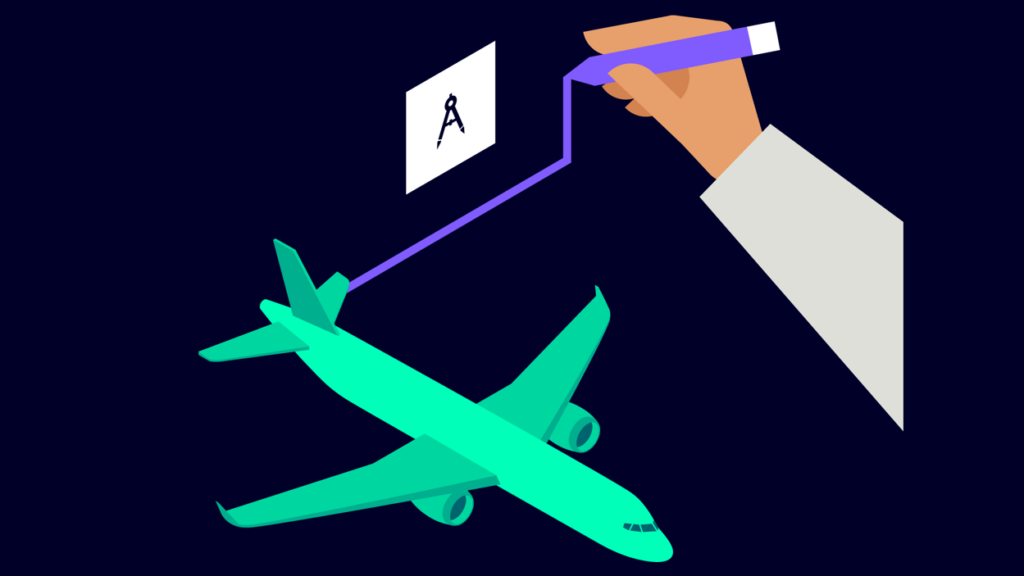
With growing design complexity, manufacturers face structural engineering challenges in aircraft structural design and analysis that hinder efficiency and innovation. One key issue is the disconnected nature of design and analysis teams, who often work in isolation, leading to rework and inefficiencies, ultimately impacting the overall development process and the program success.
Additionally, engineers waste valuable time manually extracting data and generating reports while dealing with aircraft structural design and analysis, a process that should be streamlined through automation, freeing up resources for higher-value work. This challenge highlights the need for innovative solutions that can enhance efficiency and productivity in engineering workflows.
The absence of interconnected tools further complicates the rapid exploration of alternative design options, resulting in a lack of analysis capabilities that are essential for facilitating quick design testing and optimization.
Furthermore, navigating the diverse inputs and specific requirements of multiple stakeholders involved in the program can significantly complicate and elongate the development process.
Ultimately, the prevalence of disconnected systems results in inefficiencies and errors, underscoring the need for a unified, digitalized end-to-end process to optimize workflows and unlock new levels of innovation in aircraft structural engineering.
The high cost of aircraft structural design and analysis and its impact on nonrecurring costs
Aircraft complexity can be a multifaceted aspect that varies based on aircraft class type. In a simplified model, we can consider three main classes with two extremes and one class in the middle. The first class represents a business jet, showcasing a relatively high level of complexity across its empennage, wings, fuselage, and control surfaces. Moving towards the class in the middle, we have a narrow-body commercial plane, characterized by an even higher level of complexity across all components. Finally, at the other extreme end, a multirole fighter jet stands out with the highest complexity levels for its various components.
