Bringing New Innovations to Market with Maestro Product Design
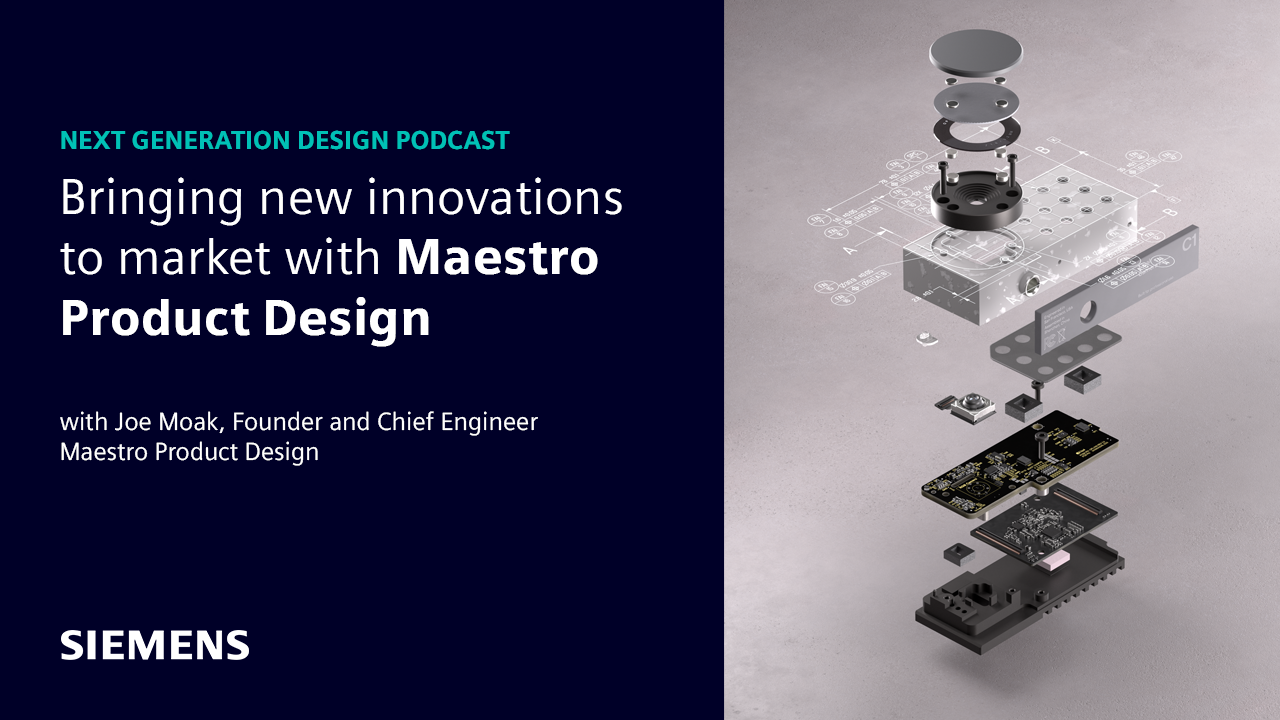
How do you create world-class products that seamlessly blend form, function, and user experience? What role do experience-driven design, sustainability and digital twin technology play in shaping modern product design?
On this episode of the Next Generation Design podcast, host Greg Arnot sits down with Joe Moak, Founder and Chief Engineer at Maestro Product Design and Senior Product Architect at Meta. Together, they explore the intricate world of experience-driven product design, the evolution of engineering tools and the balance between innovation and manufacturability.
Joe shares his journey from a curious young engineer inspired by a Sony Handycam to leading groundbreaking design projects at Apple and beyond. He discusses how Maestro helps clients across industries—from consumer products to medical devices—achieve high-quality, high-volume production while staying true to their design vision.
They also dive deep into the power of Siemens’ NX, the role of digital twins in product development and how new technologies like immersive design are revolutionizing the way engineers approach problem-solving.
Whether you’re a seasoned engineer, a product designer or just fascinated by the future of design and manufacturing, this episode is packed with insights that will expand your perspective on the next era of engineering.
