Advancing corrosion analysis in aerospace

Guest Alan Rose of Corrdesa LLC
Listen on Apple
Listen on Spotify
Show Notes
In this episode, we look at the critical role of corrosion analysis in industry innovation with Alan Rose, CEO of Corrdesa LLC. Explore the complexities of simulating corrosion processes and how these techniques are paving the way for safer and more efficient engineering practices across sectors. Alan Rose brings his extensive expertise to discuss advancements in corrosion simulation, its economic impact, and the future of materials testing.
Key Takeaways:
- The evolution of corrosion analysis from physical tests to advanced simulations and its significance in reducing operational costs.
- Insights into the collaboration between Corrdesa LLC and Siemens, with a focus on integrating simulation technologies for enhanced corrosion management.
- The importance of accurate data in driving the effectiveness of corrosion simulations and the development of new materials.
This episode of the Engineer Innovation podcast is brought to you by Siemens Digital Industries Software — bringing electronics, engineering and manufacturing together to build a better digital future.
If you enjoyed this episode, please leave a 5-star review to help get the word out about the show and subscribe on Apple or Spotify so you never miss an episode.
Watch on YouTube
Guest biographies and episode transcript
- Explanation of modern corrosion analysis methods versus traditional. (03:01)
- The importance of accurate data in effective corrosion simulations. (04:06)
- The role of material and environmental selection in corrosion testing. (06:40)
- The economic impact and cost benefits of managing corrosion. (15:32)
- Integration of corrosion analysis early in design to identify potential issues. (27:55)
- Future developments in Corrdesa’s corrosion analysis tools. (32:30)
Alan Rose 0:00
I expect over time was industries see the benefit in terms of return, being able to speed up your time to market avoiding safety and warranty issues, anything that could provide information early in the design? I think in automotive and other industries, these analysis techniques would be required.
Stephen Ferguson 0:22
Hi Chad, who’s your guest in this episode in the engineer innovation podcast,
Chad Ghalamzan 0:26
Alan rose from credenza. And what DeCordova do is a specializes in corrosion analysis and corrosion testing.
Stephen Ferguson 0:33
So I’ve been working in simulation for a long time. And apart from Alan, I’ve never talked to anybody else who does corrosion simulation. So is it widely practiced in industry? Would you say?
Chad Ghalamzan 0:42
No, but he’s trying to be an advocate to change that it’s not as widely practiced as let’s say CFD or other tools. He said in this conversation that he thinks we’re corrosion analysis is is kind of like we’re CFD was 3040 years ago, it’s on the cusp of becoming more widespread ly used, but it’s still not as mainstream as other types of analysis.
Stephen Ferguson 1:01
And I guess the consequences of not taking account for it are what? Well, unlike
Chad Ghalamzan 1:05
other factors, this will happen. If you don’t predict in advance there will be corrosion. The question is, how do you mitigate that? How do you mitigate the risks? How do you introduce new materials or test what you’re doing in advance so that way, you know, when maintenance or services required, or what combination materials to avoid, that won’t cause corrosion occur more quickly. So basically, it’s all about understanding what will occur because there’s very limited ways to prevent it completely. But even then, if you can mitigate the risks, or extend the lifespan of your aircraft, your marine vehicle, whatever, it’s gonna go a long way to improving the performance and reducing costs.
Stephen Ferguson 1:40
And it’s one of those things that occurs over such a long timescale as well, that having a simulation approach to tackling corrosion must be really advantageous. So thank you very much. For that. Let’s have a listen to this week’s episode of the engineer innovation podcast.
Chad Ghalamzan 1:52
Hello, and welcome to this episode of The engineer innovation Podcast. I’m Chad glanza. Today, I’m joined by Alan rose from Core Data. Hi, Alan, how are you?
Alan Rose 2:04
I’m fine. How you doing?
Chad Ghalamzan 2:05
I’m good. Thanks. For our listeners. Why don’t you explain who you are and what Cordova does? Yeah,
Speaker 1 2:12
sure. So we’re a small company based not far outside of Atlanta, Georgia. And we’ve developed techniques for simulating electrochemical processes. So that could mean electroplating, electrochemical machining. And on the flip side, corrosion are all electric chemical processes. So we’ve been developing corrosion simulation software, and associated data. And through that, we’ve ended up teaming with Siemens on a couple of projects and product developments. Yeah,
Chad Ghalamzan 2:40
that’s what we’re going to talk about today, the work you do and the work you do with us. So we can start with something very basic. What is exactly corrosion analysis? Because I think for most of us, corrosion is something more tasks or something you need to do in the field. Or maybe that’s the old guard thinking, but how do we simulate or what is corrosion analysis and a digital transformation type of story? Okay,
Alan Rose 3:01
well, closing analysis, while traditionally was probably like looking at tests, what is corrosion people often think of rust as just corrosion of one material. Corrosion is more of a deterioration in materials related to a specific environment. There’s the amp, PP sociation of these metal performance of protection, they define corrosion as Technosoft or even more mechanisms. So you have galvanic corrosion, stress, corrosion cracking, corrosion fatigue, there’s many forms of corrosion. And people have tested it in biophysical tests. That’s destructive testing. And it’s after the effect, the best test is put it on an airplane and fly it for three years and see what happens. But you can’t wait three years for results in terms of designing deploying new materials. We’ve been developing data techniques and workflows that enables you to simulate some of these corrosion mechanisms in minutes. So you can turn around design decisions within days rather than how to wait for months. physical tests accelerated chamber tests, take two three months, the beach test could take several ones. So corrosion analysis allows you to gather data quickly, in a robust and consistent way in the lab, implement it into your 3d solver, and then output a 3d color map of corrosion risk, where it is, how bad is going to be and so on.