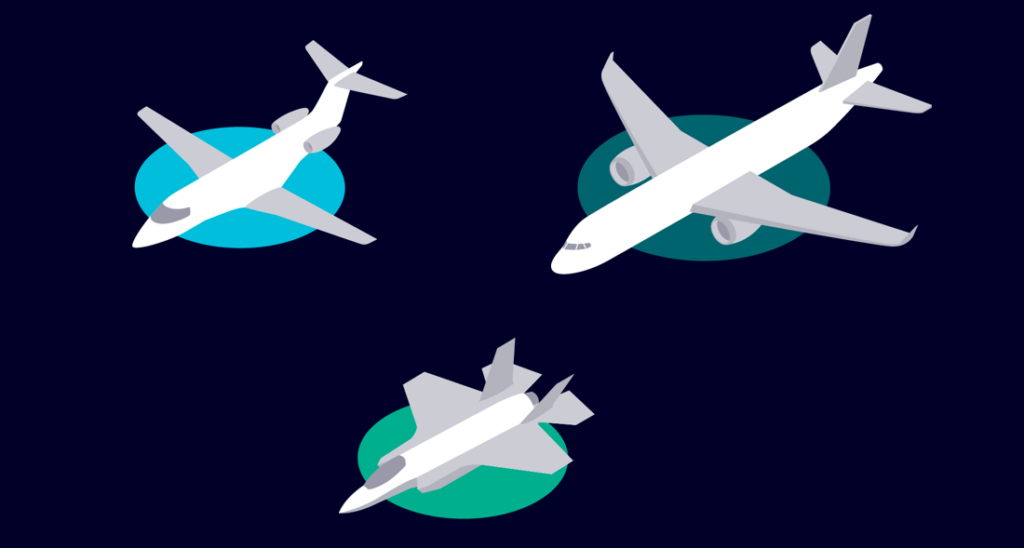
It is essential to highlight that engineering aircraft structures play a significant role in determining the total nonrecurring cost of aircraft. For the different aircraft classes including small business jets, commercial airliners, and fighter jets the percentage of structural nonrecurring costs may vary within a certain range. To set a benchmark, it is estimated that engineering aircraft structures for a commercial airline could weigh up to 65 percent1 of all total nonrecurring costs.
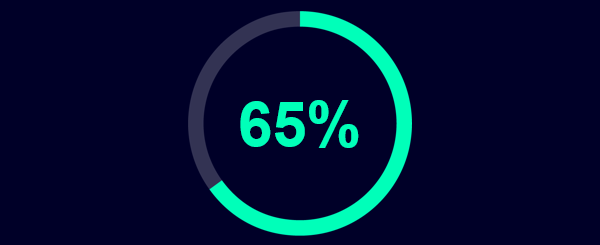
Despite potential differences that might be observed depending on the class, the importance of conducting thorough aircraft structural design, analysis and testing cannot be overstated, as it is crucial for ensuring airworthiness and safety.
Across different aircraft classes, manufacturers and integrators are charged with the responsibility of effectively managing structural engineering costs to maintain competitiveness, ensure profitability, and achieve program success.
What strategies can aerospace engineers employ to mitigate nonrecurring costs?
Aerospace engineers can implement an integrated simulation and testing approach, utilizing best-in-class aerospace simulation software to drive digital transformation. This approach can result in a seamless integration of robust engineering workflows that facilitate the adoption of targeted mitigation strategies. These strategies are designed to not only minimize costs but also achieve performance targets and ensure a smooth introduction into service.
A rigorous and creative structural engineering workflow
Modern structural engineering for aircraft should encompass a resilient and flexible workflow that enables both rigor and creativity to ensure the structural integrity and performance of the aircraft. This intricate series of specialized tasks, spanning design engineering disciplines such as weight and balance calculations, aerodynamics and performance analysis, external and internal load assessments, fatigue analysis, and damage tolerance evaluation, forms a cohesive and efficient journey from initial concepts to detailed designs, with each phase presenting distinct challenges.
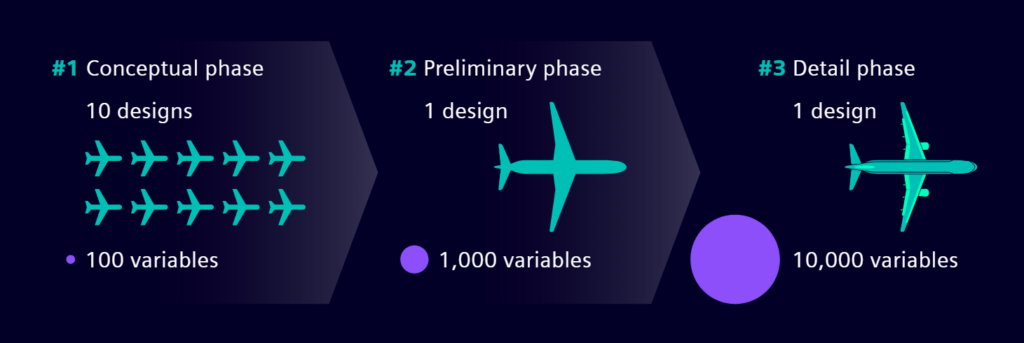
Throughout this comprehensive process, structural engineers must navigate a fine line between analytical precision and inventive problem-solving. By embracing this approach, they can craft aircraft structures that are not only optimal in their design but also high-performing in their identified missions.