What you’ll learn in this episode of the Next Generation Design podcast:
- Who is Maestro Product Design, and how do they approach engineering? (1:30)
- The balance between design vision and manufacturability (5:40)
- How Joe was introduced to CAD and NX (8:15)
- Advice for new CAD learners (8:50)
- The experience-driven design process at Maestro Product Design (10:35)
- The benefits of leveraging NX CAD at Maestro (12:55)
- Trends in the evolution of industrial design and product development (20:10)
- Advice for aspiring engineers and startup founders (25:40)
You can always listen to the Next Generation Design podcast right here, or wherever you do podcasts.
Read the summary or watch the video version of this episode: End-to-end product engineering with NX CAD | Maestro Product Design
Listen to or read the next episode of the Next Generation Design podcast: From 2D to 3D: A Model Based Definition Design Process at MTU Aero Engines Releasing Tuesday, April 15, 2025
Listen to or read the previous episode of the Next Generation Design podcast: Siemens Technology Empowers Engineers to Create Sustainable Products
Hybrid modeling that we’re able to do in NX, where we’re able to use the parametric history-based tools right alongside the direct modeling tools. I find that incredibly enabling, certainly in early phases of architecture, where we’re trying to understand the design space. It ends up speeding up the development.
Joe Moak, Founder and Chief Engineer, Maestro Product Design
Podcast transcript for Bringing New Innovations to Market with Maestro Product Design
Joe Moak
At Maestro, we focus super heavily on the details of the customer experience that our clients intend their products to deliver to their customers. What that means is we want to understand what that means in terms of metrics that we can sort of track and measure and engineer against. Once we have our hands around what the core experiences are and what the most important experiences are, then we’ll apply engineering fundamentals, get back to first principles, and really focus on designing the specific bits that deliver those experiences, and we move very quickly as we’re often building a lot of physical prototypes. Once we have an understanding of how to deliver those core experiences, we will start packaging up those bits of design into a product embodiment.
Greg Arnot
You’re listening to another episode of the Next Generation Design Podcast. I’m your host, Greg Arnot. On today’s episode, I’m joined by Joe Moak, founder and chief engineer at Maestro Product Design and senior product architect at Meta. Before we start, let’s say hello to today’s guest. Joe, welcome to the show.
Joe Moak
Great to be here. Thanks for having me, Greg.
Greg Arnot
I’d like to begin by learning a little bit more about your company. What can you tell us about Maestro Product Design?
Joe Moak
We’re an experience-driven design and engineering company, meaning that we focus on the details of the customer experience that our clients intend to deliver to their customers. And we do industrial design, product design engineering, and electrical engineering from concept all the way through high-volume production.
Greg Arnot
You’re the founder and chief engineer at Maestro, can you tell our audience a bit more about your current role and how the company came to be?
Joe Moak
It’s my company that I started from scratch and, man if we go back far enough when I was a grubby little 12-year-old riding dirt bikes out in the woods where I grew up, my family saved up and bought a Sony Sports Handycam and I just remember being in awe of this object that had never existed before and certainly existed now. There were all kinds of seals and mechanisms and motors, and I thought, “Man, this thing’s really a work of art and we can take it out into the woods and record ourselves being silly and having a good old time. And I want to make something that’s this cool when I grow up that enables people to have similar joyful experiences.”. I started asking around in the rural community of origin where I grew up and the best we could come up with was we thought mechanical engineers designed those kinds of things. And that’s when I decided, “Okay, well, I guess I’ll be a mechanical engineer” and studied mechanical engineering at Cal Poly. And then got me a job in the medical device industry and worked there for just shy of a decade and got into consumer products after that through Apple and eventually decided that I would like to help as many organizations as I can achieve really, really aspiring goals when it comes to delivering really high-quality hardware at really high volumes. And a consultancy seemed like the model that would best enable that kind of engagement, and that’s where Maestro came from.
Greg Arnot
Well, it sounds like it was all meant to be. What have you learned over the course of your career as you’ve continually taken on ever more responsibility and ownership?