Chad Ghalamzan 4:24
So you mentioned a few different types of corrosion is are you talking about all those types here when you’re talking about corrosion analysis, while
Alan Rose 4:31
it’s just like the proverbial elephant really is a piece at a time, there’s all these different mechanisms and a lot and so much more complex than others? What kicked us off at Core Data was maybe about 10 years ago, we got an award from the US Navy and they were interested in galvanic corrosion. Now, there was some models that would enable that and they wanted to look at a feasibility of computational simulation of galvanic corrosion. That was interesting to them because on the fleet at percent of the fatigue problems, were precursor by galvanic corrosion events. So obviously
Chad Ghalamzan 5:04
80% 80 Yeah, it seems like a very large amount.
Alan Rose 5:10
While we did that with tear downs as our players put it on to part and doing forensic analysis, but
Chad Ghalamzan 5:15
that but they weren’t all necessarily Castro’s catastrophic. First, it was just deterioration that maybe they didn’t destroy the ship worthiness, for example,
Alan Rose 5:22
no, they’re not catastrophic, but certainly increase the need for more frequent inspection, longer time in the depot that expected for repair because things happen sooner than expected. And to mitigate that, as you have corrosion from dissimilar materials in a hole, for instance, you would read that hole, insert a new bushing, to bring that back to damage tolerance, and there are like hundreds and hundreds of these styles. So it can become quite tedious problem, even if you have a solution for implementing it can take a
Chad Ghalamzan 5:53
while. So it’s more maintenance. And it’s increasing cost, it’s not really an issue that if you can mitigate, you’re reducing maintenance time you’re reducing costs, there’s quite
Alan Rose 6:02
a few, there’s quite a few impacts. I mean, the biggest one now is was readiness, because your plane isn’t available, if 20% of your planes are down or it won’t quieter at 80, it was almost 70 or 80% non availability. So we are all add a fifth of the fleet available, that has come down considerably for a number of reasons. But maintenance was certainly Walder, you know, readiness is very important from a defense perspective, as well as obviously safety, you know, onto an expected failures.
Chad Ghalamzan 6:30
But to get back to what you said at the beginning, you could do an accelerated chamber test, you could do beach tests, you can do some physical testing, but these issues still happen. How come
Alan Rose 6:40
is a good question because you got to figure everything has its limitations, even simulation to what we’re talking about the tests, okay, they’re not real, you have to make some surrogate kinds of specimen, you have to have your coat in an environment is critical your what the environment is. So you got to try and get an environment that’s close to what you would have in the sealed. But in the field, we know, corrosion can take place over many years, they have to accelerate the tests. And now you’re tweaking and playing around with Mother Nature. So you might change the chemistry to try and accelerate the test while really testing a different chemistry. So tests have their limitations. So physical tests, and I always think of simulations as virtual tests. In a simulation, you have a much tighter knowledge of what goes in the simulation, you define exactly what goes in a simulation. In a test, if it’s running for one or two months out, you know, you didn’t have a power failure partway through it. And maybe there’s some monitoring, we can’t control that in the simulation test, you have the boundary conditions. And
Chad Ghalamzan 7:39
I’m guessing when you have a two month test time, you’re not going to retest and retest every two months with different materials, different things like your ability to re initiate a new experiment is much more limited versus a virtual setting where it’s probably infinitesimally a fraction of that time to do the simulation and compare the results. And then you can check different types of results or different scenarios easier.
Alan Rose 8:03
Yeah, it’s a good point, because I think there’s obviously a place for simulation, virtual tests and physical tests, and they can work in a complementary way. Okay. If you’re testing a coating, and you have the there was no plan platform designed 20 years ago, and now they’re looking at new coatings. So many other things have come on the market since then, if you’re testing, like, oh, I have five suppliers. And you have to I look at all the different conditions, you soon up to there literally 1000s of specimens required. So that’s a lot. So with simulation, you can gather some of that coat and material data within a day or two in the lab, implement that data in your simulation, and first, do some simulations. And that way, you can just choose your champions, as it were, and go have tests then because still physical tests are required the part of some standards, so you can reduce that massively. And rather than two, three months or so down the road, find you’ve got yourself some duds. And you have to start again. You have to get there first time.
Chad Ghalamzan 9:01
Yeah, well, that would make a huge impact in terms of the timing and costs. And like you said, there’s only so much you can test there with that many permutations to explore.