Enhancing program efficiency through automation and exploration
Automation and the ability to rapidly explore design alternatives are essential strategies to improve program performance and mitigate nonrecurring costs in aircraft structural design and analysis. By embracing automation, engineers can save valuable time and streamline their workflows. One of the primary challenges they face is the manual, time-consuming nature of data extraction and report generation. Automating these repetitive tasks frees up resources that can be better allocated towards higher-value work, such as design optimization and problem-solving. Automated data management and report generation not only improve efficiency but also ensure consistency and accuracy, minimizing the risk of costly errors.
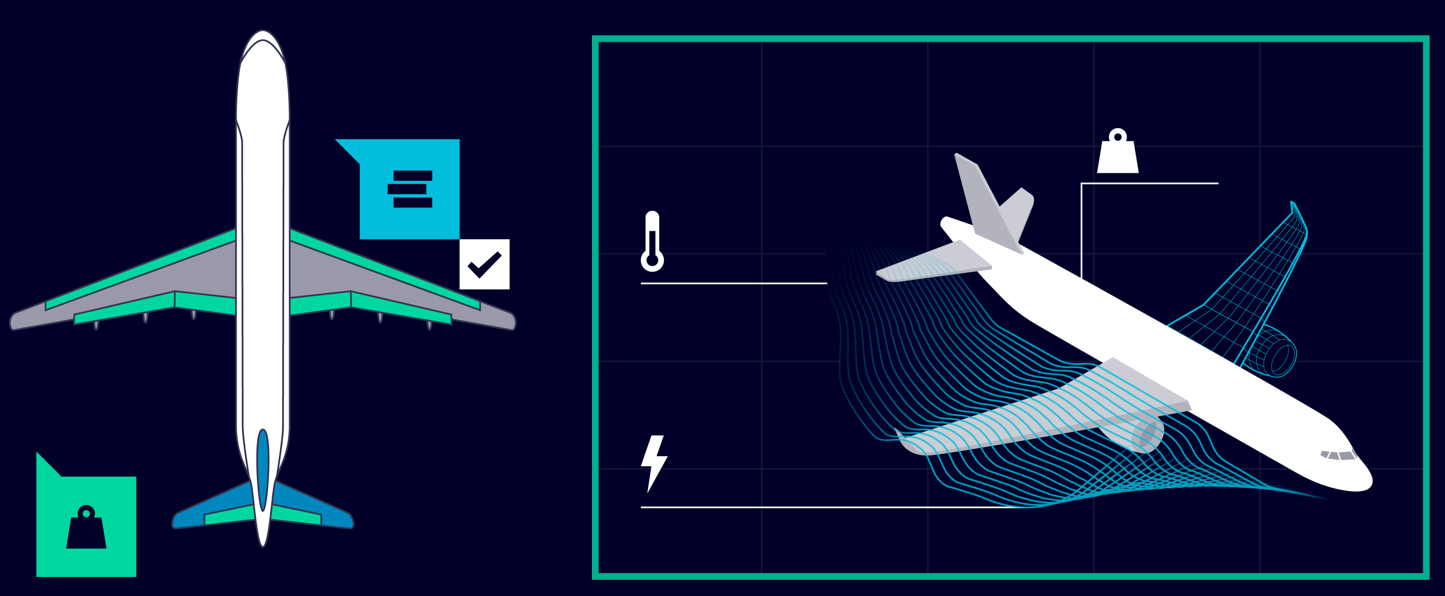
Indeed, the empowerment to rapidly explore and evaluate alternative design options is essential in driving innovation. Traditionally, the lack of connected tools and siloed workflows has hindered engineers’ ability to quickly test and refine their designs. By enhancing analysis capabilities and leveraging digital collaboration platforms, engineers can now iterate on designs more seamlessly, accelerating the development cycles and unlocking new possibilities. Through strategic automation and the freedom to creatively explore the design space, manufacturers can achieve weight reduction, increase fuel efficiency, and improve safety. These capabilities can significantly reduce nonrecurring costs associated with aircraft structural engineering.