Joe Moak
I started out my career as most engineers do, sort of designing parts and maybe small subsystems. And yeah, over the course of my career, I just kept taking on more and more ownership, doing everything I could to influence and impact a positive outcome for customers of the hardware. Eventually, that meant that I was leading teams, that meant that I was building teams, that meant that instead of spending a lot of my day working with kind of the cross-functional technical teams, I ended up working with director-level and even a VP and C-suite level folks. And I never necessarily sought or aspired to own a company and build teams, it just was sort of necessary to get the job done.
Greg Arnot
I’m curious, what kind of companies and clients is Maestro working with? Are there any specific industries that you specialize in?
Joe Moak
We work across a breadth of industries, including consumer products, of course, we do quite a bit of medical, we’ve even done some enterprise, and man, we even have an action sports type project in the portfolio as well. We typically find great partnerships with clients who are aspiring to either level up their current product quality or enter the market at a higher premium price point and they also want to get there quickly. And we’re able to engage across the entire development process. We’re just as comfortable with a blank sheet of paper figuring out what a product and a company could be as we are in a factory dialing in and optimizing high-volume production processes.
Greg Arnot
Being in such a fast-evolving industry, I imagine you see many changing trends and challenges.
Joe Moak
The trends and the challenges fundamentally, haven’t changed much. There’s this sort of thread of tension between design and manufactured reality. And there’s a trick to managing the design and engineering teams to kind of reconcile manufactured reality with that design vision. It’s really easy for teams – and I’ve seen this happen in many different organizations, and many different teams, regardless of industry – teams make a series of seemingly small decisions as they work their way through the process and it’s really easy to lose sight of the North Star and lose sight of some of the customer experience goals. And what ends up happening is after you go through that long process, what ends up coming off the production line falls short of the vision that we had when we started the program. It’s kind of a death-by-a-thousand paper-cuts situation. We put a lot of effort into understanding how every decision is going to affect the customer experience, no matter how small it may seem.
Greg Arnot
I really like that analogy. Now, it’s been years since I was an electronic engineer but I remember appreciating how each individual cog in the wheel is doing their very best to deliver their bit to perfection without necessarily having sight of the overall vision that they’re driving toward.
Joe Moak
Yeah, that’s 100 % correct. And it’s often not because the engineers are bad or that the designers are bad or that they’re trying to make things worse. Most often, it’s sort of a lack of understanding, a lack of product context. Again, it just requires a good sort of oversight and leadership to make sure that those team members are equipped with that context when they’re doing their work.
Greg Arnot
Joe, I’d like to switch gears and talk a bit about CAD. Can you tell our listeners how you were first introduced to CAD software?
Joe Moak
I was first introduced to CAD, gosh, I think in 1988, running CADKEY on MS-DOS, probably version three, not that anyone cares. The gray in the beard is real, man, I’ve been here for a while. I’ve used over a dozen different CAD packages. When I say used, I’ve designed parts and made parts in at least a dozen different packages.
Greg Arnot
And do you remember when and how you were first introduced to Siemens NX?
Joe Moak
I started using NX in 2006 when I joined Apple. I remember my first NX training session with Steve at Design Visionaries, it seemed about the same as what I was using previously and after about six months at Apple, I started to get the hang of it. And in about nine months, I felt like my hands weren’t tied behind my back anymore and I’ve never looked back.
Greg Arnot
Sounds like you’ve got quite a few years of experience under your belt. Do you have any advice for someone trying to learn NX or CAD software for the first time?
Joe Moak
The first thing is just to jump into NX if you can. I know that NX may have a reputation for being expensive and that’s lately not necessarily the case. There are definitely ways that you can get your hands on it. It’s a great tool. When you’re using NX, embrace history-based modeling and direct modeling. That’s one of NX’s superpowers. Don’t be afraid of that remove parameters command either as you get into it.
Greg Arnot
At Siemens, we like to say that NX is at the heart of the most comprehensive digital twin. From your perspective, what does the digital twin mean to you and how is it impactful?
Joe Moak
I know that there’s a sort of an industry definition around digital twin that is something like you’ve got a simulation or a model of a factory and then you’ve got a factory running and you’re sending inputs from sensors in the factory to your model ao you can kind of watch the simulation run in real-time. In the world that I live in where we’re doing these electronic products, we typically don’t get that sophisticated with digital twins, but for the longest time, I’ve considered my simulation models a type of digital twin in that we’ve got multi-physics being applied to these products that we’re designing, sort of representing loading conditions and thermal conditions and sometimes even abusive conditions.
