Advancing Healthcare Technology Through Simulation
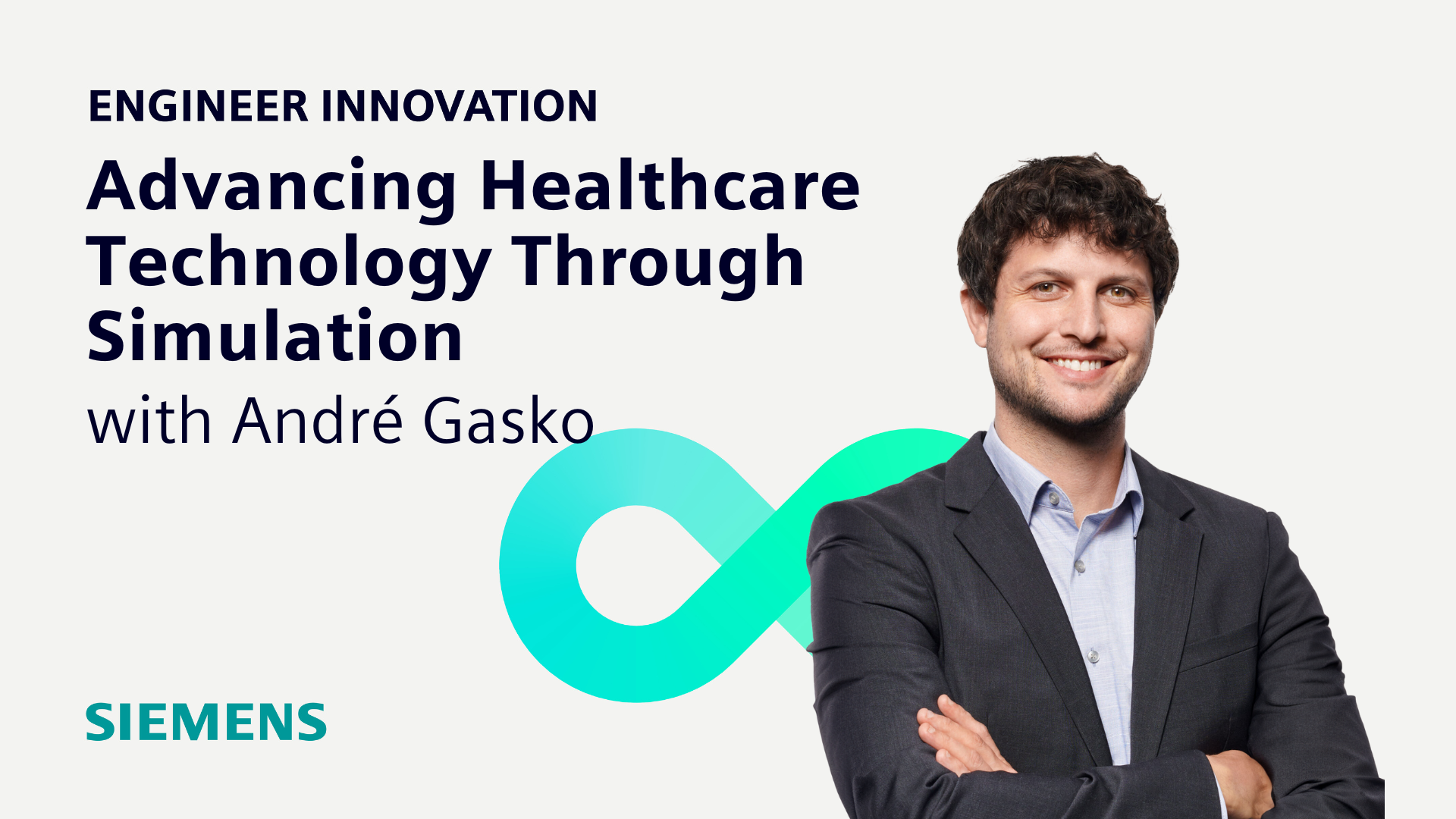
Guest André Gasko of B&W Engineering
Listen on Apple
Listen on Spotify
Show Notes
In this episode, we’re joined by André Gasko, Simulation Engineer at B&W Engineering, to explore the intersection of engineering simulations with real-world applications in electric vehicles and medical devices. With a focus on thermal management and simulation efficiencies, André provides insights into how these technologies shape the development and optimization of complex systems in various sectors.
Key Takeaways:
- Transition challenges between sectors are guaranteed, so solution strategies are a must.
- Exploration of thermal management in medical devices illustrates cutting-edge engineering practices.
- Simulations play a vital role in reducing developmental costs and timelines.
This episode of the Engineer Innovation podcast is brought to you by Siemens Digital Industries Software — bringing electronics, engineering and manufacturing together to build a better digital future.
If you enjoyed this episode, please leave a 5-star review to help get the word out about the show and subscribe on Apple or Spotify so you never miss an episode.
Watch on YouTube
Guest biographies and episode transcript
- The importance of thermal management in electric motors. (03:32)
- Engineering challenges addressed through simulation. (04:12)
- Differences in safety and design flexibility between automotive and medical sectors. (09:41)
- Detailed discussion on a peristaltic pump project and thermal management issues. (14:12)
- Benefits of simulation in validating engineering designs. (21:58)
- Future directions in medical device engineering and potential for innovation. (28:11)
- The integration of new technologies and their impact on engineering practices. (29:50)
André Gasko 0:00
Of course, you have a cost on the software, and you have a cost on the engineer itself. But then the amount of possibilities that it gives you to search for new solutions to give a big spectrum of ideas that you can use in the simulation and see which one works and which one don’t have a lot of potential is significant.