Taking the traceability burden off the engineer
Moreover, improved digitalization of aircraft structural engineering can significantly alleviate the traceability burden on engineers, unlocking key advantages to mitigate nonrecurring costs. With seamlessly tracked design changes, the digitalized workflow enables more efficient certification documentation and deployed configuration-controlled simulations. This, in turn, secures the relationship between individual aircraft components and the overall load, achieving trustworthy traceability throughout the design and analysis process. As a result, engineers can more easily prove compliance to certification authorities, reducing the manual effort required.
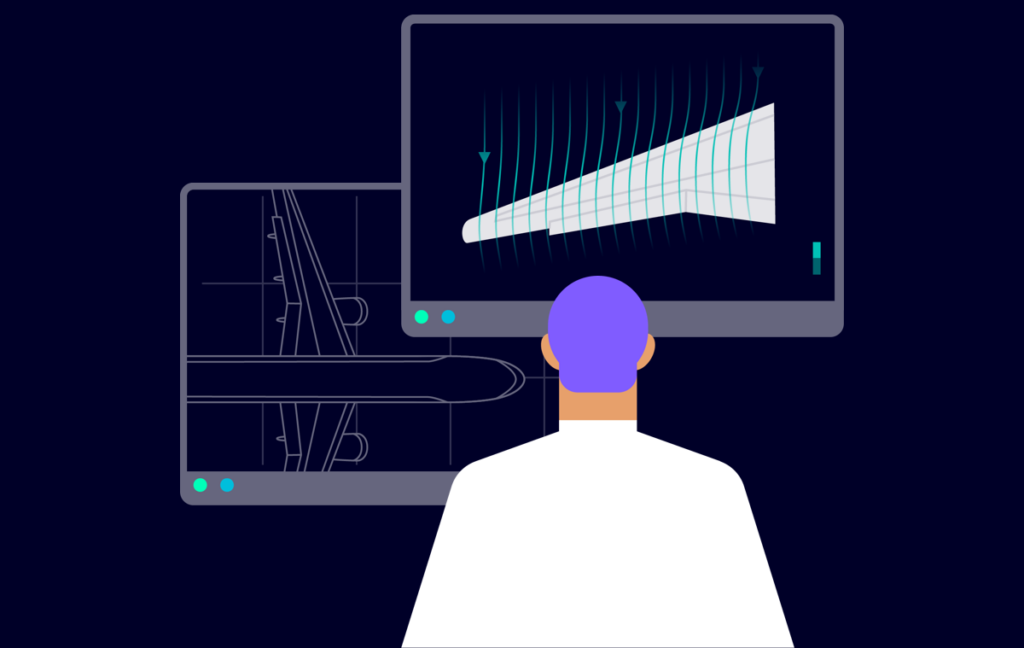
One of the possible approaches to mitigate non-recurring costs is taking the traceability burden off the engineer through enhanced digitalization. As a result of that manufacturers can optimize their structural engineering workflows, focus on higher-value tasks, and ultimately drive down the substantial impact of structural engineering on overall aircraft program costs.
Conclusion
The Simcenter™ software simulation and testing solutions, a part of the Siemens Xcelerator business platform comprising software, hardware, and services, significantly enhance the structural engineering workflow. For example, it enables enhanced and digitized collaboration between flight physics and structural analysis departments, reduces traceability costs, and ensures that data is stored, traced, and readily reusable in subsequent programs. These advancements facilitate simulation-driven optimization in aircraft structural design and analysis, potentially resulting in cost savings of up to $103 million for a narrow-body aircraft.