Greg Arnot
Yeah, bringing multi-physics into simulation can get pretty hairy. Taking a bit of a step back, can you tell me a little bit more about the overall design process at Maestro? What’s it like and how do things start once you get a client?
Joe Moak
We have a bit of a unique process at Maestro in that we focus super heavily on the details of the customer experience that our clients intend their products to deliver to their customers. What that means is we want to understand when a client says that something needs to be tactile, for example, what that means in terms of metrics that we can sort of track and measure and engineer against. Once we have our hands around what the core experiences are and what the most important experiences are, then we’ll apply engineering fundamentals. We get back to first principles and really focus on designing the specific bits that deliver those experiences and we move very quickly as we’re often building a lot of physical prototypes and – we call them test boxes – once we have an understanding of how to deliver those core experiences, then we start packaging up those bits of design into a product embodiment. And then at that point, the process looks very similar to processes you might see at other consumer product companies where we’re doing a proto-phase, EBT phase, DBT phase, and PBT phase.
Greg Arnot
And if somebody does want something tactile, what does that entail?
Joe Moak
There are just so many factors that affect tactility. I’ve got a hundred slides on all of these little elements. Zooming way out, I’ll pick an example of a button. If a product is otherwise sort of looking and feeling great and you squeeze a button or you press a button and it feels mushy, then your understanding of the value of that product has been degraded and oftentimes irreparably. So when we’re thinking about button tactility, we’re thinking about click ratios and button travel and button stability and fit and finish of the button. So there are a lot of different elements, but the engineer in me, my head immediately goes to the sort of the force-deflection response and how that click curve looks and how it feels.
Greg Arnot
That’s fascinating. I’d never really considered how tactility is actually a key part of a product’s value. Can you tell us more about the benefits you and your designers have seen using NX CAD?
Joe Moak
There’s a lot. The first thing that comes to mind is the hybrid modeling that we’re able to do in NX, where we’re able to use the parametric history-based tools right alongside the direct modeling tools. I find that incredibly enabling, certainly in early phases of architecture, where we’re trying to understand the design space. It ends up speeding up the development, even though the CAD practices might make folks who are comfortable with parametric tools cringe a little bit because I’m removing parameters all the time and extruding edges and thickening and replacing faces, but it’s just incredibly fast. Another really unique feature of NX is the round-tripping that we can do between industrial design and engineering. The CV and whole structures of surfaces are maintained when I’m collaborating with folks using other surfacing tools. Alias, for example, Black Diamond, when we were designing a carabiner. The designer would send me their proposal and then I would run structural simulations on the form and I could actually push and pull that control vertices of the surface to get the stress to flow in a manner that achieved our strength goals and then the designer could go back in and using those same surface definitions, massage the surface so that it looked nice and not just performed well. And so a few cycles back and forth, again, using the exact same surface data, we were able to really quickly land a form that was both performant and aesthetic.
Greg Arnot
Do you find that NX helps with taming product complexity and achieving that overall design vision?
Joe Moak
It just comes back to that flexibility. Again in the early stages of architecture, I’ll often build models that have parametric relationships that are sort of engineering driven or kind of calculation driven and model driven among different parts in the assembly and it’s super easy to manage all of those interdependencies in one file. And then as the team grows, we need to kind of start dividing up the work and giving ownership of subsystems and parts to other engineers. It’s super simple to take that master file and parse out the individual components into their individual files and enable each of the engineers on the team to take ownership while sort of maintaining just enough of the interdependencies that we’re building robust models without being sort of overburdened with model maintenance.
Greg Arnot
Can you help our listeners understand how important it is for you to have flexibility in the architectural design phases?