Stephen Ferguson 0:22
Hi Chad, who’s the guest on this week’s episode?
Chad Ghalamzan 0:25
This week, I’m talking to André Gasko from B&W Engineering. They’re a consulting firm based in Munich, Germany.
Stephen Ferguson 0:35
So you’re really careful to say that, B&W and not BMW, which is another famous firm from Munich, as well. So at B&W, they’re a consulting firm, what sort of consulting do they do?
Chad Ghalamzan 0:45
They do all sorts of different work. But André has been focusing mainly on medical devices. So we talked a little bit about that. But previously in his career, he worked on electric vehicles. So we compared the difference between the two, going from working on something as complex as a vehicle versus smaller medical devices, what’s the unique challenges for each? And how he brought his expertise in the thermal and electromagnetic performance of electric motors to both end applications.
Stephen Ferguson 1:15
So how different are the motors of these applications? It’s not just the case, you can pick a motor off the shelf and put it in a new application, you have to design it specifically. Is that right?
Chad Ghalamzan 1:24
Yeah, and the thermal runoff from the motor that was impacting the medical devices was a big challenge for him. Whereas the electric vehicle was more performance and getting range. So different challenges, they have to be attacked differently. And ultimately, cost for both of those applications are very different. So he was bringing in multi-level attributes in terms of the discussion, in terms of what was driving each project.
Stephen Ferguson 1:51
And so I guess as we wean ourselves off combustion devices, we’re going to see more and more electric motors. And it’s going to require more and more specialized engineering. So let’s have a listen to this week’s podcast.
Chad Ghalamzan 2:02
Welcome to this episode of The Engineer Innovation podcast. I’m Chad Ghalamzan. And I’m joined today by André Gasko from B&W Engineering. André, thanks for joining us today. How are you?
André Gasko 2:14
Thanks for having me. I’m fine. And you?
Chad Ghalamzan 2:16
I’m good. I’m good. So tell us a little bit about your background, who is André Gasko?
André Gasko 2:22
I’m a mechanical engineer. I’m 37 years old. I live in Germany for 10 years now. I’ve studied in Brazil, I come from Brazil. I worked in Germany for three different companies. The frequent companies that I work for, one was Webasto. The other one was Nidec. And the actual company of which I’m working for is called B&W Engineering.
Chad Ghalamzan 2:28
Yes. What does the Webasto, what was that company? What were you doing there?
André Gasko 2:50
So Webasto and Nidec were two companies, they were in the automotive sector, which is really strong in Germany. And Webasto was working with the development of hitting systems for cars, and battery modules. And at Nidec, I was working with the development of electric motors for electric vehicles. And at the moment, for now, six years in total, I’ve been working at B&W Engineering with the development of medical devices.
Chad Ghalamzan 3:24
So before we get into the medical devices part of your career, you said you were working on electric motors for vehicles. Was the heating also for electric vehicles? Was that for combustion vehicles?
André Gasko 3:34
Exactly. So my part in the development was the thermal management of electro motors. So I was in a team of several simulations engineers, so we had simulations engineers working with electro magnetics, making the design of the electric motor, and also, like, mechanical calculations engineers doing FM analysis. And I was working together with them to improve the efficiency of the electric motors as much as possible, given the specifications from the customer. And so the size and the power from the motor.
Chad Ghalamzan 4:14
And you said you moved away from that industry a few years ago, have you kept up with the recent developments? I think a lot has changed in the last five, six years, because of the growth of electric vehicles.
André Gasko 4:23
It has been changing. I’m following it. So I can see that the motors are getting smaller. I can see there’s also a lot of developments in cooling systems for the motors, which is a big problem because they have permanent magnets, then they get demagnetized after a certain temperature. You have to ensure that they don’t get too hot. And there is some development there. But I would say I’m not so sure if there is like a breakthrough since then, I think electric motors stayed actually approximately in the same position or the same development status. I have been seeing that they’re getting smaller and a little bit more efficient. But in itself, it’s the same thing as several years back.
Chad Ghalamzan 5:08
You don’t think… They’re still just trying to address the same issues?
André Gasko 5:12
Exactly. So you have different cooling types of electric motors. So you have either oil cooling, water cooling or air cooling, or the mixture, the combination of them together. I have seen, there’s a development of a company here, near Munich, which is doing inner cooling in the winding, so that really increase the cooling capacities. But I haven’t seen these kind of motors coming in the automotive sector until now. We’ll see. But yeah.
Chad Ghalamzan 5:43
So you’ve focused a lot on the electric machine aspect of EVs, they obviously have lots of different, let’s say, physics or different areas of critical performance to look at. So there’s both the electromagnetic performance and the cooling of it, like you mentioned. So you’d look at this both from electromagnetic side and also the CFD side of things, if I understand correctly, yeah. So a lot of people maybe go down one of those paths, not both simultaneously. What made you want to pursue work with electric motors?