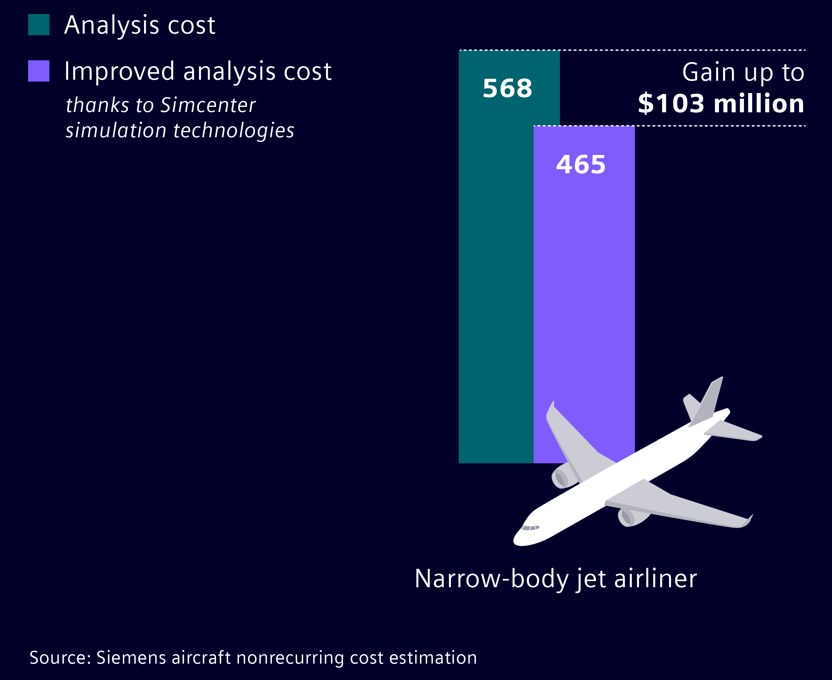
For more information on additional mitigation strategies and cost savings across various aircraft classes, download our infographic titled “Mitigating Nonrecurring Costs in Aircraft Structural Design and Analysis.”
Finally, if you are seeking in-depth technical insights into aircraft structural design and analysis, I invite you to explore the research paper l delivered at AIAA and highlighted on the Kudos website titled “Integrated Structural Design and Analysis Applied to a Large Surveillance Drone”.
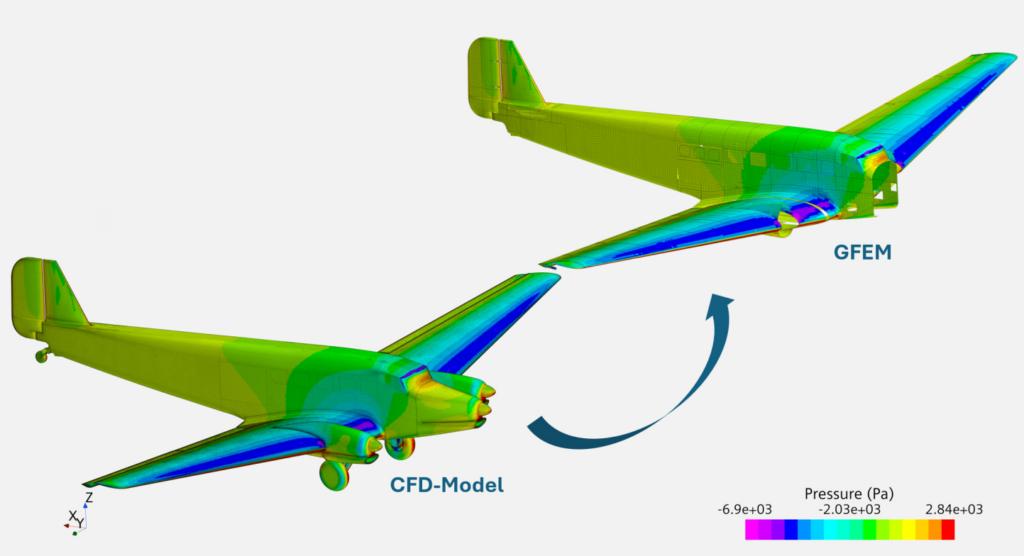
CASE STUDY
AeroFEM GmbH
Bringing the iconic Junkers Ju 52 aircraft back to life digitally
- Source: “Aircraft Cost Model for Preliminary Design Synthesis”, by Tim Lammering et al., AIAA 2012-0686 ↩︎