Alan Rose 9:10
You’re always limited by budget, because we’ve done a lot of work in aerospace and defense. And now we’re getting a lot of traction in the automotive side. And it’s completely different timescales for aerospace and defense to implement a new coating can take more than 10 years, 10 to 20 years. And that’s assuming you already have a coating, ready to try and test you know, the chemistry and everything’s already been invented. On the automotive side, they have to turn around new designs and get them on the market in two years. So out of your 24 months, they’re like 12 1314 months down the road before they’ve even established what the materials are going to be. Well, that doesn’t leave you very much time for physical testing. So if you can do more testing, you can get the data I should say in the lab and do some simulations up front at the same time as people doing their stress. crusherimpact Thermal Analysis fatigue, it’s just another engineers tool that should be run in parallel with all these others rather than by bolted on at the end. Yeah, it’s not just another technique. People either heard of CFD 40 years ago, and then you wouldn’t dream of designing some systems without use some of these CFD tools, for example? No,
Chad Ghalamzan 10:20
absolutely. I mean, it would be, I’d be curious to know who would even attempt to do so at this stage of the game. So corrosion analysis, not as widely known as CFD, as you just pointed out, maybe we can get a little bit more into the nitty gritty without obviously revealing any of your trade secrets. But what how exactly are you doing this corrosion analysis?
Alan Rose 10:41
Okay, well, like I said, there’s a several mechanisms, we certainly made a lot of progress on galvanic corrosion analysis, which is important, maybe more important aerospace compared to automotive. That said, the automotive are following the trailblazers of aerospace and defense, and they’re having to use lighter and lighter materials, these magnesium and lithium alloys and this very active need, a lot of protection was enabled, the simulation for us is the data. When I started using CFD, I didn’t have to go and find my own specific heat capacity, thermal conductivity, it was already that somebody had already supplied it. And it’s available in the database. So we had to decide with the Navy, what data is required? And then how do you actually go measure that in a robust and consistent way? Okay, so we took a step back, yeah, we can model galvanic corrosion, but data is king, if we got the right data. So it took a couple more years, we formed a consortium of industry, academia and defense on the Navy. And we did round robin tests, we got Sam back samples provided into several people and say, Look, this is the protocol that we’ve notified, go do it, and come back. And all that data was tested, that was still scattered, but it was very well, it wasn’t enough whether it was small enough to see that it was a viable method. And that protocol for gathering data is no part of a military standard, which was released a couple of years ago. So the first thing is data, you have that data. And that’s where Core Data has strength, you know, we have a third of our facilities is given over to laboratory and, you know, as people that gather that data to power and fuel the simulations,
Chad Ghalamzan 12:26
so you continue to build this data. Yeah,
Alan Rose 12:29
exactly. So we’ve got quite an extensive database relevant to the aerospace. Over a year ago, we got involved in a sponsored program from an automotive consortium of several companies that were interested in getting data on this specific outline. So we don’t use that, or that’s too expensive. We use this so we have to go get samples. And we’re halfway through that program. So our database is literally doubling in size this year. I guess that makes
Chad Ghalamzan 12:56
sense that you’d have to use the materials specific to different applications for automotive or aerospace. But also, I guess the conditions under which these materials are being subjected would play a role, I would assume. I mean, we’ve talked about aircraft, we’ve talked about Navy, Marine, and and now automotive, these aren’t the same environments at all.
Alan Rose 13:12
Yeah, yeah, they do. Right, you have to choose an environment. But in reality, the environment changes all the time, if you can imagine. Yeah, has weather effects, diurnal effects from night today, a water salty water condenses. And it dries, there are a lot of complexities, but you have to start somewhere. So the standard calls for artificial seawater emits a certain temperature and those you’ve run the alleged chemical measuring equipment in a certain way. In order to get in order to get that data out. Oil and gas, I’ve been approached by oil and gas, they’re interested in electrolyser have dissolved silver dioxide. We have embarked on anything like that. But there’s a way of going doing that we can do that with Edison research institutes that have equipment that can do high pressure, high temperature measurements. So that could be interesting. It’s an engineering solution. Okay, my background is computational fluid dynamics. And in the old days, we didn’t have a computer that could resolve the boundary layer, okay. So we have a model to stretch from the wall to the to the flow. And the way I see this, the corrosion, and the electrochemical reactions that take place close to the wall are very complex, okay. And you could try and model them. But you’ve been modeling on such a small scale, it’s not a sound engineering approach. So what we do by gathering the data to the relevant environment and the relevant materials, all the different materials have to be chosen. You capture that and you can bridge that detail that certainly with the reactions, and then you can employ the electrochemical reaction models that were already in Star CCM, which is what we did star CCM plus. So it’s quite straightforward really, once you have the data that matters really too complex?