André Gasko 6:12
So I really like big challenges. And this was a big challenge there, because you’re faced with some parameters given by the customer. And you have to achieve them, power requirements. And the thermo aspect is a big one. So because depending if it’s too good, it means your motor is too expensive, it could be cheaper. And if it’s below the cooling requirements, it means actually that you’re under the required efficiency. So you’re not getting the amount of power that the customer’s requiring, actually. So the motor is too hot. So you need to apply other measures to decrease the temperature in the winding and the magnets. And it was a very interesting subject, because it’s all really nonlinear. So you have nonlinearities in almost all the components involved. So you have nonlinearities in the steel parts of the rotor and the stator, you have nonlinearities in the power loss of the copper in the windings, for instance. And you also have the nonlinearities of the fluid, which is being required for the cooling. So the oil cooling, for instance, when it’s being used to cool down when you’re doing high voltage motors so that you have using oil and at extreme temperatures, the viscosity and the density of the oil changes really much. So it’s really high, the changes there. And this all makes the subject itself very complex. This is something that really attracts me actually, I really like working on complex subjects. And it’s not all about a routine job. So you have all these different subjects in one. So motor physics problems is something that really capture my attention.
Chad Ghalamzan 8:00
Okay, you like looking at the thing holistically, not just one particular dimension,. Did you know that you would initially be pursuing electric vehicles or working in that industry when you were studying? Or is that something that just came about afterwards?
André Gasko 8:05
No, it just something that came about when you start a career, a simulations engineer, you don’t need to stay as a certain subject, I would say up to aviation, because aviation requires a lot of certifications. But in the industry itself, when you are a simulation engineer, you know the physics about it. So you can work either way with medical devices or work with electric motors. And the physics is actually just about the same. Just the bondic renditions may differ and the aspects of the geometry itself, as well. But the physics stays the same. So the same knowledge apply. So you having a background in simulations in one area can give you a lot of advantages to follow another area later on.
Chad Ghalamzan 9:06
Of course, and I know we’ve talked a lot about work you’ve done more recently at B&W Engineering, and you’ve applied the same knowledge to the work there because you were looking at different devices, but looking at the electromagnetics or the thermal and cooling considerations there. So let’s talk a little bit about this – no pun intended – shift in career, you went from electric vehicles to working for a company and specialize a lot in medical device applications. What’s different when you go from a consumer product, or something like electric vehicles, to medical devices? What’s the difference in terms of how you need to work or how you have to approach your work?
André Gasko 9:43
There are some requirements that will come in itself different. The safety requirements are also different. So in the medical industry, you have a really higher safety factor in which you have to develop your device and it has also to be approved later on. As the same as, of course, automotive components, but the degree of the improvement is higher. So the degree of…
Chad Ghalamzan 10:06
Stricter, more strict?
André Gasko 10:07
It’s more strict. So in itself, I would say that in the automotive sector, you’re really trying, the competition is really high, it’s higher than in the medical sector, you’re really trying to get as cheap as possible in your components. And this gives you a little bit of, it holds you, it doesn’t give you a lot of freedom to explore and try something new in the geometry or in the components that you’re using or in the solutions that you are searching. And in a medical device, you have a little bit more flexibility, I would say, at least this is my experience so far, that it gave me more freedom to search for different possibilities. So different solutions for the problems at hand.
Chad Ghalamzan 10:55
Gave more of a buffer because cost wasn’t the only driver there. Okay. Which makes sense, I guess. I mean, obviously, vehicles, like you said, they’re tested, and we want them to be safe. But there’s a big difference between the safety margins that go into a vehicle versus a medical device that someone’s in care, and we want to make sure they get the care they need, definitely don’t want things to perform at the wrong level. And like you said, it’s hyper competitive that space, so you need to drive solution at the right cost. So just that extra freedom, that gives you the possibility of exploring your work in a different way than you had been able to previously? That kind of what drew you to the medical device, a part of your simulation work?
André Gasko 11:37
Yes. So I’m very driven by the challenges, the medical device industry is also… So the products that we developed are very complex. They’re very small in scale, they are made of plastic, which has a nonlinear behavior already in the elastic phase, for instance, a lot of aspects there that make the development of such products really complex. And this is something that I thought it was really interesting from start on. So the company that I work for is a consulting company that does the development for the big device developers or the device productors in Germany, and every product that comes to our company, it’s very different from the previous one. So it’s never the same thing that we’re doing. Sometimes it can be a big machine. And sometimes it’s a really small sensor that goes inside the skin. And that itself, it’s something that I think it’s very challenging, but also, it’s very cool to work with.
Chad Ghalamzan 12:45
Yeah, and something you mentioned before about motors and with electric vehicles you were looking at, a lot of active cooling systems, you had a lot of maybe options to explore but, and medical devices, obviously, it’s the same problem. Heat is the enemy, you need to reduce the heat, but you’re dealing now with a component that’s usually sealed or for other reasons needs to stay water ingress protection, so that must add a lot of difficulty there, and you don’t have the same cooling options available.
André Gasko 13:11
No. So normally, with the high energy demand in electric motors, you need some other type of cooling. So you need like water cooling or oil cooling. Where in medical devices, normally you have actually normally air cooling. So we have work with products which needed fans to cool it down. But typically, it’s natural convection, it’s the most typical thermal problem that we face. So small devices made of plastic in the housing, which has to be sealed from the environment. So there is no water ingress, and with a lot of electronic components inside producing heat, and yes, this heat has to be dissipated somehow so it doesn’t affect the mechanical integrity of the device itself. So this will be the typical calculation that we do when it’s regard to thermal management.