Joe Moak
It’s absolutely critical. Having used NX for as long as I have and then being in situations, certainly with client work, where clients require us to use a different CAD package and deliver native files in a different CAD package. Man, the history-based modeling ends up being incredibly constraining certainly in the architectural phase. As I mentioned before, I’m almost thinking of product architectures in terms of datum surfaces and clearances, being able to grab surfaces and push them and pull them and move them around, and being able to replace faces until you see them is difficult to describe. They’re just incredibly powerful commands that enable us to move incredibly quickly. We also end up leveraging a ton of vendor CAD. You download a step file of a connector from Molex, and being able to grab the well-defined surfaces in those models and leverage them without building any additional parametric ends up being incredibly enabling. Another element of NX that I find incredibly flexible, and I’ve mentioned this before, is that notion of multi-body part files where you can build in all the parametric you want as you’re figuring out system interactions and then being able to quickly parse out those parts later. I’ve done similar in several other CAD packages and it’s always more onerous in those other CAD packages. It’s just way simpler and more robust in NX.
Greg Arnot
Well, we’re always delighted to hear when NX empowers our customers to do more. Are you leveraging the simulation and the 3D visualization tools within NX, and how do those help in the design process?
Joe Moak
For sure. We use them super early in the design process to kind of validate our designs. We’re really good at coming up with lots of ideas that may be good or may be bad, and understanding how a product might perform sort of structurally and thermally is really important. Later in the process, we’re using those same tools to optimize for strength and weight, and certainly the thermal performance and cost. Those two tend to often be at odds.
Greg Arnot
There’s been quite a bit of excitement about the announcement of collaboration between Sony and Siemens that we talked about earlier this season. Do you think you’ll be able to leverage the upcoming NX immersive designer software?
Joe Moak
Oh yeah, absolutely. It’s something that I’ve been dreaming of for a long time. We often talk about CAD goggles, that’s the situation where you’ve been staring at a CAD model for a long time, and then you send off a part to get machined or printed or otherwise prototyped, and you get the part back and it’s either enormous and you’re surprised at how massive it is or you get it back and it’s super tiny. So just being able to hit the show me the real size button and have it there in front of you is, I think, a game changer. I’m super excited about this notion of collaborative design reviews and being able to share one model, one-to-one scale in the same space with other collaborators who may even be remote. So much of the work that we do now and sort of the processes that we use now really require real humans to be in the same physical space as the real parts to really understand how things are working and how they’re not working.
Greg Arnot
In addition to NX for CAD, what other Siemens software products are you using in your design process?
Joe Moak
In addition to the tools built into NX, we also use Simcenter 3D. Find the solvers there a little bit more robust, get a little bit more control over the boundary conditions and kind of fine-tune the outputs.
Greg Arnot
Joe, before I let you go, I’d like to look into the future a bit and talk about some of the trending topics in your area of expertise. How do you see industrial and product design evolving and what do you anticipate there?
Joe Moak
Certainly, the tools and the processes seem to lag other industries a little bit, but I’m expecting to see the tools evolve to, I don’t know, maybe some better interoperability. NX is great for interoperability, but I know some of my friends using other packages have had some struggles. There’s something about the cloud in there. We’re seeing some CAD tools now that are storing the CAD data offsite in the cloud, and the client is sort of a thin client on the machine. It’ll be interesting to see how those tools fare on a long timeline. Those are big ideas around tools that I think I expect. I’m a bit of a Luddite, and I tend to use the tools that are working right now. That’s what’s coming to mind in terms of tools. Well, I know we’re already seeing some acceleration in manufacturing. For example, 3D printed sintered metal parts. The cost is coming down. We used to use those processes to make tooling in some of the medical devices that we built. Now the prices are coming down enough that you can almost put those parts into products depending on your overall volumes. So I’m really excited about new manufacturing technologies.
Greg Arnot
One trend that’s really close to my heart is sustainability. I imagine this is an interesting one for you. Are you able to design with sustainability in mind?