Chad Ghalamzan 15:03
Well, it sounds like you’ve nailed the analysis part down, for lack of a better word. So we have this simulation capability, we have this tool set that could a surprise credit supplies to allow companies to start investigating the effects of corrosion. So that’s the physics. That’s the engineering aspect of it. Maybe we could talk a little bit more about the costs and what this impacts in terms of now when we’re looking at the damage, corrosion does, what’s the economics of corrosion? Say sewage
Alan Rose 15:33
is is an understatement. It’s been a number of studies done many of the cited and have been refreshed and renewed. A typical number is it considered a global domestic product is about three, three and a half percent. So that would be as you got $105 trillion, it could be created in a quarter trillion dollars of corrosion damage. So it’s a huge industry, there’s a lot of return of investment on good coatings and good techniques and mitigate control corrosion, if none of that. And if you drill it down, where we started in aerospace and defense, there’s been data and numerous reports across the branches of DOD, and corrosion can costs about $20 billion a year in DOD, and half of that is for aerospace and defense, it’s $10 billion a year, 5 billion for the Air Force. So it’s huge. Of course, there’s always a safety as well. You don’t want things to be failing prematurely. You want to be sure doing a what if analysis to try and avoid these potential problems. In the past, we’ve seen parts of airplanes just unzip, essentially, because of fastener for galvanic corrosion, round fasteners and fatigue around fasteners. Yeah, we need to avoid that. A single problem for the F 22, which is our most modern fighter costs $228 million, just one problem. And that was just a choice of what’s called a filler material between some panels. It’s used some stuff, you switch between panels, and that cost $228 million to put it right. Twitter, Twitter. So
Chad Ghalamzan 17:03
one, one material choice one material choice. Yeah. And I think you explained to me once that it’s also sometimes the interface between the materials that people neglect to take into account. So the filler itself might have been okay. But the the interface in that specific instance was problematic. Yeah,
Alan Rose 17:19
yeah, absolutely. Right is in isolation. You can there’s a what’s called general or uniform corrosion, or you put a single material, leave it out on the beach, or on your car or whatever, over time, it will corrode. But with galvanic corrosion, it can be quite insidious, actually, because you can have a corrosion rate and material a not so bad and causing them to be not so bad, put them together. And it can be 10, or more than 100 times more highly concentrated at the interface, right where you’re joining, which is where you don’t want it to be. That’s why it’s called people out. It’s like, oh, this is good, this is good, this is good. And you put them together, you can look at one or two materials. And there are traditional tables to look at to get a feeling of corrosion risk. But the standard now that uses mixed potential theory, which is what our simulation uses, requires more fidelity in the input data. And if this new military standard was in place than they would have been another that because it would have been spotted. That’s
Chad Ghalamzan 18:22
a huge cost to have because of one material choice. And we’re really talking about reliability, availability, maintenance, and safety when it comes right down to it. This is an effect we’re trying to mitigate. Sometimes when we look at engineering, we’re looking to improve performance. We’re trying to get the most out of something. This is one of those instances where we’re trying to actually either mitigate ensure it doesn’t happen or the rate is not more than expected. So are there other regulations coming into play now to force certain, I mean, militaries one for sure, but it’s either places where we’re seeing regulations or talk of regulations coming into look at this more systematically as an analysis.
Alan Rose 18:58
Like I say, on the military side, certainly. And high up, there is a requirement to find and locate potential corrosion areas on your system. So for weapon systems, aerospace weapon systems, that’s the case. And then other standards come into play to look at different kinds of mechanisms. Several years ago, I approached the automotive companies with a technique for simulating light electroplating, which is a flip side really, you’re when you’re electroplating cells in in a bath, your anodes are corroding essentially. But we’re looking at the electroplating part on the cathode on your grill, or landing gear or whatever. Now, when I first approached folks with that there was a lot of skepticism, but even now, electroplating simulation is being used and is an engineering directive in some of the automotive companies in a requirement. So I expect over time was industries see the benefit in terms of return, being able to speed up your time to market avoiding kind of safety and warranty issues, anything that could provide information early in the design. I think in automotive and other industries, these kinds of analysis techniques will be required. So
Chad Ghalamzan 20:09
what do you think are the barriers to the adoption of such an analysis right now,
Alan Rose 20:14
education, so people just simply don’t know that you can do this, you know, more progress has been made. So Ellison’s I was at university. So unless you’re in it, you don’t really know it. So that’s one of my challenges is education. Hopefully, discussions like this will.
Chad Ghalamzan 20:28
So people don’t know this exists. They don’t know. They’re relying on just the accelerated tests that you mentioned.
Alan Rose 20:34
So the way they are relevant, I think it’s human nature as well, isn’t it to believe in tests,
Chad Ghalamzan 20:40
we still correlate, right? Even when we simulate, it’s not like we completely get away from testing. It’s just we maybe try to reduce it. Yeah.