Chad Ghalamzan 14:14
And one of the first projects that you spoke to me that you were working on was a peristaltic pump, that not only those factors, there was a battery because it needed to work in blackout, a burnout situation. So there had to be a battery and the thermal considerations that go into the battery, as well, you mentioned were an issue. You couldn’t have the temperature reach a certain point otherwise the battery performance would degrade.
André Gasko 14:34
Exactly. So in this case, we had a peristaltic pump with six batteries inside and the batteries are there for in case the pump gets disconnected or there is a power outage in the hospital. So the pump can run for two hours at least after it got disconnected when the patient had been moved somewhere for instance, as well. And there, we faced the problem that because of the cleaning standards, the pump had to be sealed. And by sealing all the holes inside the pump, it meant that we cannot use an active cooling there. So the only way to cool it down to the pump would be by natural convection. And by having a housing made of plastic, that made it really hard because the heat being generated inside, which was more or less eight to nine watts, which is not much. So in electric motors, we’re talking about actually 1.5 kilowatts or two kilowatts losses, then here we are talking about only eight to nine, but the heat doesn’t get dissipated. So the housing made of plastics are really good insulation material. And there we had a problem that by the batteries reaching a temperature more than 60 degrees, they lost the possibility or the capacity to get recharged. So they get damaged. And so for that reason, this was the maximum temperature that it could be reached, and we had a problem that it was being reached this temperature.
Chad Ghalamzan 14:43
You’re crossing that threshold of…
André Gasko 14:54
They was crossing and they’re getting problems. So it came to us, we had to provide a solution for that.
Chad Ghalamzan 15:59
To keep the temperature below the threshold. And you were also trying to make this the most efficient pump or want to improve the efficiency of the actual pump itself, right? Because you were looking at not just all that, which is complicated enough looking at the battery and the thermal runoff and all that, you were also looking at the performance of the pump itself. And these pumps with the way the tubing works, also was a quite challenging problem, as well.
André Gasko 16:47
You mean about the peristaltic pump itself?
Chad Ghalamzan 16:50
The peristaltic pump itself, yes.
André Gasko 16:52
So there was another problem. And it was more a mechanical problem. And this was the problem that the display, by closing the display of the pump, you had the mounting device of the peristaltic pump would close the tubing between the mounting device and the rolls of the rotor. And we had a tolerance issue. So as I mentioned, these are small gadgets or small devices, and made of plastic which can have really high tolerances. And we try, of course, to work towards not so much expensive devices. So we tried to work where it’s possible with high tolerances. But in this case, the high tolerances would create a gap inside the tubing by closing the mounting device onto the rotor. The sum or the addition of all the tolerances together will give us more gap in the tubing. So the tubing would not be enclosed properly inside the pump, and we wanted to be sure what is the effect on the flow, on the fluid flow of the pump itself? Is this a big problem or not? And we wanted to have also an idea how much of a problem it is not only that but, okay, if we try to solve one issue in the tolerance and the tolerance gets lower but do we still have a little more, a small gap, does this solve it? So you want to have a function of the amount of a gap and the amount of a problem, or the amount of volume flow that is getting decreased by this gap. And the only way or the easiest way – not the easiest way, I would say, but let’s say the less expensive way – of testing this was by simulating it.
Chad Ghalamzan 18:38
We can talk about that in a second. But just maybe for those who aren’t as familiar with these types of devices. My understanding is the parasitic pump is for drug delivery or delivering food or what have you, nutrient supplements. Basically, these devices have to be very accurate because they’re delivering something that the doctors or medical staff need to be absolutely certain how much the volume of whatever they’re trying to introduce into the patient is what they set the machine to. So any gap, any deficiency would be extremely detrimental to the ability for them to trust this device to perform the way they want.
André Gasko 19:14
Of course. So because it’s of a device that’s used for drug delivery, for infusion fluids and also for nutrition, it is detrimental or is really important that you have high accuracy. So accuracy is everything in the development of medical devices. And there is some problems with peristaltic pumps itself where you have a relaxation of the tubing, for instance, where it gets oval with time, it doesn’t stay round. And this decreases the volume flow. Or if you have also problem with pulsation because you don’t have actually a steady flow, you also have a pulsation of the flow, depending how many rolls you have in your tube, in your pump. And, of course, also the tolerance problem where the tube itself doesn’t get completely closed. And these are all aspects that have to be, really have to be looked into in the development of the device. So the tolerance problem was only one aspect, there are other ones. But this is the one that we solved, and where we’re looking at when we’re using similar simulation tools.
Yeah, how would you even try to solve both these problems? Because they’re not directly related. But at the end of the day, you need to produce a product that meets all these requirements. How would you be able to achieve this without simulation?
You would need to test it.
Chad Ghalamzan 20:35
But would this be something feasible to do, to build and test?
André Gasko 20:46
Yes, it is feasible, you do have to get in contact with different companies that produce these parts, or you do it at your facility. Some of the parts can be 3D printed, others cannot. And you have to assemble it. And after assembling all of the pieces together, you have to test it. And after testing, you’re gonna see if there is a real problem there or not. And just then, you are sure that you need to regroup now that the engineers have to go through and try to find a solution for the problem.