Joe Moak
I worked on the first Mac Mini at Apple that made it to the EP gold status. Actually put quite a bit of effort into not just material selection, I mean, obviously, material selection is important. The material suppliers make better and better resins that represent sort of a closed loop, like post-consumer recycled products that are performing better sort of engineered resins compared to how they performed in the past. It’s pretty common for a while for any recycled material or material with significant amounts of post-consumer recycled content to have significant degradation in mechanical properties and cosmetic properties, but it’s not necessarily the case anymore. We’re also thinking about the life of the product after it leaves the customer’s hands and what we can do by design to enable the reuse of those materials in the future. So, thinking about how a service depot is going to easily separate the metal parts and the plastic parts so that those two materials can go into those recycling streams is really important. Those are kind of the two big things. It’s enabling recycling and leveraging eco-friendly materials to the extent we can.
Greg Arnot
It’s great to hear about those capabilities. Now then, maybe the most prominent trending topic right now is AI. We explored it in a previous episode of the Next Generation Design podcast, but I wonder how you put it to use in your work at Maestro?
Joe Moak
I’m definitely not a power user of AI. I found it most useful recently sort of as a research tool. I’m hitting AI first using the large language models to do research and then kind of validating the research with Google. That tends to be the workflow now. It’s pretty interesting, I found that previously my research had been mostly thinking about the questions that I had, thinking about the domain I was trying to understand, and boiling it down to single-line questions that I could punch into Google. I feel like the AI tools make it sort of more conversational and I can, there’s just a higher bandwidth of information transfer. It tends to make the research go more quickly.
Greg Arnot
Well, using AI to accelerate your research is a perfectly valid use case. If I can ask you to make a prediction, what do you see as the future or the next generation of design? What does that look like to you?
Joe Moak
My observation has been that the manufacturing world and the design world are connecting in new and different ways. When I started my career, it was a bit of a challenge to sort of get engagement from manufacturing as a design engineer. I have to often get in my car and drive to a shop to talk to a machinist, drive to a factory and talk to a tool maker, or get on an airplane. And because manufacturing is sort of scaling and proliferating and becoming a little bit more democratized and the tools of design are also proliferating and becoming a little bit more democratized, my observation has been that the folks designing the parts – professionals and amateurs – are able to engage more effectively, more easily with folks making the parts. And I really like this theme. It seems like the merging of design and manufacturing with engineering there in the middle, kind of reconciling the goals of each. I just expect that whole process to become a little bit more effective over time.
Greg Arnot
Joe, one last question before we say goodbye. I know you’ve worn a lot of hats in your career, so I wonder, is there any advice you would give to someone starting out in their engineering career and any entrepreneurial advice for up-and-coming startup funders?
Joe Moak
Speaking from the perspective of a product design engineer, I don’t know if this is true of engineers designing rocket engines, I’m sure there are some similarities, but so much of the work that I do and so much of… I don’t know, think about the CAD that I own, and the designs that I end up owning, many of the details are driven by the needs of my cross-functional team members. Certainly, these highly integrated electronics products that have lots of features have many stakeholders and it’s really important that we’re providing mechanical designs that enable each of those technologies to operate well. And I’m often not the expert on all of those things. As a matter of fact, I’m not an expert on any of those technologies, certainly, you’re thinking about RF and circuit boards and displays and microphones and buttons. I know how to integrate all of those technologies, but I end up having these really deep relationships with each of these cross-functional team members. So the advice is just to get comfortable having technical conversations with designers and engineers and marketers and leaders from different domains and spend the time to understand the language. Often we use different words to express the same ideas. Sometimes ideas in their domain don’t actually exist in our domain, so it takes some time to understand those ideas. If nothing else, that’s super important. Entrepreneurial advice, that’s a tough one. I’m kind of a shoot first, ask questions later, take action first, ask questions later kind of a guy. I guess my entrepreneurial advice is to make sure that you get paid before you pay. Certainly, starting out manage your cash flow. Put a lot of effort into knowing where your money’s coming from and where it’s going.
Greg Arnot
That’s great advice. Thanks so much for that and thank you for your time today. It’s been a real pleasure learning more about Maestro Product Design and the work that you and the company do.
Thanks again to Joe, we look forward to having you back again soon. Thanks also to our listeners for tuning into today’s episode. Join us again next time for more discussions about the latest in design innovation and software applications. If you haven’t already, please consider subscribing to our podcast on your favorite platform and if you’re enjoying the content, please leave us a review. I’m your host, Greg Arnot, and this has been the Next Generation Design Podcast.