Alan Rose 20:47
But it’s still a simulated environment isn’t a test, I think, but the career that I lead a foot in test, physical simulation, and virtual simulation, some folks that have just gone along the physical simulation, will think that oh, this is the data this is true. But even measuring, after tests can be subjective, and the tools and techniques for quantifying the amount of corrosion. So there’s education, there’s the way people have already done it before. It’s not knowing that this exists, the way it’s been done before. And it’s new. Everybody resists change. So unfortunately, I’m persistent. So just keep kicking down doors and listen,
Chad Ghalamzan 21:27
yeah, well, I think it’s there’s some industries have been more conservative than others in terms of adopting new tools or such, because of the nature of the industry. Aerospace, I think is a good example. Because of the way that industry functions. They’re not as maybe as quick as others. But it sounds like militarily. That’s because the military, sorry, they push that more, but there’s other companies or other industries that you think it’s just the lack of knowledge. Is there any other maybe barriers, even if they understood that this was available? Are there other barriers? Is there a lack of confidence in the analysis? Is there maybe too many assumptions that go into the analysis? Or once people are aware? What’s their hesitation at that level?
Alan Rose 22:02
Well, yeah, I mean, we have a lot of validation verification data are so there is data there. And we’ve published quite a bit of that. But still, just because you publish, it doesn’t mean that people see it. I have literally been in presentations, were talking company to company, and they see some of these results. And there was one just before Christmas. And there was an aerospace company that started looking at this, and they couldn’t believe what higher firewood got with that, okay.
Chad Ghalamzan 22:29
They couldn’t believe because it IVIG it was valid, it couldn’t believe as they were impressed.
Alan Rose 22:33
Oh, they were pressed because it was more accurate. At the end of the day, what are your simulations for? Okay, I don’t think you have to be able to out eventually you could but predict to several decimal points, you do a simulation to help an inform a decision. That’s the way it is why we do it. Otherwise, what would be the value and you may want to decide to take one path or another, it’s definitely comparatively your simulations have got to fall in line and rank in the same way that your tests work. And we certainly do that. We’ve shown that over and over again. But we’ve gone further down the road in terms of quantifying it more accurately on the physical tests, for example, you can put some specimens in one part of the corrosion chamber. And in another part of the corrosion chamber on one sec can pass on one second tail, it’s the still to stochastic issues with physically doing the tests if you have the material available. I think over time, people will adopt simulation working in hand with testing, held rationalize our program, I think that’s the way I failed with CFD that really got a start when it pulls some people out of a deep quagmire, like the king’s Crossfire and London years and years ago in the underground that really brought CSD forward in terms of a viable tool for fire modeling and stuff. And now that we’ve fixed a few bad problems, were beginning to get people’s ear and attention. Yeah, it will become part of the design tools like everything else. And the thing is, it uses some tools that people already have, folks is the adult read through the star CCM plus manual, which is like 14,000 pages long, you wouldn’t know that deep in, there are electrochemical modeling techniques, I think there might have been done to some battery at work. And in the days it were even there. So we saw that those were available, we figured out how to compose the model. And we figured out what data was required. We didn’t have to reinvent CAD, that 3d handling the solver, we just leverage that with our data and no error and move forward. So now when we talk to people that are already using star CCM plus, we can very quickly get them up to speed and we’re doing that with a number of companies now. So it’s incremental to what people already have to hand with the rest of the tool chest.
Chad Ghalamzan 24:53
So that’s how we’re partnering together Siemens and Codesa and I believe There’s also you’ve mentioned some centers star CCM plus, as one way we’ve our partnership is in effect. What about at x corrosion analysis? Can you tell us a little bit about this new module?
Alan Rose 25:12
Oh, yeah, to put it in perspective, out of our Navy program, we created our software corrosion, Jen. Okay. So corrosion Jn is CAD agnostic, it will tell you given some materials, what that corrosion rate would be at the interface. So we come to compare it to your wall material to corrosion at the interface. And we can do that several times, or metallic and alloy pairs. So I’m talking to Tony Solana what to call friends. He’s a product developer within NX. And he was very proud of the NX coatings that he produced his CAD system module. And what the Penix coatings does is really unique. You can specify your coat in stackup. Just as you have electronic and hydraulic systems or coating is a system there’s primer and topcoat and other surface finishing that will have done it’s a system. But the thing is that information is often added on as notes or on some table to be unkind, sticky labels. And it gets disconnected with the rest of that model for your product. So but with coatings, you can capture all those your coating thicknesses, coating material, and so on. Because it’s surface data, or use not just solid material data that you need. With coatings, you also need surface data. And once I realized that’s what he was gathering, I said, Well, look, I said this data if you’ve already got it, and we have a database, so that you can