Chad Ghalamzan 21:25
It takes a long time, it’d be very costly. Doesn’t simulation help you reduce the number of tests you need to do? Even for a medical device?
André Gasko 21:34
Yes, we actually after a lot of years now of experience, we can actually even give numbers to this problem. So the company exists longer than we use simulations for the development. And we can say that the cost reduction went to something like six times lower using simulation tools.
Chad Ghalamzan 21:59
Six times?
André Gasko 22:00
Six times.
Chad Ghalamzan 22:01
Wow.
André Gasko 22:01
It really depends on the kind of product and the amount of pieces being used.
Chad Ghalamzan 22:06
But you’re looking at a significant reduction.
André Gasko 22:08
It’s a significant number. So, again, we will… Of course, you have a costs on the software, and you have a cost on the engineer itself. But then the amount of possibilities that it gives you to search for new solutions, to give a big spectrum of ideas that you can use in the simulation and see which one works and which one don’t have a lot of potential is significant. Before it was like you regroup and you say, okay, let’s try to find a solution now. And we’ll come to the solution that will probably give the best hopes of solving the problem. And then you do test again, and then if it doesn’t solve the problem, then you are already much over already the expenses and the costs. Otherwise, you would solve it using simulation. So in simulations, you do all the virtual testing beforehand and give the final solution, which has to be of course, in the end, verified or validated by testing. And this is the cost part, which was six times lower. And the time part, it’s 10 times lower.
Chad Ghalamzan 23:15
Okay, which must make a huge impact on your ability to deliver, as a consultant, projects.
André Gasko 23:21
Yeah, you have to get in contact with the, again, the companies developing the parts, and you have to assemble. So for the pump, for instance, the peristaltic pump, the prototype could take up to two months to assembled.
Chad Ghalamzan 23:37
That’s a long lifetime then, every time you want to…
André Gasko 23:39
Exactly. And it could take a long time. And then, of course, you have the assembled and then you test it. Then you have the problem if it doesn’t work. And then you have to do again. Of course, it’s not gonna take two months, but you can see the problem that it takes a long time. And with simulation, we were able to reduce a lot.
Chad Ghalamzan 24:02
For both the issues you mentioned, you were able to use Simcenter’s STAR-CCM+ to look at alternatives for both the battery issue and the heating for the battery and the tubing. So that you were able to simulate, and you were able to meet the requirements in the end?
André Gasko 24:18
Yes. So in the battery problem, we were able to simulate the status quo design. So the design which you had the problem, and you see already in simulation together with tests being done, that you have exactly the same temperature getting the simulation as you’re getting in the tests. And you see there’s a problem there. And then already, so by using STAR-CCM+, for instance, that you can actually, really fast, change some properties in the geometry, for instance, or in the material properties can already have different results. See what’s really helping here and what’s not. Thermo problems are really hard to solve, harder to solve than mechanical problems, that’s my experience. So it’s really good to solve them already in the concept phase, not later on in the project. Because normally, these are kind of problems that need a lot of geometry optimizations to solve it. So in the passive cooling, so natural convection, you really, normally you need a heat sink, for instance, to solve a problem there. And to integrate a heat sink into the device, well, we have to make changes into the geometry of the housing, have to make changes on the layout of the PCB inside the component, in the cables. So there are big changes there in the device, that has to be taken in account.
Chad Ghalamzan 25:44
Yeah, the earlier you do it, the less of an impact it’s going to have.
André Gasko 25:47
It’s less of a problem. Exactly. And the peristaltic pump problem was more to have an idea how much it could impact this go up inside the tubing, on the accuracy. And we saw then, already, with the calculation, that the impact was really big. And so we knew then before our tolerance analysis engineers, they knew which components had to be changed or fixed. So the tolerance doesn’t get that high. So we don’t have the problem by applying the amount of pressure of the tubing device into the rotor.
Chad Ghalamzan 26:24
So which is more complex, an electric vehicle or the peristaltic pump, in terms of design? Sounds like they both were equally difficult in terms of trying to adjust to the challenges, maybe just looking at it in a different perspective.
André Gasko 26:36
This is hard to say. I wouldn’t… I don’t even know how to compare both of them. Because increasing the efficiency of electric motor is also not easy, especially regarding, let’s say, oil cooling. So oil cooling is really complex, you have oil being injected into the shaft. And depending on the speed of the shaft, you have different volume flows on both sides of the electric motor. So because you need cooling on both sides of the electric motor, the A side and B side. So the both sides of the rotor, because otherwise you have a hotspot on the other side. And depending on the speed and temperature of the oil, it changes the flow on both sides. And this is a very complex analysis itself. It’s very different. But on the other hand, if the peristaltic pump or you have the fluid structure interaction analysis, which you have hyperelastic material like the tubing being compressed. And this has to also change the geometry of the fluid because it’s attached to the fluid. So the fluid is being also compressed, and is changing its geometry. And this is also a very complex analysis. It’s hard to say, actually, which one of them was more complex than the other, but both are very complex.