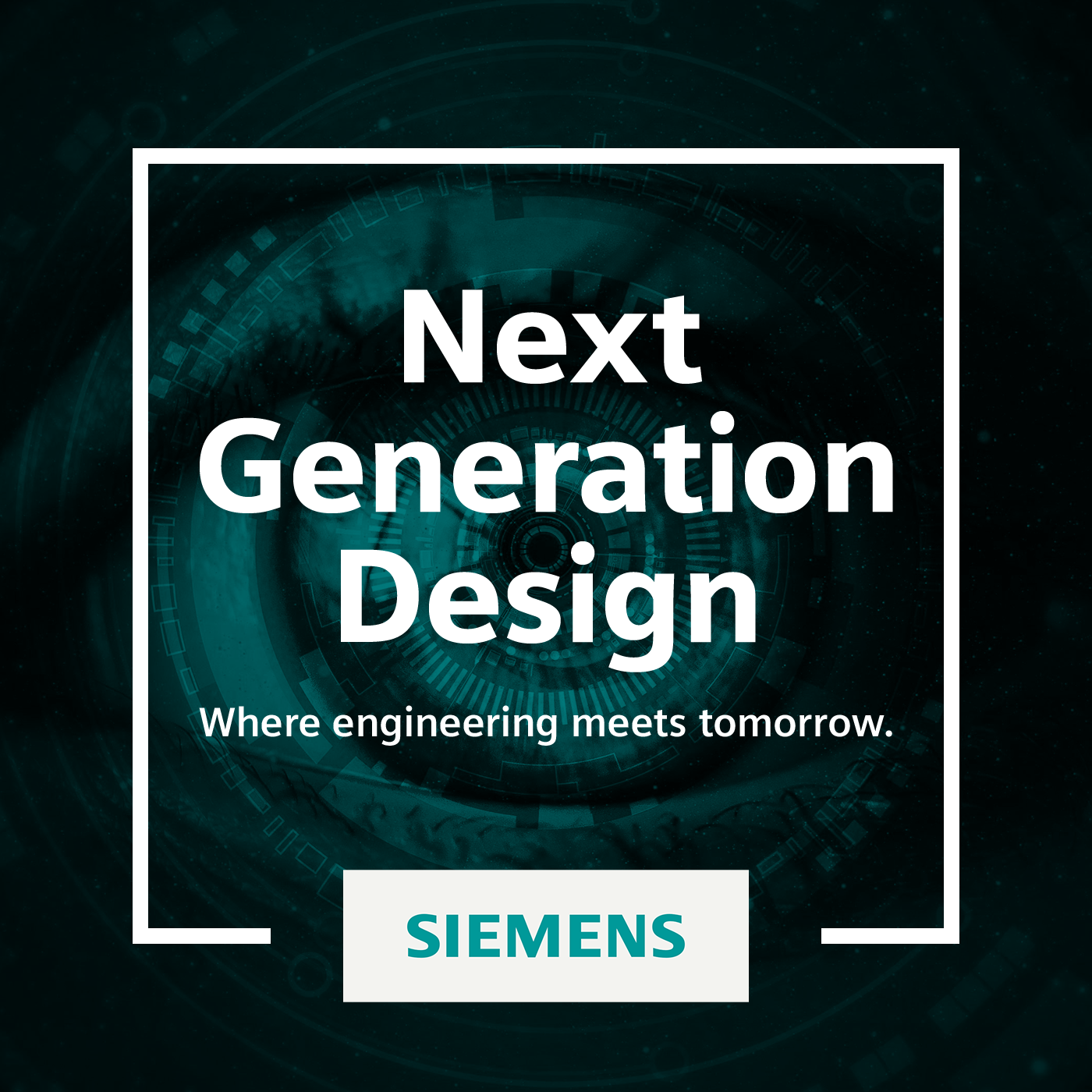
As product engineering tools continue to morph and expand at speeds human expertise may not be able to endure, Revolutionary design technologies that span beyond industry borders, will prove their necessity for companies looking to take over their markets in the future. What will the future of design technologies and machinery look like? What will your digitalization story be? Where engineering meets tomorrow.