apply the right information. And we can read that and doing analysis. So essentially, the new version of NX the cancer Stan came out December last year, it’s like running gene on steroids, you can get a full 3d system of your product, press a button, and the people at Siemens created the algorithm to search that database. It finds each and every interface not but wash your butt joints and giant black giant whatever. Each of those interfaces integrators while the coatings are either side, it reaches into the crow’s engine database and figures out what the corrosion rate is. So literally in seconds, I mean, you run it live, I press a button, you see all these interfaces, and then it’s color coded. So it lights up like a Christmas tree and things are really bad. So you get these red, amber green areas for all these interfaces. And then you can interrogate any of that. And the good thing whilst the designer is in the CAD system, you don’t have to have a deep knowledge of materials and processes, you can make some trade choices, you maybe you made a mistake, maybe you applied the wrong kind of coating or the wrong kind of titanium. So it was spots, areas admissions very quickly, they’ll just light up just
Chad Ghalamzan 27:50
going to make it easier for cause analysis to be taken into account earlier in the process. Absolutely,
Alan Rose 27:55
I see this as a risk analysis, it tells you as one standard, I said find your corrosion pro locations. If it’s a new design, you’re not going to know where they are because you can’t extrapolate. You can use experience too. But there’s like I said, with galvanic corrosion, it can be quite insidious. So yeah, it’ll light it up, you can make some changes there and then and eradicate some issues. But if it needs more of an engineering attention, maybe a redesign of that fixture system, you can then just take that piece out, feed it into CCM plus, and then do your deep dive 3d model. That’s how they work. I see the NX was corrosion risk, invest, investigate these areas, and you can apply your budget and your title and people correctly to the issues that really matter in the deep dive. So there’s a new release of it coming up in June, we’ve got a lot of ideas to enhance that capability. There’s nothing like it. June
Chad Ghalamzan 28:48
2024, just pre release at the timestamp these things. So you mentioned experience, you obviously have a lot of experience in this area. This is something you’ve dedicated, but you founded the company in this area has using these tools ever yielded results that was counterintuitive to your experience about a specific application or materials. Because obviously you develop a gut feeling for things over time instinctively whether it’s right or wrong has, Have you even been surprised by what the analysis will show. Because as you mentioned, it’s an insidious problem. And the results can come from different factors. A
Alan Rose 29:25
table is very static. And there are assumptions if you compare one material with another that those materials are equal in an area ratio between adults and council is one to one. But if you have that data in a 3d solver, you can implicitly take care of that area because the geometry is known. And that can change things around what you might consider bad isn’t so bad because the way that ratios work in your cat or you might just simply have to make things smaller or bigger. Sometimes that’s a workaround. I think one thing that really took a lot of people the bicep eyes. But there was a lot of nodding heads in the rooms when they did these presentations because it came out with that field experience. And that was when I talked earlier on about materials for bushings and fasteners, okay. In the past fasteners in aluminum alloys, they’ve chosen stainless steel, if I know that stainless steel doesn’t rose, but like I said before, on his own is good, but in conjunction with other materials can be bad. And an alternative to the stainless steel is titanium and titanium alloy. Now on the old system when they just looked at galvanic potentials, because like a football league is bad actors and good actors, titanium looked worse than stainless steel. But if you look at the kinetics, the new way of looking at it mathematically in the simulations, we can show now that titanium is a better option. So people in the past would say, Oh, I can’t use detainees, because the standard says that would be bad. And then folks will go well, we actually used it and it wasn’t so bad, but they couldn’t quite explain it. This has really helped explain that a lot of people now are accepting these kind of simulations, because now they can characterize similar materials and new allies and coatings, and we can show their effectiveness in simulation.
Chad Ghalamzan 31:16
Well, it goes back to what you said it’s to make a decision. And now that decision turned out to be valid. And you can now explain why it was valid. It’s that’s I guess what you’re alluding to here.
Alan Rose 31:28
True. Yeah. And another thing as well, some people I have thought that anodising and aluminum alloy, a treatment would resist corrosion issues. Now that resists a kind of a general uniform kind of corrosion issue. But it’s not very good as a protection against galvanic corrosion, we found that with our measurements, it it makes you think of things in a different way. So if you’ve got all these fasteners on a wing, it could be on the chassis of an automobile or this array of fasteners. Rather than change the structure material, there’s things that you can try to change the material of the fastener and the fasteners only about 25 cents, 50 cents, or whatever. So you can think of things differently. And this I get fast as coated with this, and it only cost me a few cents extra, that would just save my very expensive chassis. So you can look at things differently. And you have more time to do so because a very quick simulations.
Chad Ghalamzan 32:24
So what’s the next step in Codesys evolution and corrosion analysis.