Chad Ghalamzan 27:55
I’m glad that you were able to work on both because you seem to be very knowledgeable. I have a lot more confidence with someone like you who is willing to look at it holistically, trying to solve those issues. Has there been any other interesting projects you’ve been able to work on at B&W in the medical device space?
André Gasko 28:12
We worked also in the development of diabetes care device. And we used a lot of STAR-CCM+.
Chad Ghalamzan 28:20
What type of device was it, like, for diabetes? Because there’s lots of devices on the market.
André Gasko 28:25
Of course, it’s for diabetes care. So it’s a device to measure the amount of blood sugar into the body.
Chad Ghalamzan 28:32
So more like the droplet type, not like the device types that are attached to your body?
André Gasko 28:37
No, but these devices have been developed by B&W, as well. But the device in question, which there was a lot of simulations being involved, was a device where you had blood coming out of the finger, you have to pinch your finger and come bloods out, and you come with a test stripe, collect the blood and put into the device, which then calculates the amount of blood sugar that the person has.
Chad Ghalamzan 29:02
So why was that necessary to simulate? I mean, compared to what we just talked about, electric vehicles and the pump. Okay, those are very complex devices, lots of considerations that go into the cooling, what have you. A pinprick blood droplet doesn’t sound nearly as complex Why did you have to simulate it?
André Gasko 29:18
For actually similar reasons to the peristaltic pump, which also has a battery inside, but the main problem there was the wireless charging device being used by this device. So the idea was similar to the peristaltic pump, that you have as less as possible water ingress. You try to make the device as waterproof as possible. And by doing that, the device had to be wireless-charged, so you don’t have the inlets for charging device. You do it wirelessly. And the problem there is that it also gets hot, the wireless charging device itself, so the pad gets really hot. And when, depending on some geometric differences into the housing, it could got hotter or less hot. So we had to get the optimum housing thickness. And so we get the highest charging capacity. So it gets charged in less time. But at the same time, the less thermo, so the less temperature increase or thermal problem inside of the device because of this proximity to the…
Chad Ghalamzan 30:32
Right, because you don’t want it sitting there charging for three days, because that would…
André Gasko 30:35
It can. So it charges, the temperature rises and comes to a plateau, it comes to a steady state, it doesn’t get hotter than that. And we have to ensure that this temperature, it’s not as high that’s going to damage the battery. And also is not going to affect the region where the test stripe is being inserted to make the analysis. So the temperature can also not be that high, because the chemical process being used in the test stripe is also a little bit sensitive to temperature.
Chad Ghalamzan 31:09
Okay, so you had to really make sure the heat was… Another heat issue. Okay.
André Gasko 31:12
So you had the region where you insert a test stripe is being isolated from the other components. And it’s a compromise. You want to reach the highest efficiency by charging the device, and the same time, the lowest possible temperature inside the housing, because it can affect the battery and it can affect the test stripe region.
Chad Ghalamzan 31:37
And were you able to address the issue? Were you able to come up with induction charging situation where it wouldn’t impact battery and the test stripe?
André Gasko 31:45
Yes. So it was possible to make a motor physics analysis there, in which you have the wireless coil in the transmitter and the receiver parts, and which is really good by using STAR-CCM+, as it gives you this ability to make electromagnetic simulations. Which is something that I knew already from my previous work with the development of electric motors, which was, actually, I always wanted to make all-in-one simulation to have the temperature impacting the electro magnetic behavior of the motor. Never got to it in the end. I was just doing the electro thermal part. But here was really nice to see this function in use, where we could change the topology of the housing. And this would change the distance between the receiver part and the transmitter part of the coils. And this will change the current being induced into the receiver, which will change the temperature behavior of the device itself. So it was really good actually to finally give the possibility to do this in the simulation. We were able to solve the problem, to find at least what is the minimum thickness of the housing and the material properties from both components to have the highest charging capacity without having the highest temperature into the test stripe region and into the battery.
Chad Ghalamzan 33:17
So you’re originally from Brazil, I believe?
André Gasko 33:20
Yes.
Chad Ghalamzan 33:20
Which part of Brazil are you from?
André Gasko 33:23
San Paolo.
Chad Ghalamzan 33:24
That’s a very warm, tropical area, right?
André Gasko 33:27
It’s normally what you think about Brazil, but San Paulo is a little bit souther than Rio and it’s really high. So it’s 800 meters high. It’s hot in the summer, of course, it can go up to 30 degrees. Not much more than that.
Chad Ghalamzan 33:42
But how cold does it get, when it’s in the winter?
André Gasko 33:45
Five…
Chad Ghalamzan 33:46
Five? That’s…
André Gasko 33:47
At coldest, I would say, we had like situation where there were three degrees. And then this is already calamity, is already…
Chad Ghalamzan 33:55
No, because you’ve relocated to Germany, I was wondering if you, like, just like all of the engineering problems where you seem to be trying to get away from the heat, did you go from Brazil to Germany because, again, in your life, you were trying to get away from the heat?
André Gasko 34:06
I want the heat not to be a problem.
Chad Ghalamzan 34:09
Exactly. You went to some place where it wouldn’t be a problem.
André Gasko 34:12
I have to be honest, I don’t like heat that much. I don’t like saunas. I actually really like the weather in Germany, I have to say. I’m in the souther part of Germany, in Munich, which is sunny. It’s not like the northern part. And I’m okay with it.
