The five keys to next-generation IC packaging design: Part 2
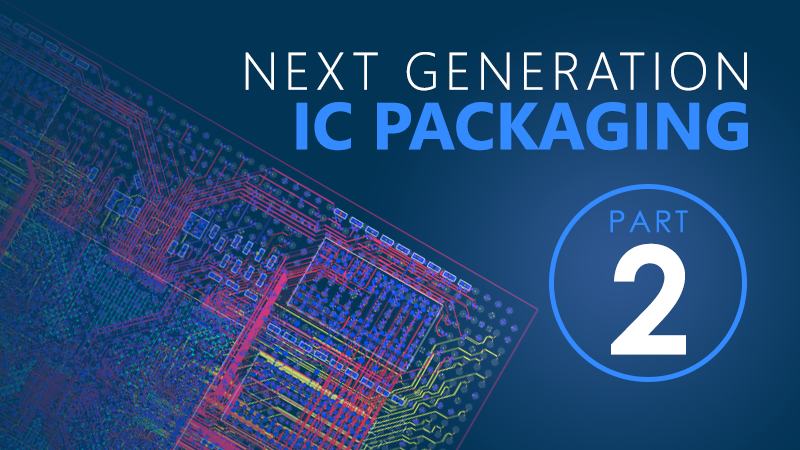
Part 2: Multi-domain integration for advanced semiconductor packaging
In the last blog, I talked about the new challenges presented by advanced semiconductor packaging and why a system-level, digital-twin prototyping approach is a proven design methodology for heterogeneous multi-die and multi-substrate design, verification, and signoff. (If you missed it, click here to read it.)
In this blog, I’ll explore the multi-domain and cross-domain integration that a digital twin methodology enables. Bringing more complex advanced semiconductor packages to market faster requires more seamless integration of design and verification, from electronic substrate design to mechanical package heatspreaders/heatsinks and PCB mounting hardware, including the inter-related aspects of electrical, thermal, test, reliability, and, of course, manufacturability.
The importance of multi-domain integration
Advanced semiconductor packages contain multiple dies of different process nodes integrated on and through multiple substrates. Without a system-level approach to design and verification you risk experiencing costly re-spins or worse. Sticking with traditional disaggregated design and verification approaches is no longer an option.
According to a recent Aberdeen group survey, 82 percent of best-in-class companies utilize a system that allows for ECAD and MCAD design data to be incrementally exchanged throughout the design process. These companies realize that synchronization of electrical and mechanical information is essential to ensuring that no physical violations occur when a package is placed within an enclosure or an entire system. They determined that the incremental exchange of data during design is fundamental to ensuring ECAD-MCAD compatibility and increased first pass success. It also aids in the creation of more robust designs while increasing productivity and achieving faster time to market.
This research showed that around 50 percent of today’s advanced CPU/GPU/MCU semiconductor package designs required at least one additional design iteration to address electro-mechanical integration issues. Typically, this iteration was regarding the design and integration of a custom Integrated Heat Spreader (IHS), which was key to overall device thermal management. In this design scenario it was deemed important that both the semiconductor package designer and the IHS designer can visualize, explore, and optimize the integration, ideally as an asynchronous process that minimizes cross-domain interruptions and prevents such avoidable design iterations.
Now this is just one example of the importance and need for multi-domain integration based around a digital twin model. Other areas include thermal management, mechanical stress analysis, signal integrity analysis and of course 3D EM modeling and extraction and even more.
If this is something you would like to read more about then please download this white paper.