Alan Rose 32:30
Okay, I like our collaborative result with the NX, that corrosion gene is completely integrated. And as a comes out as a Siemens NX product, and it’s very, very easy to use. At the moment, our 3d modeling is easy to implement. But the approach is a little bit fragmented. So the next evolution is to have a similar fully integrated product that allows people to do simulations, corrosion simulations, and CCM plus more fluidly. So we’re working on that. And towards the end of the year, we hope there’s some enhancements deep within CCL plus a will help the implementation and deployment of what we bring coordination in terms of the data. So essentially, inside a ccm plus similar to NX, you’ll be able to just change materials and call all the materials on the fly instead of preparing and reading them in a particular fragmented way. So that’s definitely one enhancement. A couple more announcements, start looking at some of these other corrosion. crevice corrosion is another big one, the big hitter for some people. And we have some ideas on that, that we’ve been developing. Maybe one of the biggest ones is many systems at the end of the day, are painted of the topcoated. That failure mechanism for degradation of the polymer top costs in organics. So the organic top codes there, we’ve been working on this a couple of years, where we sped up the degradation of these organics in the lab, characterize them. And now putting that data into our simulation. So it’s not just in organics and metallic can conductive coatings, we can also look at the impact of the top coats as well. So that’s they’ve been asked in the three more years down the road, but it’s very important. I think the CCM plus enhancements will come along first sounds
Chad Ghalamzan 34:21
like there’s still lots of work to be done. But what you’ve demonstrated or just spoke about today, in terms of what code analysis can offer sounds like a very important tool that if you’re listening and aren’t considering you should start considering now. Because I guess if you don’t do it upfront, you’ll pay the price tenfold later. Thank you so much, Alan. It was great talking to you. And I hope you come back on the podcast when you have more corrosion types covered with your solutions and we’ve dealt more with NX and star CCM plus with corrosion. Thanks. Thank you for listening to this set. Episode of the engineer innovation podcast. Make sure to leave a review if you’ve enjoyed it. And we look forward to speaking to you again next time. Bye.
Host 35:10
This episode of the engineer innovation podcast is powered by some Santa turned product complexity into a competitive advantage with some Sanza solutions that empower your engineering teams to push the boundaries, solve the toughest problems and bring innovations to market faster.
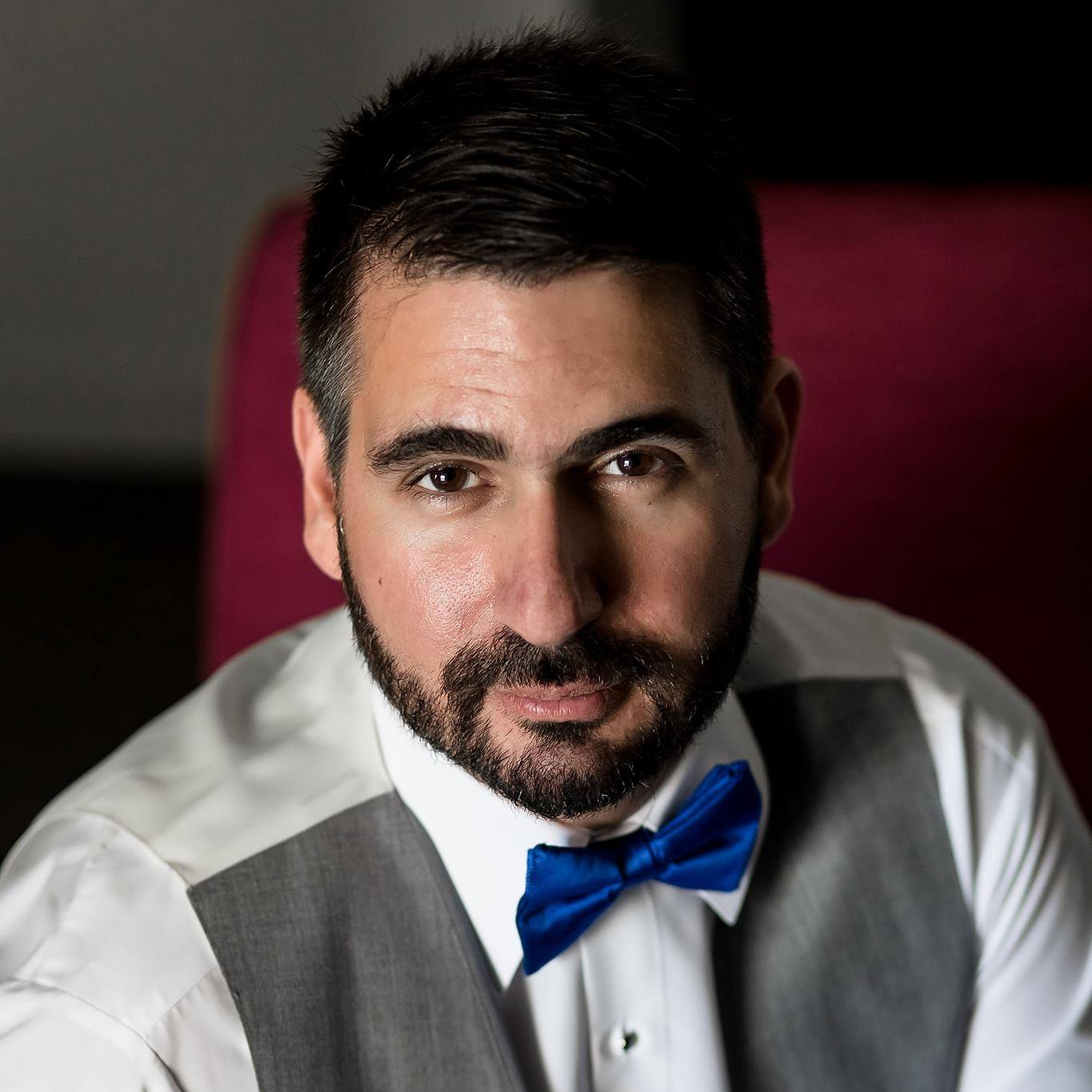
Chad Ghalamzan – Host
Chad Ghalamzan is a computer engineer with over two decades of experience in sales and marketing for the simulation and test industry. He co-hosts the Engineer Innovation podcast and creates content for Siemens Digital Industries Software. He’s tired of people calling him ChadGPT.