Chad Ghalamzan 34:26
There’s obviously no arguing with taste. The one thing we haven’t had a chance, and I’m in a phase where I ask almost everyone that comes on the podcast the same question, just to wrap things up. A lot of talk about artificial intelligence, a lot of talk about how that might change how we approach our work. No matter what type of work you do. What do you think? Is artificial intelligence going to change… You like to look at things, like you said, holistically. Is that a tool that will help you to do that?
You mean in the simulating part or overall?
Either way but mainly, I guess, simulation. That’s your main line of work.
André Gasko 35:00
I don’t know, to be honest. I can see the day when you could just upload the geometry and explain a little bit what’s happening there and the artificial intelligence is gonna understand the problem because it faced similar problems before like this, and is gonna be able to give a solution. But I have to be honest, I work with a lot of complex problem which requires much physics. And every problem is different. It could be the case, it could happen, that we get to this stage. But just like today, you have the artificial intelligence but you still have to be sure that what’s being given is correct now, because you get a lot of things that are not correct. So we’re gonna need an engineer in the end to see this now, to prove it. But I don’t know, if you’re that close to this, but I could see the potential, yes.
Chad Ghalamzan 35:42
Great. Thank you for talking with me today. It’s been a lovely chat. I hope you’ve enjoyed it. And it’s been really interesting learning more about medical devices and your experience with cooling electric machines.
André Gasko 36:06
Thank you very much for the time and for the talk. I really like it, as well. Thank you.
Chad Ghalamzan 36:12
Great. Thank you for listening to this episode of the Engineering podcast. Make sure to tune in for our next episode. I’m Chad Ghalamzan.
Speaker 1 36:21
This episode of the Engineer Innovation podcast is powered by Simcenter. Turn product complexity into a competitive advantage with Simcenter solutions that empower your engineering teams to push the boundaries, solve the toughest problems and bring innovations to market faster.
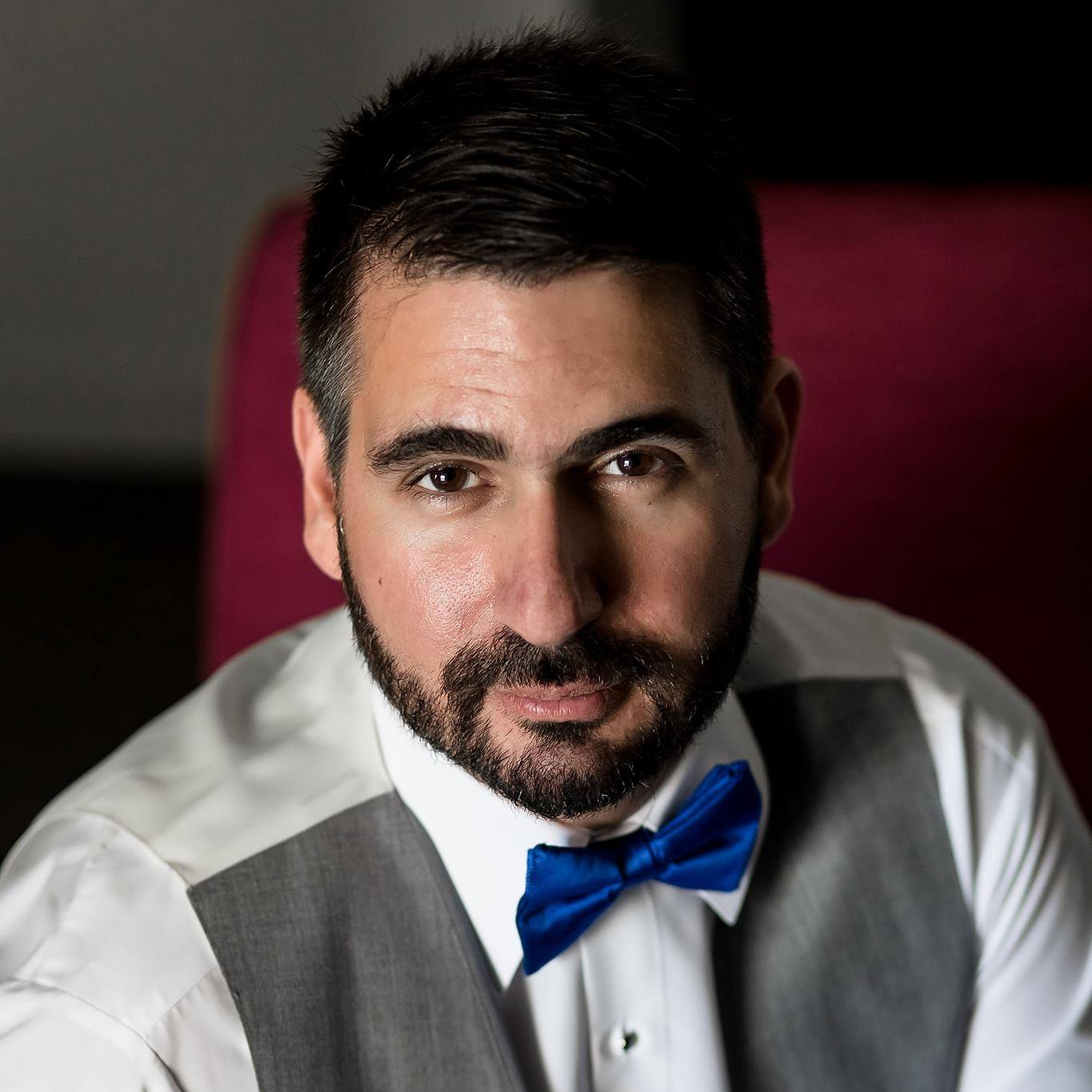
Chad Ghalamzan – Host
Chad Ghalamzan is a computer engineer with over two decades of experience in sales and marketing for the simulation and test industry. He co-hosts the Engineer Innovation podcast and creates content for Siemens Digital Industries Software. He’s tired of people calling him ChadGPT.
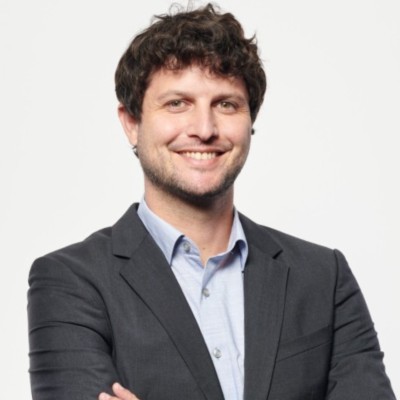
André Gasko
André Gaskois an experienced CAE Engineer specializing in thermal, mechanical, and fluid mechanics analysis for the automotive and medical technology industries. With over a decade of engineering experience in Germany, André has contributed to projects at Nidec Motors and Actuators (Germany) GmbH and Webasto Thermo & Comfort. Currently, André serves as a Simulation Engineer at B&W Engineering
Take a listen to a previous episode of the Engineer Innovation Podcast: Engineer Innovation: Failure Is Not an Option: Digital Transformation in Mission Assurance with Nancy Lindsey and Todd Tuthill on Apple Podcasts
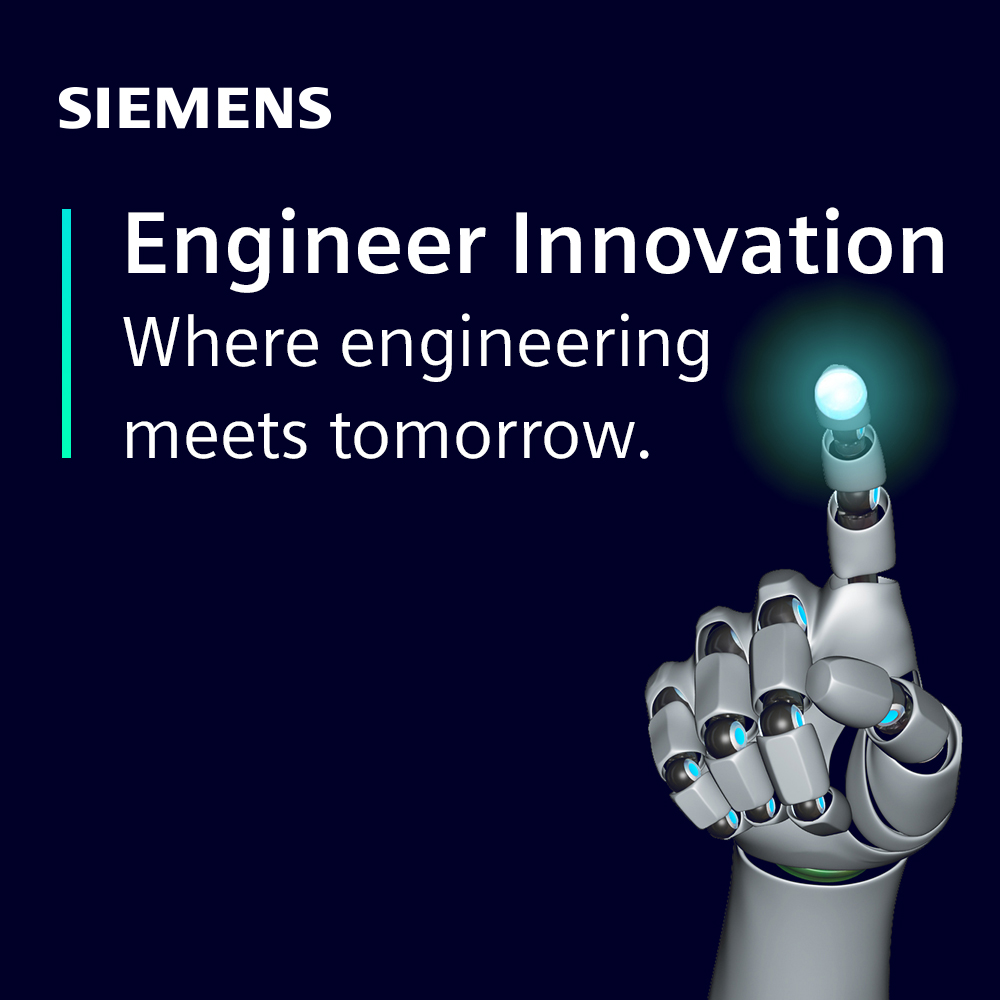
Engineer Innovation Podcast
A podcast series for engineers by engineers, Engineer Innovation focuses on how simulation and testing can help you drive innovation into your products and deliver the products of tomorrow, today.