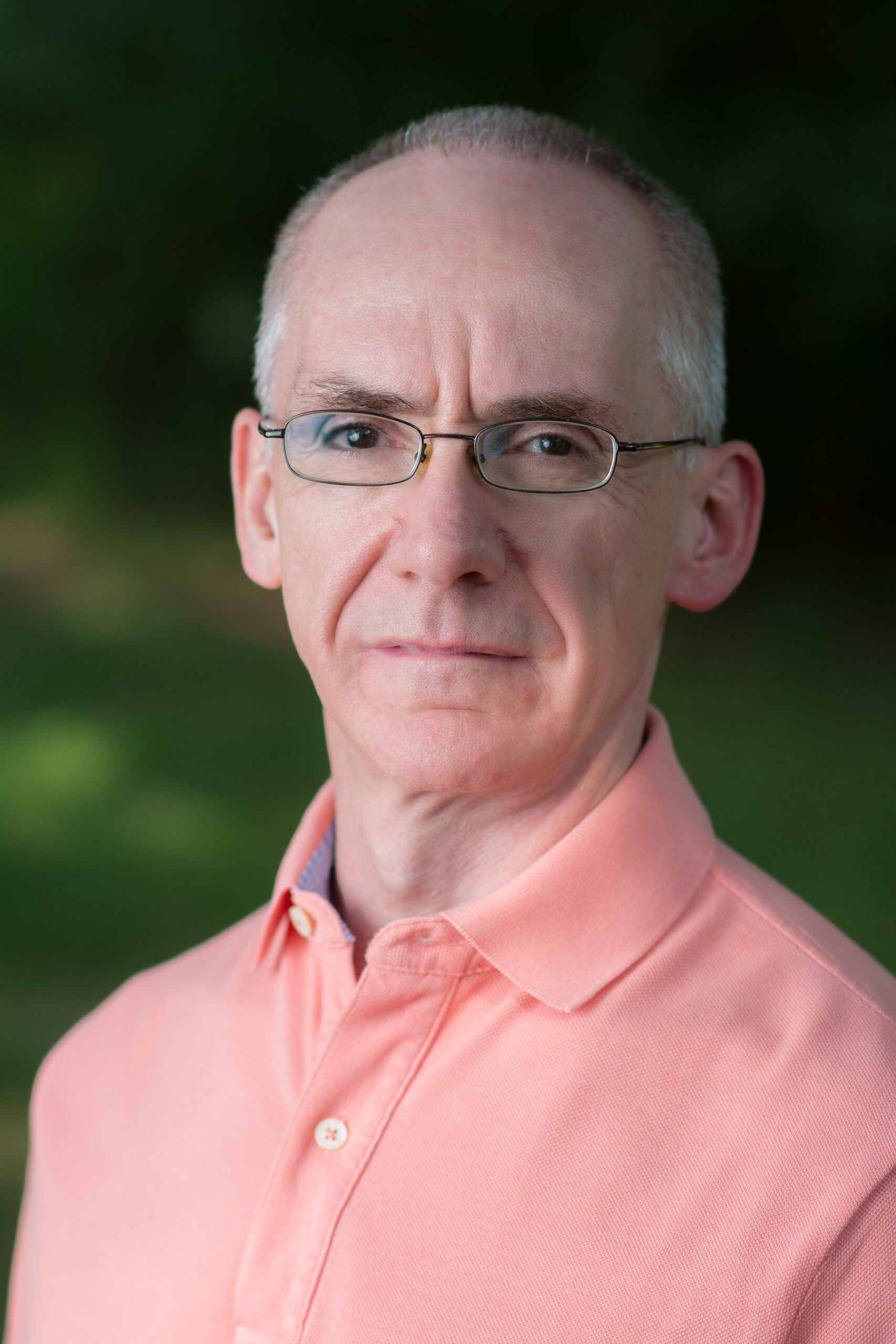
Alan Rose
As CEO of Corrdesa LLC, Alan Rose works with commercial and military customers, developing technology and software tools to enable Corrosion Resistant Design. He has spent 30 years transitioning computational engineering simulation tools into daily, engineering use. Starting his career applying CFD for process design and safety studies in the nuclear industry and then moving to the USA validating CFD on gas turbine combustor design. Over the last 15 years Alan has implemented electrochemical simulation into corrosion prediction and scale-up of electrochemical processes such as electrochemical machining, plating and anodizing. Alan’s BSc is from the University of Manchester, England, and his PhD from the University of Sheffield.
Take a listen to a previous episode of the Engineer Innovation Podcast:Engineer Innovation: 100,000 Simulations a Day! AI Powered Simulation with PhysicsX on Apple Podcasts